FS – Fueling Sustainability, located near Lucas do Rio Verde, Mato Grosso, is the first corn-only ethanol plant in Brazil. The phase 1 production started in 2017 with an initial capacity of 250 million liters per year. The facility utilizes the latest process technologies from ICM, an innovative company headquartered in Colwich, KS, USA that has become a world leader in biorefining technologies and processes. In addition to bioethanol, some high-value coproducts such as corn oil as well as high-protein and high-fiber dried distiller’s grains are produced. The plant also generates electricity from the biomass, partly for internal use and the surplus for sale.
FS – Fueling Sustainability is recognized as the most modern and efficient corn ethanol plant in the world. The production facility is equipped with top-class pumping equipment from Sulzer and value-added, patented technologies from ICM such as Selective Milling Technology™ (SMT™), Fiber Separation Technology™ (FST™), and Base Tricanter System™ (BTS™).
The Challenge
Each step of ethanol production from corn involves pumps with technically demanding applications. The liquids can be complex, have high solids contents, be viscous, corrosive, hot, erosive, or explosive. The right pump materials and optimal sealing systems must be carefully selected to ensure reliable and long-lasting operation. Furthermore, all pumps must be highly efficient, both in terms of energy and water savings, so that the complete plant is operating to its full potential.
The Solution
In close cooperation with the customer, we chose AHLSTAR and SNS pumps for all applications – from initial mash slurry transfer to final ethanol truck loading. In total, more than 80 single-stage pumps were installed for phase 1. The AHLSTAR pumps in duplex material are handling liquids containing solids and other particles, while the SNS pumps are running on clean liquids. Most of the pumps are equipped with double mechanical seals.
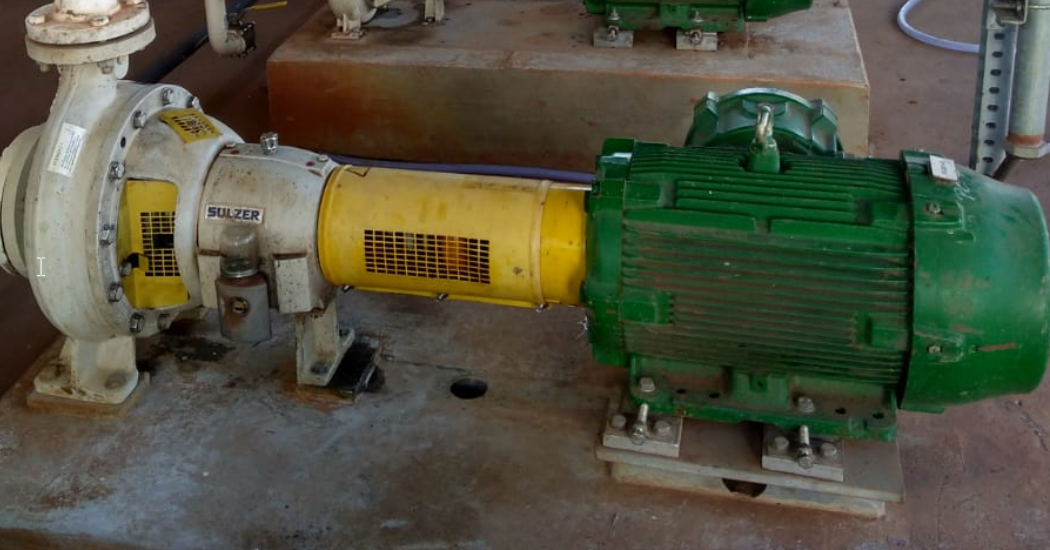
SNS3-80 pumping unit for anhydrous ethanol
Customer Benefit
Sulzer has thorough experience in pumping solutions for corn-based ethanol plants worldwide. In the United States alone, more than 200 plants are in operation today, and about 70% of them are equipped with Sulzer pumps. Our successful references strengthened the confidence of the client from the very beginning of the project.
After careful commissioning and start-up, all pumps have been working perfectly. For the toughest applications, the AHLSTAR pumps with adjustable side plates provide high performances continuously. For clean liquids, the new SNS pumps simply have the highest efficiencies on the market – they exceed the benchmark efficiency index MEI 0.7.
Both the AHLSTAR and the SNS pumps have open impellers with balancing holes that optimize the shaft seal function. For pumps with double mechanical seals, it was decided after a few months’ operation to switch from API piping plan 54 (external pressurized source) to API piping plan 53 (external pressurized reservoir). This change helped to further reduce the water consumption and operational costs. The versatility of the pumps and the dedicated Sulzer service technicians made this upgrade easy and fast.
During 2018, a duplicate of the existing plant was built (phase 2). This doubled the production capacity of the Lucas do Rio Verde site. Extremely satisfied with the collaboration, FS – Fueling Sustainability ordered new similar Sulzer pumps for this extension. The site was further expanded in 2019 (phase 3) with additional Sulzer equipment installed. Today, in total more than 300 AHLSTAR and SNS pumps are running smoothly in the plants.
“Top-efficiency. Not only for pumps, but also for service provided throughout the project.” Júlio César Santana, Project Manager, FS – Fueling Sustainability
Product Data
The corn ethanol site has a total of 307 Sulzer single-stage process pumps in duplex or stainless steel 316 materials. Most AHLSTAR pumps with double seal are equipped with the simple and reliable Sulzer thermosiphon SP8 seal pot system. The AHLSTAR and SNS pump ranges have a wide choice of wet end sizes to cover exactly the required flows (2 to 1’230 m³/h) and heads (4 to 105 m). This allows the pumps to always run at duty points close to the best efficiency points, which means direct and maximized savings in energy costs.
The Sulzer plus
• Recognized supplier in the biofuels market
• More than 20’000 single-stage process pumps installed in bioethanol production plants worldwide.
• Close cooperation with the customer during the whole life cycle of the equipment
• AHLSTAR and SNS pumps for demanding bioethanol applications ensure minimum power consumption, trouble-free operation, and reduced maintenance.
About Sulzer
Sulzer is a global leader in fluid engineering and chemical processing applications. We specialize in energy-efficient pumping, agitation, mixing, separation, purification, crystallization, and polymerization technologies for fluids of all types. Our solutions enable carbon emission reductions, development of polymers from biological sources, recycling of plastic waste and textiles, and efficient power storage. Our customers benefit from our commitment to innovation, performance, and quality and from our responsive network of 180 world-class manufacturing facilities and service centers across the globe. Sulzer has been headquartered in Winterthur, Switzerland, since 1834. In 2022, our 12’900 employees delivered revenues of CHF 3.2 billion. Our shares are traded on the SIX Swiss Exchange (SIX: SUN). www.sulzer.com