Problem
Rajitha Papagari, Lead Process Engineer with LyondellBasell, performed a hydraulic study to evaluate a 28% production increase. The study used a calibrated AFT Fathom model to evaluate the existing infrastructure’s capacity and identify bottlenecks.
The existing system was composed of a pump feeding parallel vessel trains, heat exchangers, control valves, and other fittings (Figure 1).
Solution
At the increased design capacity, the control valves indicated both the original pump and maximum impeller diameter were inadequate, requiring Papagari to size a replacement pump.
The model helped identify several high-pressure drop components to replace, such as small orifice flow meters. Upsizing several pipes and adjusting the pipe layout further reduced head requirements for the replacement pump (Figure 2). Collectively, modifications to the system reduced pump suction pressure drop by 72% which also improves NPSHA for the replacement pump. Further testing worst-case scenario testing at higher system losses verified the replacement pump and existing control valves would be suitable.
The AFT Fathom model enabled Papagari to find cost effective and simple modifications to increase production, saving on project cost and completing work ahead of schedule.
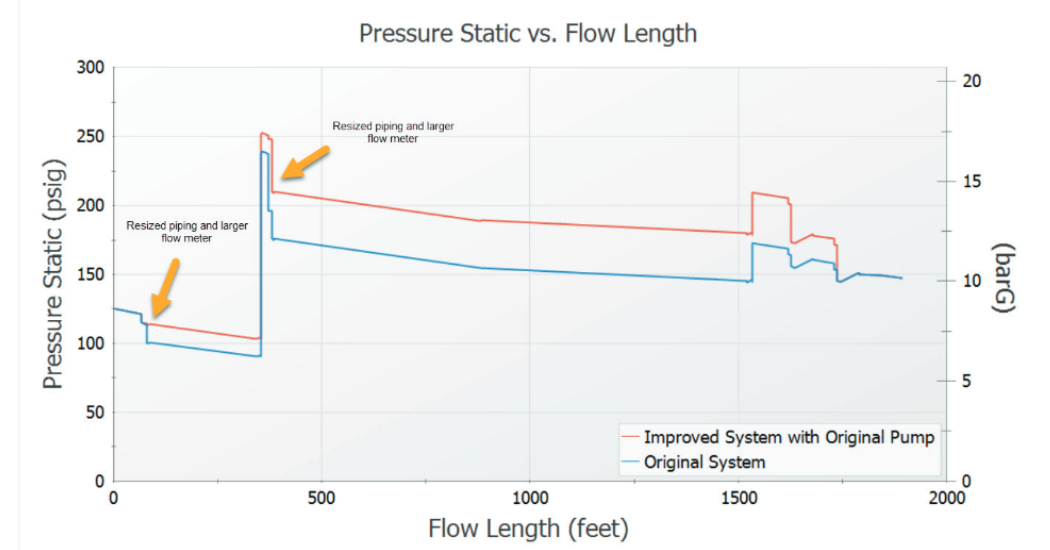
Figure 2-Pressure profile graph comparison highlighting the adjusted high-pressure loss components.
Analysis
Papagari’s model was built from piping isometric, fittings databases, and datasheets for pump curves, flow meters, and control valve characteristics. Complex components, such as heat exchangers and packed vessels, were modeled as pressure drop vs. flow resistance curves. The process fluid’s properties change as the fluid is heated and cooled, which Papagari also captured in the model.
The model was calibrated against plant pressure data at specific control valve open percentages, adjusting pipe resistance to match pressure along the piping profile. A large deviation between the calibrated model and measured data revealed a faulty pressure measuring device, which was verified by plant personnel.
Model in hand, Papagari could evaluate each possible design using the system’s flow control valves. With the control valves set to the higher flow capacity, the valves would fail open when the system could not meet the flow requirement. Alternatively, the valves could indicate the additional head required to achieve the specified flowrate in the system.
“AFT Fathom helped identify excess pressure drop precisely in the existing pipe network which plant data alone couldn’t reveal.” – Rajitha Papagari, LyondellBasell
Figure 1- Workspace view of the parallel vessel piping system, highlighting the pumps, high-loss flow measurement devices, and flow control valves used to evaluate designs.