In many pump systems, a mechanical seal is the first component to fail. Often, however, the seal is not to blame. Other culprits include:
- Improper seal installation
- Wrong seal choice
- Lubrication contamination
- Bearing wear
- Vibration
- Misalignment
Pinpoint the Root Causes of Failure
How do plant and maintenance managers identify the root cause of the failure? One way is to have a seal manufacturer perform a seal failure analysis. Sealing Equipment Products Company (SEPCO) has provided this service for many years and analyzes its technology as well as seals from other manufacturers. End users simply send their mechanical seal to our experts or members of our team can come on-site if multiple seals need to be diagnosed. Usually, if a seal is mailed to our experts, the analysis can be completed in about two weeks.
Takeaways from the Analysis
With a seal failure analysis from SEPCO, end users receive a complete diagnosis of why the mechanical seal failed and what actions they should take to prevent future failures. A sealing failure analysis helps end users in multiple ways. The experts who examine the seal can ensure that the ideal seal for the application is being used. If not, they will make recommendations of alternative technologies.
The team will also help end users optimize their operating conditions and achieve the best possible run from their assets. Optimizing mechanical seal performance will also improve shutdown to shutdown processes. This information along with alternative proposals as needed will help end users prevent further failures and improve their return on investment.
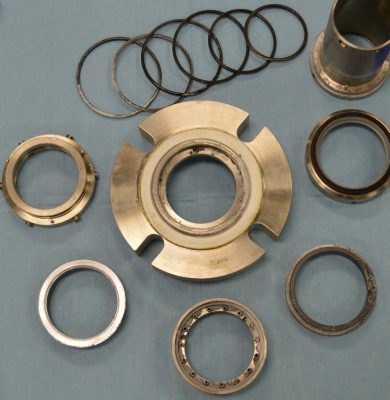
Mechanical seal experts disassemble the seal and examine all aspects to determine the true cause of failure.
Major Benefits of Seal Failure Analyses
A sealing failure analysis will help you:
- Improve environmental controls
- Choose the best installation methods
- Prevent future equipment failure
Comments