Case Description
The Proximity Hotel, located in Greensboro, North Carolina and privately developed by Quaintance Weaver Restaurants & Hotels, prioritizes comprehensive energy efficiency in its design. To that end, the hotel’s hydronic-based HVAC system uses Taco’s single pipe LoadMatch system for the project to provide an energy efficient system that would assist leed credits and one that would also meet the budget by upfront savings in installation costs, especially in piping and valves.
Summary
A new privately owned “loft style” hotel opening this month in Greensboro, North Carolina has been designed and built with energy efficiency and guest comfort in mind. Significantly, the project is going for LEED Gold certification and includes a $2.5 million TraneTaco variable flow HVAC system that will earn up to 15 points under the USGBC LEED certification process. Taco’s LoadMatch® single pipe system is a key design element in delivering energy efficiency and superior indoor comfort.
Close by the Greensboro airport, the Proximity Hotel is located adjacent to an existing landmark in contemporary Greensboro, the O’Henry Hotel, named after the famous short story writer and Greensboro native. The new Proximity Hotel is an eight story hotel with just under 150 rooms, to include 10 luxury suites. The Proximity takes its name from a former textile manufacturing facility by the same name that was located in Greensboro at the end of the nineteenth century, operated by Moses Cone, who was known in his day as the “Denim King.”
The Proximity Hotel, like the O’Henry, is owned by the same private developer, Quaintance Weaver Restaurants & Hotels. Principal Dennis Quaintance, who also operates the Lucky 32 restaurant chain in the Carolinas, wanted to build a “green’ hotel with a hydronic cooling and heating system but needed the system to meet the budgeted cost. He wanted the hotel to be LEED certified to demonstrate his commitment to the environment.
Quaintance first heard about LEED back in 2003 at a hotel industry conference. He thinks that sustainable, “green” buildings are the way to go, and he sees solid marketing value in being environmentally responsible. “LEED is the benchmark that we wanted to affiliate with,” said Quaintance. “We want to be one of the greenest hotels in America.”
He also thinks his employees will take pride in knowing that they work in a green building. “I believe most of our employees will be glad that we’re employing sensibilities that they share themselves,” said Quaintance, who, like Theodore Roosevelt, calls himself a “practical idealist.”
Beyond marketing savvy and good employee relations, Quaintance sees real long-term savings in building the most energy efficient hotel possible. Unlike other hotel developers he has no plans to sell his hotel after a few years of operation. “Most hotels are built, then stabilized, then sold,” he explained. “That’s the dominant financial model in our industry. We intend to own these hotels long term.
“That being so, energy costs mean more to us because we’re the developer and the owner. We’re able to look at things over a longer term — 10, 20 even 30 years. That’s the bet I made with this property: that energy costs will increase per increment, however you measure them, so we’re going to stay ahead of them. Better comfort at better operating costs.”
But to Quaintance, guest comfort trumps even energy efficiency. “Comfort comes first; energy efficiency second. When it comes to energy efficiency,” he said, “we wouldn’t have done anything, not one iota, if it had a negative effect on guest comfort.” Taco guarantees superior comfort with its LoadMatch system. According to Taco, hydronic-based chilled water systems provide more even indoor temperatures, better IAQ and superior comfort over DX systems, and are far easier to install and maintain, especially using a single pipe system like LoadMatch. They also provide better dehumidification, an important need in humid climates like North Carolina.
Selection of the LoadMatch system as the delivery mechanism for heat in winter and air conditioning in summer was a carefully vetted process, and was introduced to the pre-selected design-build firm for the job — Superior Mechanical, Inc. of Randleman, N.C. — by Taco and its sales representative firm for the area, Heat Transfer Sales of the Carolinas.
Superior Mechanical’s owner, Joe Millikan, had not worked with the LoadMatch system prior to this project. He was also new to the LEED process. Joe had been challenged by Quaintance to install a system for the Proximity Hotel that would be energy efficient and that would provide great comfort. “He wanted an innovative design…but, of course, we had to be budget conscious,” recalled Millikan, who has partnered with QuaintanceWeaver Restaurants and Hotels on other projects, to include the O’Henry Hotel back in 1998. “So it was a design challenge to save energy and provide the comfort that had to be there — and not break the bank doing it.”
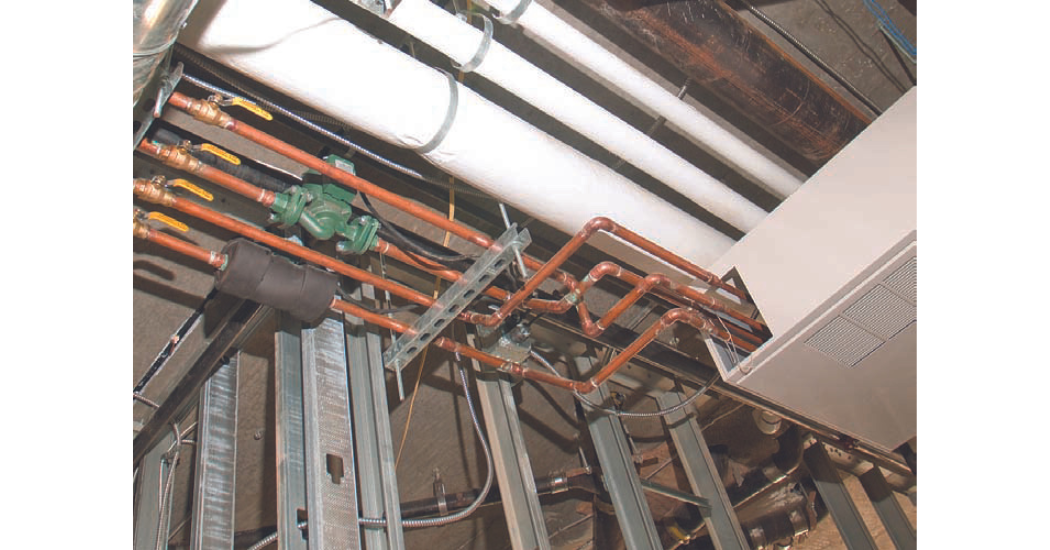
Superior Mechanical Inc. of Randleman, N.C. installed the LoadMatch system using some 350 LoadMatch circulators and Twin Tees throughout the hotel’s interior.
Final Result
“With the LoadMatch system you’re not wasting energy pushing water through two-way control valves. Plus, its upfront costs savings — we’ve eliminated about 35% of piping because we didn’t have to run hot and cold loops.”
Joe Millikan was impressed with the projected materials cost savings in less pipe needed and less need for control valves. “I don’t like control valves,” Millikan admitted. He also liked the Taco guarantee on the system itself. Working with a system design provided by Bryan Payne of Taco using the company’s HSS (Hydronic Systems Solution) software, Superior Mechanical recommended Taco’s single pipe LoadMatch system for the project to serve both owner mandates — a “green,” energy efficient system that would assist LEED credits and one that would also meet the budget by up-front savings in installation costs, especially in piping and valves.
“Taco partnered with us on the design and guaranteed us that it would work,” said Millikan. “Then we went to Dennis and sold him on the system. We had to tell him how it worked and why it was better. He dug down deep so there were a lot of questions we had to answer. That was part one. Part two was that it’s got to be better when it’s done and working.”
Mechanical design and installation of the HVAC system was overseen by Superior Mechanical. Installation of the LoadMatch system was accomplished using approximately 350 LoadMatch circulators and Twin Tees through the hotel’s interior installed with Trane-supplied fan coil units sized to run with warmer water temperatures. For each guest room in the hotel there are two LoadMatch circulators per fan coil unit in the ceiling, affording each guest total control over their room temperature using Tranesupplied thermostats. There are approximately 25 zones per floor in the hotel.
LoadMatch’s single pipe construction also meant less pipe showing along the hallways, as the hotel’s loft design comes with exposed ceilings. “The LoadMatch system is both simpler and a lot more accessible,” said Millikan. “The pumps are located outside the fan coil units so if we ever have to take care of a leak, it’s all right there — a lot easier to get to.”
The small LoadMatch circulators will also save on pump horsepower. “Pump horsepower went to practically half,” said Millikan. “We’ve saved a lot of energy because our head pressure dropped significantly – from 90 to 45 feet of head pressure.”
“With the LoadMatch system” he said, “you’re not wasting energy pushing water through two-way control valves. Plus, its upfront costs savings — we’ve eliminated about 35% of piping because we didn’t have to run hot and cold loops — and projected energy savings make it an ideal system for this project.”
The rooftop mechanical room holds two gas-fired Raypak modular boilers for redundancy along with various Taco base-mounted pumps, expansion tanks and 4900 Series air and dirt separators. The Trane chilled water system, which comes with four 50-ton multi-stack chillers, provides energy savings through its eight stages, and is also rooftop mounted for space savings. “We opted for a multi-stack chiller that has part-load efficiencies greater than full-load,” said Millikan. “As it unloads it gets more efficient.”
Humidity is not a factor. The system comes with a 24/7 ventilation system. The make-up air unit removes moisture from the outside air, delivering fresh air with a dew point of less than 50% to the guest rooms and public spaces. The system comes with a dedicated make-up air unit that takes outside air to the rooms, cools the air to 48°F, and then heats it back up to 70°F.
The hotel’s HVAC system is a variable primary pumping system. “This hotel is built with total energy efficiency in mind. We’ve got frequency drives on everything in the building, — on the cooling tower, on the pumps, even on the hood fans in the restaurant kitchen,” Millikan said.
As a future LEED-certified property, the Proximity Hotel comes with an array of solar panels (for domestic hot water) on a white membrane roof, R21 wall insulation and low co-efficient window glass, water cooled refrigeration units and lots of recycled materials. According to Dennis Quaintance, four percent of the concrete used in the hotel’s construction is recycled coal cinder from spent coal ash.
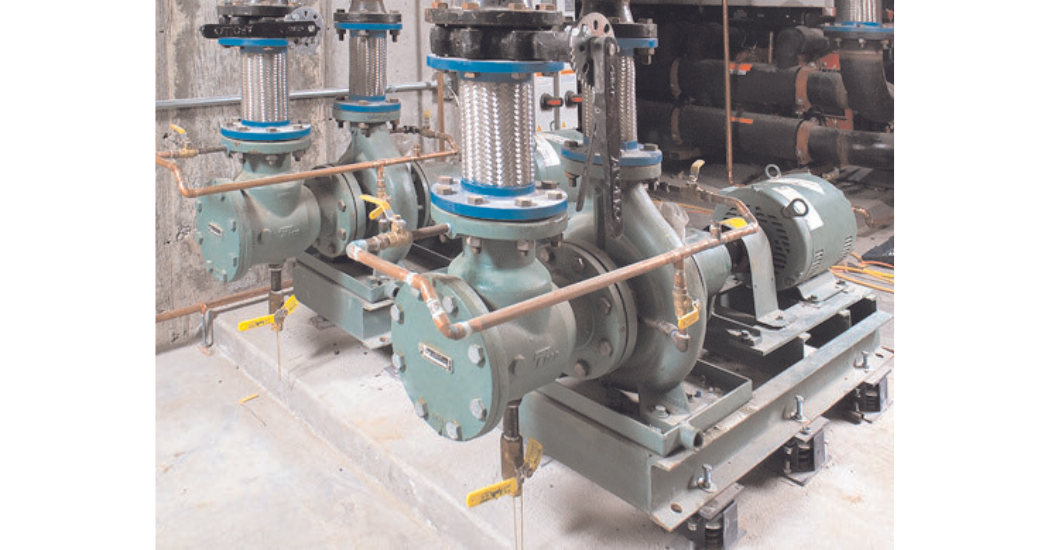
The rooftop mechanical room holds various Taco base-mounted pumps and two gas-fired Raypak modular boilers for redundancy Using small LoadMatch circulators throughout the system saves on pump horsepower, cutting hp requirements nearly in half.
Quaintance and Millikan contend that the hotel’s energy model provides better projected savings than stipulated in the ASHRAE 90.1 energy code– they predict energy consumption will be some 35% less than required by the 90.1 standard. And to the North Carolina energy code, some 50% less. “We were startled at how much efficiency, and hence comfort, you can give the guest if you just pay attention to the technology that’s available today,” said Quaintance.
Comments