Sulzer Electromechanical Services provides round-the-clock engineering support for synchronous exciter
In the oil & gas industry, any downtime can be costly, especially if it involves a large piece of production equipment, such as a compressor. For one long-standing customer of Sulzer, having a spare motor was part of the solution, but it needed an overnight modification to the exciter to ensure the plant could restart the next day.
Customers that operate around-the-clock need 24-hour support because even with the best-planned maintenance regime, sometimes the unexpected happens and a repair needs to be completed quickly. In this case, the call came in at 1 a.m. with a report of an 11,000 hp (8,200 kW) synchronous motor driving a reciprocating compressor that needed attention.
Sulzer’s relationship with this site includes field service support and holding a spare motor for this application. However, due to the size and complexity of the installation, the change-out time for the spare motor would be around seven days, which would incur significant production losses. As speed was of the essence, the decision was taken to use the exciter assembly from the spare motor and keep the downtime to a minimum.
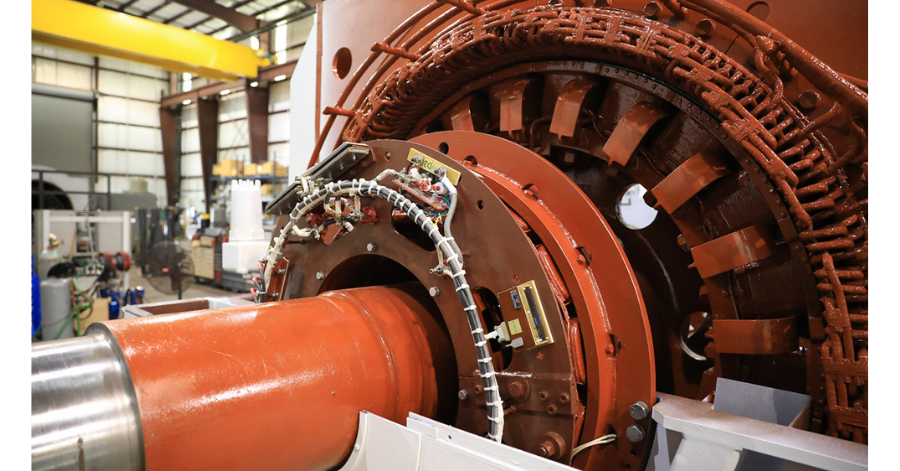
The modified exciter assembly was ready within 24 hours of the request for support from the customer
Overnight repair
Field service engineers from Sulzer’s Orange Service Center attended site and completed an initial inspection of the exciter assembly. They found that the two motors were not quite identical and some of the parts would need to be modified because they had different bolt centers. To quickly adapt the design, the replacement exciter assembly was sent to the Pasadena Service Center where it arrived at 6:30 p.m.
The engineering group, which had been made aware of the situation, went to work on developing a solution overnight. The customer arrived in Pasadena at 10:30 p.m. to see if any progress had been made and was ecstatic to see that the job was almost complete.
By 11:30 p.m. the new parts were ready for shipment back to the site. Once they arrived, the installation and commissioning were completed early the next day by the field service team. Having reinstated the unit in the field, Sulzer then addressed the repairs to the damaged parts so that the motor in storage was back to operational status.
As part of the project, the customer asked Sulzer to assess the cause of the exciter failure to try and avoid a similar incident. The investigation showed that the motor had been overloaded during startup. The customer therefore requested Sulzer to build another complete exciter assembly for the motor in service as a spare part to reduce the downtime in the event of a similar incident.
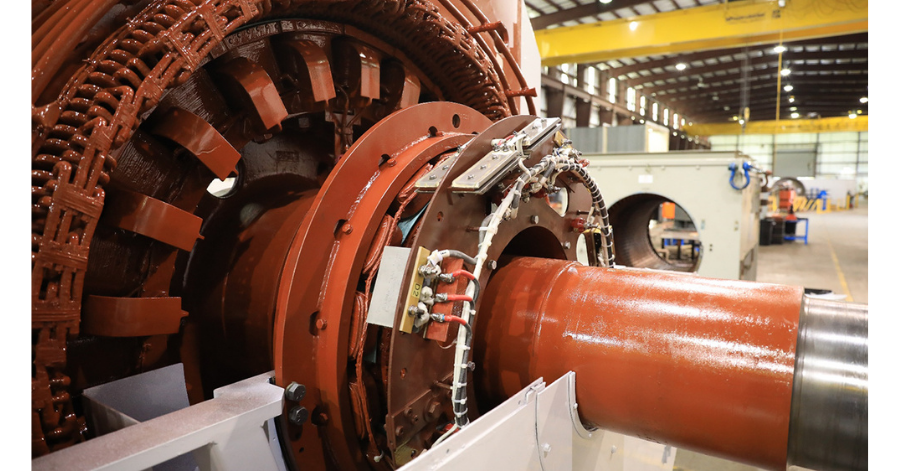
The customer requested Sulzer to build another complete exciter assembly as a spare part
Marcin Chojnacki – Pasadena Service Center Manager, comments: “The Sulzer network of service centers always work together to ensure the quickest solution for the customer. With such a wide range of in-house facilities and resources, overnight repairs can often be delivered when time is of the essence.”
About Sulzer
Sulzer is a global leader in fluid engineering. We specialize in pumping, agitation, mixing, separation and application technologies for fluids of all types. Our customers benefit from our commitment to innovation, performance and quality and from our responsive network of 180 world-class production facilities and service centers across the globe. Sulzer has been headquartered in Winterthur, Switzerland, since 1834. In 2020, our 15’000 employees delivered revenues of CHF 3.3 billion. Our shares are traded on the SIX Swiss Exchange (SIX: SUN). www.sulzer.com. The Pumps Equipment division specializes in pumping solutions specifically engineered for the processes of our customers. We provide pumps, agitators, compressors, grinders and screens developed through intensive research and development in fluid dynamics and advanced materials. We are a market leader in pumping solutions for water, oil and gas, power, chemicals and most industrial segments.
Throughout the Americas, Sulzer provides cutting-edge parts as well as maintenance and repair solutions for pumps, turbines, compressors, motors and generators. We service our own original equipment as well as third-party rotating equipment operated by our customers. Our technology-based solutions maximize reliability and lifecycle cost effectiveness.
For more information on Sulzer, visit www.sulzer.com