Illustrated by a case study of melting sulfur
Sulfuric acid is the key chemical used in the production process of wet phosphoric acid. That is why the production of sulfuric acid in the vicinity of the phosphoric acid plant offers many advantages. Not only does it reduce transport costs, but the nearby production of sulfuric acid, which is an exothermal process, allows the residual thermal energy to be used for the manufacture of concentrated phosphoric acid. The steam generated is fed to the heat exchanger located within the concentration unit of the phosphoric plant.
In this article, Patrik Kolmodin at Sulzer explains how agitators for the chemical industry can be optimized. The article includes a case study on melting elementary sulfur, subsequently to be used in phosphoric acid production.
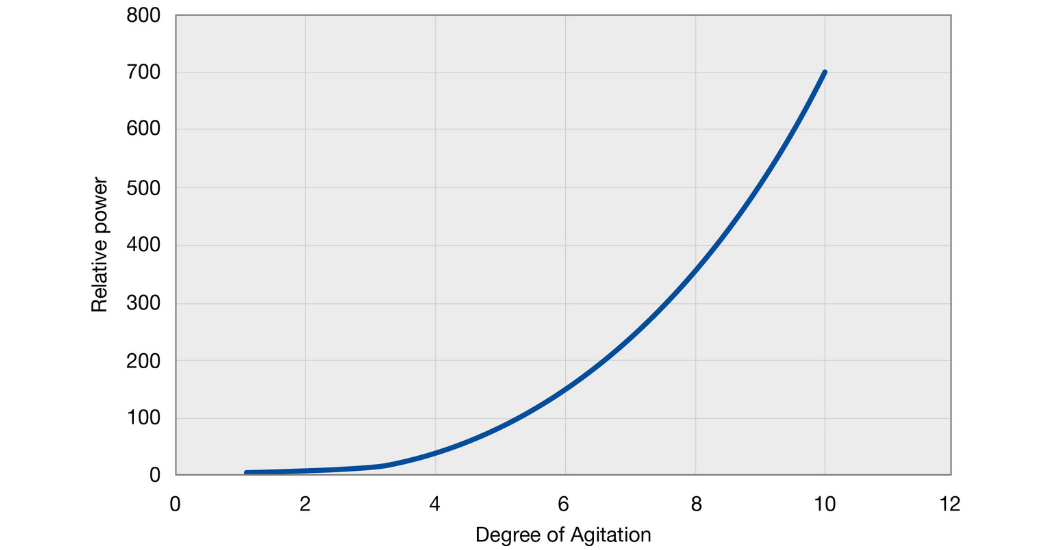
A higher degree of agitation will require much more power.
Agitators in the chemical industry
In capital-intensive industries with high focus on productivity and uptime, it is easy to stick to old truths. But that does not mean that something that has worked for many years would be the best design now, or in the future. A common approach for agitators in the chemical industry is it-is-working- now-so-do-not-touch-it principle. This is caused by the fear of malfunctioning processes and is often a result of poor knowledge and the belief that the current process equipment always comes with the lowest risk. There are, however, great opportunities to save both operational and capital costs and even increase reliability without jeopardizing process performance.
Agitators need to have a flexible design to suit various tank sizes and shapes. It is also important to adapt the agitation intensity to the process needs. Unlike pumps, it is not possible to select an agitator based on t flow and head. Instead, the agitation must be quantified in other ways to manage the process. This often leads to misunderstandings, oversizing and costly investments. When designing an agitator, the most common mistakes are:
- Not getting the right agitation intensity
- Replicating existing agitator design
- Poor input data
- Poor evaluation of the energy costs
- Mechanical design – heavy-duty or light-duty design?
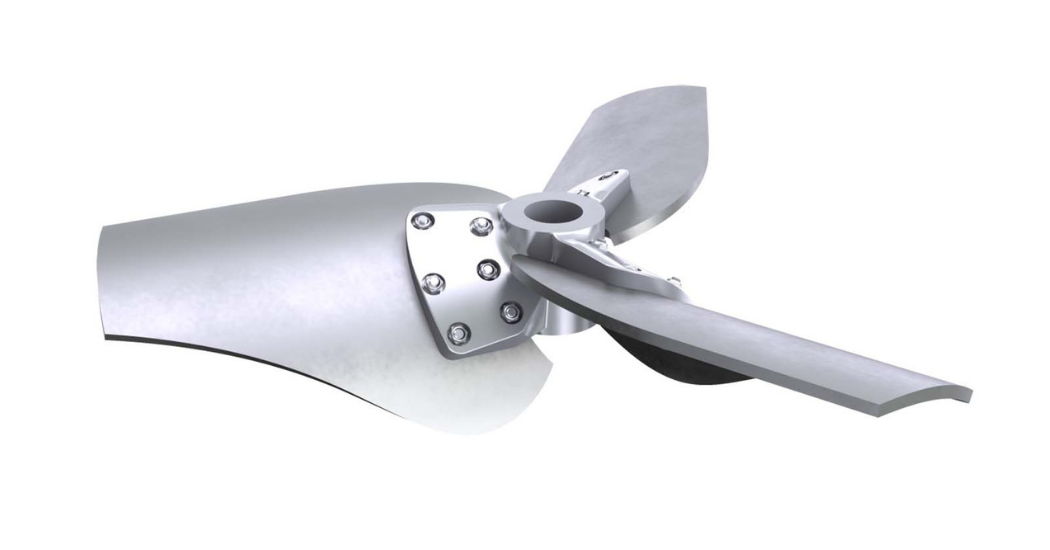
Greater power savings could be achieve with Scaba hydrofoil high-efficiency impeller versus pitch blade turbine
Quantifying agitation
Most people have some intuitive idea of mixing and blending processes. For example, the infusion from tea leaves will remain near the bottom of a cup of hot water until it is stirred. Just a small amount of stirring will blend the mixture. Continued stirring will not improve the blend.
There are many processes in the chemical industries that require agitators. Contrary to the way in which we blend tea, many agitators mix too much and at too high intensity, without achieving a better result.
For quantifying, Sulzer uses methods such as the degree of agitation, which is based on the liquid velocity at the surface of the tank. This is a very powerful design method for many types of processes, different rheologies, and different tank shapes. It also takes more efficient hydraulics into account. Other less good dimensioning tools are for example power per volume, using W/m3. This is a poor dimensioning principle which is neither good for scaling, nor does it take more efficient hydraulics into account.
Another method is to use the impeller pumping capacity. This method can be difficult as well because suppliers have different measuring methods and – not least – it depends on the impeller diameter and rotational speed. A large, slow-running impeller will generate a higher pumping capacity at the impeller than a smaller impeller running at a higher speed, while the overall agitation level may still be the same. In addition, the impeller pumping capacity does not consider the pumping direction.
When targeting a certain agitation level, it is important to understand that a small increase in the agitation level may result in a much higher power consumption, because the power need increases exponentially with the degree of agitation. An increase in the degree of agitation from 8 up to 10 may double the power consumption, but the agitation intensity only increases by 25%.
Too strong agitation?
Mixing a cup of tea intensively for ten minutes will not do much harm; it will still be a properly blended cup of tea ─ although a bit colder. In an industrial process, the implications of overmixing are more serious. First, the power consumption will be higher than needed and will increase the overall energy bill unnecessarily. A higher motor power will also result in a heavier agitator design. This will increase the investment cost, not only because of the agitator itself, but a higher weight will also require a more robust tank support. Furthermore, the higher the agitation intensity in the tank, the more vibrations might occur, as well as more load on the blades, shaft, bearings, drive unit, and motor. Particularly for suspensions, there will be more wear, causing shorter equipment lifetime. All in all, these issues may result in a short lifetime or even in costly, unplanned shutdowns.
Venturing outside the comfort zone
In a demanding industry where uptime and reliability are key factors, the easy way is to continue with existing and proven technology. This is not the best way to utilize technology development such as efficient hydraulics, new design tools and higher reliability. In the fertilizer industry, Sulzer frequently receives agitator enquiries specifying identical copies of old existing designs with too high power, poor hydraulics, and oversized equipment. If we offer an efficient design with lower power consumption and thereby lower installed weight instead, not only can the operating cost be reduced, but also a longer lifetime and higher reliability can be achieved.
It may indeed be scary to venture outside the comfort zone, but if you dare to, longer-term benefits from lower energy cost and higher reliability will be achieved.
How much agitation is needed?
Good enough would be fine! The challenge in designing agitators is that what is “good enough” for one may be different for another. There are basically three things we must know to make a good agitator design:
- The tank shape. This also includes the agitator mounting height.
- The process. What is the application or how much intensity is needed?
- The media. For example, for mineral suspensions, it is important to specify parameters of the solids, such as the particle density and the size distribution, the liquid properties, and a process description.
These three simple rules will allow good selections, even though not necessarily according to the original expectations.
Adapt to the prevailing conditions
Agitators are used for several industrial processes, including purposes other than just mixing. These can be blending liquids, keeping solids in suspension, heat transfer, leaching, dispersion, emulsifying and dissolving.
In the fertilizer industry, it is important to adapt not only the agitation intensity, but also the mechanical design of the agitator to the process. Parameters such as reliability and criticality of the process must be considered, as well as the local site conditions.
For lighter applications, agitators can be of a leaner design. This can, for example, mean a drive unit with a gearbox only, lighter shafts and propellers and the use of a bottom bearing, which may require regular service. A heavy-duty design can include a separate agitator bearing, a high gearbox service factor, a stronger mechanical construction, and free-hanging shafts where the agitator runs safely outside the critical speed interval.
Heavy-duty designs are needed in critical applications, tanks with violent agitation, rock slurries, erosive and/or aggressive media and when running the lowest impeller through the liquid level. Lighter applications can be applied to the storage of clean liquids, slurries with small particles at a low solids content and light-weight chemicals.
A more expensive agitator of a heavy-duty design can help avoid costly shutdowns and reduce the maintenance cost. A lighter design is, however, sufficient for many applications, still achieving long lifetime but with a lower construction weight. Agitators are machines that usually operate at a low rotational speed. A correctly designed agitator will have a longer lifetime and need fewer spare parts than, for example, a pump. Therefore, the application and criticality must be considered when selecting the agitator. Sometimes additional mechanical margins are needed, sometimes not. High margins will lead to a higher investment cost.
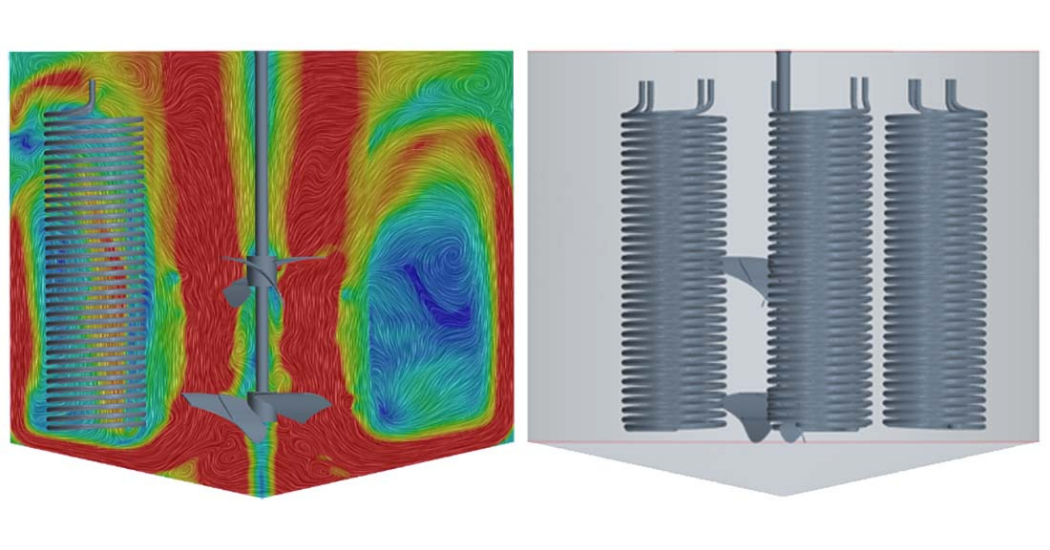
Computational fluid dynamics (CFD) studies were performed to compare the local velocity at the heating coils for 132 vs 200 kW motors. The local velocity was increased by only 4% with the higher motor power.
Case study
The manufacture of sulfuric acid from solid sulfur starts with producing molten sulfur. The granules are melted in specifically designed equipment. The molten sulfur is then filtrated and conveyed to the sulfur burner. It is highly important to work with reliable equipment from the very beginning of the process. Any issue in the very first step of the process may have significant consequences on the whole fertilizer complex. Proper melting of sulfur requires well-performing agitating equipment.
A client had an expansion project which included two sulfur melters. The heat transfer through heating coils was extremely important to manage the process. In addition, cold winters and hot summers caused challenging ambient conditions. It was specified that the agitator should have a 200-kW motor to drive pitch blade turbines.
Rather than just following the specification, Sulzer wanted to fully understand the process and the conditions to propose the best technical solution. The Scaba SHP hydrofoil propeller was calculated to provide more agitation than a pitch blade turbine and would generate higher velocities and better heat transfer. Sulzer concluded that a 132-kW motor was enough, thanks to the highly efficient hydrofoil impellers.
During the engineering phase, Sulzer evaluated two options, 132 and 200 kW. The velocities inside the tank and locally at the heating coils were examined in a CFD (computational fluid dynamics) study. The average flow velocity in the tank would increase by 11% with 200 kW, while the local velocity at the heating coils would be only 4% higher versus the 132 kW. This illustrates how much more motor capacity is needed to achieve a higher velocity.
Sulzer supplied two agitators of type Scaba 240FVPT-Sff with hydrofoil SHP impellers to the customer. The agitators were equipped with variable frequency drives for lower operating cost. The agitators are running at the rate of 132 kW or lower, while the actual installed motor is 200 kW, only as capacity reserve for extremely cold days. The power saving resulted in annual energy savings of approximately 20’000 euros.
Due to the critical application and the demanding site conditions, these agitators are of heavy-duty design. The ambient temperature spans from -47 to +40°C, which required special precautions for the drive unit and the motor. The agitators are equipped with an industrial gearbox with both heaters and coolers. The wetted parts are made of standard stainless steel, 316L or duplex stainless steel for critical parts where higher strength is required. The gas phase inside the tank can be aggressive, and the parts exposed to gas are made in 904L with additional rubber lining on top for extra security.
This project summarizes some important points when designing an agitator for the chemical industry:
- The agitator is designed with the correct agitation level. Neither too much nor too little.
- It was not only engineered to fulfill the enquiry, but to be better.
- Substantial energy savings were considered during the evaluation.
- This is a critical position and the conditions are severe. The agitator must therefore be of heavy-duty design.
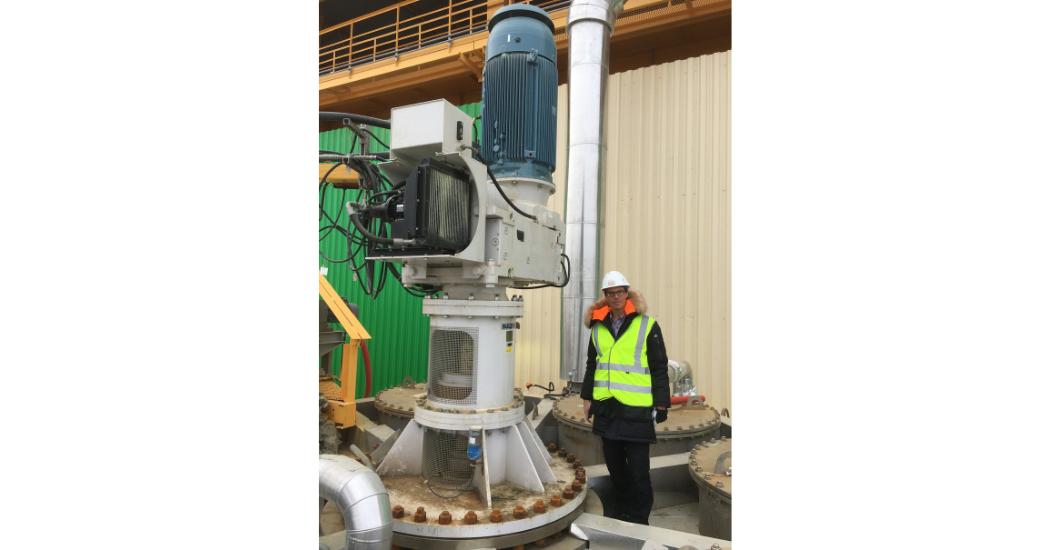
A heavy-duty Scaba 240 FVPT-Sff.
About Sulzer
Sulzer is a global leader in fluid engineering. We specialize in pumping, agitation, mixing and separation technologies for fluids of all types. Our customers benefit from our commitment to innovation, performance and quality and from our responsive network of 180 world-class production facilities and service centers across the globe. Sulzer has been headquartered in Winterthur, Switzerland, since 1834. In 2020, our 15’000 employees delivered revenues of CHF 3.3 billion. Our shares are traded on the SIX Swiss Exchange (SIX: SUN). The Flow Equipment division specializes in pumping solutions specifically engineered for the processes of our customers. We provide pumps, agitators, compressors, grinders and screens developed through intensive research and development in fluid dynamics and advanced materials. We are a market leader in pumping solutions for water, oil and gas, power, chemicals and most industrial segments.