Aeration systems are among the biggest energy consumers in a wastewater treatment facility and they can be a maintenance challenge too. To keep costs under control, plant operators have a choice of designs to upgrade to blowers that run efficiently and reliably under all expected operating conditions.
Edward Paro, Portfolio Manager Compressors & Aeration for Sulzer, looks at different blower technologies and how to improve the reliability and efficiency of legacy plants.
Modern diffused aeration systems have transformed the design of wastewater treatment facilities. Capable of operating in deep tanks, these systems allow operators to process more water in less space. They can run for multiple years with minimal maintenance and, with the right control systems, they can manage the highly variable demand experienced by many municipal and larger industrial sites.
To deliver these benefits, every system requires a reliable, efficient supply of air. The blower systems used to supply the air occupy a niche place in the spectrum of industrial and commercial air handling equipment. They operate at higher pressures than the fans used in HVAC applications, but must deliver larger volumes of air than typical industrial compressors. At the same time, in order not to risk breaching regulations and permit requirements they need to offer high levels of availability. They need to work efficiently while also being quiet and easy to control.
Volumetric blowers
Some blower designs operate using volumetric principles. Air is drawn into a chamber which is then reduced in size, squeezing the air to boost its pressure before releasing into the outlet pipework. Rotary lobe blowers, also known as Roots blowers, achieve this with two interlocking rotors that spin in opposite directions.
Roots blower technology was introduced in the 1800s. It remains largely unchanged to this day and is still widely used in wastewater applications, especially in Europe. These blowers are simple, reliable and require little maintenance. Their efficiency is limited by not having a reducing chamber built-in, but rather pushing the air into the discharge.
In addition, as all volumetric designs’ efficiency is held back by the need for small gaps between the parts, some air will escape back into the inlet, some of it will leak to the outside through seals and some of the already pressurized air may leak to a less pressurized part. The design also produces pulses of air, making these blowers noisy in operation and creating vibration in the discharge pipework and its components.
Another volumetric compression approach that has become popular in recent years is the rotary screw blower. This uses interlocking male and female helical rotors that rotate to decrease the available volume between them. At the start of the compression cycle, the inlet air fills the flute space and becomes trapped. The air is then continually compressed as the male and female components rotate with each revolution until the air is pushed through the discharge outlet.
Compared with traditional lobe blowers, the way air is internally compressed in rotary screw blowers reduces energy consumption by 30%. Screw blower noise levels are typically lower than conventional tri-lobe Roots blowers. The pipework noise is somewhat reduced because the output is continual rather than pulsed.
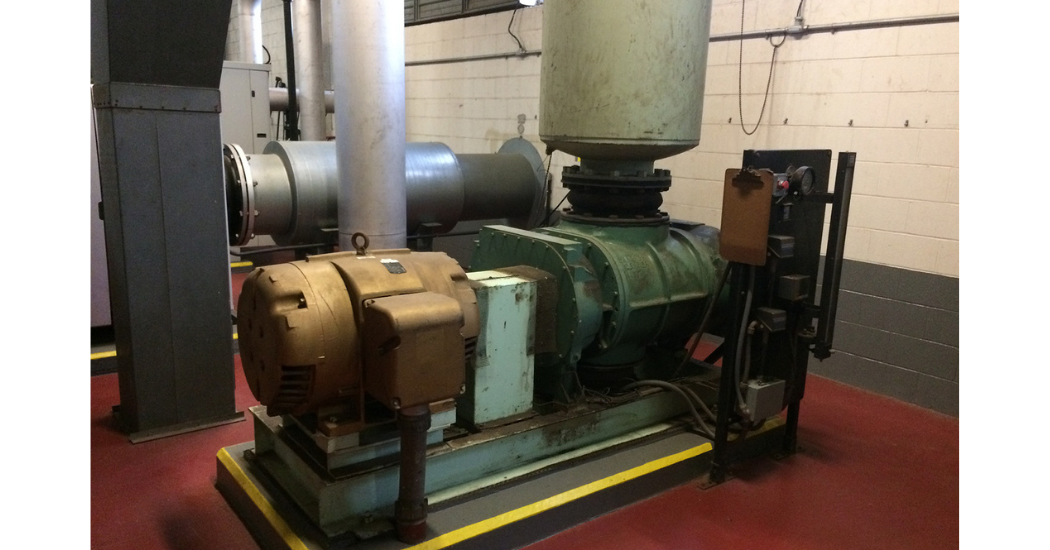
In the past rotary lobe blowers, also known as ”Roots” blowers, were a popular selection for waste water aeration.
Kinetic blowers
Compression can also be achieved by changing the velocity of the air rather than its volume. Centrifugal blowers do this using a rapidly spinning impeller. Air is drawn in close to the center of the impeller, turned through 90 degrees and accelerated as it is thrown outwards by the rotating blades. Multi-stage centrifugal blowers, commonly used in U.S. wastewater treatment plants, mount several impellers on the same shaft, with air moving from one to the other, increasing its pressure as it goes.
The output of a single stage centrifugal blower depends upon the size of the impellers and their rotational speed. To avoid large, heavy and expensive impellers, this type of blower often includes a gearbox to speed up the rotation of the motor. That has downsides, however, including friction losses, a larger number of wearing parts and the need for additional maintenance and overhauls.
An alternative to mechanical gearboxes is the use of a variable frequency drive (VFD) and a high speed motor to run a small impeller at very high rotational speeds. “Turbo blower” designs, such as Sulzer’s HST™, are mechanically optimized and highly efficient, with a design that utilizes specialized bearings to cope with the elevated speeds.
The magnetic bearings used in Sulzer HST turbo blowers ensure there is no metal-to-metal contact between the shaft and the bearing. These systems eliminate mechanical wear, extending the life of the blower and their ability to support the shaft from zero speed keeps the HST efficient and wear-free through frequent on-off cycles.
Turndown requirements
The air demand in a wastewater treatment process can vary significantly depending on the volume of water entering the system. Optimum performance requires the ability to adjust blower output as conditions change. Volumetric blowers can typically “turndown” to 30% of their full output; reducing the speed of the motor reduces the output of the blower and the energy consumed by the system. Multi-stage centrifugal compressors have a narrower operating range, allowing turndown to 60% or 70% of full output before efficiency begins to drop off significantly. Single-stage centrifugal blowers using adjustable vanes at the inlet and/or outlet and high speed turbo compressors using variable speed operation can reach between 30-50% turndown from maximum flow, depending on pressure.
For applications where demand varies beyond the turndown capabilities of a single compressor, operators usually install multiple units, switching them on or off in sequence, according to demand. This approach optimizes energy efficiency and improves the overall availability of the system, since spare capacity is available outside peak times should a blower be unavailable.
Reducing maintenance costs
The different types of blowers will call for different types of maintenance. The gear box of the single-stage centrifugal blower will need regular attention according to a strict service and maintenance program. The screw blower design will need to be checked regularly in order to avoid costly breakdowns and often an exchange of the core elements can be expected at some point.
The Roots type of blower is often not cared for properly and hence is prone to seizing up. If that happens, it is usually repairable but may lose significant volumetric tightness and as a result efficiency will suffer. High-speed designs with magnetic bearings do not have wearing parts and the HST turbocompressor is unique in not containing any liquid. This limits physical maintenance tasks to checking and exchanging air filters.
Introducing more efficient and more reliable blowers can have a significant benefit to the operational and maintenance budgets. For example, in one case where HST blowers were introduced, maintenance costs were reduced by 95% while in another, energy costs were reduced by 30%. One installation saved EUR 12’000 per blower in annual maintenance costs. In fact, the installation of four HST units at one site in Europe saw the combined energy and maintenance costs drop by EUR 175’000 per year.
In municipal wastewater treatment applications, Sulzer often installs 10 to 15 HST turbo blowers at a single site. Some recent large-scale projects have involved up to 40 units. In each case, their efficiency as well as their reliability have surpassed expectations and treatment plants have made considerable savings in terms of operational and maintenance costs.
About Sulzer:
Sulzer is a global leader in fluid engineering. We specialize in pumping, agitation, mixing, separation and application technologies for fluids of all types. Our customers benefit from our commitment to innovation, performance and quality and from our responsive network of 180 world-class production facilities and service centers across the globe. Sulzer has been headquartered in Winterthur, Switzerland, since 1834. In 2020, our 15’000 employees delivered revenues of CHF 3.3 billion. Our shares are traded on the SIX Swiss Exchange (SIX: SUN).www.sulzer.com Our shares are traded on the SIX Swiss Exchange (SIX: SUN). www.sulzer.com. The Pumps Equipment division specializes in pumping solutions specifically engineered for the processes of our customers. We provide pumps, agitators, compressors, grinders and screens developed through intensive research and development in fluid dynamics and advanced materials. We are a market leader in pumping solutions for water, oil and gas, power, chemicals and most industrial segments.
Comments