Introduction
Electric motors are the backbone of industrial operations, powering everything from conveyor belts to HVAC systems. However, while they provide the necessary mechanical force, they are also susceptible to electrical issues that can lead to costly downtime and premature failure. One often overlooked aspect of motor reliability is shaft grounding—a simple yet crucial protective measure that prevents electrical damage within the system.
As an engineer at WorldWide Electric Corporation, Andrew Dunn has seen firsthand how ignoring shaft grounding can lead to expensive repairs, excessive downtime, and even safety hazards. In this article, he explores when shaft grounding is necessary, why it’s important, and what happens when it’s neglected.
What Is Shaft Grounding?
Shaft grounding refers to the practice of installing a grounding system that directs stray electrical currents away from the motor’s shaft and into a safe, designated path to prevent bearing damage. These grounding systems typically include:
- Shaft grounding rings
- Brushes
- Carbon-block grounding devices
These components serve to safely discharge unwanted electrical charges before they can cause harm.
Why Is Shaft Grounding Important?
Many modern electric motors, especially those controlled by Variable Frequency Drives (VFDs), are susceptible to stray electrical currents that can build up and discharge through the bearings. When this happens, it can lead to Electrical Discharge Machining (EDM), where the high-energy electrical arcs cause pitting and premature wear on the bearings.
Key Benefits of Shaft Grounding
- Prevents Bearing Damage – Reduces electrical pitting, wear, and overheating.
- Extends Motor Lifespan – Protects bearings and reduces replacement frequency.
- Minimizes Downtime – Helps avoid costly breakdowns and production interruptions.
- Improves System Efficiency – Reduces energy losses and ensures smooth operation.
- Enhances Safety – Prevents potential electrical hazards and unexpected failures.
When Should You Use Shaft Grounding?
While not all motors require shaft grounding, certain applications and conditions necessitate it to
prevent damage.
1. Motors Controlled by Variable Frequency Drives (VFDs)
When to Use: Always
- VFDs create high-frequency common-mode voltages that can induce unwanted currents in the shaft.
- These currents seek the easiest path to ground, often through the bearings, causing electrical pitting and premature failure.
- Shaft grounding provides a direct, safe path for these currents, eliminating bearing damage.
2. High-Power or High-Speed Motors
When to Use: When operating at 100 HP or more
- Large industrial motors tend to generate greater electrical noise, increasing the likelihood of shaft voltage buildup.
- High-speed motors also experience increased friction and wear, making grounding crucial to long-term performance.
3. Motors Operating in Critical Equipment
When to Use: Always
- If motor failure can cause severe production downtime, costly repairs, or safety risks, shaft grounding is a must.
- Applications such as HVAC systems, data centers, and medical equipment rely on continuous operation, making prevention a priority.
4. Motors with Insulated Bearings
When to Use: In combination with insulated bearings
- Insulated bearings help block electrical currents but do not eliminate the voltage buildup.
- A proper shaft grounding system ensures that stray voltages are safely discharged instead of finding alternative, destructive paths.
What Happens Without Shaft Grounding?
Neglecting shaft grounding in the wrong conditions can lead to a cascade of issues that increase costs and operational headaches.
1. Bearing Damage & Failure
- The most common consequence is Electrical Discharge Machining (EDM), which creates microscopic pits in the bearing surfaces.
- Over time, these pits lead to rough operation, increased friction, and ultimately failure.
- Bearing failures account for nearly 50% of motor breakdowns, and electrical discharge is a leading cause.
2. Increased Maintenance Costs
- Motors without proper grounding require frequent bearing replacements.
- The added maintenance costs—both in labor and parts—quickly add up.
- In high-duty cycle applications, bearings can fail within months if shaft currents are left unchecked.
3. Unexpected Downtime
- Equipment failure due to bearing damage results in unplanned production halts.
- Unscheduled repairs disrupt operations and can lead to financial losses, particularly in continuous production environments.
4. Secondary Equipment Damage
- Shaft currents can travel beyond the motor, affecting connected components like gearboxes, pumps, and driven machinery.
- These components are not designed to handle stray electrical currents, leading to further failures down the line.
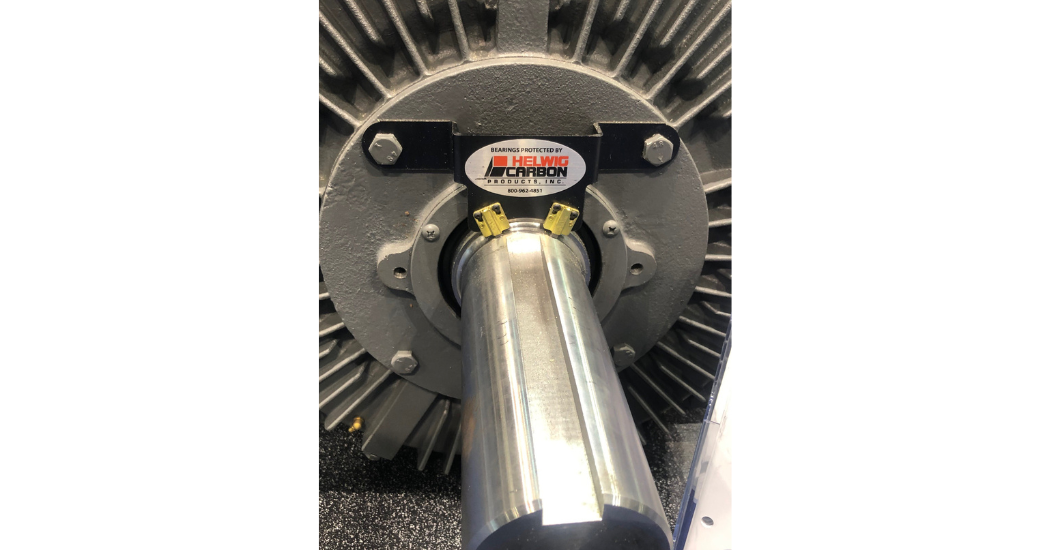
WorldWide Electric Severe Duty Motor with After Market Brushes attached
How to Implement Shaft Grounding
Now that we understand the importance of shaft grounding, let’s discuss how to apply it
effectively.
1. Install Shaft Grounding Rings
- One of the most effective solutions for VFD-driven motors.
- Grounding rings use conductive microfibers to provide a low-resistance path to ground, preventing shaft currents from reaching the bearings.
2. Use Carbon Brushes
- Carbon brushes conduct stray currents away from the shaft and into a grounding system.
- While effective, they require regular maintenance and replacement.
3. Consider Hybrid Bearing Protection
- A combination of insulated bearings and shaft grounding rings offers a two-tiered protection strategy.
- Ideal for high-risk applications where motor longevity is a key concern.
4. Regular Monitoring and Testing
- Use shaft voltage testers to check for unwanted electrical buildup.
- Conduct routine motor inspections to detect early signs of bearing wear.
Conclusion: Shaft Grounding Is Essential for Motor Reliability
Shaft grounding is not just an option—it’s a necessity for many industrial motor applications. Whether operating on a VFD, high-power system, or in a critical environment, proper grounding protects bearings, reduces maintenance, and improves overall system reliability.
At WorldWide Electric Corporation, we’ve seen firsthand how investing in shaft grounding can extend motor life, prevent costly failures, and enhance operational efficiency. If you’re unsure whether your motors require grounding, consider conducting a shaft voltage assessment or consulting with an expert.
Take Action Today
- Evaluate your motor applications to determine if shaft grounding is necessary.
- Invest in proper grounding solutions to avoid premature failures.
- Consult a motor specialist if you need assistance implementing an effective grounding strategy.
By taking a proactive approach, you can protect your motors, reduce downtime, and maximize efficiency—saving both time and money in the long run.
Author | Andrew Dunn | Product Manager, Motors and Gears | WorldWide Electric Corporation
ABOUT THE AUTHOR
As a seasoned engineer at WorldWide Electric Corporation, I’ve spent years navigating the complexities of industrial maintenance. With a passion for innovation and a knack for troubleshooting, I’ve witnessed the evolution of maintenance strategies from the ground up. Through this journey, I’ve learned that the best approach adapts and evolves, much like the technology we rely on daily.