Authors: John Conway and Jack Creamer, Schneider Electric
This is Part 2 of a series. Read Part 1.
That are the three distinct operational environments will set the stage for the smart manufacturing enterprise to emerge.
Smart Enterprise Control:
One of the biggest potential benefits of next generation IIoT systems is the breakdown of enterprise silos. The technologies will allow for closer integration of production systems and ERP systems, Product Lifecycle Management (PLM) systems, Supply Chain Management and Customer Relationship Management (CRM) systems (see Figure 1). Today these systems are managed somewhat independently of each other, which prohibit a holistic view of the enterprise. It is believed such a holistic approach could facilitate an enormous efficiency gain of up to 26 per cent¹ for enterprises.
Smart enterprise control does not mean replacing current automation systems with completely new systems. Instead, it implies the connection of current automation systems with enterprise, lifecycle and value chain systems. This optimizes the entire manufacturing enterprise and enables a much greater degree of business control.
Tighter integration will allow enterprises to not only be more efficient, but also more profitable thanks to greater flexibility and responsiveness to volatile market conditions. The notion of control will expand from the real-time control of a physical parameter, to the right-time control of the whole business, including both physical and non-physical parameters. Benefits will include the ability to enhance protection against cyber threats, more innovation, and the ability to better manage safety, performance and environmental impact.
Examples of smart enterprise control include the following: mass customization and lot sizes of one, reducing the size of product recalls, detection of defective products earlier in the manufacturing process and modification of product design to eliminate root causes, modification of production planning based on weather forecasts, modification of production plan/recipes based on the spot price of raw materials.
Asset Performance:
Asset performance management applications such as energy management and predictive maintenance are not new to industry, but have had limited uptake due to the cost of implementation. The costs of physical connectivity (the cost of cabling to the sensors) and logical connectivity (integration with existing systems) have been prohibitive. Wireless IP connectivity and cloud-based architectures now overcome these cost barriers. In addition, a new generation of simple, small and low cost sensors is emerging; As a result, next generation IIoT systems will deliver innovative solutions in the area of asset performance (see Figure 2).
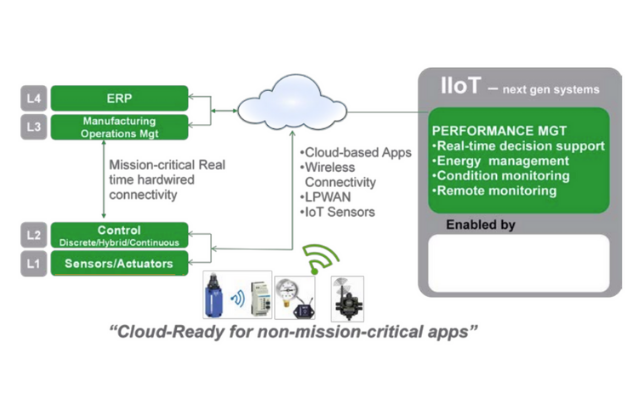
Figure 2 Asset performance accel- erates the adoption of new performance management applications leveraging big data and analytics, and cost effective wireless technologies.
Consider the example of condition-based monitoring/predictive maintenance. Much money is wasted maintaining equipment that doesn’t require maintenance, or by neglecting equipment that subsequently fails and causes unanticipated production downtime. Solutions such as condition-based monitoring do exist today, but uptake has been limited by cost. Next generation IIoT systems promise to significantly reduce implementation costs for such solutions.
Augmented Operator:
The use of mobile Human Machine Interface (HMI) technologies such as smart phones, tablets and wearable, combined with IP-access to data and information (analytics and augmented reality) will transform the way operators work. Portable wireless devices will expand their capabilities and technologies such as dynamic QR codes will improve the operator experience and render the “augmented” operator more productive (see Figure 3). Today, operators only have access to information from automation systems. Tomorrow, augmented operators will access information from all of the needed enterprise systems and will manage not just process performance/efficiency, but also process profitability.
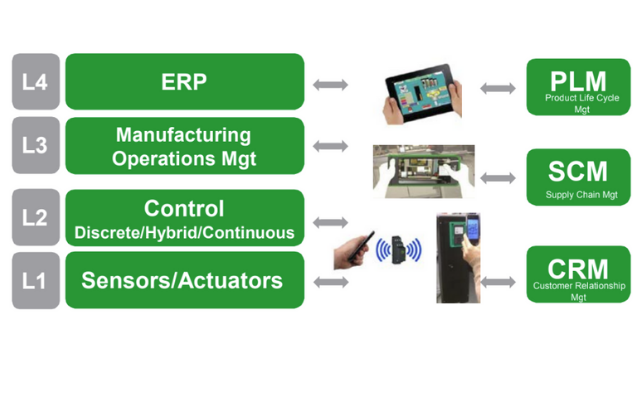
Figure 3 Augmented operators are more productive because they receive the right information at the right time.
Today, operators only have access to information from automation systems.
Tomorrow, augmented operators will access information from all of the needed
enterprise systems and will manage not just process performance/efficiency, but
also process profitability.
Read Part 3: Barriers to Adoption (coming next week!)
About the Authors:
John Conway is Schneider Electric’s VP for Strategy & Partnerships. In this capacity, he is responsible for strategic intelligence, strategic planning and merger & acquisition activities for the Industry Business Unit. During his 17 years with the company, he has held a variety of roles, starting out as director of microelectronics key accounts. He then moved into the creation and deployment of automation solution centers in Asia and Eastern Europe before running the Advanced Services and Mergers & Acquisitions activities for Industry. Prior to joining Schneider Electric, John held sales and engineering management positions within the automation divisions of Siemens and Texas Instruments. John has a Bachelor of Science in Mechanical Engineering and a Master of Science in the Design of Machine Systems. He is currently based at Schneider Electric’s Horizon office in Carros, France.
Jack Creamer is Schneider Electric Segment Marketing Manager – Pumping Equipment, based in the United States. Mr. Creamer has more than 30 years in the Electrical Industry, and has been involved for 10 years in the Pumping Industry. He is involved in key industry organizations such as the Hydraulic Institute and Submersible Wastewater Pump Association, where he holds both Committee Chair and Board level positions. In his time in the Pump industry, he has help Schneider create numerous solutions that both enhance pumping efficiency and address issues such as maintenance and downtime.
Comments