Improving efficiency by developing pumps for higher temperature systems
The technology to exploit renewable energy sources is continuing to advance, improving efficiency and reducing costs. In concentrated solar power plants with central tower and molten salt, the sun’s energy is used to raise the temperature of molten salts, which are pumped to a steam generator that powers a turbine. The efficiency of this process can be improved if the working temperature is increased and this has led to a large-scale project to develop the corresponding pump technology.
Claude Mockels, Product Development Manager at Sulzer, looks at the design of pumps in these challenging applications and how the next generation will cope with temperatures above 700 °C (1’300 °F).
High temperature salt pumps are primarily used in nuclear and solar power generation as well as chemical and salt manufacturing. These pumps are currently used at temperatures up to 600 °C (1’100 °F), but now designers are looking at extending the current limitations and creating pumps that can be used in applications where even higher temperatures can be beneficial.
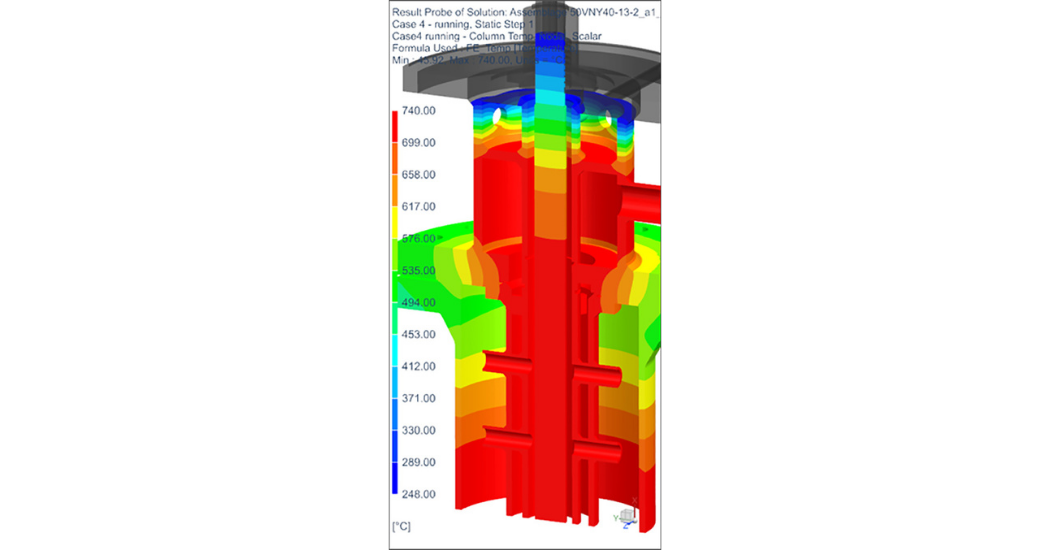
Sectional drawing of Sulzer VEY Molten Salt Pump
Raising the bar
In large-scale solar plants, mirrors focus the sun’s energy to a central tower where it is used to increase the temperature of the molten salts. Pumps are used to transfer molten salts from the ‘cold’ tank through the pipes to a hot salt tank and on to a steam generator. The steam powers a turbine, which turns a generator and produces electricity for the local grid.
For renewable solar energy plants, efficiency can be improved by increasing the temperature of the salt used to store the sun’s energy. Until recently, various salts have been used at temperatures around 600 °C (1’100 °F) and the pumping technology for this application is well-established. The plan is to increase the working temperature for new systems beyond 700 °C (1’300 °F).
At these temperatures, molten chloride salt has to be used, but this presents additional issues, such as its corrosive properties, that are not a problem with 600 °C pumps, which operate with more benign salts. The existing second generation pumps have many proven design characteristics that now need to be extended.
The next generation
For the next phase of more advanced solar plants, third generation pumps are in development, with projects being funded by the Department of Energy (DoE) in the United States and other organizations in Europe. Work is underway to establish the materials and components that need to be upgraded to enable this project to be successful.
Sulzer, has been supplying components to the solar industry since 1984 and has pioneered the market in molten salts pumps. The company, which has a wide-ranging expertise in pump design and manufacturing, has a long-standing portfolio of molten salt pumps. These are vertical mixed-flow pumps that have proven hydraulics and are engineered to meet the requirements of this demanding environment.
Both designers and product developers are working together to develop new materials for wear components that will be used in this arduous environment. One group of high-toughness, ceramic-metal composite materials, known as cermets, will be used to manufacture strong, long-lasting components, such as bearings and sealing elements.
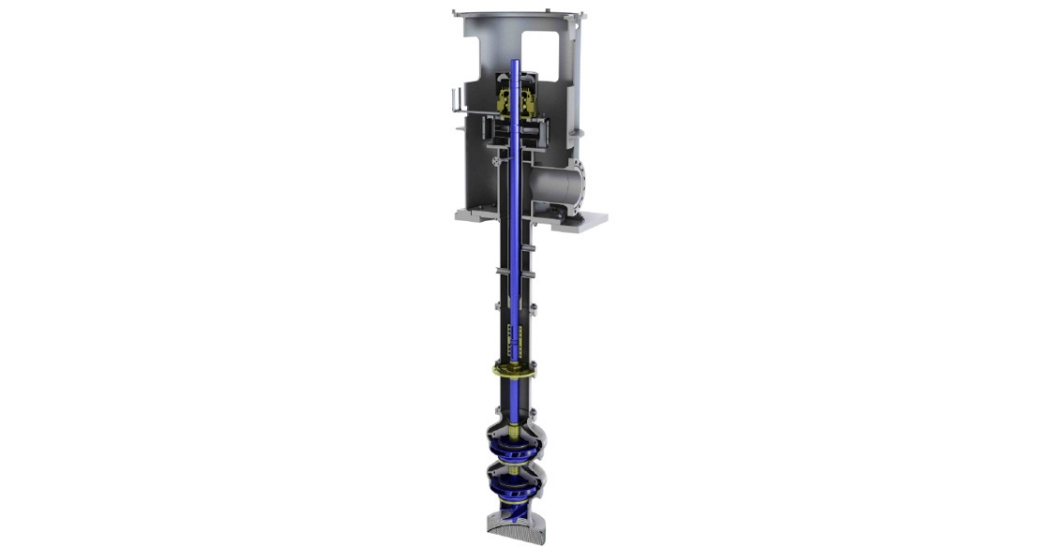
Thermal analysis results performed on Sulzer Gen 3 Molten Salt Pump
Material evaluation
To overcome this challenging application, the materials need the correct mechanical properties as well as temperature and corrosion resistance. The mechanical properties of any material must also be sufficient to handle the energy required to drive these pumps; driveshafts must be capable of delivering the torque necessary to pressurize the system.
The pump design must take account of the thermal expansion of the pump components to ensure clearances are maintained. This is an important consideration for mechanical parts such as press-fit bushings, where clearances and axial elongation are important for reliable operation of the plant.
Theoretical modeling
At the heart of any design for a pump that will operate in such a hostile environment is the computer model. Although parts that are in contact with the molten salt will be designed to handle the elevated temperatures, other parts need to be kept cool to ensure optimum performance.
The huge variations in temperature distribution have a significant effect on the mechanical design of the pump. The theoretical model helps the engineers to understand this distribution and to develop both materials and a physical design for the pump.
Heat radiation must also be examined as well as ensuring that components not in contact with the molten salt, such as the electric motor and the top bearing, remain cool. Sulzer uses a sophisticated thermal model to examine the differences between the current designs and those required for the next generation. This has led to refinements of the cooling system which will be important in creating a reliable pump with a long service life. The numerical model will then be compared to the real-world results that are obtained from the pilot project.
Seal design
Together with the University of Wisconsin-Madison, Sulzer’s design team will validate the manufacturing processes and evaluate the performance of the pump at these elevated temperatures. The goal is to establish a design and prove its performance in an environment that will be even more challenging than before.
As with any pump, the seals play an important role, but the materials and physical design must withstand the rigors of the application. In this case, a floating ring seal, a similar system to the existing design, will be implemented for the third generation pump.
Cost-effective solution
Using Sulzer’s expertise and knowledge in hot salt pump design, the research team is tasked with building and testing a corrosion-resistant pump and related components. The prototype will be used to evaluate performance and the manufacturing processes used to create it.
The data collected from this trial will enable the costs of a pilot plant to be estimated and establish the effectiveness of using cermets or other alternative hardfacings for high temperature solar applications. In addition, the project will highlight the durability of the pump design and predict the wear of components that are exposed to molten salt.
The aim is to refine the materials required for a process that will improve the efficiency of solar power generation. The need for high temperature performance as well as excellent corrosion resistance and manufacturability to achieve this goal, will undoubtedly lead to a new generation of pumps that will serve the industry for years to come.
First published in the June 2021 issue of Pump Engineer Magazine.
About Sulzer:
Sulzer is a global leader in fluid engineering. We specialize in pumping, agitation, mixing, separation and application technologies for fluids of all types. Our customers benefit from our commitment to innovation, performance and quality and from our responsive network of 180 world-class production facilities and service centers across the globe. Sulzer has been headquartered in Winterthur, Switzerland, since 1834. In 2020, our 15’000 employees delivered revenues of CHF 3.3 billion. Our shares are traded on the SIX Swiss Exchange (SIX: SUN).www.sulzer.com. Our shares are traded on the SIX Swiss Exchange (SIX: SUN). www.sulzer.com. The Pumps Equipment division specializes in pumping solutions specifically engineered for the processes of our customers. We provide pumps, agitators, compressors, grinders and screens developed through intensive research and development in fluid dynamics and advanced materials. We are a market leader in pumping solutions for water, oil and gas, power, chemicals and most industrial segments.