Sulzer’s cutting-edge solutions for separation processes are supporting the pioneering EU-funded project ‘Steelanol’, which aims to turn carbon-rich industrial emissions into bioethanol fuels. By winning this contract, Sulzer is further strengthening its reputation in providing high-quality, reliable and innovative process engineering services and equipment for more sustainable and efficient processing plants.
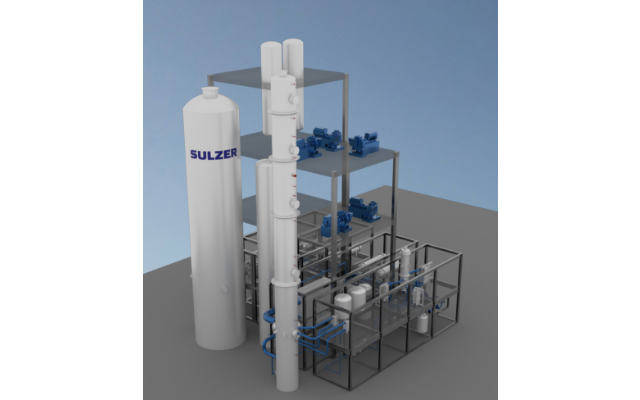
Sulzer are supporting the pioneering EU-funded project ‘Steelanol’, which aims to turn carbon-rich industrial emissions into bioethanol fuels.
Sulzer Chemtech, the leader in separation and mixing technology, was appointed by ArcelorMittal to provide distillation equipment to its steel production plant in Gent, Belgium. This will help converting waste gases from the steel manufacturing process into approximately 80 million liters of bioethanol annually.
While the steel industry is one of the biggest sources of carbon emissions, the world’s leading integrated steel and mining company ArcelorMittal is actively engaged in the Steelanol project to turn its sites into smart carbon plants. To do this, the company has partnered with LanzaTech, a developer of a biotechnology that uses acetogenic bacteria, which is able to ferment carbon monoxide (CO)-rich gases to produce ethanol.
In order to develop a suitable system to extract the biofuel after the bacterial metabolic process, it was essential to select a specialist in separation technology. Sulzer was appointed on the basis of its extensive expertise, in-depth knowledge and manufacturing capabilities for the processing industries.
The overall carbon footprint balance is a crucial aspect for Sulzer and ArcelorMittal. In fact, for a successful breakthrough process, it is necessary to reduce any energy consumption, rather than increase it. To do that, Sulzer proposed and designed a first-of-its-kind solution that simplifies the process and the equipment necessary, whilst creating closed loops that can re-use key resources and dramatically reduce energy usage.
Jacques Juvet, Head Process Plant at Separation Technology for Sulzer Chemtech, commented: “Thanks to our capabilities, we are well-placed to support such a far-sighted project. With this contract, we are partnering with ArcelorMittal and LanzaTech to create a novel integrated manufacturing plant that produces steel and ethanol on a large scale with the lowest energy consumption and wastage worldwide. In this way, we are developing key strategies to meet the most demanding carbon emission mitigation policies.”
About Sulzer:
Sulzer’s core strengths are flow control and applicators. We specialize in pumping solutions and services for rotating equipment, as well as separation, mixing and application technology.
The Chemtech division is represented in all important industrial countries and sets standards in the field of mass transfer and static mixing with its advanced and innovative solutions. The product offering ranges from process components to complete separation process plants. The customer support covers engineering services for separation and reaction technology and tower field services to perform tray and packing installation, tower maintenance, welding, and plant turnaround projects. Our customers benefit from a network of over 180 production and service sites around the world. Sulzer has been headquartered in Winterthur, Switzerland, since 1834. In 2017, we achieved sales of roughly CHF 3 billion with around 14’700 employees. Our shares are traded on the SIX Swiss Exchange (SIX: SUN). www.sulzer.com
About ArcelorMittal
ArcelorMittal is the world’s leading steel and mining company, with a presence in 60 countries and an industrial footprint in 18 countries. Guided by a philosophy to produce safe, sustainable steel, we are the leading supplier of quality steel in the major global steel markets including automotive, construction, household appliances and packaging, with world-class research and development and outstanding distribution networks.
Through our core values of sustainability, quality and leadership, we operate responsibly with respect to the health, safety and wellbeing of our employees, contractors and the communities in which we operate.
For us, steel is the fabric of life, as it is at the heart of the modern world from railways to cars and washing machines. We are actively researching and producing steel-based technologies and solutions that make many of the products and components people use in their everyday lives more energy efficient.
We are one of the world’s five largest producers of iron ore and metallurgical coal. With a geographically diversified portfolio of iron ore and coal assets, we are strategically positioned to serve our network of steel plants and the external global market. While our steel operations are important customers, our supply to the external market is increasing as we grow.
In 2017, ArcelorMittal had revenues of $68.7 billion and crude steel production of 93.1 million metric tonnes, while own iron ore production reached 57.4 million metric tonnes.
ArcelorMittal is listed on the stock exchanges of New York (MT), Amsterdam (MT), Paris (MT), Luxembourg (MT) and on the Spanish stock exchanges of Barcelona, Bilbao, Madrid and Valencia (MTS).