Contributor: Alex Edwards, Marketing & Communications Manager, Rotating Equipment Services, Sulzer
Cost-effective solution to maintain wind turbines’ reliability and efficiency
Renewable energy sources, especially wind power, are becoming increasingly important in delivering the total electrical demand of the UK. Many of the early, large-scale wind farms have been in operation for well over a decade and owners are keen to find dependable maintenance partners to ensure continued reliability of the equipment. For one installation in the Scottish Borders, Sulzer was able to offer a cost-effective solution.
In most cases, when a wind farm is built and handed over to the operator there is a contract that requires the operator to use the original equipment manufacturer (OEM) for all maintenance activity in order to retain the warranty on the turbine. Operators have had mixed experience with these contracts, but many have decided to find an alternative maintenance provider as soon as the original contract expires.
The search for expertise
The owners of 85 wind-powered generators were looking for an alternative to the fixed contract with the OEM that was due to expire shortly. This was an important step to safeguard the reliability of the turbines which provide the power equivalent to the annual consumption of 110,000 homes. In view of the variety of motors, gearboxes, generators and controls within wind turbines, it was essential to select a company that had wide-ranging expertise and the facilities to deliver high-quality repairs.
Paul Richardson, Sulzer’s Middlesbrough Service Center Manager, explains: “Due to the remote location of many of the wind turbines, the on-site workshop facilities can be quite limited, so reliability of components is essential. The best solution is a single-source supplier that can provide a wide variety of services to a very high standard.”
In this case, the operator has a small team of engineers who carry out planned and reactive maintenance work. This team carries spare parts and is able to exchange the parts when necessary, which minimizes the downtime of the turbine.
Maximizing efficiency
However, this created a collection of faulty parts that, potentially, could be repaired and reused, providing the process was cost-effective. Therefore, the operator was looking for a maintenance provider, which ultimately led to Sulzer’s door. The expertise and facilities within the Middlesbrough Service Center were a perfect match for the turbine operator.
Initially, detailed repair procedures were developed for each component. All this documentation had to be agreed and signed off before any work could pass through the workshop. Having completed the necessary checks, Sulzer has demonstrated its expertise and high-quality workmanship from the outset.
For the pitch motor, which is used to adjust the blade pitch according to the wind speed, the operator’s repair team routinely changes six to twelve motors at once, installing new ones at the same time. Having developed the necessary repair procedures, the first six motors were sent to the service center to be refurbished as part of an ongoing repair program.
All of the motors were turned around in just 10 days, with continuous communication maintained throughout the project. Once they were complete and the expense was compared to buying new components, it was clear that using Sulzer would be a cost-effective solution. Furthermore, compared to the original process of sending the motors to the OEM’s workshop for repair, the experience with Sulzer was both transparent and easy to manage.
Cost-effective solutions
This advantage is compounded in situations where larger components, such as the generator or the gearboxes are in need of repair. In these cases, a mobile crane will be required, which can incur a considerable expense. If the maintenance team has a replacement component ready to install, then the crane only needs to be erected once to complete the repair.
Without the necessary spare parts, the alternative would be to remove the component, repair it, and bring it back to site, which would require two crane visits, and add considerable expense to the overall cost. Sulzer has considerable expertise in repairing and rewinding generators, especially the multi-megawatt units that are installed in large-scale wind farms.
The Middlesbrough Service Center also has the facilities to carry out a full load test of these generators after the repairs have been completed. This ensures that the refurbished components have proven their ability to perform before they are reinstalled and returned to service.
Paul continues: “Customers are always welcome to come and see the progress of any repair, we conduct very transparent partnerships. This is in contrast to the experience many have with other companies, and in this case, our customer had experienced some issues with parts being returned late and the long-distance communications were less than ideal.”
Since the original repair project was agreed, the Middlesbrough Service Center has expanded the scope of components to be repaired to include fan units, hydraulic pumps, slew gearboxes and variable speed drives. Having proven the capabilities and expertise of the service center, it is set to deliver a comprehensive service and ensure the reliability of the wind turbines is assured for years to come.
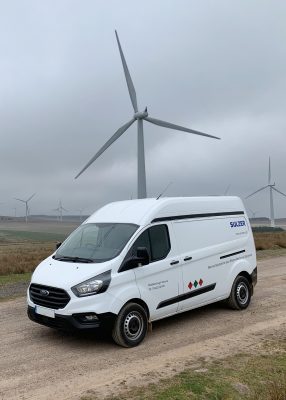
Owners and operators of wind farms are keen to find dependable maintenance partners to ensure continued reliability of the equipment
About Sulzer
Sulzer is a global leader in fluid engineering. We specialize in pumping, agitation, mixing, separation and application technologies for fluids of all types. Our customers benefit from our commitment to innovation, performance and quality and from our responsive network of 50 world-class manufacturing facilities and 100 service centers across the globe. Sulzer has been headquartered in Winterthur, Switzerland, since 1834. In 2018, our 15’500 employees delivered revenues of CHF 3.4 billion. Our shares are traded on the SIX Swiss Exchange (SIX: SUN).