Contributor: Sulzer
Improved durability and extended outage and inspection intervals for combustion turbines
Power generation plants need to operate as efficiently as possible in order to keep up with the growing demand for electricity. In order to maintain high reliability rates, it is necessary to perform periodic inspections and maintenance as specified by the original equipment manufacturer (OEM). However, thanks to a series of modifications and enhancements from Sulzer, one power plant in Missouri is hoping to increase significantly its maintenance interval for its turbines and therefore reduce its maintenance costs.
The Holden Power Plant in Missouri, which is owned by Associated Electric Cooperative Inc. (AECI), operates three Siemens V84.2 simple-cycle dual fuel combustion turbines that have a combined output of 321 MW. Designed as a peaking plant, they are used to meet peak power demands that are over and above the base load demand on the local electricity grid.
Due to the fluctuating demand for power the amount of time each gas turbine operates can vary greatly; this means that maintenance schedules are defined both in terms of equivalent operating hours (EOH) and calendar years. Units that operate infrequently will therefore reach the calendar based intervals first.
Such units are unlikely to exhibit any great amounts of wear, but oxidation of the compressor is a much more likely issue and so it is important to enforce regular inspections, even on equipment that is used infrequently.
The Siemens V84.2 requires a hot gas path (HGP) inspection every 25,000 EOH or every six years and a major inspection every 50,000 EOH or every 12 years. The units at the Holden plant had accumulated around 10,000 EOH during 12 years of service. As such, the owner wanted to investigate the possibility of extending the calendar based inspection intervals without affecting the performance or reliability of the turbines.
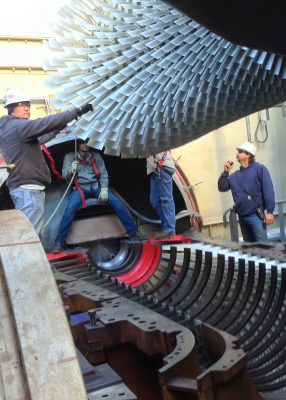
As a leading independent service specialist, Sulzer has considerable expertise in delivering maintenance and performance improvements for gas turbines.
As a leading independent service specialist, Sulzer has considerable expertise in delivering maintenance and performance improvements for both Siemens SGT and V-Series gas turbines. The experienced design team at Sulzer proposed a range of modifications and enhancements to both the rotating and the stationary sections of the turbines.
Work was carried out on the entire compressor with both the rotating and stationary sections, as well as the inlet guide vanes, being coated with Anti-Fouling / Anti-Corrosion coatings in order to prevent oxidation. The new coating has greatly improved the corrosion resistance and enabled the plant not to be dependent solely on the inlet dehumidification equipment.
In a standard V-series turbine, the flame tube F-ring has a tendency to oxidize and produce scale which can be ingested by the turbine during normal operating conditions. To improve this situation, the component was carefully machined to expose fresh material and allow an Inconel overlay to be welded to the fresh surface before being machined back to the required diameter. Inconel 82 is a nickel chromium alloy with high strength and an outstanding corrosion resistance that will improve the durability of the component.
The combustion section of the turbine was also protected with a full thermal barrier coating (TBC) being applied to all of the upper flame tube and other hot gas path components. A ceramic TBC was applied to the bezel rings and segment plates, mixing elbows and inner casing, in order to increase the resistance to thermal distress in the hottest areas of the unit. In addition, a chromium carbide coating was applied to all of the mating surfaces of the combustion section to minimize wear as the parts expand and contract.
Finally, additional cooling holes were drilled in the flame tube behind the A-row tiles to improve cooling in this area and increase the durability of the holders by reducing the oxidation and erosion.
Having completed all of the design modifications, the turbine was reassembled and put back into service. The Sulzer engineers worked closely with the plant maintenance personnel to ensure that the project was managed and delivered in line with the operational requirements of the power plant.
Gabe Fleck, Manager of Gas Plant Operations at Associated Electric Cooperative Inc. (AECI) comments: “Projects such as this require a considerable level of expertise and technical knowledge in order to complete them successfully. Working with Sulzer, we have managed to increase significantly our inspection periods, improving the availability and durability of our plant.”
In recognition of the improvements that have been implemented at the Holden site, the owner was presented with a Best Practices award for improved performance by the Combined Cycle Journal.
Following the completion of all the work, which has eliminated a number of areas of concern, the power plant is looking to extend the HGP inspection to at least 10 years and the major inspection to 20 years. Following the success of this project, the same improvements were also implemented on the other two gas turbines at the site.