Author: Tom O’Donnell, Director of Business Development for Neptune™ Chemical Pump Company and PSG®
At first glance, the treatment of municipal wastewater seems pretty straightforward – water that has been fouled flows into the wastewater-treatment facility, makes its way through the treatment system where any harmful impurities or particulates are removed, and once it has reached a predetermined level of cleanliness, is either released to the environment, i.e. a local stream or pond, or sent out for reuse.
In reality, however, treating wastewater is a highly complicated process featuring any number of critical steps that must be performed to exacting criteria by highly technical pieces of equipment. The system is also only effective when the proper chemicals are used to treat the water, and these chemicals can cover a wide range in terms of pH level, viscosity, material compatibility and handling characteristics.
A few of the more commonly used chemicals in wastewater-treatment applications, and their characteristics, include:
- Sodium hypochlorite: Known throughout the world as bleach, this liquid is most commonly used for disinfection at the treatment plant. It is one of the most difficult chemicals to handle as most metals will corrode when coming into contact with it, and it cannot be mixed or stored with ammonia and other acids, organics and reducing agents that might be used at the plant. It’s also difficult for metering pumps because of its tendency to off gas, which can cause metering pumps to become gas bound. Special vent valves are available for diaphragm pumps to prevent this from occurring. Also, peristaltic pumps can be used, which does not allow this phenomenon to occur.
- Sulfuric Acid: Used for pH adjustment, it is provided either as a concentrate or dilute with concentrated solutions being less corrosive than dilute solutions. Concentrated solutions can be handled in many situations with cast iron, steel materials or Alloy 20 while dilute solutions require plastics such as PVC or Kynar®.
- Sodium Hydroxide: Used for pH adjustment, it is often provided in solution strengths from 25% to 50%. Special care is required for metering-pump elastomers, such as Viton® (often a material used for O-ring seals within a metering pump), which is not compatible. Also, especially when provided in higher solution strengths, this chemical has a tendency to gel in the pump if the pump is idle for a period of time. Flush valves or special pump heads can assist with this issue.
- Sodium bisulfite: One of the most commonly used dechlorinating agents at treatment plants. A mixer is commonly required to keep this chemical in solution in the metering-pump supply tank. Both plastics such as PVC and Kynar, as well as metals such as 316 stainless steel are suitable materials for this chemical.
- Emulsion Polymer: Fed as a coagulant to assist the dewatering equipment within a wastewater treatment facility, this chemical is often extremely viscous and is shear-sensitive, once hydrated. Diaphragm pumps with high-viscosity head designs or peristaltic pumps are often required.
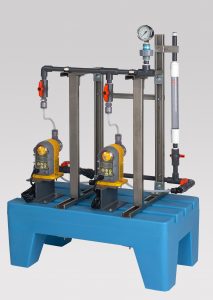
Solenoid-actuated diaphragm metering pumps are a viable choice in chemical-dosing applications at wastewater-treatment facilities because they offer highly reliable dosing accuracy, even when working with extremely low flow rates and operating pressures.
Faced with the myriad chemicals that can be used in wastewater-treatment systems, and knowing that each one contains unique handling and implementation characteristics that must be followed to the letter, plant operators must be certain that they have selected the proper metering pump technology for their dosing applications.
With that in mind, they must be made aware that there is no “one size fits all” solution to the metering pump selection. In fact, creating the most efficient, effective and – most importantly – safe chemical-handling operations in wastewater treatment will most likely require the use of different types of pump technologies, all of which bring their own set of benefits to the operation.
Here’s a look at four pump technologies that can play a key role in an optimized wastewater-treatment operation if implemented properly:
Mechanical Diaphragm Metering Pumps
Mechanically actuated diaphragm metering pumps offer an ease of operation and start-up that makes them an attractive alternative for many applications. They normally offer a lower initial cost than other motor-driven metering pump designs, especially at higher flow rates, but can have higher operating costs.
These pumps offer excellent suction-lift capabilities and also provide the ability to handle liquids that off gas, such as sodium hypochlorite, and more viscous chemicals since the diaphragm is attached to the piston for a positive return usually aided by a spring. They are somewhat limited in discharge pressure capabilities with many being around 100 to 150 psi (7 to 10 bar) max. Repeatable accuracy is normally about +/-2%. They are generally not offered with an on-board relief valve, so an external relief valve is usually required to prevent damage to the pump in an over-pressurized situation.
Hydraulic Diaphragm Metering Pumps
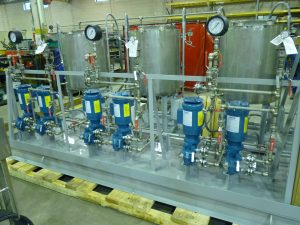
Because many pump manufacturers also design the other components that make up a complete chemical-feed system, they can be a significant source of assistance, or even a provider of comprehensive turnkey systems, for wastewater-handling operations.
Hydraulically actuated diaphragm metering pumps are ideal for operation in the harshest chemical-handling conditions as they are a low-maintenance pump that is designed for 20 years of service. This longevity and low maintenance is largely due to most of their moving part being submerged in a bath of hydraulic fluid coupled with fact that the diaphragm is hydraulically balanced. Hydraulically balanced means that the hydraulic fluid is on the oil side of the diaphragm while the chemical being pumped is on the other side (wetted or process side) of the diaphragm. The piston, internal to the pump, pushes oil against the diaphragm but never comes in direct contact with it. These pumps are capable of pumping against extremely high pressures, if need be, so long discharge lines are not a problem.
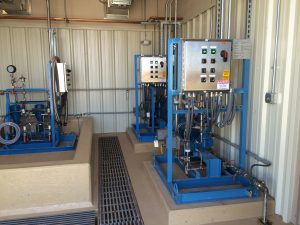
Hydraulically actuated diaphragm metering pumps are a leading technology of choice for wastewater-treatment plants because they can handle the hardest chemicals, can pump against extremely high pressures, offer highly repeatable dosing accuracy and have been designed for 20 year of service.
Hydraulic diaphragm pumps are equipped with an adjustable internal relief valve that prevents an over-pressurized situation from happening and damaging the pump. They also offer a repeatable dosing accuracy of +/-1%.
Solenoid Diaphragm Metering Pumps
Solenoid actuated, or electronic, metering pumps are a viable economical option in wastewater treatment operations for low-flow/low-pressure chemical-dosing applications. They are generally available to a maximum of 20 gph (76 L/hr) and at those capacities maximum pressures are normally about 30 psi (2 bar). The lower and medium capacities are compatible with pressures of 100 to 150 psi with low flows (less than 1gph) to over 200 psi (14 bar). They offer a repeatable dosing accuracy of +/-3%. They are normally provided with an on-board relief valve to prevent pump damage from over-pressurization.
Peristaltic Pumps
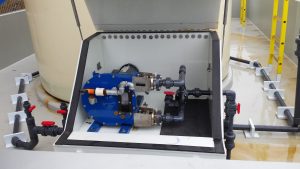
Peristaltic pumps are ideal for various chemical-handling applications in wastewater treatment because their simplistic design and operation allows them to reliably handle both viscous and abrasive chemicals.
This pump technology, simplistic in its design, is perfect for handling viscous and abrasive chemicals. Because the design features a rotor with shoes or rollers that squeeze the hose or tube and force the liquid to the discharge port, peristaltic pumps are able to run dry, a feature that competitive technologies like progressive cavity pumps can’t provide because their rotors and stators will be damaged in run-dry conditions.
Peristaltic pumps also do not have valves that can become clogged. This is an important consideration when the pump needs to be shut down during a product run; the lack of valves in the peristaltic pump eliminates any clogging issues, especially when handling viscous liquids or those that will solidify or become gelatinous when resting. This also makes the peristaltic pump ideal for the handling of abrasive or corrosive chemicals.
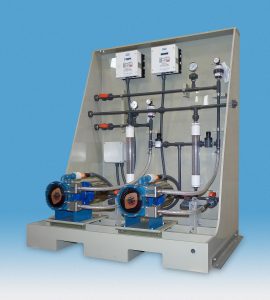
A wastewater-treatment plant’s chemical-transfer system can be optimized through the use of peristaltic pumps because the technology does not contain any valves that can become clogged. This means that when the pump is shut down any viscous liquids that will generally solidify or become gelatinous when resting will not adversely affect the pump’s operational capabilities.
While all of these pump technologies can provide an unquestioned list of benefits for the wastewater-treatment plant operator, it is still a challenge to know exactly which pump is best for which chemical-metering application. This is where the pump manufacturer can lend a hand. Many pump manufacturers also design and manufacture many of the components that are included in a complete chemical-feed system, i.e. relief and back-pressure valves, calibration columns, tanks, mixers, injection quills and control panels. Some even offer the complete chemical-feed systems as an option and possess the capability to build a system that meets the specific needs of the treatment plant.
Who better to provide the system than the manufacturer of its components? So, while the task of properly outfitting a treatment facility may be overwhelming, the manufacturers of the various components that will be used to optimize the system, or the manufacturer of a complete system, can be a significant source of assistance in determining how to best outfit the plant.
Conclusion
Ensuring that communities have the cleanest water possible for cooking, cleaning, drinking, bathing and recreational activities like fishing and boating places a great amount of pressure on water and wastewater-treatment facilities to perform their jobs as effectively, efficiently and safely as possible. The number and type of chemicals that may be required in the various treatment processes only help to increase the risk for the plant operator. Therefore, the operator can only be certain that the operation reaches the pinnacle of proper performance if the best pump technology is chosen for each of the many critical chemical-metering processes that must take place every day.
With so many varying flow rates, viscosities, compatibility issues, pH levels and handling characteristics to consider, a varying array of pump types must be employed to guarantee optimized operation. When it comes to chemical handling, mechanical, hydraulic and solenoid metering pumps, along with peristaltic pumps, have been proven to offer the best operational capabilities. When used in the proper application, these technologies can help overcome any concerns the plant operator can have – and the pump manufacturers themselves stand ready to lend a hand in order to ensure that the treatment system will reliably operate at the highest level.
About the author:
Tom O’Donnell is Director of Business Development for Neptune™ Chemical Pump Company and PSG®. He can be reached at (215) 699-8700, ext. 3327 or Tom.ODonnell@psgdover.com. Based in North Wales, PA, USA, Neptune is a leading manufacturer of chemical metering and peristaltic (hose) pumps, chemical feed systems, chemical injection accessories, make-down systems and industrial mixers. Neptune is a product brand of PSG®, a Dover company, Oakbrook Terrace, IL, USA. PSG is comprised of several of the world’s leading pump companies, including Abaque®, Almatec®, Blackmer®, Ebsray®, EnviroGear®, GriswoldÔ, Mouvex®, NeptuneÔ, QuattroflowÔ, RedScrew™ and Wilden®. You can find more information on Neptune at neptune1.com and psgdover.com.