Installing modern materials and design upgrades through retrofit projects in chemical plants
Modern chemical manufacturing plants depend on numerous important assets for reliable operation to maintain productivity. Retaining legacy equipment is a cost-effective way to minimize capital expenditure, provided efficiency and reliability can be upheld. The implementation of retrofit projects allows modern materials and parts manufacturing techniques to update existing components extending the asset’s service life.
In many cases rotating equipment, such as steam turbines, generators, pumps, compressors and expanders, make up an important part of the production process. Through continued use, components wear and clearances increase, leading to reduced efficiency. At the same time, processes change and greater productivity may be expected from the legacy equipment; tackling these challenges successfully can reduce operating costs and improve reliability.
Pharic Smith, Head of Engineering, Parts Retrofit at Sulzer explains how many areas of a modern chemical manufacturing plant can benefit from retrofit projects.
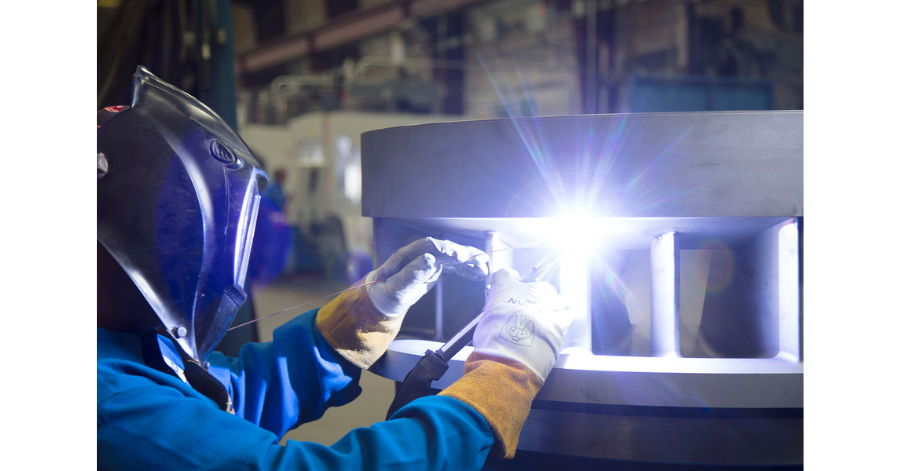
Custom manufacturing of new components can reduce lead times
Optimizing uptime
The chemical manufacturing sector offers many challenges, not least the operational environment, working with corrosive materials as well as steam can increase the pressure on the maintenance team. Working with equipment that has been in service for many years, especially when there is no support available from the original equipment manufacturer (OEM), means alternative solutions have to be found when repairs and upgrades are required.
Tight production schedules mean that downtime has to be minimized so, using a planned maintenance program is always preferred to prevent unexpected failures that can cause lost revenue. While on-site maintenance teams are often well-versed in the operation of the equipment – expert support can reduce repair times and deliver cost-effective solutions for more complex repairs.
To maximize the original investment in equipment, the service life needs to be extended as far as economically possible. Retrofit projects offer the opportunity to upgrade or replace components that can increase performance through improved design or materials.
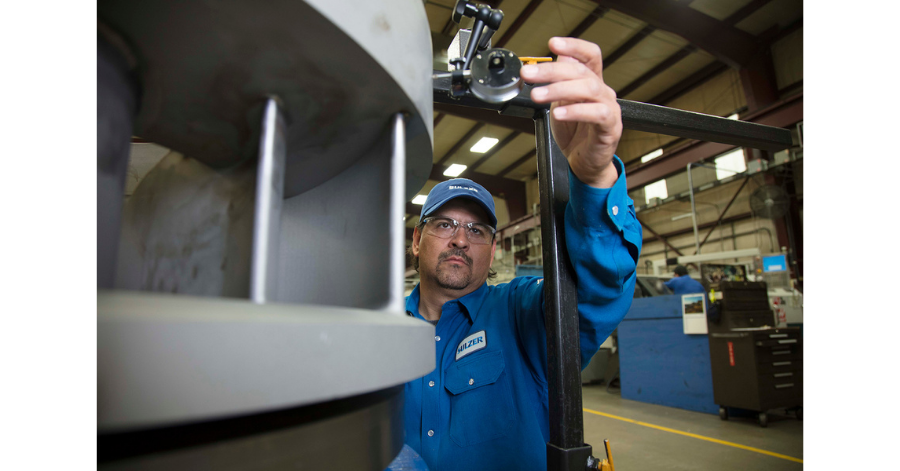
Precision fit of gas turbine parts increases efficiency
Cost-effective solutions
Large-scale pumps are often cited for retrofit projects because a life of continuous operation can lead to wear of the impellers/rotors, which reduces efficiency and increases running costs. Those operating in the chemical manufacturing industry may have to endure a challenging working environment.
For example, nitric acid, which is an essential raw material for the manufacture of fertilizer, is created using inexpensive components, ammonia, water and atmospheric air. However, the manufacturing process is very energy and capital intensive, using several turbomachines such as compressors, pumps, tail gas expansion turbines and several large motors. It is, therefore, important for manufacturers to maintain a high level of efficiency for the process to remain profitable.
Rather than replacing complete assets when their productivity starts to drop, it is far more cost-effective to repair the worn component and even improve its design at the same time. Modern 3-dimensional (3D) laser scanning technology means that the original OEM drawings are not required; parts can be created from the original component, even if it has been damaged.
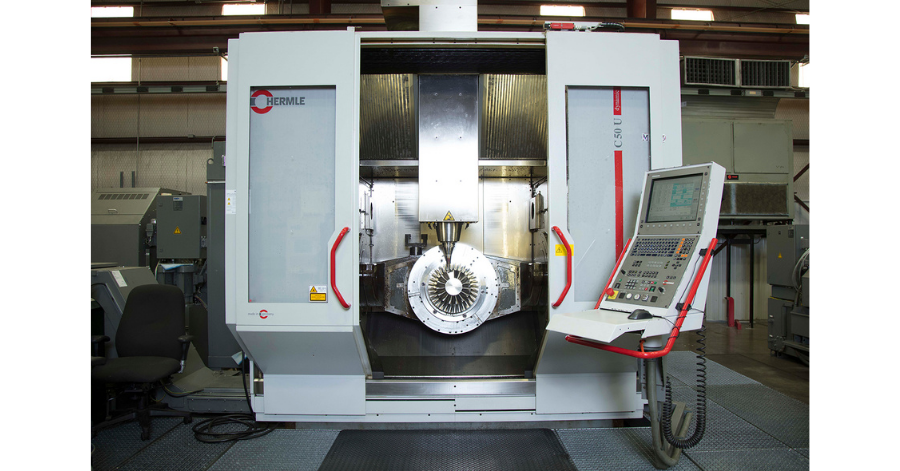
Modern machine tools can reduce the lead time on new, optimized components
Boiler feed pumps
Many manufacturing plants use steam to generate their own electricity supply and these systems rely on boiler feed pumps to deliver a consistent water supply. In many cases these important assets can perform reliably for decades, but reduced efficiency will take its toll on cost of operation. However, after so many years, the OEM may not be in a position to supply new parts, so an alternative solution is needed.
Today, seal improvements and efficiency upgrades through non-metallic wear parts and improved rotor designs can be created and manufactured using state-of-the-art equipment. Modern design processes and additive manufacturing techniques can greatly reduce the lead-time for new parts.
Retrofit programs can go much further and alter the output of the asset where demand from the pump has changed over the years. By changing impeller profiles or reducing the number of stages, the pump can be optimized for its current application, often reducing the power requirements and reducing running costs.
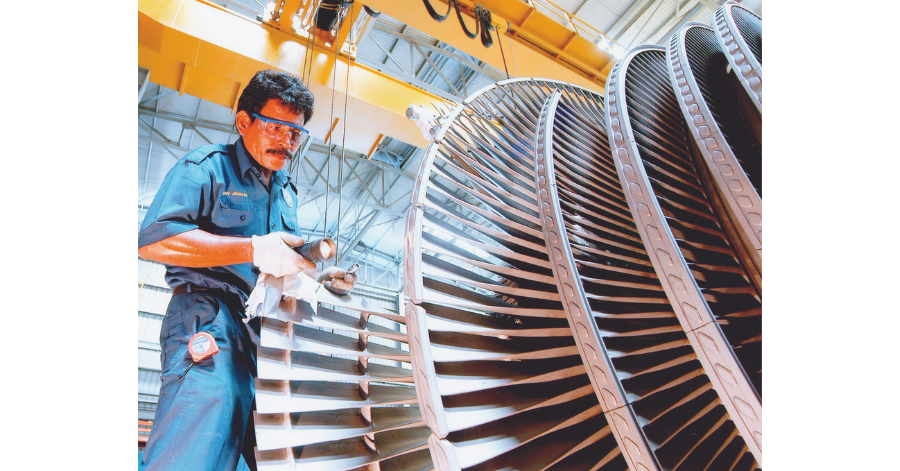
Steam turbine reliability can be improved through retrofit projects
Compressors
Large compressors are commonplace in the chemical manufacturing sector and they often operate around the clock. As such, reliability and efficiency are very important, so rigorous maintenance schedules and condition monitoring equipment are usually in place.
In many cases, compressor operators hold spare rotors that can be exchanged quickly, minimizing downtime and allowing more time to refurbish the rotor that has been in service. However, this procedure does not enable time to access to the stationary section of the compressor, which may also need attention during an overhaul or a retrofit project.
This can be mitigated by using laser scanning technology and by creating a 3D CAD model of the rotor and the casing. By combining the two, and using cutting-edge technology, a performance chart for the 3D model can be generated. This can be compared to the actual data from the compressor itself and used to refine the model until it is a true representation.
Modeling improvements
From this point designers can introduce improvements to the model and establish their influence on output and efficiency. Changes in impeller profiles, enhancements to bearings and labyrinth seals, can all be simulated and evaluated to establish to most beneficial designs.
Modern manufacturing and machining technologies can be applied to not only reduce lead times, but also create more efficient components, such as impellers with 3D vane geometry. These can all be used to improve performance and increase the mass flow rate if necessary.
The advantage of the theoretical 3D CAD is that the suggested improvements can be trialed and assessed for their impact on other components, such as the intercoolers. In some cases, upgrading the ancillaries can be justified for the increased output. Furthermore, the data can all be examined to enable a more informed decision.
Hot gas expanders
With such huge amounts of energy involved in chemical manufacturing, any method of recovery needs to be properly maintained to maximize its benefit. The operational environment of hot gas expanders means that they are subject to challenging conditions with considerable stresses put on the rotor and its bearings.
Rotating at speeds up to 11’000 rpm, the rotor needs to be supported by bearings that can withstand the operational stresses and provide long-term reliability. A retrofit project can upgrade the cylindrical sleeve bearings to tilt pad components. Spherical seated bearings can be replaced with a design using cylindrical rollers, offering better long-term performance.
The rotor itself has a multi-stage design where a hollow shaft with internal cooling passages holds the turbine disks and blades in position with a single thru-bolt. This bolt is subjected to considerable thermal stress and is often machined from stainless steel in the original build specification.
The part can be upgraded to 450 stainless steel alloy that allows increased bolt stretch and greater bundle crush on the rotor assembly. The dimensions are machined to exactly match the original using the 3D CAD drawings and can be installed as part of a rotor refurbishment.
Improved blade performance
Hot gas expanders can also benefit from a reduction in blade tip leakage, which accounts for substantial losses in efficiency in legacy equipment. Installing an abradable coating on the stator inner surface provides improved clearance control for the rotor blades. Clearly this sort of upgrade requires the expander to be under maintenance for an extended period, so is best suited to a planned shut-down period.
Further improvements can be achieved by upgrading the materials used to manufacture the blades themselves. In applications requiring high strength and good corrosion resistance up to 1’300 °F (700 °C) the use of a superalloy, such as A286, in the blades can be beneficial.
Of course, with turbine blades operating in high-temperature environments, gas turbines have several characteristics in common with gas expanders, and as such, similar technologies can be applied to both. Developments in blade coatings can reduce fouling and oxidation in both the rotating and stationary sections.
Gas turbines
Important pieces of equipment, such as gas turbines can provide both primary and back-up power supplies, so, their reliability is paramount. Over time, design improvements have been developed both by the OEMs and independent maintenance providers and these can be applied to the installed equipment through retrofit projects.
For example, in the Siemens V-Series gas turbines, the flame tube F-ring has a tendency to oxidize and produce scale that can be ingested by the turbine during normal operating conditions. To improve this situation, the component can be machined to expose fresh material and allow an Inconel overlay to be welded to the new surface before being machined back to the required diameter. Inconel 82 is a nickel-chromium alloy with high strength and an outstanding corrosion resistance that will improve the durability of the component.
Similarly, the combustion section of the gas turbine can be protected with a thermal barrier coating (TBC) applied to all of the flame tubes and other hot gas path components. A ceramic TBC applied to the bezel rings and segment plates, mixing elbows and inner casing, increases the resistance to thermal distress in the hottest areas of the unit.
Other improvements can be made to the cooling performance of certain parts, such as the flame tube, to increase durability of the parts by reducing oxidation and erosion. Together, all of these improvements can extend reliability and ensure continued efficiency of the gas turbine.
Meeting new standards
As legacy equipment continues to deliver reliable service, modern standards evolve for the benefit of the environment and the improvement of operation and efficiency. Many of these can be applied retrospectively, and it is often quicker and more cost-effective to modify existing machinery, rather than replacing it with new equipment.
Understanding what can be achieved by a retrofit project and how best to apply it, are important skills that are gained through experience in both the industry in question and in developing state-of-the-art solutions. By developing theoretical models and fine-tuning the design, engineers can highlight the benefits and ensure that the equipment is suitable for refurbishment.
The ability to improve efficiency and reduce energy consumption through modern engineering also offers the opportunity to reduce the environmental footprint of the business. As more pressure is placed on industrial plants to improve the environmental impact of their operations, so the retrofit project has the potential to deliver both a cost and CO2 emission reduction.
Reaping the benefits
Every piece of plant equipment presents its own challenges, but it is possible to address many of them by working with experienced engineers who understand the demands of the process as well as the design of the equipment involved. Using a well-defined and integrated upgrade program can deliver significant improvements to the expected service life of the equipment as well as improving productivity.
Retrofit projects represent an opportunity for the cost-effective and efficient introduction of new components that use modern materials and manufacturing techniques. The ability to create one-off parts quickly, without OEM drawings, minimizes downtime and ensures a successful turnaround during a planned outage.
By making significant improvements in efficiency and reliability, chemical plants can reduce their CO2 emission by making better use of the energy-from-waste gases, which in turn reduces the amount of energy that is required from steam powered generators. Independent service providers can offer expertise in reducing losses, improving turbine performance and upgrading rotating equipment, enabling chemical manufacturers to see enhanced performance and improved life-cycle costs.
About Sulzer:
Sulzer is a global leader in fluid engineering. We specialize in pumping, agitation, mixing, separation and application technologies for fluids of all types. Our customers benefit from our commitment to innovation, performance and quality and from our responsive network of 180 world-class production facilities and service centers across the globe. Sulzer has been headquartered in Winterthur, Switzerland, since 1834. In 2019, our 16’500 employees delivered revenues of CHF 3.7 billion. Our shares are traded on the SIX Swiss Exchange (SIX: SUN).