For many job sites, especially in the mining and tunneling industries, pumps are crucial to staying on schedule — when they start to fail, the entire project can be delayed. When it comes to water features, a failing pump can mean the difference between a charming ambiance or a stagnant eyesore. Following a major disaster, a well-working pump can make all the difference in getting a life or business back on track.
With so much at stake, it is crucial that professionals learn to recognize and detect the most common causes of pump failure and how to root them out through analysis and troubleshooting. The following is a breakdown of the typical reasons why pumps start to fail and how one could go about diagnosing and fixing their problems.
No matter what the issue might be, pumps should only be disassembled and analyzed by authorized mechanics.
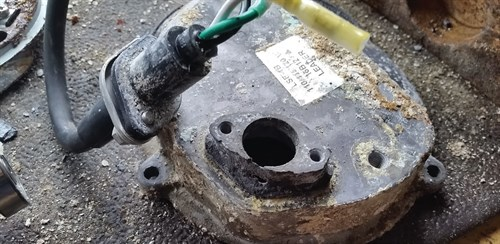
Anatomy of a pump failure
Regardless of the cause of failure, it is necessary to analyze the job site to see what might have gone wrong and to disassemble the pump for a closer inspection. This is especially true in the case of domestic water features, such as backyard waterfalls and ponds — because homeowners may not have the same engineering expertise of a mining aggregator or wastewater professional, misuse in applications is not uncommon. A thorough examination of a pump application will include an evaluation of the installation, the piping, the amount of flow and head, water content and the pump type used for a particular application.
When it comes time to disassemble the pump, the task should not be undertaken by the end user — it is recommended to have the work performed by an authorized maintenance and repair shop. An accredited shop will have strict guidelines on how motor evaluation and pump repair are performed. Authorized mechanics can take a pump apart and accurately assess the bearings, mechanical seal, impellers and general signs of abrasive wear. After every factor is scrutinized, a determination can be made and a course of action chosen.
Problems with voltage
Pumps are rated according to the watts or horsepower required to run them, and the needed amount of power is taken from either the pump’s voltage or its amperage. If the proper voltage is not available during operation, it will use more amperage to compensate, resulting in excess heat that can lead to motor failure.
This kind of pump failure can happen during home applications, such as the running of a water feature. If a customer needs to use an extension cord to bridge the gap between an indoor electrical outlet and an outdoor pump, voltage drop can occur. For example, a utility may provide 230 volts (V), but if an improperly sized extension cord is used, it could bring the voltage at the pump down to 190V, increasing the amperage and causing the excess heat to burn the motor out.
An analysis of this type of failure requires an examination of the burn pattern on the stator or internal motor protector, where the tell-tale signs of overheating or overamping are fairly simple to spot by a trained professional. Stator insulation that is deteriorated in all three phases is a typical sign that the pump has been running with an improper voltage. Motor protectors can shut the pump down automatically before any damage occurs. If the pump is subjected to this type of recycling over a long period, it may have a negative effect.
A burned pump motor caused by improper voltage during use.
Pumping outside the best efficiency point
Every pump has a point at which its flow becomes optimally efficient — this is referred to as the best efficiency point (BEP), which is indicated on a pump’s performance curve. Operating a pump too close to shutoff head (left of the curve) or at runout (right on the curve) can result in bearing failure, mechanical seal failure or shaft breakage. A pump should operate within 30 percent of its BEP to avoid these failures, maximizing the pump’s life span and power consumption.
Sometimes when a pump fails, a customer requests a replacement based only on horsepower. It’s possible that the previous failed pump was misapplied and not operating at the proper BEP — simply replacing it without knowing the pump’s BEP will lead to disaster as well. For example, if the user chooses a pump that is designed to create 15 feet of head, but only 2 feet of head are needed, it will not take long for the bearings to wear out. A good distributor or rental professional will let the customer know this beforehand.
Knowing a pump’s BEP is critical in the forensic process of pump failure analysis — only through pressure readings of the system or calculations of an application’s piping system can one determine this duty point. Some pump manufacturers will have engineers in-house who can create a performance report to assist customers in determining the BEP.
Water incursion into the motor
When water makes its way through to a pump’s motor, it is often assumed a manufacturing defect must have come from the factory. While this certainly can happen, more than likely the culprit is a cable that has been cut or otherwise damaged, allowing water to pass into the copper conductors and wick back into the motor.
Water can also penetrate the pump’s motor after running too long at the runout level specified by its performance curve. This is a common cause of water incursion, where radial movement of the rotor shaft causes the mechanical seal to open up slowly over time.
Chemical incompatibility can play a role as well. Pumping overly acidic or basic chemicals can erode the rubber portion of the mechanical seal, O-rings or gaskets.
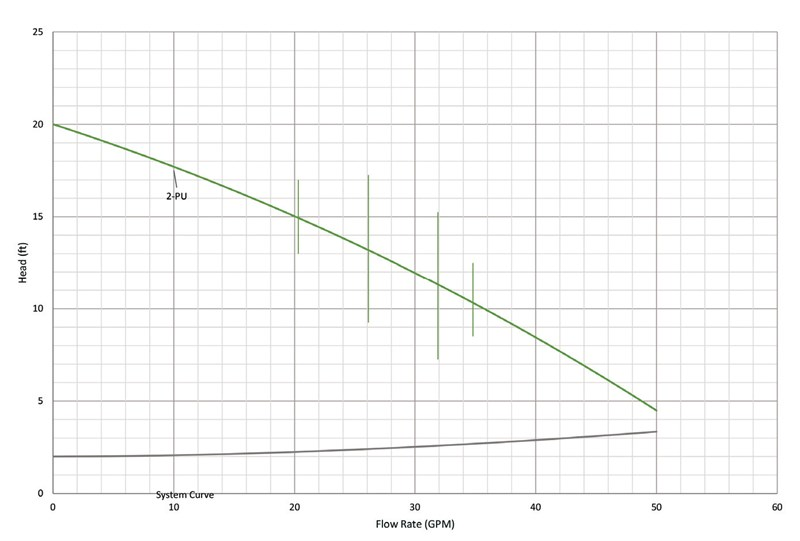
A custom pump performance report can help customers determine a pump’s best efficiency point. This report shows a system curve plotted against select pump curves. Static head: 2 feet. Pipe length: 25 feet. Pipe diameter: 2 inches
Know your pumpage
It is important to consider not only the pump itself during failure analysis, but also what exactly is being pumped. Certain dewatering pumps are designed with high chrome or urethane-lined components to handle abrasive solids, while other wastewater pumps are designed for pumping soft, compressible solids using simpler cast iron components.
Occasionally a customer will call regarding the reduced capacity of a pump. When it was first installed, it pumped great, but now he or she simply gets a trickle. As far as the customer knows, the water being pumped is perfectly clean. It is not uncommon in this situation to disassemble the failed pump and find that the impeller is worn down. Further inspection of the surrounding area reveals that the water being pumped contains high levels of silica-rich sand — this is a prime example of using the wrong pump in the wrong situation, which ultimately leads to failure.
A cut or damaged cable can lead to water incursion that corrodes the pump over time.
A matter of time
Replacing or repairing a failed pump is considered by many to be an inevitability. Much like a lightbulb in a warehouse, a pump’s failure is all but guaranteed — it is only a matter of when. With so many customers buying pumps online these days, they are not getting the expert advice or consultation on the job site firsthand, making pump failure in the home or on the job site that much more inevitable.
The good news is that with assistance from a knowledgeable engineer, rental professional or motor shop mechanic, pump failures and their analyses do not have to be a complete mystery. Having dependable assistance throughout the life cycle of a pump can often be the deciding factor in getting the job done.
Mike Klimes is an application engineer for Tsurumi America, a division of Tsurumi Manufacturing, and has more than 20 years of engineering and manufacturing experience. He is responsible for solving customer issues by offering in-depth performance analysis through the complete life cycle of pumping applications. Tsurumi America has been providing more than 35 years of leading pumping technology in construction, civil engineering, mining, industrial wastewater, domestic wastewater, sewage treatment, flood control and scenery creation fields. For more information, call 630-793-0127 or visit tsurumipump.com.