With reliability issues, excessive downtime, and repairs amounting to $126,000, AFT Fathom™ was used to determine a new pump configuration that increases reliability and saves $200,000 a year in energy!
Phil Sneeringer, Tier 1 reliability engineer at Flowserve Corporation, used AFT Fathom to perform a cooling water study at an existing refinery in the Midwest, USA. The purpose of the study was to identify the most economical scenario to run their cooling water pumps and provide a solution for the excessive erosion at the suction bell of an existing high-performing pump (Figure 1 above).
Operational confidence in the pump and system reliability had decreased due to equipment downtime which resulted in nine work orders totaling $126,000. Four of those work orders included high vibrations or other substantial mechanical failure.
Sneeringer’s team was asked to monitor the system to determine why pumps were having premature suction bell erosion, and then identify the most economical way to run the cooling tower pump system.
Using wireless technology, flow and pressure data was collected throughout the system. They then used this data to model and analyze the system and tune an AFT Fathom model (Figure 2). Their AFT Fathom model predicted almost exactly what their field data showed. Sneeringer states, “the accuracy achieved was excellent.”
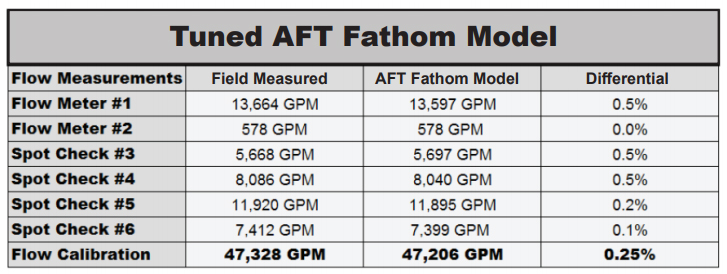
Figure 2. Field data was used to tune an AFT Fathom Model. The AFT Fathom model was “highly accurate.”
Based on several AFT Fathom modeled scenarios, Flowserve then presented the refinery with six recommended pump configurations that would provide the required flow and head to remove heat from the units (Figure 3).
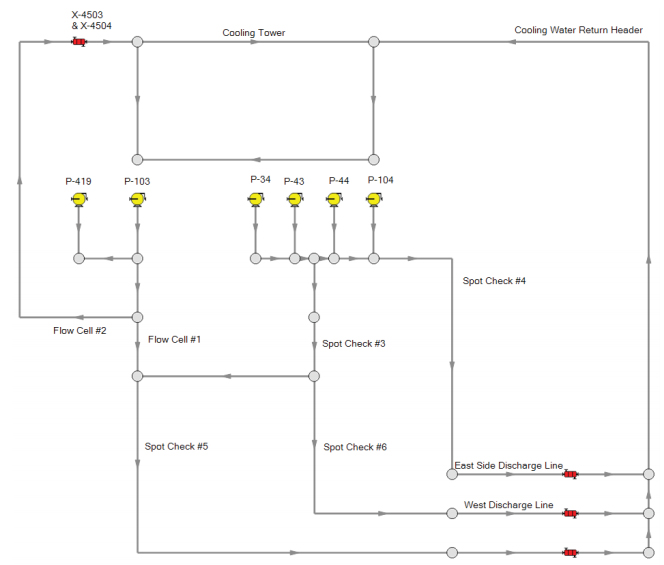
Figure 3. AFT Fathom model of the existing system used to create new pump configuration scenarios.
By using AFT Fathom, the customer had the required data to change the way they ran their cooling water pumps. They were able to achieve the required cooling at the units while running with 4 pumps instead of 6 (Figure 4). This saved them $200,000 per year in
operating cost!
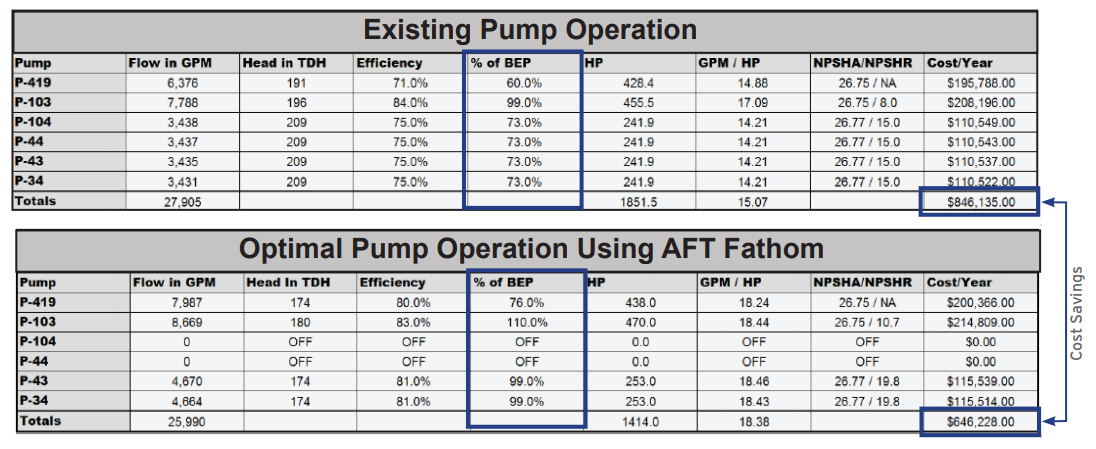
Figure 4. Identifies the existing pump operations compared to the optimal pump operations for the cooling water pump system. The cost savings is approximately $200,000 per year.
Comments