Using pump data to predict downtime and identify engineered solutions
For those in the energy industry, being able to identify pre-failure conditions and anomalous operation can offer a considerable advantage to a repeatable budget and bottom-line margins. Using this intelligence to permanently remove failure modes through retrofit solutions will further extend the service life of rotating equipment.
Seth Tate, Technical Advisor with Sulzer, looks at how a cutting-edge software solution can analyze existing pump telemetry to reduce downtime and justify engineering improvements.
Around the world, operators of high-energy pumps are well aware of the high running costs and therefore looking for effective and reliable strategies to reduce them. Implementing pro-active maintenance strategies is well-known to have a positive effect on downtime. Now it is possible to use data from existing sources to provide intelligence that will allow system availability and reliability to be improved.
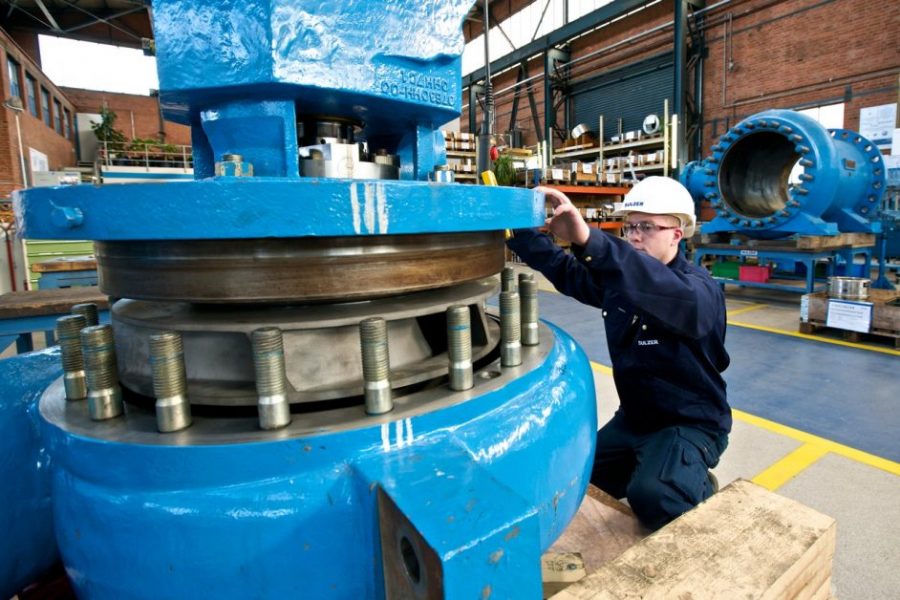
A well-organized pump repair workshop reduces downtime and minimizes costs
Cost of downtime
The reduction in maintenance costs and equipment repair time are directly linked to corrective maintenance strategies, such as preventative maintenance, discrete predictive maintenance or online predictive maintenance. As the techniques to identify pre-failure conditions become more sophisticated, it is possible to perform the right maintenance task at the most opportune time. In addition, the insight provided can also be used to justify retrofit solutions.
These extend the normal operating conditions of high-value assets. At the same time, predictive maintenance strategies can leverage existing data sources and maximize their efficiency by applying big data analysis principles. This enables operators to achieve maximum availability and throughput and when high-value commodities are involved, this can amount to a lost profit opportunity (LPO) of USD 200’000 per day.
In terms of performance and efficiency, a 4’000 hp (3’000 kW) pump operating at 43% of its best efficiency point (BEP) flowrate will present an LPO of approximately USD 300’000 per year. Looking at how reliability affects outcome, chronic seal failures in high-energy equipment can cost USD 18’000 per occurrence but including lost production can see costs rise to USD 144’000 per failure.
Therefore, being able to implement remedial actions during planned maintenance periods before component failure occurs as well as understanding the root cause of an issue can deliver considerable value for the business.
Pump data acquisition
In order to translate equipment performance data into actionable intelligence, the related sensors as well as a conduit between the sensors and software must exist. Many pumping systems already have the necessary resources to satisfy data acquisition needs. The historical performance data that is already being stored can provide insights that are essential for the active monitoring process. By making better use of this stored data, it is possible to accelerate the journey to realizing value.
Advanced pump analytics
By developing a software solution that integrates with existing data platforms, the opportunity already exists to conduct big data analyses. Equipment that is designed using advanced physics can be monitored under the same principles. Sulzer’s solution, known as BLUE BOXTM, creates a prediction map of equipment operation using both Sulzer’s expertise in failure mode and effects analysis (FMEA) modeling and machine learning intelligence.
What if operators were informed that equipment is running below minimum continuous stable flow? What advantage is there to knowing that a bearing is failing?
Using the gathered data, this advanced analytics approach goes beyond just a digital twin to detect pre-failure conditions and optimization opportunities. Key to the added value are an out-of-the-box readiness, false-positive prevention, advanced physics, and an operational dashboard.
At the same time as identifying future maintenance interventions, there is a requirement to derive the most effective solution and justify the cost in terms of lost performance or downtime that can be saved. This enables engineering managers to assess potential solutions and provide a cost analysis, all before the predicted issue has an impact on production.
Retrofit to improve existing assets
Having identified the issue, retrofit solutions can be used to permanently remove causes of failure through improved engineering, design, maintenance or operation. The best course of action can be identified through gap analysis – comparing the current solution, which is experiencing reliability issues, to the best-in-class design. Today, the latest engineering technology can do more than just remove specific failure causes on legacy equipment.
In addition, retrofits can be implemented to address new or updated hydraulic needs. Having identified the performance topography, a new hydraulic profile can be manufactured without disturbing the footprint of the pump installation by applying computational fluid dynamics (CFD) and an original equipment manufacturer’s (OEM’s) considerable hydraulic experience.
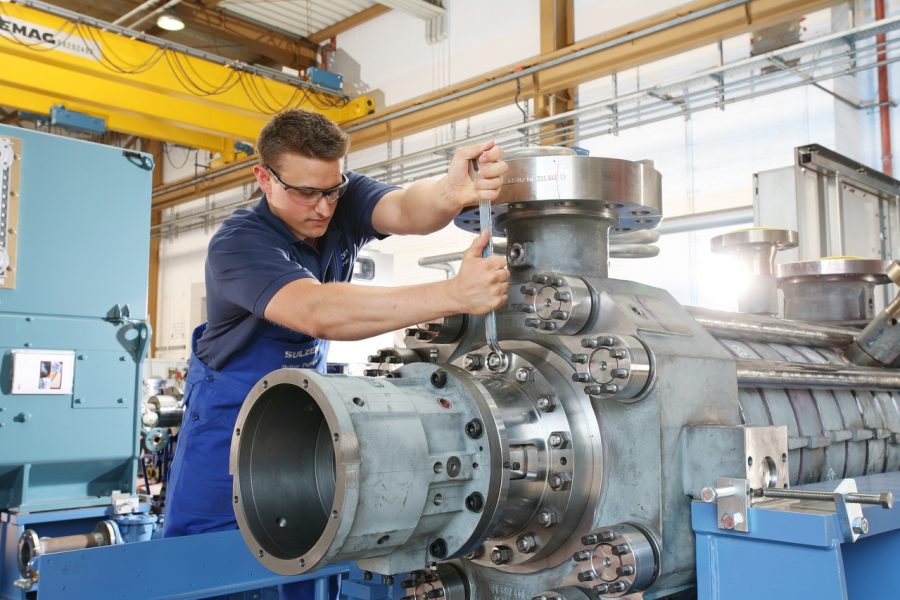
Retrofit solutions can be used to permanently remove causes of failure through improved engineering, design, maintenance or operation
Total cost of ownership
In a world where downtime can be measured in hundreds of thousands of dollars per day, even modest improvements in availability can have a significant improvement in operating costs. For instance, an improvement of 0.08% in the performance of a high-energy pump will equate to 72 hours per year of uptime that would have otherwise been lost. This can potentially deliver an improved annual income of approximately USD 650’000.
In the example of pump performance, the data analysis solution can illuminate tangible opportunities for effective improvements. In addition, removing the residual effect with off-BEP performance can eliminate failure modes and extend the service life of the pump, promoting uptime and reducing the total cost of ownership (TCO). Putting this into numbers, recovering 32 efficiency points equates to approximately USD 290’000 in running costs.
Expert pump support
As an original equipment manufacturer (OEM), Sulzer has combined its expertise in pump engineering and extensive experience in pump operation to create BLUE BOX, an advanced analytics solution that can deliver expert insight into any pumping system.
Simple integration, with no additional hardware and a secure interface, BLUE BOX uses existing telemetry and communication protocols to analyze the data. It is designed to grow with future technological changes and provide continuous visualizations through a customized operator dashboard. Now, it is possible to predict the future of maintenance operations and use this information to optimize business performance.
Author bio: Seth Tate is a Technical Advisor at Sulzer, with 15 years’ experience in equipment maintenance and reliability. He has been a pipeline SME, refinery engineer, and a mechanical seal engineer. He contributes to the efforts of the Society for Maintenance and Reliability Professionals (SMRP) and is a certified reliability leader through the Association of Asset Management Professionals (AMP). This experience has enabled him to become an expert in delivering technical direction, supervision, and repair training for Sulzer’s customers as well as offering economically justified long-term solutions.
About Sulzer
Sulzer is a global leader in fluid engineering. We specialize in pumping, agitation, mixing, separation, and application technologies for fluids of all types. Our customers benefit from our commitment to innovation, performance, and quality and from our responsive network of 180 world-class production facilities and service centers across the globe. Sulzer has been headquartered in Winterthur, Switzerland, since 1834. In 2019, our 16’500 employees delivered revenues of CHF 3.7 billion. Our shares are traded on the SIX Swiss Exchange (SIX: SUN).
Throughout the Americas, Sulzer provides cutting-edge parts as well as maintenance and repair solutions for pumps, turbines, compressors, motors, and generators. We service our own original equipment as well as third-party rotating equipment operated by our customers. Our technology-based solutions maximize reliability and lifecycle cost-effectiveness.
For more information on Sulzer, visit www.sulzer.com