These materials make up the base of 99% of plastics used in most industries.
Many types of industrial plastic can be found everywhere. Plastic is inexpensive, lightweight, durable, and easy to modify. This explains why its usage has increased rapidly and continues to grow.
All plastic is industrialized, and different plastic products have distinct properties. These properties can be seen primarily in their:
- Thermal-resistance
- Physical and mechanical properties
- Density
- Structure
Plastic consists of polymers, which are large organic molecules. The molecules are composed of repeating carbon-based units or chains. Polymers are produced when molecules called monomers form long chains in a process called polymerization.
High-Performance Plastics for Critical Applications
This article focuses on engineered, high-performance plastics often used for or with critical sealing technology. Five base materials are used 99% of the time. They are often used to design compounds by adding fillers to suit specific applications, such as the following:
- A throttle in an air seal
- A lantern ring for a stuffing box
- Bushings or bearings for shaft stabilization
The plastics used are important. These components cannot be constructed from any plastic on the shelf. These five are the primary bases for most industrial, high-performance plastics. Each has unique characteristics, strengths, and limitations. A plastic should be selected carefully to match the parameters of each application.
1. Polytetrafluoroethylene
Polytetrafluoroethylene (PTFE), a universal material, performs well in many applications. It is the most commoditized of the engineered industrial plastics because of its dependable nature for many purposes.
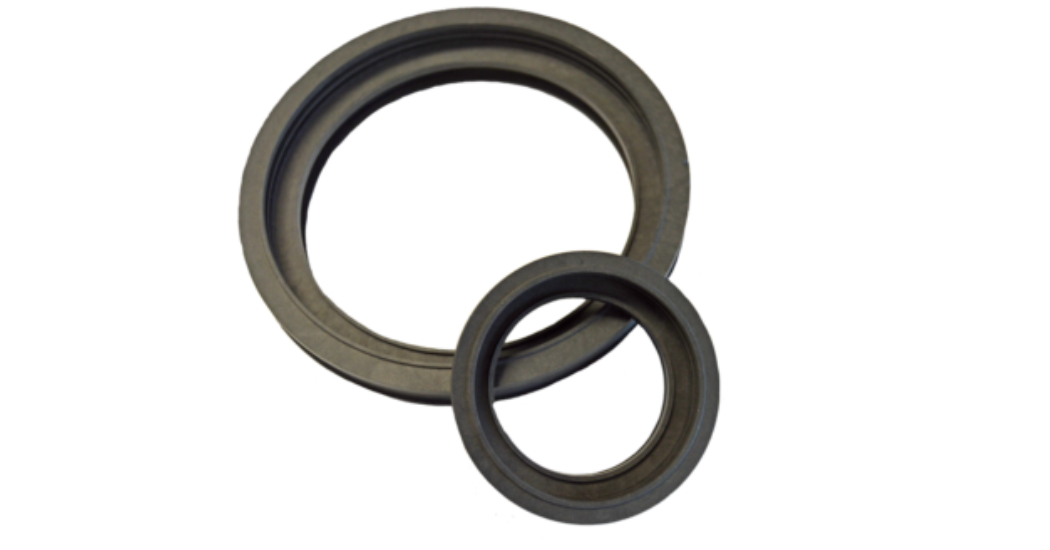
An example of PTFE
PTFE has a wide temperature range and broad chemical resistance. An inexpensive option, it is compatible with most other materials. Table 1 details the material’s strengths and limitations.
Strengths | Limitations |
Broad chemical resistance | Creep and cold flow |
Nonflammable | Relatively soft |
Flexible at low temperatures | Low thermal dissipation |
Low coefficient of friction (COF) | Poor dimensional stability |
Stable at high temperatures | High material shrinkage |
Relatively easy to process | Low rigidity |
HF resistance | Low electrical conductivity |
Table 1. PTFE strengths and limitations |
2. Polyethylene Terephthalate
Polyethylene terephthalate (PET) is a very hard, dense material. It is primarily used for bearings and bushings. With a relatively low service temperature, it is only good to about 210℉.
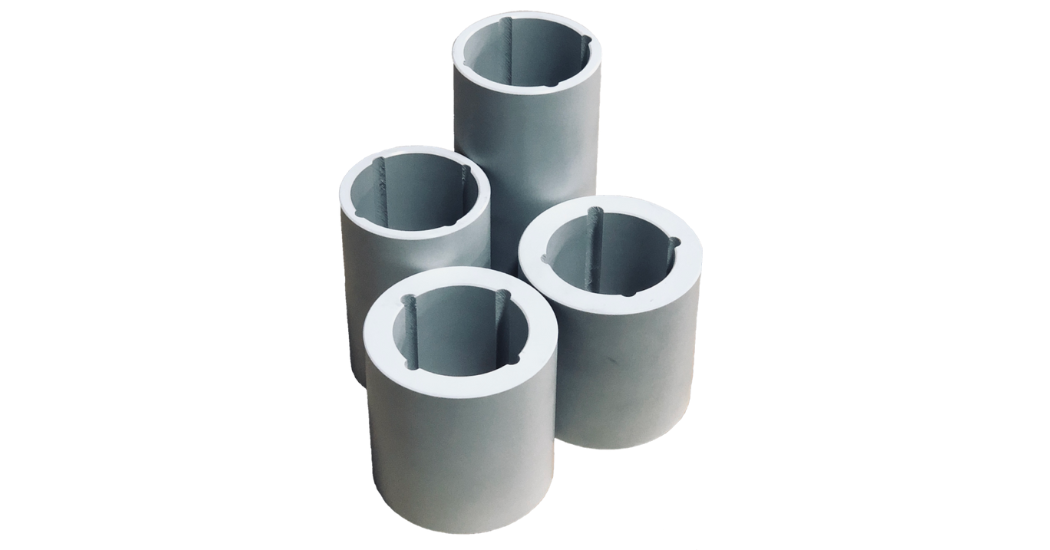
An example of PET
PET is primarily used in conjunction with proprietary fillers for vertical pump bushings. It is very dimensionally stable, fairly inexpensive, and easy to machine. Table 2 details its strengths and limitations.
Strengths | Limitations |
Very rigid and strong | Low melting point |
Good dimensional stability | Narrow chemical resistance |
Low COF | |
Hydrophobic | |
Easy to machine | |
FDA approved for food and liquid contact | |
Table 2. PET strengths and limitations |
3. Polyphenylene Sulfide
Polyphenylene Sulfide (PPS) is a higher cost, very hard material. It has a broad temperature range and chemical resistance. Sometimes, it is referred to as PET’s older, more established brother. PPS has about the same hardness as PET but with broader chemical and temperature resistance. Its range is 500℉ to 550℉.
PPS primarily appears as shaft stabilizing bushings. Anytime a shaft has run out or wobble, a PPS bushing stabilizes the shaft. It works in conjunction with the whole system:
- The PPS bushing
- A lantern ring
- The packing
- These all make up a stuffing box.
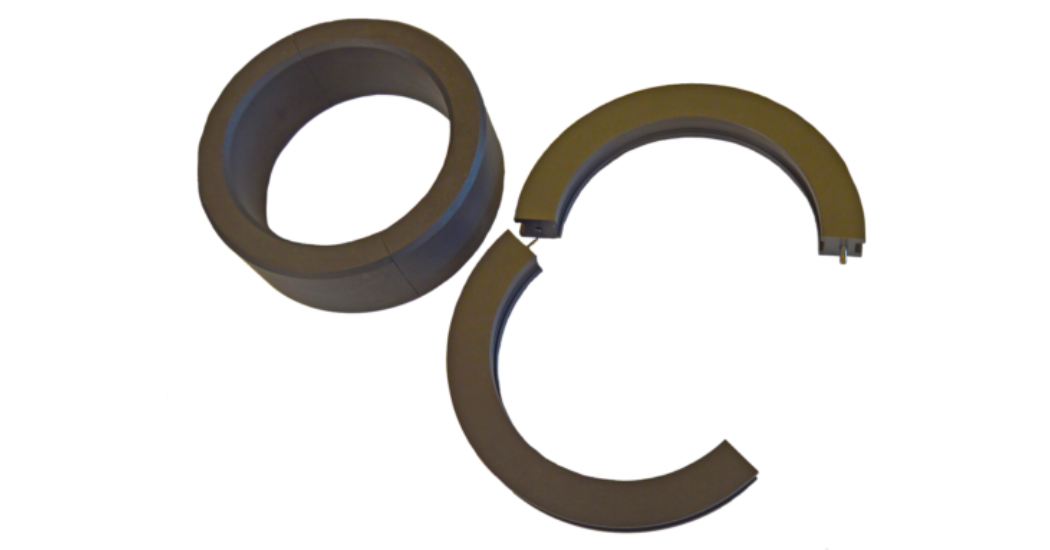
An example of PPS
Two types of PPS are available: linear and branched. Table 3 details the characteristics of each, and Table 4 lists the strengths and limitations of both.
Linear | Branched |
Long linear molecular chains similar to PTFE | High rigidity |
Higher tensile strength and elongation | Increased hardness |
Better melt stability | Increased dimensional stability |
Less prone to absorbing moisture | Increased creep resistance |
Better impact resistance | More difficult to process and generally requires pre-curing/cross-linking |
Table 3. Linear and branched PPS characteristics |
Strengths | Limitations |
Excellent chemical and radiation resistance | Can be very brittle |
Excellent water absorption | Poor resistance to chlorinated hydrocarbons (Example: vinyl chloride and chloromethane) |
Dimensionally stable | High cost |
Superior abrasion resistance | Challenging to process |
Continuous use up to 450℉ | |
Table 4. PPS strengths and limitations |
4. Polybenzimidazole
Polybenzimidazole (PBI) is a high-temperature material. it withstands temperatures up to almost 900℉. This makes it an ideal plastic when dealing with difficult, high-temperature chemical applications. It is chemically resistant and dimensionally stable. Many experts consider it the Lamborghini of materials because it can do almost anything.
Strengths | Limitations |
Highest compressive strength of any unfilled resin | Can be brittle |
Excellent tensile and flexural strength | Expensive |
Dimensionally stable | |
Very low creep | |
Low COF | |
Continuous use up to more than 800℉ | |
Table 5. PBI strengths and limitations |
5. Polyether Ether Ketone
Polyether ether ketone (PEEK) is most similar to PPS with the main difference that PEEK is not brittle. It is basically a flexible version of PPS with the same temperature range. The concern with PPS is that it might break or fracture. With PEEK that is not a concern. Therefore, this makes it the plastic of choice in many applications.
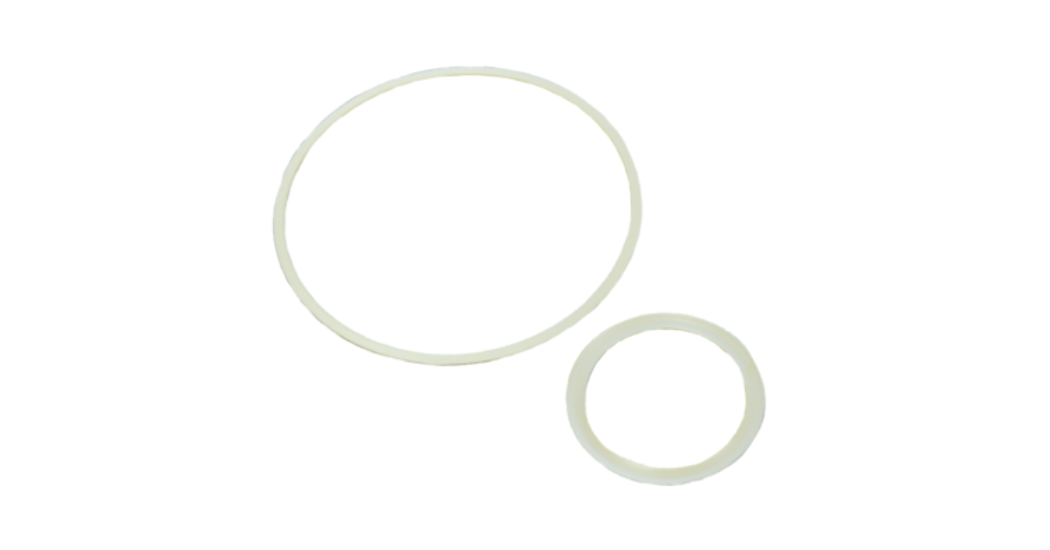
An example of PEEK
However, PEEK is more expensive partly because of this flexibility. It is often chosen for high-pressure applications. For example, PEEK might be used to make a lantern ring for a high-temperature and high-pressure application.
Strengths | Limitations |
Excellent tensile strength, elongation, and wear properties | Not suitable for nitric or sulfuric acid |
Superior chemical resistance | Expensive |
Withstands long exposure to high pressure water and steam | Difficult to process |
Excellent chemical resistance | |
Very low flammability | |
Resistant to Gamma radiation | |
Continuous use up to 500℉ | |
Table 6. PEEK strengths and limitations |
High-Performance Industrial Plastic Trends
The mass production of industrial plastics began in the 1950s, and since then, the industry has grown exponentially. Why? According to the Plastics Industry Association, it is the diversity of plastic applications that makes the industry so unique and able to continually expand. It has grown to include new materials and new markets that the industry’s earliest practitioners may never have expected or predicted.
Plastic technology continues to increase in terms of what plastics can do. They replace metal components in industrial applications because they are versatile, lighter and stronger. They also do not corrode. For example, lantern rings were once almost always made out of brass. Today, they are most likely made from PTFE or PEEK. Similarly, some materials that were once bronze are plastic now.
While these trends in the sealing industry occur, uses for plastics are expanding. Plastics are taking center stage in the automotive industry, particularly PBI, PPS, and PEEK. These plastics are noncorrosive and lighter than automotive components previously made of metal.
Another area of expansion is 3D printing plastic components for many different applications. Previously, machining an industrial plastic part for a specific purpose was impossible. Now, 3D printing may make it possible.
Once a plastic component is installed, it may have a very long life. The technology continues to improve, and over time, plastics will be seen in even more applications. Plastics are the future of many industrial applications. High-performance industrial plastics for the sealing industry will grow. They may also be used in previously unheard-of ways.
About the Author
Lori Ditoro joined SEPCO in November 2018 as content marketing manager. Before that, she was content marketing strategist for Fluke Accelix; editorial director of the Process Flow Network, publishers of Water Technology, Processing, and Flow Control; editor of Pumps & Systems; and editor of Upstream Pumping. In her roles, Ditoro has learned about the process and manufacturing industries and the equipment and technology that keep plants and other facilities operating. She also developed a passion for telling the operators’ and technicians’ stories.