A lantern ring is a perforated hollow ring located near the center of the stuffing box of a pump. Despite its simplistic appearance, it plays a crucial role in the successful operation of a pump system.
The Lantern Ring’s Role
Lantern rings simultaneously serve three main purposes:
Protection — The term lantern ring comes from the primary use of the word lantern. A lantern is a vessel or device that covers up or protects a light source. Lantern rings help protect the stuffing box by allowing flush water or pressure to enter. They also keep contaminants out. If the material that is being pumped or any other foreign matter enters the stuffing box, it could destroy the packing or damage the shaft or stuffing box.
Outlet for cooling — Lantern is also an architectural design term for a structure on top of a roof or in an attic that allows for ventilation. These structures allow buildings to breathe. Lantern rings provide an opening and assist cooling in the stuffing box. This keeps the system from being completely closed off.
Lubrication — Another main function of the lantern ring is to facilitate lubrication. The fluid entering the lantern ring lubricates the packing. This reduces friction against the shaft. In addition, lubrication helps reduce wear of the machine parts and the amount of excess heat generated within the system.
Only Used with Packing
In these three applications, lantern rings are only used in conjunction with packing. It is a crucial element, because packing tends to generate heat. Heat increases wear that could shorten the life of the packing and the shaft. Placing a lantern ring between packing rings extends the life of the packing, the stuffing box, and the shaft. Ultimately, this increases the lifespan of the whole system long term.
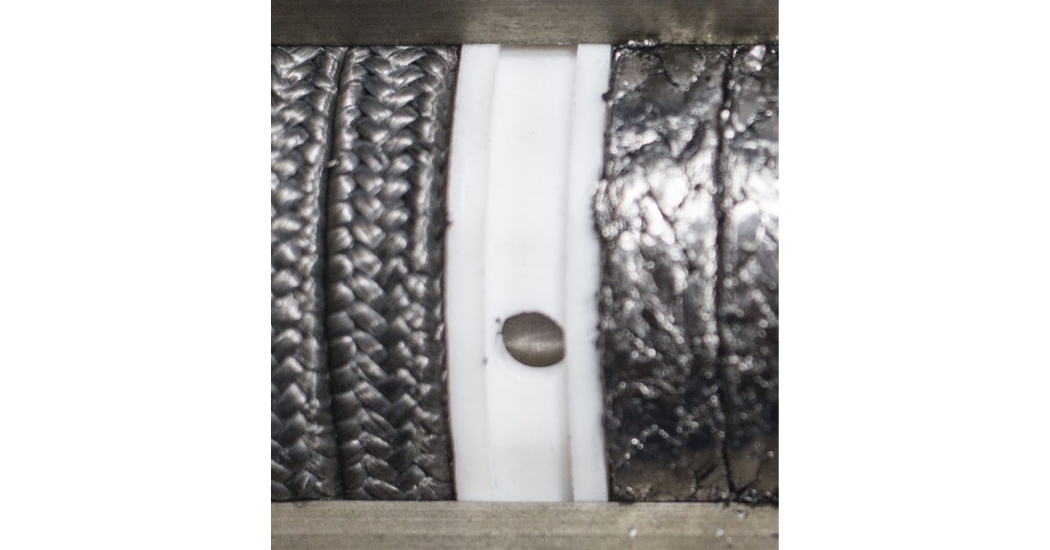
A lantern ring installed between compression packing rings
Many times, end users overlook lantern rings within the system because they do not perform the sealing function. Primarily in a stuffing box, teams focus on the packing and which style to use. However, the lantern ring is just as important as the packing. Without the lantern ring to provide protection, ventilation, and lubrication, the packing will not function properly.
The Ideal Material: PTFE vs PEEK for Lantern Rings
Using lantern rings that are made from the right kind of quality material is critical. Low-quality plastic material options will soften and melt much more quickly and easily over time. If this happens, the ability to protect, cool, and properly lubricate the packing is greatly diminished. This will lead to premature packing failure.
Manufacturers primarily make most lantern rings out of either polytetrafluoroethylene (PTFE) or polyether ether ketone (PEEK). Before PTFE was so widely used, lantern rings may have been made out of many different materials, such as brass, bronze, low-quality plastics, or metal. Some plants use these other materials in some instances.
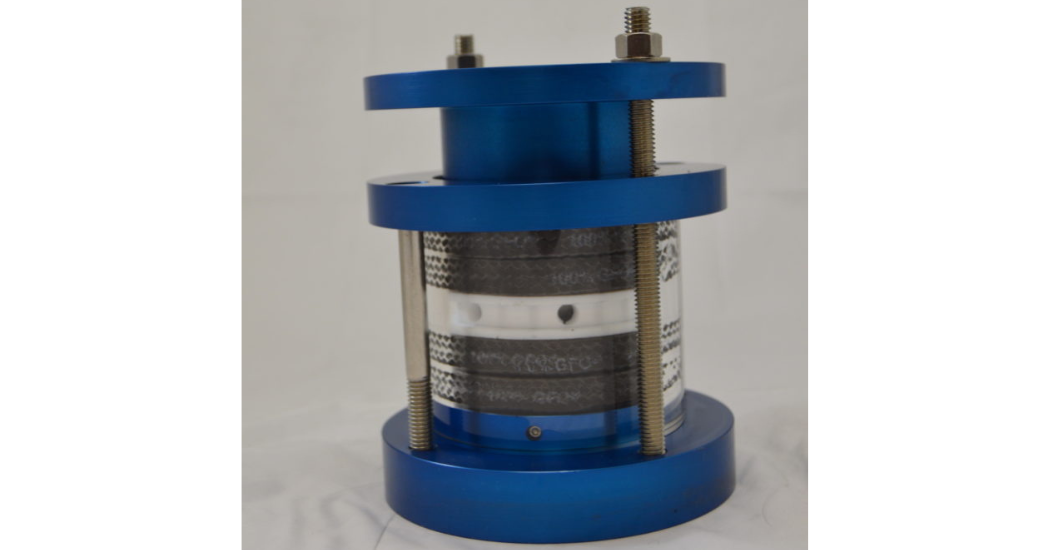
A lantern ring and packing installed in a clear stuffing box
Choosing the right material includes several considerations:
- Will the system operate in a water-tight or air-tight environment?
- What kind of lubricant will be used?
- What are the system pressure demands?
- How much flexibility is needed?
- Are there components with abrasive or hard-wearing qualities?
- What is the reactive nature of the materials contacting the lantern ring?
- Are there any hygienic considerations?
- What are the operating temperatures?
- Will maintenance be easy or difficult?
- Are there any financial limitations?
PTFE
PTFE has become the standard for lantern rings because the flexible material holds a wide temperature range. It will tolerate temperatures from -300℉ to 500℉, which provides roughly an 800℉ temperature range. Few other materials can withstand such a wide range. Other benefits of using PTFE for lantern rings include the fact that it complies with FDA regulations and is chemically resistant. These properties make it a universal material for lantern rings.
PTFE strengths are:
- Broad chemical resistance
- Nonflammable
- Flexible at low temperatures
- Low coefficient of friction
- Stable at high temperature
- Relatively easy to process
- High-frequency resistance
PTFE weaknesses are:
- Creep and cold flow
- Relatively soft
- Low thermal dissipation
- Poor dimensional stability
- High material shrinkage
- Low rigidity
- Low electrical conductivity
PEEK
While PTFE may be the standard choice for lantern rings in many instances, there are high-temperature applications in which the temperature of the stuffing box could potentially exceed 500℉. In these situations, PEEK is a better material to use for lantern rings. PEEK is always a good choice and performs well, but it is more costly. It is the premier material. However, because of its higher price, plants typically use PTFE about 95% of the time.
PEEK strengths:
- Excellent tensile strength, elongation, and wear properties
- Superior chemical resistance
- Withstands long exposure to high pressure, water, and steam
- Excellent chemical resistance
- Very low flammability
- Resistant to gamma radiation
- Continuous use up to 500℉
PEEK weaknesses:
- Not suitable for applications involving nitric or sulfuric acid
- More costly
- Difficult to process
Make the Right Selection
Choosing the right material for a lantern ring is a critical decision when taking a total systems approach. Lantern rings should be given equal consideration because they are equally as important as packing.