What is High Pressure-High Temperature (HPHT)?
Some companies are willing to drill and develop very deep wells to reach oil reservoirs due to the potential for a lucrative payout. Greater challenges for well construction and operation arise when drilling deeper, though. At a certain point the limits of standard oil tools are reached and consideration must be given to redesign. In recognition that these deeper wells require different standards for equipment and operation in order to ensure integrity and safety, the Society of Petroleum Engineers (SPE) has defined High Pressure-High Temperature (HPHT) conditions. These are considered to be pressure greater than 69MPa (10,000psi) and/or temperature greater than 150°C (300°F).
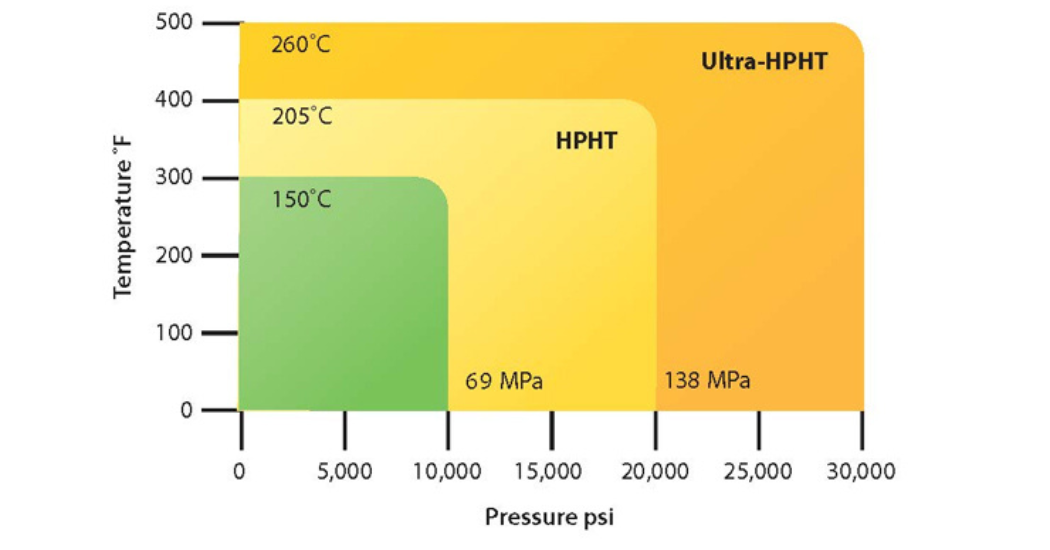
Figure: HPHT Definition
It is worth noting that a well does not need to meet both pressure and temperature limits per SPE definition to be called HPHT. Rather, a well is considered HPHT if it has either high pressure or temperature that qualifies. While pressure is typically related to depth, temperature may be abnormally high due to a local geothermal hotspot or due to usage of enhanced oil recovery (EOR) such as steam injection.
Impact to Equipment Design
Drilling, evaluation, completion, and production tools used in very deep wells must withstand high pressure while also fitting into increasingly smaller diameters. Equipment is typically designed from higher strength alloys to maintain stability and avoid collapse. Wireline and Logging While Drilling (LWD) tools are used to transmit data about the conditions of a wellbore, and house electronics which must be protected from the downhole environment. Increased pressure means greater challenges to design of sealing systems which prevent flooding and damage to costly equipment.
As downhole temperatures increase seals conventionally used can be adversely impacted. In addition, high temperature drilling operations typically require a change from conventional Water-Based Fluids (WBFs). Basically, these WBFs thicken, and their efficiency in lubricating and cooling the bit, as well as their ability to carry rock cuttings away, diminish. As a result, companies move away from these and towards Oil-Based Fluids (OBFs) or Synthetic-Based Fluids (SBFs) which can be more chemically aggressive.
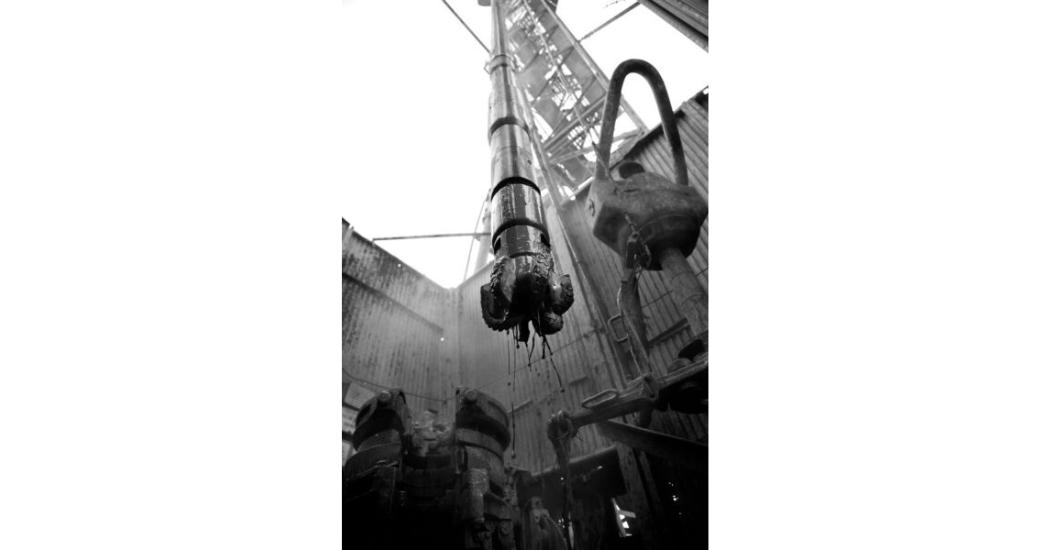
Figure: Drilling Operation
Sealing Challenges
In an HPHT well sealing elements must be thermally resistant while resisting extreme pressure. While all seals need to be resistant to produced fluids including oil, natural gas (CH4), water, seawater, and even hydrogen sulfide (H2S), these fluids may be even more aggressive in an HPHT environment. In addition, drilling and treatment fluids may be different by virtue of increased well depth or temperature.
Extrusion: Extreme pressure can lead to extrusion of typical sealing elements. Clearance gaps may increase due to higher wellbore pressure. Higher temperature can result in material softening and reduced extrusion resistance.
Thermal degradation. Materials may soften or even harden at especially high temperature. Cracking may occur on surfaces exposed to highest temperature.
Compression set. High temperature can lead to excessive thermal growth. Exposure to unexpected chemicals may result in volumetric swell. General loss of elastic properties can occur at high temperature with compression set the outcome.
Rapid gas decompression (RGD). Gases forced into the sealing element may be unable to escape upon system decompression. This may result in partial or complete destruction of the seal.
Chemical attack. Exposure to especially aggressive media such as amines and H2S can result in chemical degradation such as blisters, cracks, or discoloration.
Design Strategy
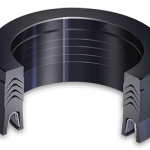
Figure: Stacked Set
Sealing elements may need to be fabricated from special rubber or plastic materials to meet HPHT conditions. Further, profiles selected may be slightly different to reduce high pressure and high temperature implications. Finally, some thought may need to be given to redundant or ancillary seal elements where not previously employed as with a stacked set.
Pressure Resistance. As pressure increases consideration to reduced clearance gaps should be given. Where this is not possible, a higher modulus seal material should be used. Backup or anti-extrusion devices made from PEEK may be required.
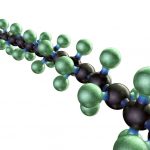
Figure: PTFE Molecule
Thermal Stability. A material with appropriate temperature resistance should be employed. For seals made from rubber, a fluoroelastomer (FKM) will at minimum be required. Polytetrafluorethylene (PTFE) has a maximum continuous use temperature of 260°C (500°F).
Compression set resistance. Gland design should ensure there is no overfill of the seal at maximum temperature. One may need to move from a compression style to spring energized seal.
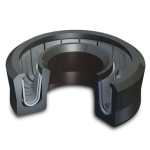
Figure. Spring Energized Seal
Gas sealing. If a rubber is used choose one with higher hardness. Polymeric seals are a good option since they do not see RGD damage. Consider use of NORSOK M-710 compliant or certified materials.
Chemical resistance. Choose materials chemically compatible to the fluids of exposure. PTFE is one of the most chemically resistant polymers available. Consider materials with sour service approvals.
Summary
Sealing in HPHT equipment requires careful considerations. Seal profiles must be wisely selected and materials appropriately chosen to suit these applications. This will ensure productive deployment of equipment while maximizing mean time between maintenance (MTBM) intervals.
For more information on how to choose spring designs and materials for specific applications, download the Chesterton Spring Energized Seal Guide. Learn more.
About the author:
Ron Taylor is the Business Development Manager for the spring energized seal (SES) product line. He has an Engineering background in the design & development of seals and related materials. He is able to promote these through his understanding of markets including Oil & Gas, Aerospace, and Industrial.
Comments