Sulzer technology is playing a key role in Energiefabriek West, an innovative bio-power scheme in the Netherlands
The Rivierenland Water Authority in the Netherlands is investing in new infrastructure to improve the performance of its wastewater treatment systems while also reducing its impact on the environment. The utility is aiming to become energy neutral by 2030, and Sulzer technology is helping it to realize this goal.
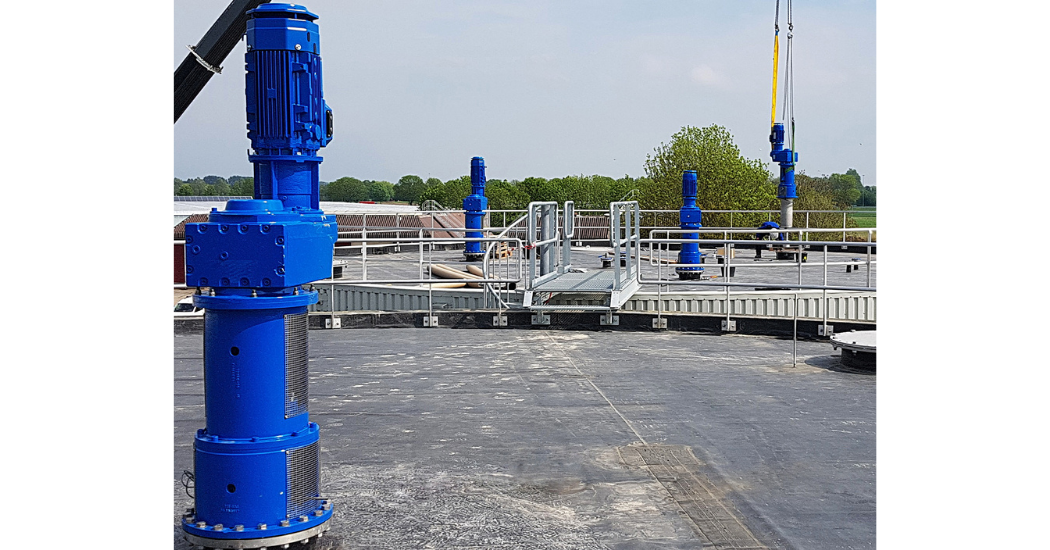
A total of five SCABA agitators were installed in the reactor tanks.
The newly expanded Sleeuwijk wastewater plant serves around 64’000 people and has been designed to optimize the performance as well as efficiency of sewage treatment in western Rivierenland. Consolidating three older wastewater facilities into one, an important part of the rationale for the new treatment plant was the opportunity to install a more efficient sludge digestion facility where methane gas is upgraded to natural gas quality, after which, it is introduced into the Dutch natural gas network.
The “Energy Factory” at Sleeuwijk is one of the first facilities of its type to use Ephyra® technology, an innovative approach to sludge digestion that offers greater capacity in a smaller space. Developed by Royal HaskoningDHV, this process breaks down sludge more effectively than conventional reactors, increasing gas production by 20 to 30 percent. The system requires fewer chemicals for sludge thickening and generates an end-product that is easier to dewater before disposal. In addition to the sludge generated on-site, the Sleeuwijk energy factory is also designed to process material shipped in from a number of smaller wastewater treatment plants in the west Rivierenland region.
The Ephyra system uses the plug-flow digestion concept. The reactor vessel at the Energy Factory is divided into three compartments, with sludge moving between the compartments under computer control. The concept allows the different stages of digestion to be optimized separately, maximizing the efficiency of the process while reducing dwell time in the tanks to as little as 7 ½ days in the Ephyra reactor and 7 ½ days in the after digester.
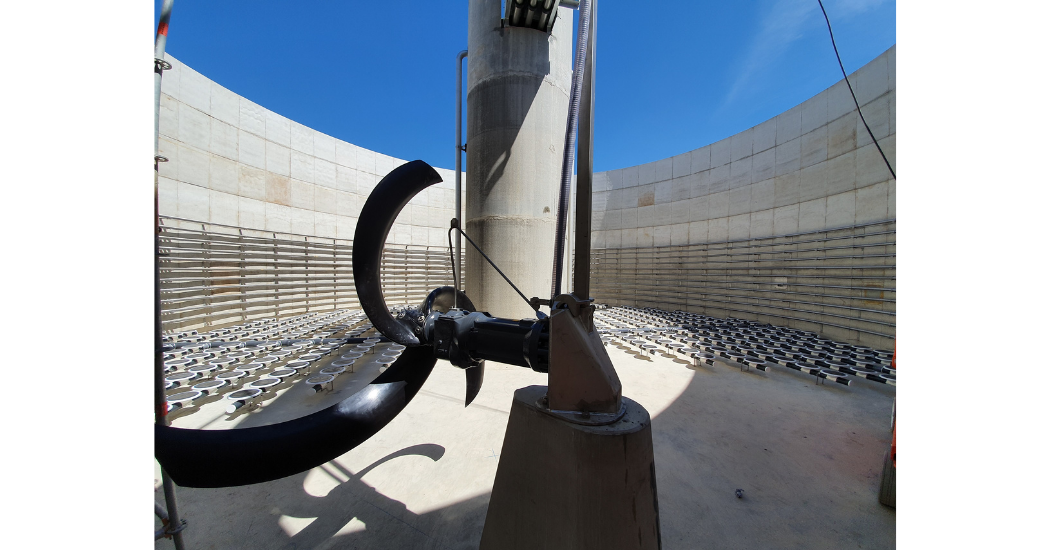
The annamox process uses 480 disc diffusers supplied by two HST 2500 turbocompressors.
Sulzer in the mix
In order to work effectively, the Ephyra system relies on efficient mixing of the material in each tank compartment. After searching the market for possible solutions, the main contractor selected Sulzer as a key supplier and technical partner for the project.
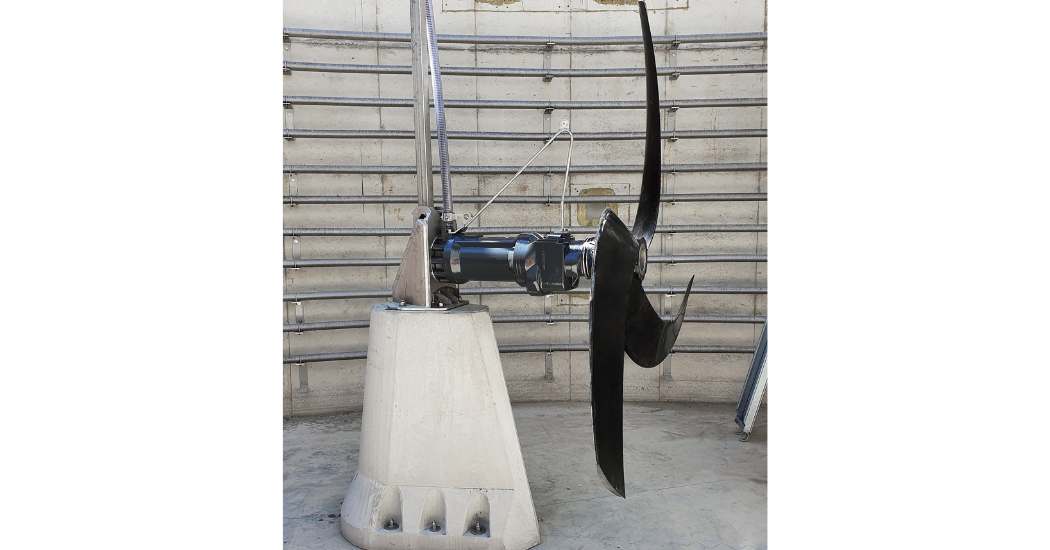
The floor-standing flow booster optimizes the sludge and air mixing process.
Flow through the system is highly complex, impacted both by the performance of the mixers and the effect of the pumps that move material between the tank compartments. Using computational fluid dynamics (CFD) simulations, Sulzer wastewater treatment specialists developed a customized sludge mixing approach that met the project’s requirements for performance and energy efficiency.
The Sulzer solution uses a combination of five top-entry SCABA agitators, ranging in size from 2.2 kW to 11 kW. Since the reactor tanks produce potentially explosive gases, each unit is built to Zone 1 ATEX specifications.
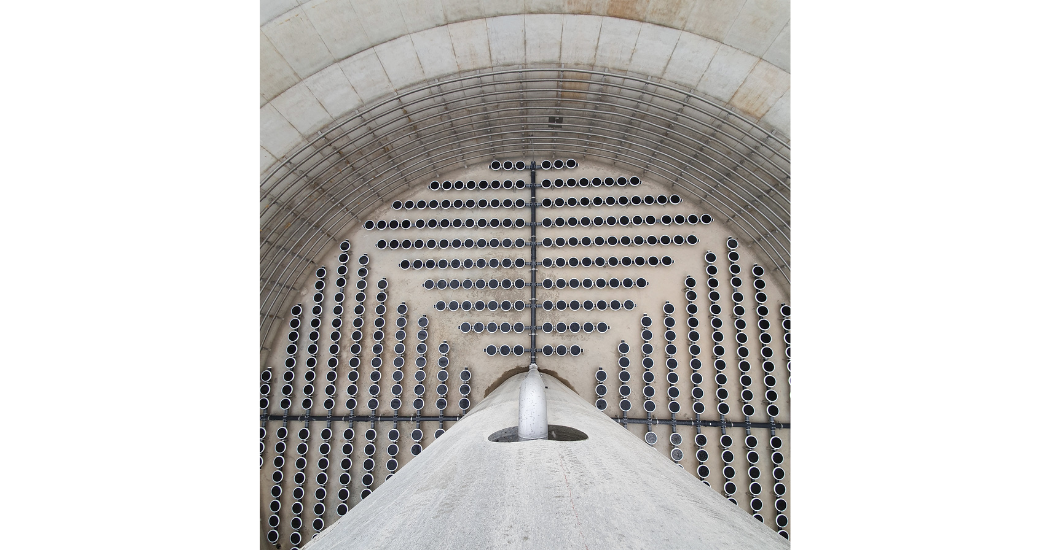
The configuration of the disc diffusers and pipework was designed by Sulzer for optimal efficiency.
Nitrogen neutralizer
After digestion, the sludge is pumped to another tank for concentration and nitrogen removal using the NAS-ONE anaerobic ammonium oxidation (anammox) process. In this part of the system, air is blown through the sludge to remove excess nitrogen, and once again, the contractor responsible for the work called on Sulzer’s expertise. Compressed air for this process is generated by two highly efficient HST 2500 turbocompressors, and enters the bottom of the tank through 480 DDS PRK 300 disc diffusers, arranged in three banks. One of Sulzer’s floor-standing flow boosters, the XSB 2232 LX, further ensures efficient mixing of air and sludge in the NAS-ONE system.
Elsewhere on the site, two XFP submersible pumps were installed in a sewerage pumping station and two others are responsible for pumping effluent to a buffer tank, from where it is transferred to the heat pump by one of Sulzer’s SNS pumps.
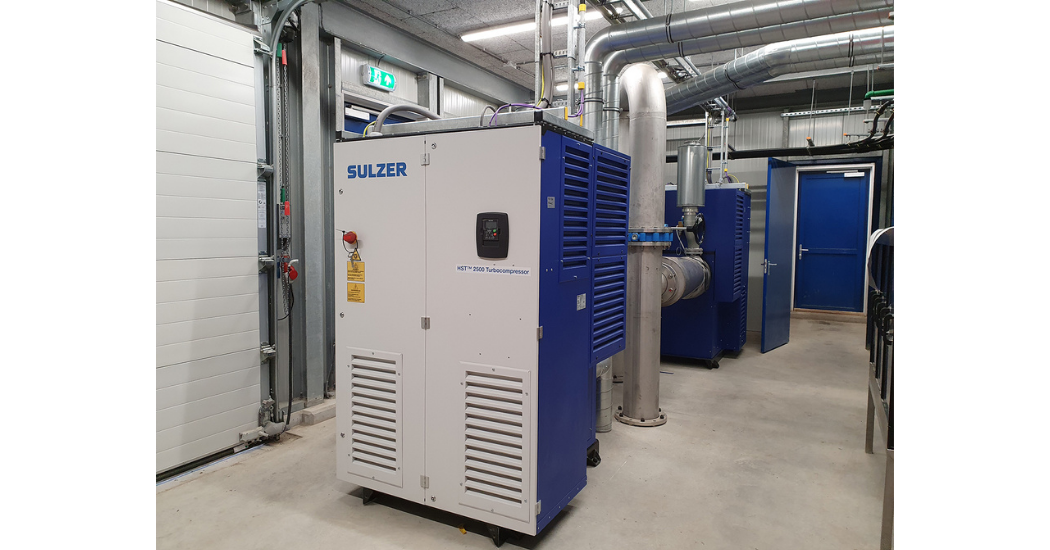
Compressed air for this process is generated by two highly efficient HST 2500 turbocompressors.
Execution of the whole project required Sulzer’s teams to work closely with the different contractors responsible for the Ephyra and NAS-ONE systems, delivering and installing equipment in accordance with the tight build schedules. Controls for the plant are complex and highly integrated too, with all equipment on-site connected to a master SCADA system. In the case of the NAS-ONE in particular, the HST compressors require extremely precise control to ensure the correct volume of air is always sent to the system, a feature that is built in to these products.
Construction and commissioning of all the equipment was completed on schedule during 2020. The Energy Factory began full operation at the beginning of 2021 and has been performing efficiently since.
About Sulzer:
Sulzer is a global leader in fluid engineering. We specialize in pumping, agitation, mixing, separation and application technologies for fluids of all types. Our customers benefit from our commitment to innovation, performance and quality and from our responsive network of 180 world-class production facilities and service centers across the globe. Sulzer has been headquartered in Winterthur, Switzerland, since 1834. In 2020, our 15’000 employees delivered revenues of CHF 3.3 billion. Our shares are traded on the SIX Swiss Exchange (SIX: SUN).www.sulzer.com Our shares are traded on the SIX Swiss Exchange (SIX: SUN). www.sulzer.com. The Pumps Equipment division specializes in pumping solutions specifically engineered for the processes of our customers. We provide pumps, agitators, compressors, grinders and screens developed through intensive research and development in fluid dynamics and advanced materials. We are a market leader in pumping solutions for water, oil and gas, power, chemicals and most industrial segments.