Experience and in-house capabilities are essential to cost-effective maintenance of 7FA gas turbines
The amount of energy created by gas turbines on a global scale, especially in combined cycle applications, continues to grow as their popularity increases. Operators of assets such as the 7FA can take advantage of experienced independent maintenance providers, who can deliver regular inspections as well as repair services.
James Neurohr, Gas Turbine Product Manager for Sulzer, looks at the expertise and facilities that are required to deliver a comprehensive service that will optimize reliability and keep downtime to a minimum.
The drive for lower energy costs, as well as increased demand, means that the gas turbine still has a large role in the power generation market. Gas turbine operators are keen to extend the service life of an aging fleet to make their power generation reliable, cost-effective, and with reduced emissions.
Large frame industrial gas turbines, such as the 7FA, are used mainly in co-generation plants, producing between 170 and 190 MW each. The power utilities will usually have at least two units per site, but due to the scale of their output, any planned outage will have to be covered by the remaining assets supplying the grid. Preventative maintenance is far and away more preferable to reactive maintenance, which presents huge issues when dealing with equipment of this scale.
National power grids can be a mixture of utility companies and independent suppliers, with the latter often suffering penalties for unexpected outages. Therefore, apart from the lost revenue for the period of the outage, replacement power may need to be purchased as well to avoid penalties. The costs associated with unplanned equipment downtime have made for a very risk-averse industry and one that views maintenance procedures in minute detail.
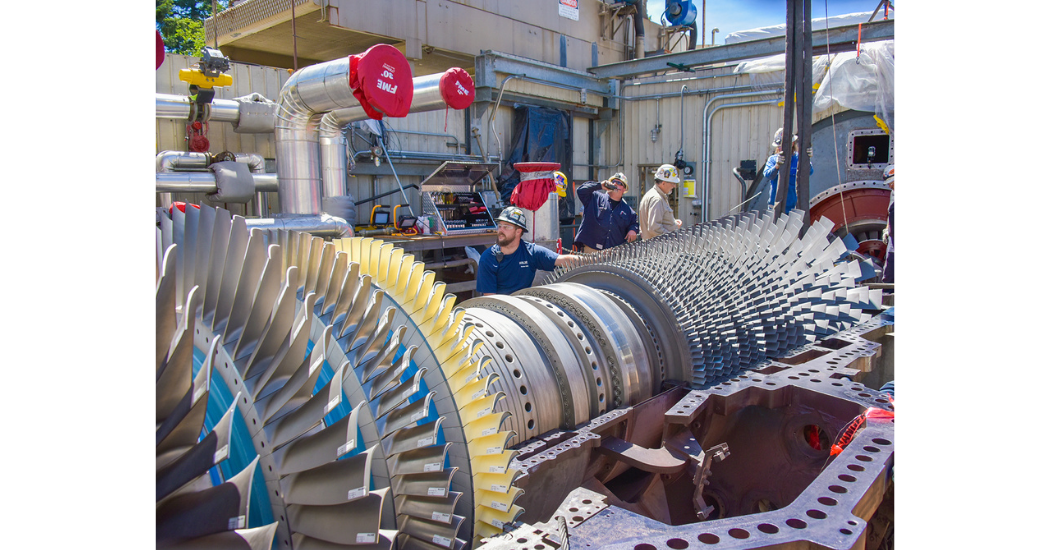
Gas turbine maintenance projects require considerable expertise on-site for an efficient conclusion
Approaching end of life
Maintenance projects are interval-based using a single document, currently GER-3620 rev N, which states when maintenance needs to be completed. Depending on the application, this can be on operating hours or the number of starts.
The OEM is starting to move away from support of some of the earlier 7F variants, which have been around since the mid to late nineties, and is offering upgrades to these models instead. They are equipped with new, improved components, such as hot gas path parts that will improve performance by 5-10 percent, but at a cost of millions of dollars.
For the bulk of the population of 7FA units, the 20-year anniversary is rapidly approaching. GE has assigned the shortest service lifetime to the 7FA rotor compared to any other gas turbine it has manufactured. 144’000 factored fired hours is set as the end of life term for this rotor. At this point the OEM offers an end of life (EOL) assessment, and advises if the rotor has any life remaining or if a new rotor is required, at a cost of approximately USD 25 million.
Recovering this size of investment can take a considerable amount of time, and some operators are looking at independent maintenance providers for a more cost-effective solution. For example, a typical repair of the same hot gas path components would be in the region of USD 1.5 million. This illustrates how the choices made during the EOL assessments can have significant implications for the overall cost of operation.
Independent expertise
The gas turbine is a precision machine and with the correct tooling and expertise, it can be operated and maintained for many years of service. With greater experience, it is possible to not only maintain the asset but also improve individual components to extend operational performance and improve reliability.
Independent maintenance providers can offer several advantages over OEM services, but it is important to highlight the importance of experience and proven repairs. In this industry, claiming to have the knowledge and tools for the job must be backed up by records of satisfied customers. In Sulzer’s case, it has delivered over 900 repairs to 7FA components including combustion hardware and hot gas path components, as well as 36 7FA rotor overhauls.
Sulzer is the only independent maintenance provider that can offer the full suite of EOL inspection assessments in-house. The company also provides the industry-standard warranty on all of the maintenance projects.
Field service support
From the outset of any planned outage, efficient management and allocation of resources is essential for a successful project. The combination of technical directors, diagnostics engineers, supervisors and skilled technicians ensures that all on-site aspects, including diagnostics, inspections and start-up support are completed efficiently.
Field service engineers can split the case, remove the top section and either carry out in-situ inspection and maintenance or remove the rotor for repairs at the specialist service center in Houston. Sulzer is one of only a very few maintenance providers that can deliver a comprehensive maintenance service exclusively using in-house resources.
Furthermore, operators are frequently including clauses in the requests for quotation that require repairs to be completed in the same country as the turbine operates so that the customer can visit the service center to observe progress. To this end, Sulzer’s worldwide network of service centers, all of which can call on the expertise of the others, is a distinct advantage for turbine operators.
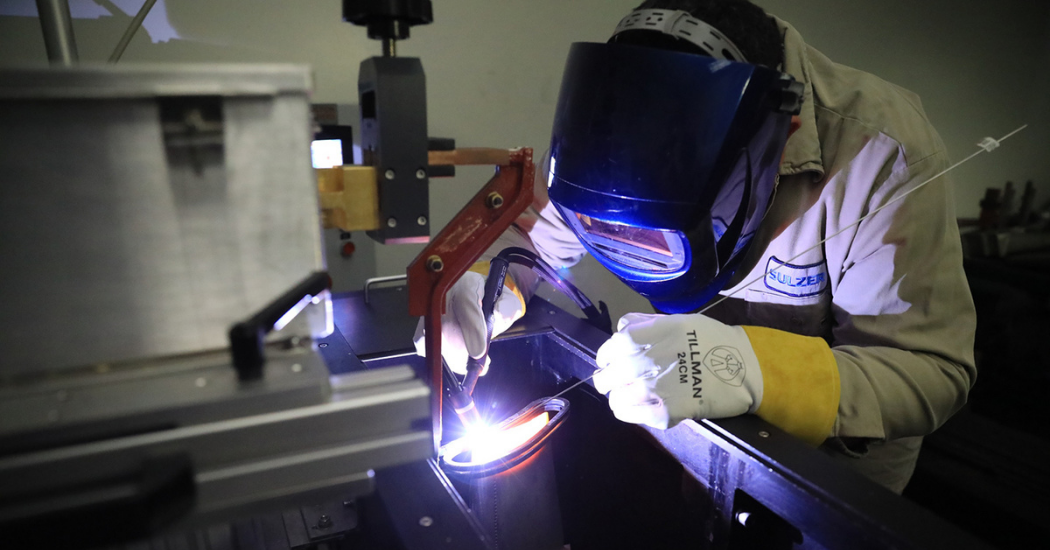
In-house component repair capabilities are important for minimizing project timings
Component repairs
Every component within the 7FA is precision-made and must be carefully inspected for wear or damage, as detailed in the service document. Each group of components has their own challenges, from compressor stator segments to liners and fuel nozzles. Working with a maintenance provider that can offer expertise in all areas of the gas turbine can reduce downtime and simplify project management.
The ability to design and manufacture new compressor blades and stationary vanes, as well as having a complete set of 7FA blades and vanes in stock, helps to minimize repair times. Coupled with a component repair facility, where all the combustion and hot gas path components are refurbished, and a specialized coating facility, a dedicated team of repair experts can offer a truly comprehensive service.
In addition, with such a challenging operating environment, it is important for service centers to be able to deliver advanced bucket repairs. These require expert metallurgy and welding equipment as well as the capability to upgrade materials for enhanced durability.
Cooling is very important to maintain bucket operational temperatures below the melting point of the materials. This is achieved by integral cooling galleries, but any damage to the bucket tip will allow cooling air to escape and can result in surface temperatures exceeding 2’000 °F (1’100 °C). By tackling this problem ahead of time, it is possible to prevent tip cap losses by using thicker materials and specialized coatings to prevent oxidation and subsequent material failure.
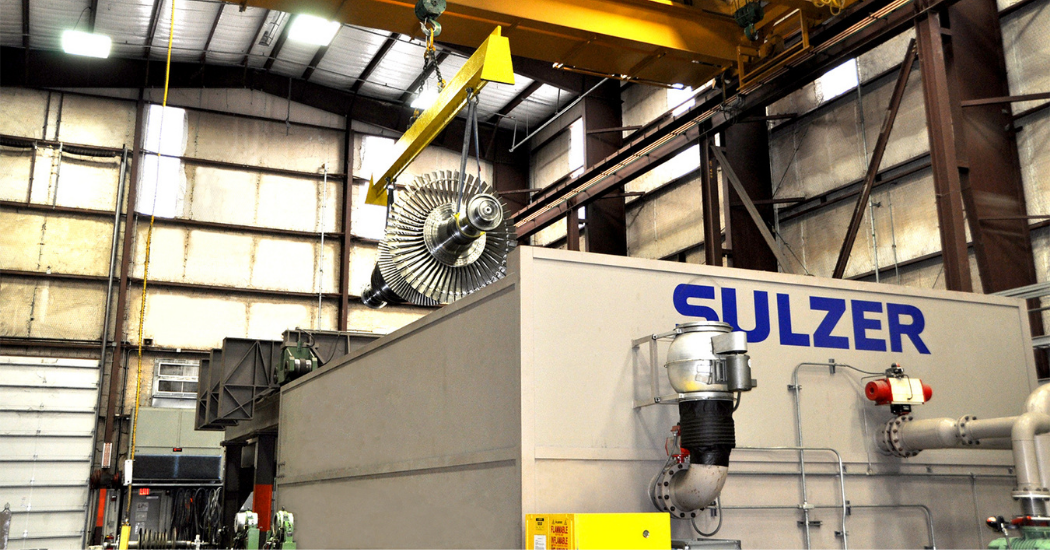
High speed balancing facilities are essential for continued reliable operation following a repair project
Lifetime extension
Sulzer is unique as an independent maintenance provider that has a full in-house metallurgical lab, enabling root cause analysis (RCA) to be completed quickly and efficiently. Samples can be taken without destructive testing to determine how much service life remains in a component.
This can be used when a component is approaching what the GER-3620 describes as EOL, to prove that additional service time still remains. Again, this has a significant benefit as maintaining or refurbishing a part is far more cost-effective than replacing it.
Ultimately, operators of gas turbines are seeking cost-effective, but more importantly, experienced maintenance services. Sulzer offers years of expertise and can deliver one-off projects or long-term service agreements can be arranged, supported by a stock of exchange components that ensure downtime is minimized.
Using an initial population of hot gas path parts, for example, these can be installed during a refurbishment and the parts that are removed can be repaired before being installed in the customer’s next turbine under repair. These parts continue to be used, where possible, through the customer’s fleet. This removes the need for a set of parts to be purchased to start the process and also maximizes the volume of their own parts being retained within the fleet.
7FA units are often installed as part of a combined cycle power plant and for these installations Sulzer offers an almost unique offering. As an experienced provider of services for all types rotating equipment, Sulzer can deliver a maintenance project for the complete drive train, from the gas turbine to the steam turbine, its feedwater pumps and the generator. Above all, the whole project is coordinated and managed by the local service center, simplifying communication and maintaining a transparent repair process.