Contributor: Sulzer
Sulzer moves and refurbishes 180-tonne welder for Tata Steel
The steel industry requires robust and reliable equipment to maintain productivity but this ruggedness has to be balanced with a need to integrate new technologies to maintain overall operational efficiency. The sheer scale of plant items such as welders for example present a number of challenges to modernization; hence the need for experienced engineers and designers, such as those at Sulzer, to achieve a seamless update and integration project.
The high cost of new equipment means that relocating and refurbishment of existing plant can offer a more cost-effective way of maintaining productivity and reliability. The key to completing such a project lies with the expertise and experience of the engineers who are responsible for relocating, redesigning and reassembling the equipment.
The Avonmouth Service Center has built up an excellent working relationship with a number of customers in the steel, marine, mining and water industries and has a reputation for completing large mechanical and electrical repairs within tight deadlines. One such example recently completed for Tata Steel required a flash butt welder that was originally located in Port Talbot, to be dismantled, refurbished, relocated and commissioned on a pickling line in the Llanwern Works.
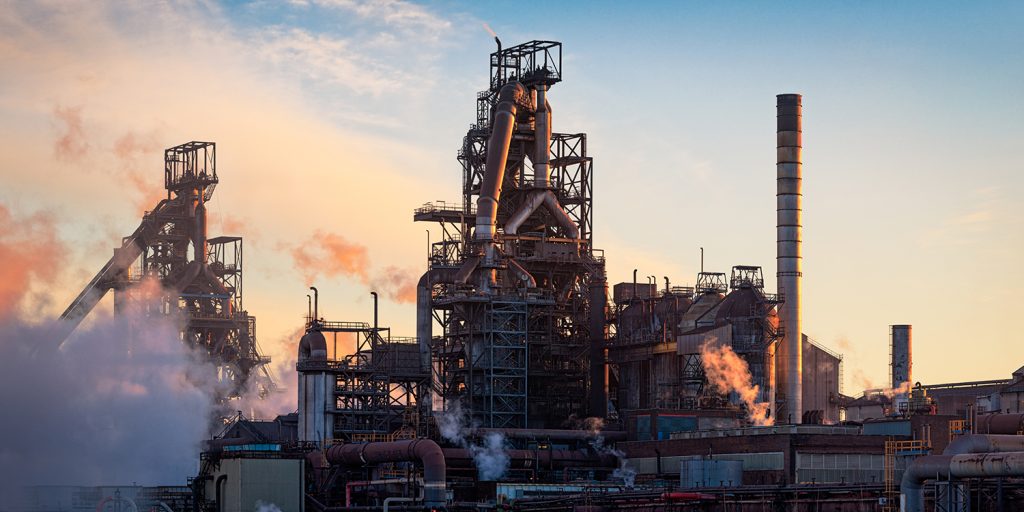
The welder is used to join two rolls of steel together and requires precision control for a high-quality weld [ Source: Shutterstock / pisaphotography]
The initial part of the project was to dismantle the welder into modules to allow it to be transported by road to Sulzer’s Avonmouth Service Center where it was fully dismantled and inspected to perform a complete appraisal. The findings and recommendations were then communicated to allow the customer to take a decision on the viability of the refurbishment project.
One major design change was to the machine handling and control systems which had to be reconfigured due to the steel strip flow being in the opposite direction in Llanwern. A completely new electrical wiring system and software was installed along with all new hydraulic and pneumatic piping. In addition, new hydraulic valve stands with upgraded hydraulic pumps were also incorporated into the refurbished machine.
While this work was being completed in Avonmouth, in Llanwern the existing machine had to be removed to install new foundations in preparation for the arrival of the refurbished welder. Careful coordination between Sulzer and Tata Steel ensured that the site would be ready and the project timetable would be maintained.
With the upgrades complete the entire welder was reassembled at Sulzer Avonmouth to ensure that all the modifications had been successful and that the operation of the machine met the required Operational Engineering Standard. The ability to complete in-house testing of equipment such as this is an important asset that ensures the Sulzer service center delivers the refurbished equipment without the need to spend precious time resolving glitches.
The fully functioning welder was then dismantled into modules for the final time for the short journey across the Severn Estuary before being reassembled in the Llanwern Works. The Sulzer engineers completed the assembly and the connections with the rest of the production line before functional testing and initial welds were completed. Full production was possible in less than two weeks following delivery to the site; a testament to the planning and the functional testing carried out in Avonmouth.
Sulzer GTC’s President honored with Hydrocarbon Processing Lifetime Achievement award
Comments