Author: James Farley, Centrifugal Pump Product Manager, PSG® Griswold™
Faithfully rising each morning for uncountable generations, our familiar sun remains a master at hiding the significant secrets of its fundamental physics. Its behavior can have major effects on our everyday life on Earth. Solar flares and coronal mass ejections can negatively affect or even completely shut down radio communications, GPS satellite availability and the power grid.
Scientists, in their ongoing quest to learn more about Earth’s nearest star, are continually creating new models to explain its nature and predict its behavior. As the complexity and sophistication of these models grow, they require increasingly advanced solar telescopes with resolutions beyond the capabilities of current installations, even those in space, for validations.
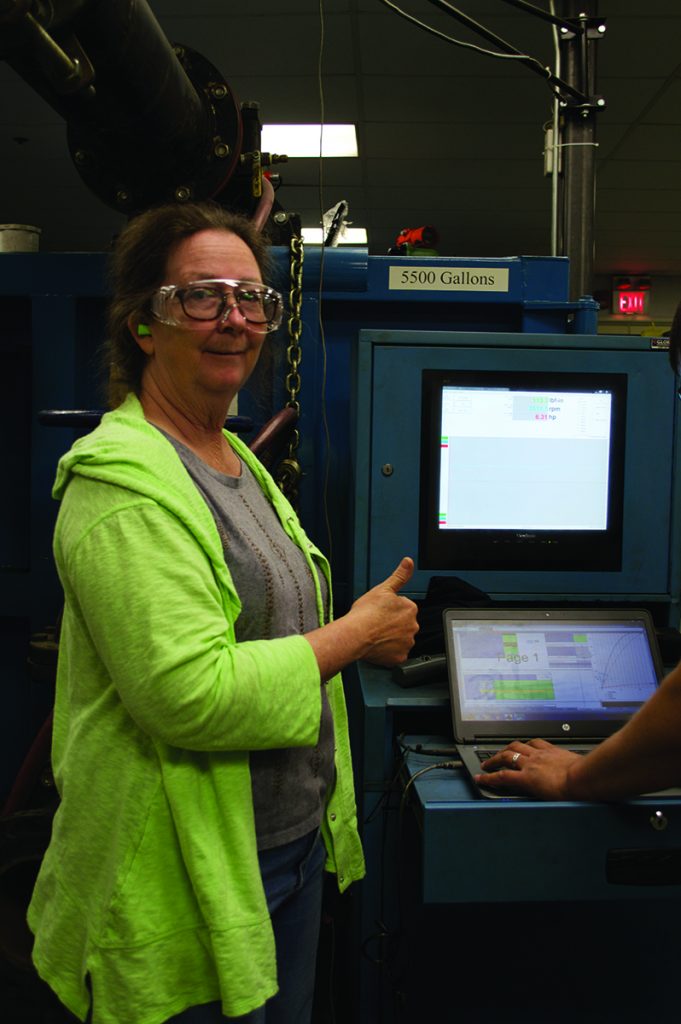
LeEllen Phelps, NSO Thermal Systems Manager, signals that the Griswold™ 811 Series pumps passed all required factory-acceptance tests. (Photo Courtesy of Griswold Pump Company, part of PSG®)
To meet this important need, the National Solar Observatory (NSO) is constructing the Daniel K. Inouye Solar Telescope (DKIST) at an elevation of 10,000 feet (3,048 meters) on the Haleakalā volcano summit in Maui, HI. NSO is funded by the National Science Foundation under a cooperative agreement with the Association of Universities for Research in Astronomy, Inc. All research here is based in part on data collected with the DKIST, a facility of the NSO.
While the DKIST’s innovative adaptive optics will provide the sharpest views ever taken of the solar surface, obtaining precise optical performance will require close control of the telescope’s thermal environment. This entails closely matching the surface temperature of the observatory dome’s exterior to the ambient air temperature in order to eliminate any density differential in the air that would degrade the optical path.
Maintaining the precise dome temperature in the extreme weather environment atop the volcano requires high-pressure coolant to circulate throughout a network of sheet heat exchangers that are mounted onto the observatory structure. In selecting a suitable pump for this task, the NSO set high operating specifications, including a wide temperature range, and also called for an extremely tight delivery schedule in order to keep the aggressive construction timeline on course.
JCH Sales Engineer Dean Newbold and LeEllen Phelps with Griswold™ 811 Series pumps ready for shipment to Hawaii. (Photo Courtesy of Griswold Pump Company, part of PSG®)The DKIST
To provide solar scientists with a telescope capable of observing the sun at the required high resolution, a collaboration of 22 institutions, headed by the NSO, National Science Foundation (NSF) and Association of Universities for Research in Astronomy (AURA), joined together to build the world’s largest solar telescope. The $344-million DKIST will allow for observations with unprecedented spatial, spectral and temporal resolution via sub-second spectroscopic and magnetic measurements of the solar photosphere, chromosphere and corona. Its location on Haleakalā was selected for its reliable, clear daytime atmospheric viewing conditions.
Construction at the DKIST site began in January 2013, and full operational capability is scheduled for 2020.
Controlling Observatory Exterior Surface Temperature – A Critical Function
When telescopes operate with such high resolution, all factors affecting performance must be managed to ensure maximum equipment accuracy. One of those factors is control of all observatory and telescope thermal surface environments, which is overseen by LeEllen Phelps, NSO Thermal Systems Manager. Phelps manages the design, equipment acquisition and construction of all facility thermal systems at the DKIST.
“It is critical that we control the thermal environment of every optic, every instrument and every path that the optical train passes through,” explained Phelps. “To do this at the required precision, we must install numerous thermal-management systems throughout the structure. Our goal is to maintain the instruments and facility at a uniform temperature matching that of the ambient air within ±2°C (±3.6°F). Only so much of that degradation can be compensated for in the optics of the telescope.”
An important thermal environment that must be controlled is the exterior surface of the telescope enclosure. The dome presents more than a quarter acre of surface area whose temperature must be precisely regulated to closely match the ambient air. Any temperature differentials between the ambient air and the building surfaces create what scientists call “seeing,” which is a density differential within the air that degrades the optical path and results in image distortion.
According to Phelps, the pumps are the heart of the coolant-distribution system that manages the thermal environment of the observatory exterior. “We will use pumps to circulate 10 different temperatures of closed-loop heat-transfer fluid to cool different components of the observatory, including the exterior, to a very precise temperature that follows whatever the ambient temperature happens to be at a given time. Several closed loops will circulate coolant a few degrees below the ambient temperature to keep the exterior skin temperature at a state constantly matching ambient conditions even with the sun hitting the surface and with varying wind conditions.”
Pumps used for this purpose must meet strict specifications. “In this application, we are using an ionic brine for the heat-transfer solution in a regime of low temperatures that are much lower than what conventional HVAC pumps could handle without freezing up and having issues,” said Phelps. “It’s mostly the low temperatures in some of the cooling regimes that determined the most important pump-specification parameters. Energy efficiency was also an important factor because of the high cost of power on Maui.”
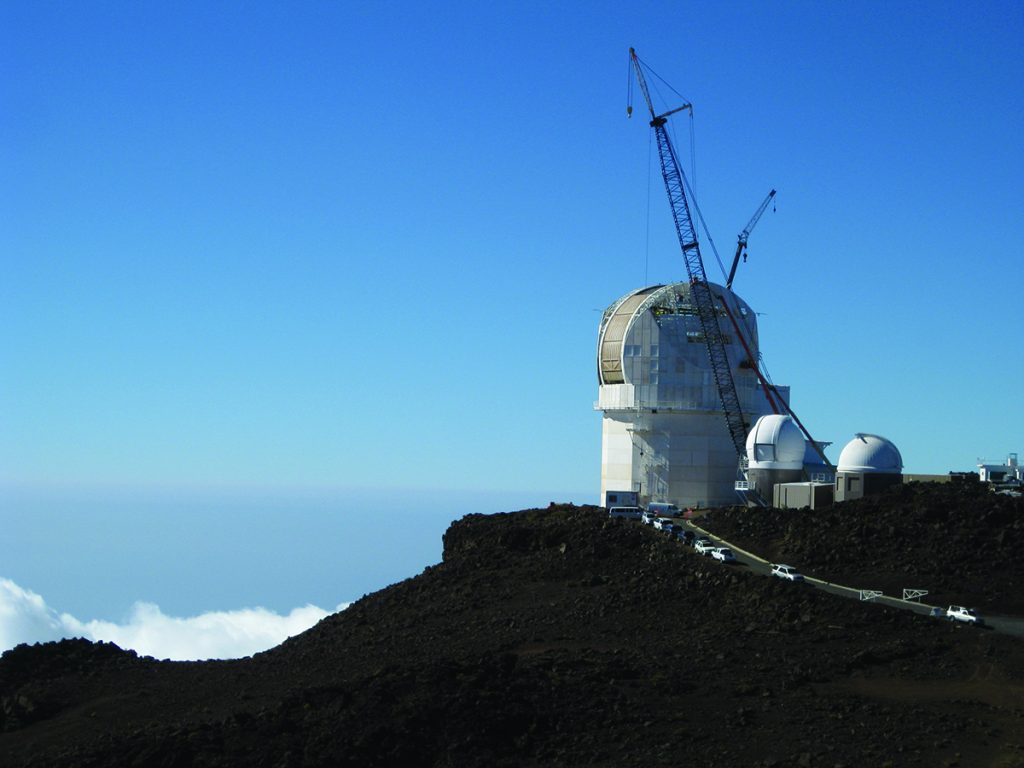
The DKIST will study solar phenomena such as these superheated plasma loops in much greater resolution than possible with current installations. (Photo Courtesy of NASA SDO Instrument Teams)
Griswold™ Meets Critical Construction Schedule
From the onset, the NSO set an aggressive construction schedule, and thermal-system component selection and acquisition were no exception.
After a competitive-bid process, the pump contract was awarded to James, Cooke & Hobson, Inc. (JCH), a major industrial equipment distributor based in Albuquerque, NM, USA, with offices in Arizona, New Mexico, Texas, California and Nevada.
JCH Sales Engineer Dean Newbold was assigned as lead on the project, but knew immediately that meeting the aggressive deadlines set by the NSO would be a challenge. At that point Newbold contacted Griswold™ Pump Company, Grand Terrace, CA, USA, part of PSG®, a Dover company, based in Oakbrook Terrace, IL, USA, for assistance.
“Because of the fast-track nature of the project, only Griswold could meet the required testing and delivery timelines, as well as the strict pump-performance specifications,” said Newbold. “This was not a small project because there were 26 pumps, motors and baseplates needed. I had dealt with Griswold in the past, so I went to them first when the scheduling issue came up because Griswold is known for its quick deliveries.”
Griswold worked closely with Newbold to meet the deadlines by building, testing and delivering 26 811 Series ANSI Centrifugal Pumps in nine different sizes and configurations, including some with a low-flow configuration. NSO staff personally monitored pump testing to measure suction pressure (psi), discharge pressure (psi), power (HP), speed (rpm), flow (gpm), fluid temperature (°F) and vibration.
Exceeding standard ANSI construction requirements, the 811 Series offers many design innovations that deliver long-term operational reliability, including:
- A fully open impeller with rear adjustment capability and twice the wear area of enclosed models for superior handling of solids, corrosives and abrasives
- Back pump-out vanes that reduce hydraulic loads and seal-chamber pressure, resulting in smooth, stress-free operation
- Standard bronze labyrinth oil seals that keep outside contaminants from entering the lubrication media, which significantly extends bearing life
- Extra-heavy casings that incorporate a standard Class 300 wall thickness that extends casing life even when used with severely corrosive or erosive fluids
- Heavy-duty shaft that minimizes vibration and shaft deflection, resulting in optimized pump life, and bearings that are sized for a 10-year life span
“The Griswold 811 Series is perfect for demanding applications like this,” said Newbold. “The NSO staff was very impressed with the construction quality and the performance.”
Thanks to Griswold Pump Company and its ability to quickly meet tight delivery deadlines with high-quality pumps, the construction of the DKIST’s exterior thermal-cooling system is right on schedule.
“Griswold was incredible in ensuring all timetable commitments were met, and we were especially impressed since everything occurred during the holiday season,” said Newbold. “Griswold is a partner we know we can count on, no matter what, plus their pumps have the quality and workmanship needed to meet rigorous specifications, including those for the cooling systems on the DKIST.”
About the Author
James Farley is Centrifugal Pump Product Manager for Griswold™ and PSG®. He can be reached at James.Farley@psgdover.com. Griswold is a global leader in centrifugal pumps from PSG, a Dover company. Headquartered in Oakbrook Terrace, IL, USA, PSG is comprised of several of the world’s leading pump brands, including Abaque®, Almatec®, Blackmer®, Ebsray®, EnviroGear®, Griswold™, Mouvex®, Neptune™, Quattroflow™, RedScrew™ and Wilden®. For more information on Griswold or PSG, please go to griswoldpump.com or psgdover.com.