Air seals effectively seal solids and powders, and require no maintenance or flushing.
By their nature, dry powder handling machines are difficult to seal, and air seals may be an updated solution. Bulk solids and powders are transported and handled in many industries, including:
- Chemical
- Food and beverage
- Pulp and paper
- Pharmaceutical
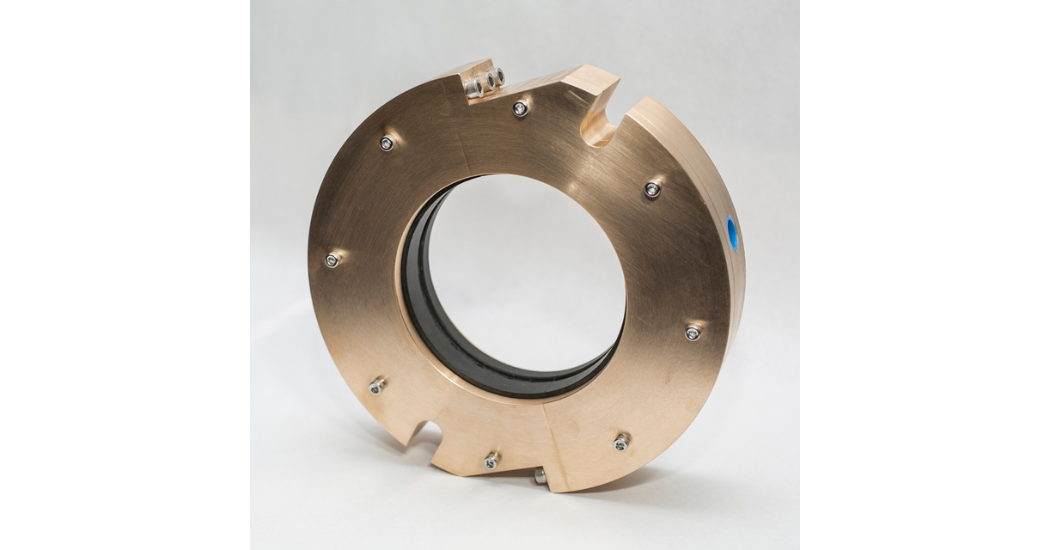
Image 1. An air seal
Traditional methods are packing, air purge seals, or in-face and other mechanical seals. With these methods, the product contacts the sealing element and leads to accelerated wear of the sealing components and the shaft/sleeve of the machine. Excessive wear leads to product loss and higher overall operating costs. Another challenge in sealing dry powder equipment is that many of the vessels are fabricated, and the seal must mount against the wall of the vessel, which may be perpendicular to the shaft.
An air seal (see Image 1) is designed to accommodate some shaft movement, conditions that are difficult, in some cases, to seal effectively. Packing may stabilize the shaft. However, depending on the service and operating conditions, it will also fret the shaft or sleeve to a point where the product is no longer sealed and it ends up on the floor. Also, air seals have been successfully used in wet applications, such as hydro pulpers, agitators, mixers and some slurry pumps.
Operation of Air Seals
Air seals use engineered clearances and directional flow paths. These create uniform pressure and velocity profiles, generating a pneumatic seal. To accommodate the inherent misalignment that may be present in many of the applications in which this technology is installed, a floating throttle is used that handles ±0.125 inch of parallel movement.
By controlling the internal pressure or flow profile, a circumferential boundary layer of air is formed between the throttle and the shaft/sleeve. This boundary mitigates any damage that would occur because of mechanical runout because the throttle floats on the boundary layer.
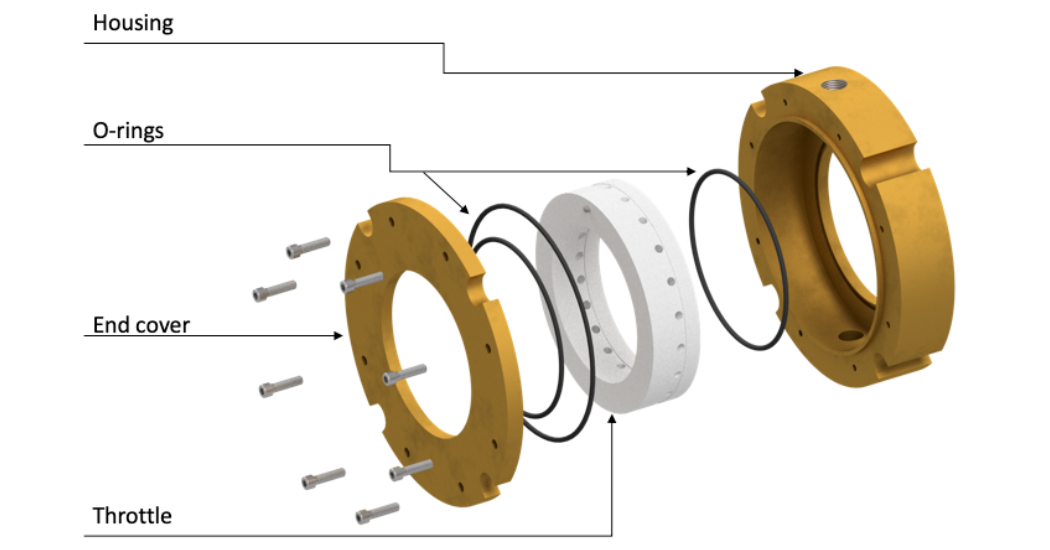
Figure 1. Exploded view of an air seal
Installing Air Seals
The air seal comes in solid and split configurations and is designed for ease of installation. Proper installation of the seal is achieved by using spacers that dictate the gap between the seal housing and the shaft. The throttle floats and no adjustment is required on installation.
Adequate air supply and auxiliary hardware must be installed as shown in Figure 2 for each seal. Startup of the system is predicated on the air being turned on at least 1 minute before product is introduced to the machine. This ensures that the seal body is at the required pressure.
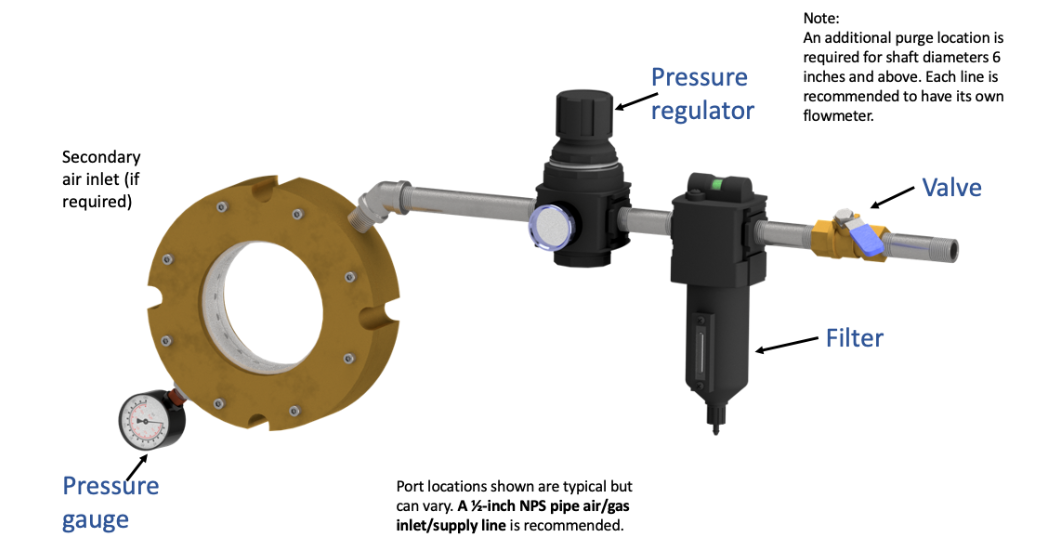
Each air seal must have an air system.
No Maintenance Required
These air seals require almost no maintenance as long as air flows continuously to the seal. By design, product will not enter the seal or throttle area, which eliminates the need for maintenance. Its materials of construction keep wear and corrosion from occurring. However, system upsets occur, and if product enters, the seal can be easily disassembled, cleaned and reassembled.
If the air supply is turned off during operation and with product inside the equipment, the product may enter the seal. This will lead to the internal air passage way becoming clogged, disrupting the uniformity of the pressure profile. Should this happen, seal disassembly may be required. The seal is very simple and can be easily rebuilt, but contact the manufacturer if this occurs.
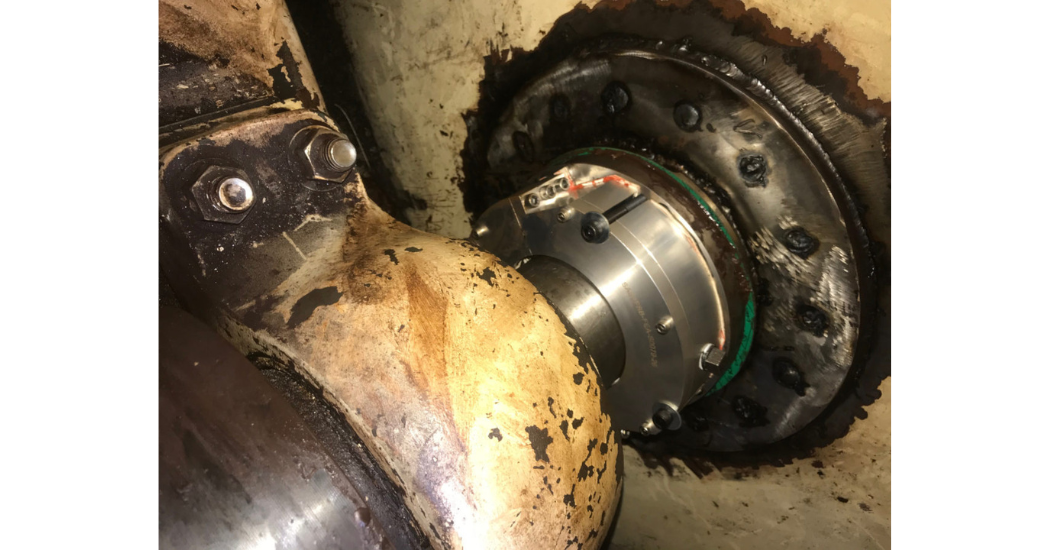
Image 2: This air seal completely contained a conche for a large chocolate producer.
Conclusion
With the development of air sealing technology, end users will experience a dramatic reduction in operational costs of the machine because of the mitigation of maintenance, repair, and cleanup and the elimination of product loss.
Air Seal Features & Benefits
The design minimizes air use while maintaining the internal sealing pressure profile.
When installed correctly the seal is a non- contact design and will run without issue for the life of the equipment.
- Air seals are resilient to angular and parallel shaft movement.
- The seals are available in solid and split designs.
- They require little to no maintenance when installed and operated correctly.
- Applicable to bulk handling material assets, including:
- Mixers
- Blenders
- Agitators
- Pulpers
- Screw conveyors
- Refiners
- Rotor valves
About the Author
Mikal Hayes is an applications engineer for SEPCO and a member of the Processing Editorial Advisory Board. Hayes’ roles include designing, analyzing and testing new mechanical seals, bearing isolators and air seals — with a focus on product research and development. Hayes received his BSME from the University of Alabama at Birmingham (UAB).
Articles & Media Mentions
How air seals work.