Working through a framework agreement ensured high quality repairs were delivered on time, extending the service life of vital pumping assets at a power station. Sulzer’s combined resources and expertise also delivered overhaul projects for high voltage motors at the facility.
Adrian Larmour, International Sales Manager for Sulzer UK, explains how a framework agreement can streamline maintenance projects.
Electricity plays a vital role in everyday life, powering industrial and domestic equipment. Meeting this demand requires careful management of the assets involved in producing electrical power. Coordinating generating capacity with maintenance requirements is a delicate balancing act, and one that benefits from minimal downtime.
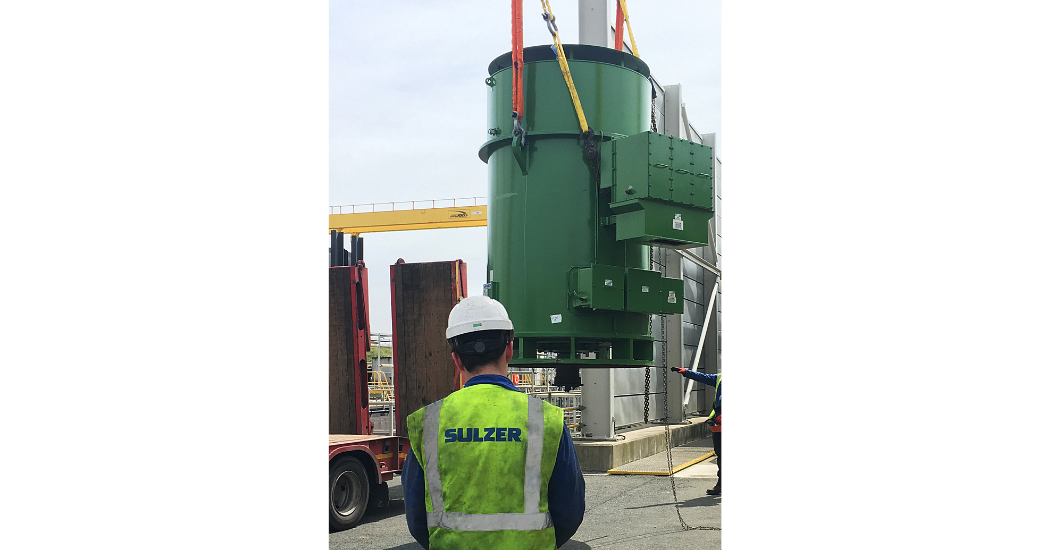
Sulzer removed and installed the pumps as part of the project
Quality and time optimization
The power generation industry appreciates the advantages of high-quality workmanship in prolonging asset performance and increasing reliability. One of the procedures used to minimize delays and optimize maintenance tasks is the framework agreement. This establishes a short-list of suppliers that have shown they meet the required standards for workmanship, health and safety as well as management procedures and cost efficiency.
At the same time, a scale of costs can be agreed between the two parties, enabling the customer to have an accurate understanding of the costs involved in a wide variety of projects. As an approved supplier, Sulzer can be asked to quote for maintenance projects in the knowledge that they have already met the necessary criteria. This can reduce the time to repair important assets and maintains the high standards of the generating plant.
Another example of time optimization is to remove large assets, such as pumps and motors from service and overhaul them as part of a preventative maintenance strategy. Sulzer has been involved in such projects with several power generating sites throughout the UK and now has a number of framework agreements that are managed by the service centers closest to the customers’ sites.
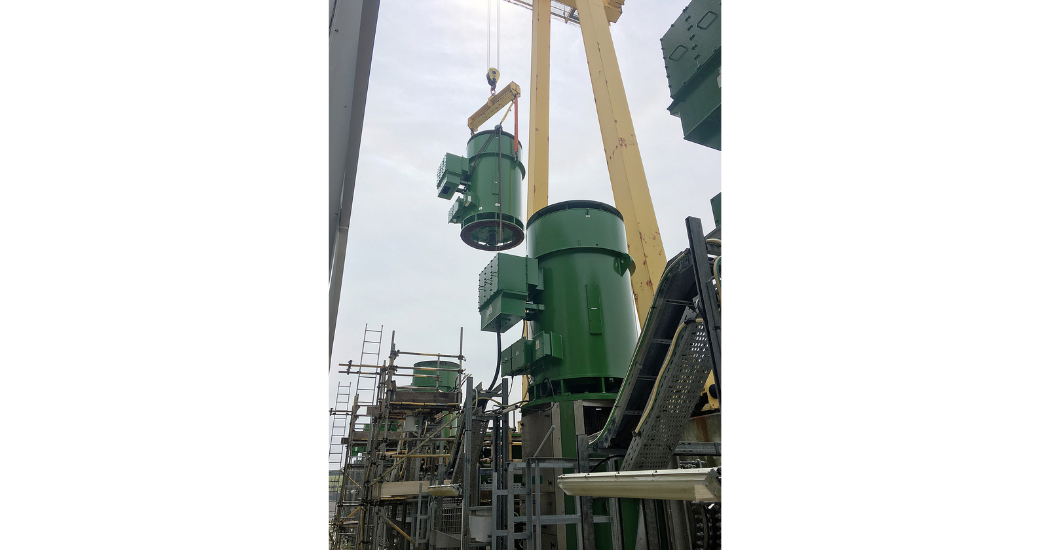
Sulzer delivered a turnkey project including removal and installation
Case study: High voltage pump motor overhaul
As the initial point of contact, the local service center coordinates all of the assets and personnel required to deliver the project through the comprehensive service center network. A good example is the recent overhaul of two high-voltage motors, one from a cooling water pump and the other from a boiler feed pump.
Both motors were disconnected and removed from service by engineers from the Avonmouth Service Center, which is located close to the power station. The refurbishment work was completed by the Southampton Service Center with additional expertise provided by engineers in Birmingham, where the motors would be finally tested before being returned to the customer.
In this case, the boiler feed pump motor had a history of high partial discharge readings in the windings and action was required to manage the situation and extend the useful life of the windings. This would allow the power plant to plan for a complete rewind at a later date and improve the reliability of the motor until that time arrived.
Extending service life
Sulzer suggested reconfiguring the windings by breaking the star point and connecting the original supply leads to create a new star point. This will extend the service life of the stator winding by taking the in-rush current away from the phase coils, reducing the stress on the windings and allows the operator to start planning for a complete rewind in the future.
Having reinsulated and varnished the new windings, the motor was reassembled with new bearings and seals before the remainder of the testing was completed. Both motors were shipped to the power station and reinstalled by Sulzer’s field technicians before being commissioned.
The framework agreement with this customer was a great advantage because all the terms and conditions have already been agreed. This saved time when repairs were needed and also provided assurances of the quality and the procedures used to complete the project.
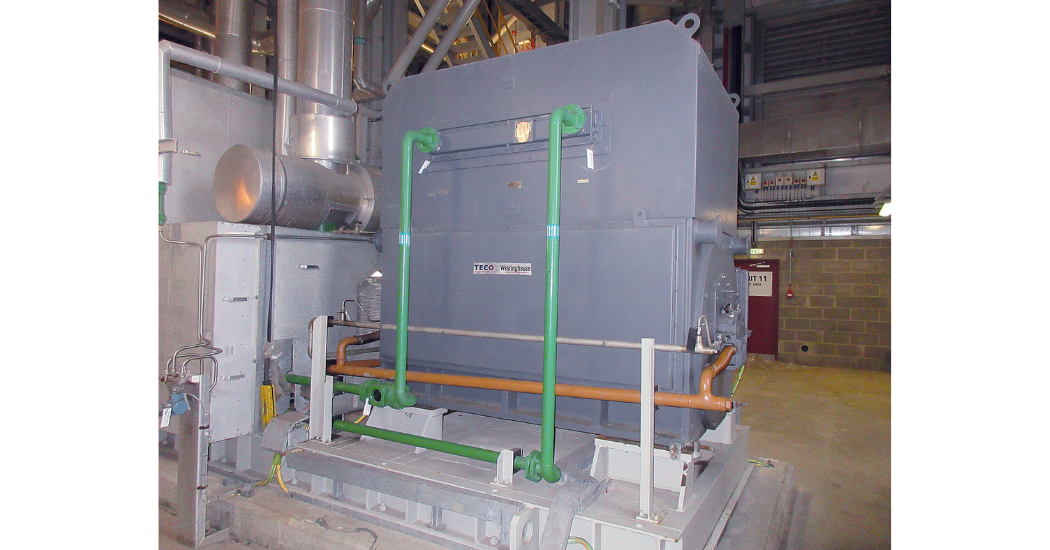
The boiler feed pump motor windings were reconfigured to extend its service life
Expertise and efficiency
As with any work that Sulzer carries out, customers are invited to visit the service centers to review progress or see first-hand any unforeseen developments that are uncovered during an inspection. Through continuous communication and a transparent repair process, customers receive an efficient and cost effective solution.
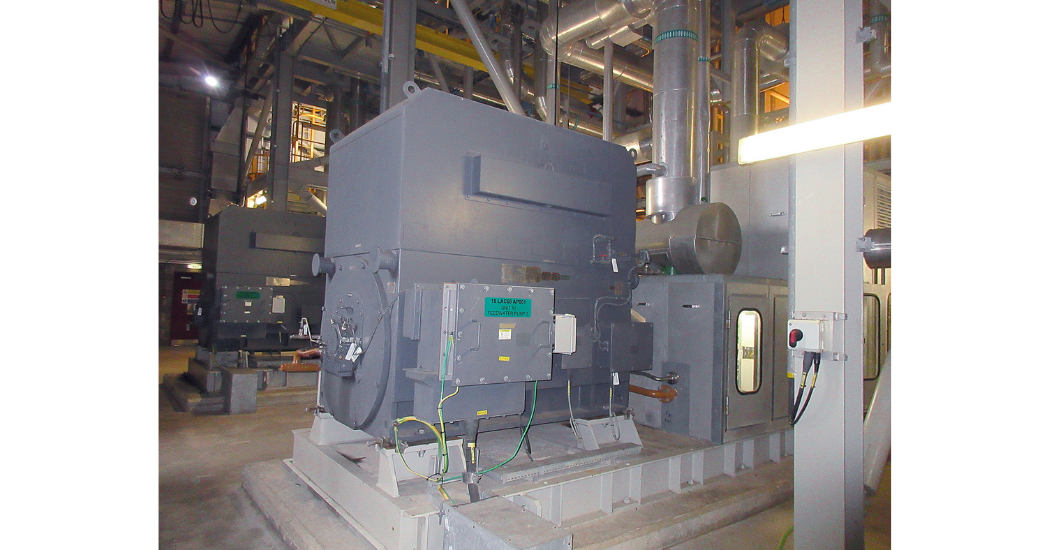
Both motors were reinstalled by Sulzer’s field technicians before being commissioned
The final result from this project was very positive. Downtime has been minimized and plans are in place to make further improvements during the next planned outage.