Author: Tom O’Donnell
There is no question that water is the lifeblood of boiler operation, whether the boiler is used for power generation or as a way to heat commercial buildings, hospitals or schools. With water being so integral to the boiler’s ability to produce the steam that can be converted into heat, it is imperative that the water – which can be rife with impurities that can result in rust, scale, corrosion and, ultimately, boiler failure – be properly treated so that the impurities are removed or neutralized.
Boiler-water treatment generally involves the injection of any of a wide array of chemicals into the boiler water. These chemicals must be dosed at highly accurate rates and speeds so that they themselves do not interfere with the quality of the water and the operation of the boiler. This means that the operator must identify and employ the right type of chemical-injection technology, one that will deliver reliable injection and flow rates no matter the amount of chemical that is required.
This white paper will illustrate how hydraulic and solenoid actuated diaphragm metering pumps, along with filter feeders, can be the ultimate solution for the accurate, reliable injection and dosing of chemicals that are critical to maintaining proper boiler operation.
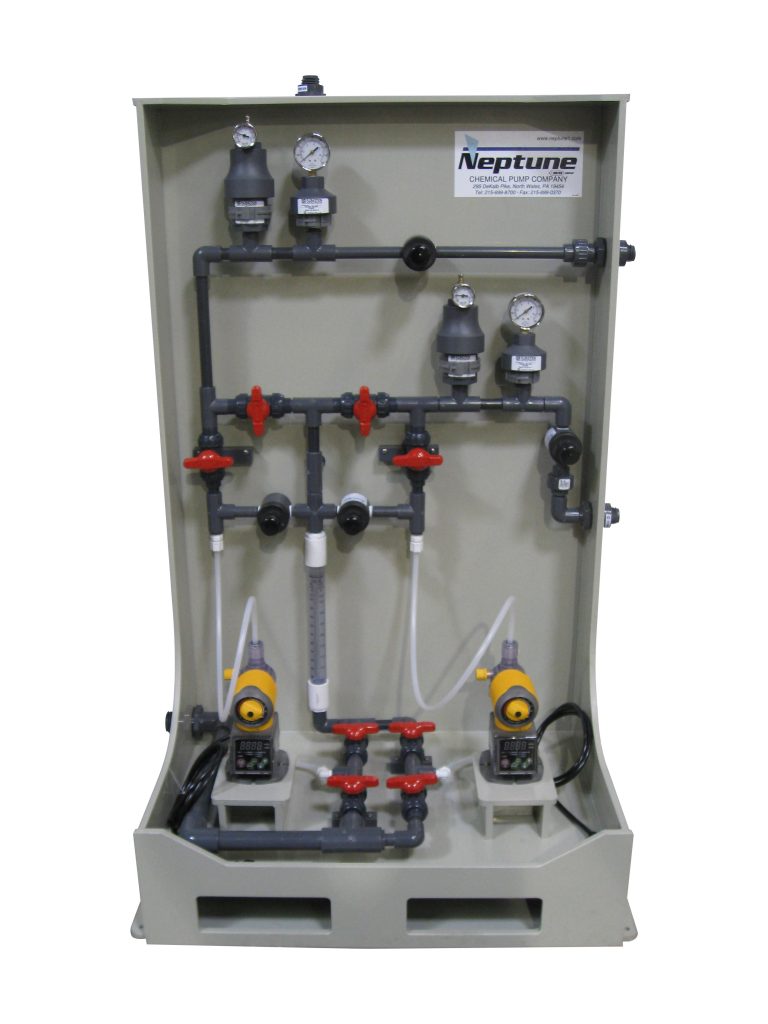
Boiler-water treatment involves the injection of any of a wide array of chemicals into the boiler water, all of which must be dosed accurately and reliably in order to guarantee that the boiler components will not experience any costly mechanical failures.
The Challenge
It’s a fact of boiler life that impurities in water will leave solid deposits like scale, rust and corrosion as steam evaporates. Over time, the accumulated deposits will thermally insulate the boiler’s heat-exchanger surfaces, which will not only gradually reduce the boiler’s rate of steam generation, but also cause boiler metals to approach failure temperatures.
This is where the treatment of boiler water enters the picture. The different types of boiler-water chemicals are designed to perform different functions, depending on the boiler system and water utilized. Some chemicals are added to maintain desired pH levels, which will minimize the water’s solubility, i.e. the ability to be dissolved. Other chemicals can be added that can consume oxygen before it can corrode the boiler, prevent foaming, precipitate dissolved solids before they form scale on steam-generating surfaces, and remove any precipitates from the vicinity of the steam-generating surfaces.
Specifically, these are some of the more common chemicals that are able to be used to treat boiler water:
- Boiler water can be treated with ferric chloride or hydrated potassium aluminum sulfate (better known as “alum”) as a way to get any suspended particles in the water to clump together, or “flocculate.” These heavier clumps of impurities – which are often called “sludge” – then drift down through the water and accumulate at the boiler’s bottom, where they can be removed during a boiler “blowdown” procedure.
- While the coagulation process removes suspended impurities from the water, the sludge clumps are still corrosive and can damage the boiler as they rest on the bottom of the unit. To combat this, sodium phosphate can be added to the water, which controls the pH level of the clumps and helps prevent harmful caustic corrosion from occurring.
- Oxygen Scavengers. Oxygen is a significant cause of corrosion in metals, so it is beneficial to the life and operation of the boiler if any excess oxygen is removed from the water. In this case, oxygen scavengers such as sodium sulphite or hydrazine can be used to help remove oxygen and protect against damaging corrosion.
- These are specialized molecules that can bind to positively charged metal ions and prevent them from forming insoluble precipitates. Common water-treatment chelants are ethylenediaminetetraacetic acid (EDTA) and nitrilotriacetic acid (NTA), which are used to form complex ions with calcium and magnesium in the water. The chelant is said to “sequester” the metal ions as a way to control scale formation in the boiler.
In addition to knowing which chemicals work best with the impurities that are found in general boiler water, operators of power-generating boilers must be aware of the potential pitfalls that can arise when “superheated water” is required for the operation. By definition, superheated water is that which is used under pressure and at temperatures that range from the typical boiling point of 212ºF (100ºC) all the way up to the critical temperature of 700ºF (370ºC).
Special attention must be paid to the operational characteristics of superheated water because at temperatures of more than 570ºF (300ºC) the water can be more corrosive than at ordinary temperatures. This requires that special care be taken in selecting materials of construction – carbon-steel and stainless-steel piping has been shown to be effective in these applications – as well as the chemicals that may be needed to treat the water.
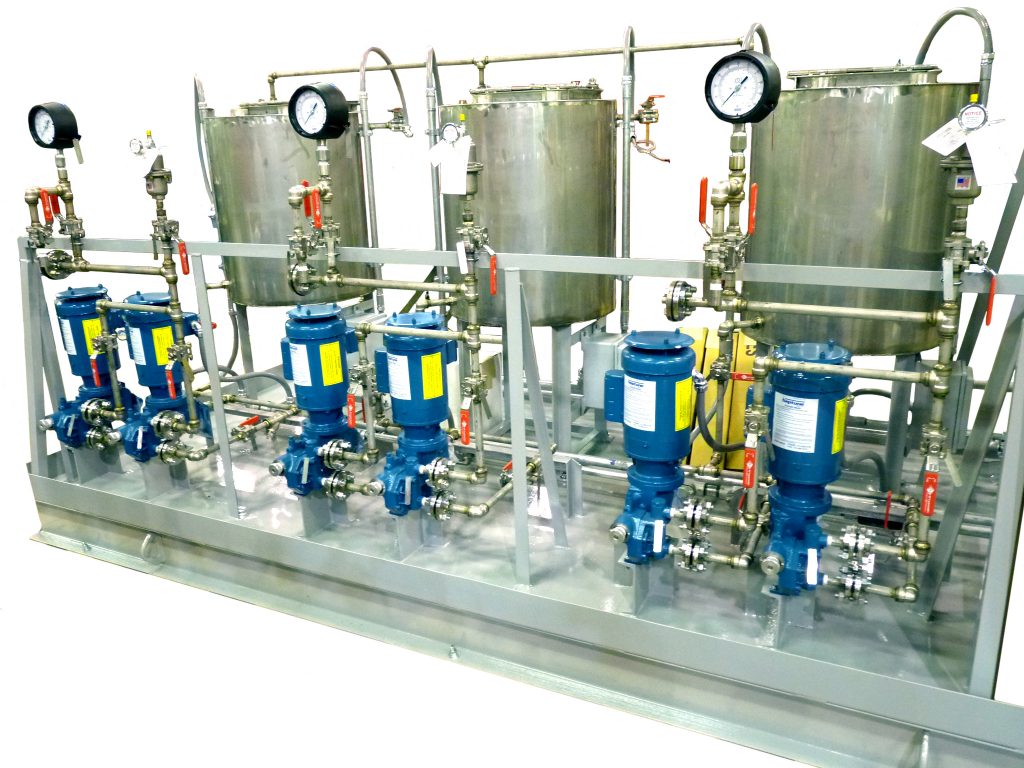
Outfitting a chemical-feed system with the proper hydraulic or solenoid actuated diaphragm metering pump plays a major role in ensuring the proper operation of boilers.
The Solution
As mentioned, there are specific types of pump and filter feeder technology that can be reliably deployed in chemical-injection activities for the different types of water treatment required and the different types of boilers. Here’s a closer look at three different options:
Hydraulically Actuated Diaphragm Metering Pumps
Hydraulic metering pumps can be ideal for chemical handling because they have been designed to inject a precise and controlled amount of chemical, with a repeatable accuracy of +/- 1%. This lets the operator know that dosage will consistently meet the predetermined requirements for use, as well as limiting the waste and higher costs that can accrue as a result of over-dosing. Also, because the pump’s diaphragm is hydraulically balanced, it is capable of operating against much higher discharge pressures than a mechanically actuated diaphragm pump.
Other features and benefits of hydraulic metering pumps include its robustness and longevity (designed for 20 years of service), internal relief valve; leak-free operation; ability to inject chemical at extremely high-pressures if necessary for the application (100 to 4,000 psi and higher); automatic control with either an electronic stroke control or variable-speed motor and manual control via adjustable micrometer dial. These pumps can be outfitted with a multitude of motor configurations in order to meet any service requirement.
Some models feature variable oil-bypass adjustment that delivers better valve performance then those that have a variable-linkage design. The variable oil-bypass adjustment optimizes performance because it gives the pump’s valves extra time to seat since they are idle during the bypass portion of the suction and discharge strokes. It also creates a much smaller footprint than many other hydraulic diaphragm metering pump designs.
Hydraulic metering pumps are also available in many different materials of construction – 316 stainless steel, C-20, PVC and Kynar® being the most common – which helps quell any material-compatibility concerns that can arise when handling different types of chemicals.
Solenoid Actuated Diaphragm Metering Pumps
Solenoid actuated, or electronic, metering pumps are an economical option in chemical injection for low capacity/low pressure injection (usually less than 2 gallons per hour and less than 250 psi) applications for boiler-water treatment because they offer repeatable dosing accuracy of +/-3%. Many are able to operate at any single-phase voltage from 94 to 264 VAC, or 50/60 Hz, and are generally unaffected by voltage fluctuations. Some feature high stroke rates of 300 strokes per minute or more, which allows them to provide more even distribution of chemical at low flow rates.
Many models feature a manual frequency adjustment or speed control that allows for convenient stroking-speed adjustment. Some models provide both frequency adjustment and stroke-length adjustment, which allows extremely large turndown capabilities.
Typical materials of construction are 316SS, PVC or Kynar pump heads, Viton® or PTFE (Teflon®) seals, PTFE diaphragms and 316SS, ceramic or PTFE check valves, which gives them the versatility to be used in a wide range of chemical-injection applications during boiler-water treatment activities.
Filter Feeders
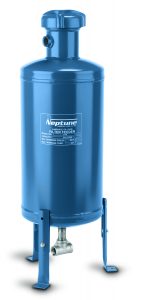
Neptune™ FTF Series Filter Feeders are a convenient way to introduce solid or liquid chemicals into boilers, while they simultaneously possess the ability to filter out any contamination that may harm the system.
A technology that is growing in acceptance for use in chemical introduction to boiler water – while also possessing the added bonus of filtration capabilities – is the filter feeder for use in low-pressure gravity or pump return-type steam-heating systems. Namely, the filter feeder combines the ability to inject various water-treatment chemicals with the capability to perform high-capacity filtering of the rust, corrosion, scale and coagulated solids that are produced in one piece of equipment, essentially giving it the ability to kills two birds with one stone.
The leading benefit of using the filter feeder is its ability to protect against harmful particles and debris due to the use of a filter bag that can trap almost all contaminants rather than relying on inefficient and unreliable strainers or dirt/air separators. While 60- to 90-mesh screens can intercept larger particles, today’s filter bags have been designed to capture impurities that can be as small as one micron, which is five times smaller than the width of a human hair.
Another benefit of the filter bag is that when it becomes full it can be removed from the filter feeder and thrown away, meaning that all of the solid particles that have been captured are finding their way into the garbage and not being reintroduced into the boiler system.
In the end, filter feeders are a convenient and reliable way to introduce solid or liquid chemicals into the boiler while possessing the ability to filter out at the same time any rust, scale or other contaminants that may compromise the overall performance of the boiler, or any of its sensitive internal components.
Conclusion
Boilers are an undeniable necessity when the goal is to produce heat for many different types of buildings, or generate the power that is needed to light them. The boiler can only perform its job effectively if the water that is used to generate steam is of a quality that does not affect the boiler’s operation. With most boiler water containing some type or level of impurities, it is imperative that the water be treated with chemicals that can make it safe for use. Accordingly, those chemicals can only perform their assigned tasks if they are used at the proper doses and feed rates. Operators of boiler systems are finding that they have many options when considering the best way to inject water-treatment chemicals, with hydraulic and solenoid pumps, along with filter feeders, moving to the fore as a technology of choice in crucial chemical-injection applications.
About the author:
Tom O’Donnell is Director of Business Development for NeptuneÔ Chemical Pump Company and PSG®. He can be reached at (215) 699-8700, ext. 3327 or Tom.ODonnell@psgdover.com. Based in North Wales, PA, USA, Neptune is a leading manufacturer of chemical metering pumps, peristaltic pumps, chemical feed systems, filter feeders and bypass feeders, chemical injection accessories, polymer make-down systems and portable mixers. Neptune is a product brand of PSG®, a Dover company, Oakbrook Terrace, IL, USA. PSG is comprised of several of the world’s leading pump companies, including Abaque®, Almatec®, Blackmer®, Ebsray®, EnviroGear®, Finder, GriswoldÔ, Mouvex®, NeptuneÔ, QuattroflowÔ, RedScrewÔ and Wilden®. You can find more information on Neptune at neptune1.com and on PSG at psgdover.com.