Julian Yeo, United Electric Controls, and Saurabh Sanghavi, Vimal Fire Controls, discuss the crucial role of instrumentation in a rim seal fire protection system.
Tank farms, with their vast arrays of storage tanks, serve as critical nodes in the supply chain of various industries, including petrochemicals, oil and gas, and chemical manufacturing. The sheer scale and volatility of the substances stored in these tanks, as well as the potential for catastrophic incidents, makes tank safety paramount. This article examines safety systems on floating roof tanks, particularly rim seal fire protection systems (RSFPS). Selecting the right instrumentation for such a system is crucial for tank storage safety.
Industry standards
There are several standards that are associated with RSFPS. The ‘API RP 2001: Fire Protection in Refineries’, which was published by the American Petroleum Institute (API), provides guidelines for the design and installation of fire protection systems in refineries, including recommendations for rim seal fire protection. The National Fire Protection Association (NFPA) published a standard, ‘NFPA 11: Standard for Low-, Medium-, and High-Expansion Foam’. This standard covers the design, installation, operation, and maintenance of low-, medium-, and high-expansion foam systems, which may be used for rim seal fire protection. In Europe, there is the ‘EN 13565-2: Fixed firefighting systems – Foam systems – Part 2: Design, construction, testing’. This standard provides specifications for foam systems, including those used for rim seal fire protection. In specific countries like India, there is the ‘OISD-STD-117: Fire Protection Facilities for Petroleum Depots, Terminals, Pipeline Installations and Lube oil installations’, an Oil Industry Safety Directorate (OISD) standard which is being used to design rim seal protection systems.
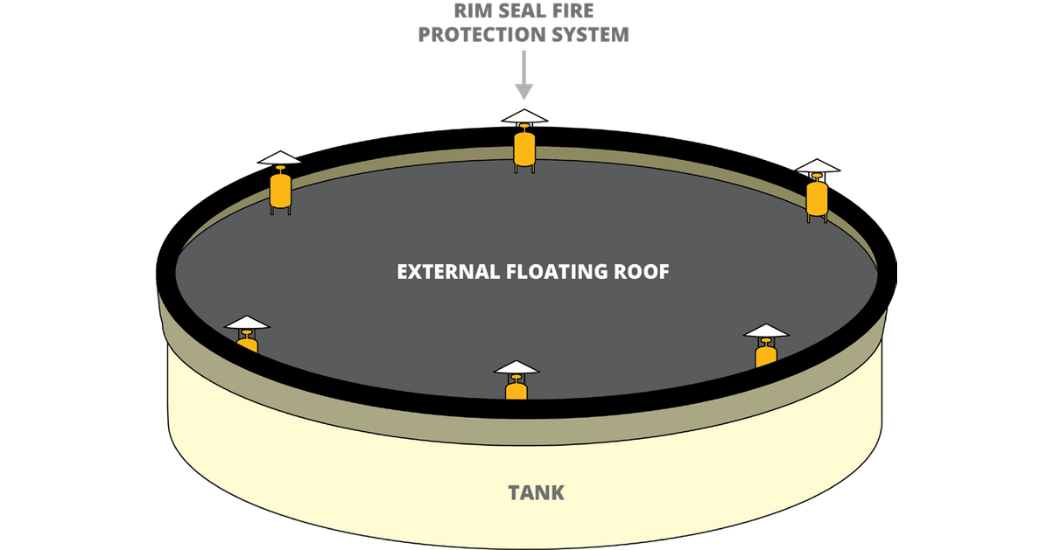
Fig. 1 External floating roof.
Rim seal fire protection system (RSFPS)
A RSFPS safeguards floating roof tanks (Figure 1), the most common type used in tank farms. These tanks consist of a roof that floats on the stored liquid, allowing for minimal vapour emissions. The rim seal is the area where the roof meets the tank shell, forming a critical seal. However, this area is vulnerable to fires due to lightning strikes, static electricity, or equipment malfunctions. 90% of fires in open floating roof tanks start in the seal between the floating roof and the tank wall, known as the rim seal.
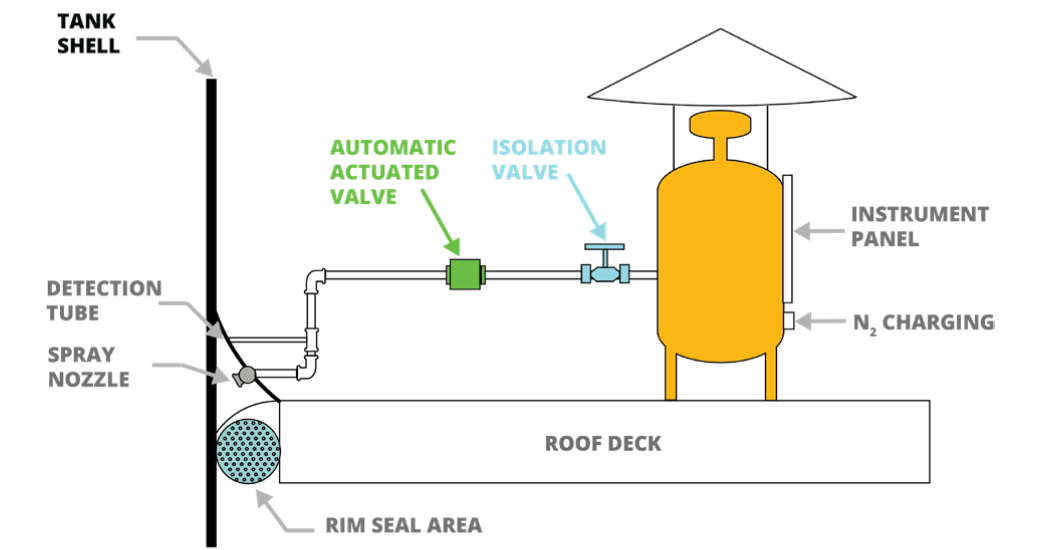
Fig. 2 A rim seal fire protection system (RSFPS).
A RSFPS (Figure 2) detects and suppresses fires at the earliest stages and typically comprises three key components:
- Detection system: this includes sensors like heat detectors, flame detectors, or fusible elements strategically placed around the rim seal. These sensors quickly alert the system of even minor fire outbreaks.
- Extinguishing system: this consists of a network of pipes, nozzles, and pressure tanks containing the necessary pressurized fire-suppressing agents like foam or water. Upon detection, the system automatically releases the agent, extinguishing the fire efficiently.
- Control system: this central unit monitors the sensors, receives alarm signals, and activates the extinguishing system.
The role of instrumentation in a RSFPS
Instrumentation plays a pivotal role in the effectiveness of a RSFPS. The roof of the tank is an unmanned area where access is restricted, which makes instrumentation all the more important as it serves as the eyes and ears of the system. Various sensors, including those for pressure, level, temperature, flow, and heat, are strategically placed to monitor conditions and identify abnormalities. Precise and reliable instrumentation ensures that:
- Real-time data is communicated continuously: instruments like sensors and transmitters provide data on factors like temperature, pressure, and flow rate. This data allows the control system to predictively monitor the system’s health, enabling proactive maintenance and minimizing downtime.
- Accurate detection: sensors positioned strategically around the rim seal detect fire at the earliest stages, minimizing the potential for damage.
- Extinguishing agent delivery is optimized: by analyzing data from various sensors, the control system can optimize the delivery of extinguishing agents, ensuring effective fire suppression while minimizing waste.
Selection of the right instrumentation
The RSFPS has a control system unit that monitors the sensors, receives alarm signals, and activates the extinguishing system (Figure 3). The following is a set of criteria that designers of RSFPS would look for in their instrumentation:
- Reliability: the instrumentation should function dependably even in harsh environments and extreme conditions. This is likely the most important factor as it ensures the RSFPS can perform its mitigation function, which can determine if there is minimal or severe damage to plant assets and personnel. A trustworthy instrumentation brand with superior performance is recommended.
- Durability: the instrumentation should be built to withstand weather elements and the long-term wear and tear of a tank farm environment. An IP66 or NEMA4X rating should be a minimum.
- Accuracy and stability: precise measurements and data are essential for effective pressure monitoring, fire detection and suppression. In the instance of pressure readings, setpoints would be stable over temperature and time.
- Easy maintenance and after-sales service: simple maintenance procedures (e.g., field calibration with minimal tools) and readily available spare parts with quick lead times are crucial to minimize downtime and maintain system performance.
- Remote diagnostics: since the roof of the tank is an unmanned area, a device with remote diagnostics capability can inform the user if the instrument needs to be replaced immediately instead of waiting for the next maintenance round to discover the faulty instrument.
- Compliance with standards: instruments must comply with relevant international industry standards and regulations for safety and performance.
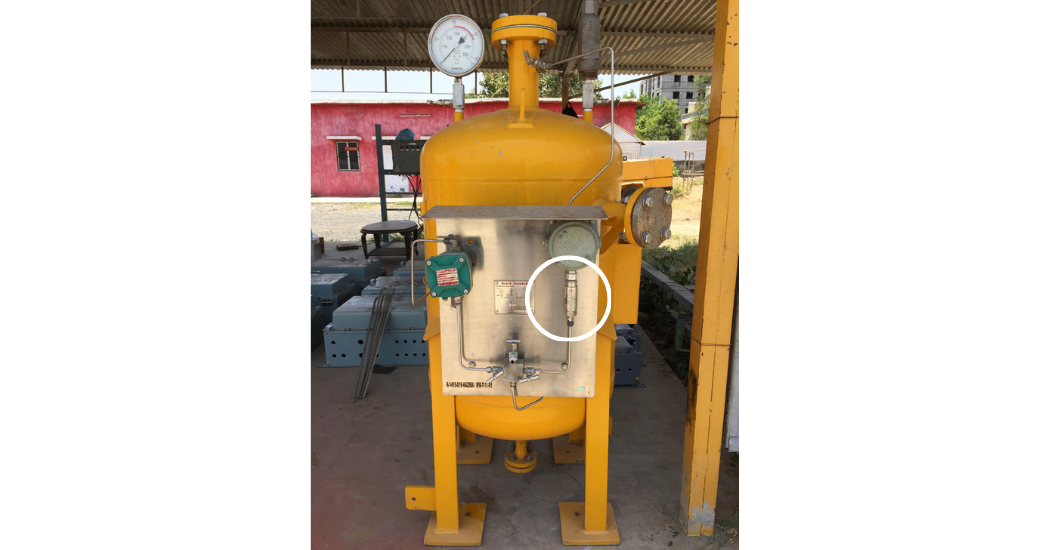
Fig. 4 Actual tank in a RSFPS with 12 series instrument circled.
Consequences of poor instrumentation selection
The consequences of selecting inferior instrumentation for the RSFPS can be severe and far-reaching. False alarms triggered by unreliable instrumentation can lead to unnecessary shutdowns and interruptions in operations. This not only incurs financial losses but also disrupts the efficiency and continuity of industrial processes. The ramifications of these disruptions can extend beyond immediate financial implications, affecting the reputation of the facility and its operators.
In addition, inaccurate or unstable readings or delayed response times due to faulty sensors can result in the system failing to detect a fire in its early stages. This, in turn, may lead to the uncontrolled escalation of the fire, causing significant damage to assets, posing environmental risks, and jeopardizing the safety of personnel. Non-compliant instrumentation can lead to significant fines and legal repercussions for regulatory violations.
Case study
The following case study demonstrates how a global RSFPS manufacturer, Vimal Fire Controls, partnered with a global instrumentation manufacturer, United Electric Controls, to design a reliable RSFPS for some of the largest clients in India.
Vimal Fire Controls manufactures RSFPS for floating roofs in tank storage facilities for facilities in India and the Middle East. A few common challenges arise in the design of a RSFPS:
- There is limited real estate on a tank roof. Space is a premium and hence the RSFPS must be compact in design.
- The extinguishing agent is only as effective as its coverage on the tank roof. This is heavily dependent on the agent’s discharge pressure. The effective functioning of the RSFPS is hinged on the reliability of the pressure monitoring device on the RSFPS.
- Maintenance efforts required on top of these storage tanks can be a hazardous and labor-consuming process.
Vimal Fire Controls selected United Electric Controls’ (UE) All-Stainless-Steel, SIL2-rated, compact 12-series pressure switch as the pressure instrumentation on the RSFPS. The discharge tanks (Figure 4) are pressurized to 15 kg/cm². When the pressure falls to 12 kg/cm², an alarm is triggered by the pressure switch to notify the operator that there is insufficient pressure in the tank. Insufficient pressure reduces the trajectory of the extinguishing foam, leaving areas of the tank susceptible to fire.
The 12 series was ideal for this application as it was compact enough to be fitted on the foam agent tank. The pressure switch has a Belleville spring design that provides the instrument with setpoint stability to eliminate false trips and reduce costly maintenance.
UE was chosen by Vimal Fire because of its reputation worldwide as a manufacturer of reliable instrumentation used in safety, alarm and shutdown applications. The 12 series also has two major certifications, UL and ATEX, which were requirements for the majority of its customers.
Conclusion
RSFPS are a critical component of safety measures in tank storage facilities, particularly for floating roof tanks. The selection of high-quality instrumentation is central to the effectiveness of such a system. Investing in reliable, sensitive, and interoperable instrumentation not only enhances the safety of tank storage facilities but also ensures the continuous and efficient operation of industrial processes. Conversely, the consequences of neglecting the importance of proper instrumentation selection can be severe, jeopardizing not only the assets within the tank farm but also the overall integrity and reputation of the facility. It is vital for engineers to understand the crucial role that instrumentation plays in a safety system.