Author: Peter Schüten, Almatec Product Manager, PSG
In many industrial processes that feature the handling of liquids, the substances that are being transferred may occur in an aqueous or “muddy” state, with the liquid portion needing to be removed. This liquid-removal stage may take place during the production process – for example, in the filtration of edible oils or yeast solutions – but it more frequently occurs at the end of a process like wastewater treatment when the waste sludge that has formed must be withdrawn.
Since the disposal of such sludges is calculated based on weight and volume, their thickening and drying is particularly lucrative for the processor. During the thickening and drying process, the sludges are treated using chemicals and/or physical processes so that the waste sludge forms into flake-like solids. After adjusting the pH level to neutral or alkaline via the use of milk of lime, the subsequent dewatering process separates the water for disposal, with the remaining volume of sludge significantly reduced.
The simplest technology for this process involves collection and thickening of the sludge through the use of gravity. However, it is significantly more effective to use technical drying methods via processes such as centrifuges and evaporators, or more commonly, chamber filter presses (Fig. 1).
The operational principle of the chamber filter press relies on the use of a number of plastic frames that are pressed together under high pressure. Inside the frames are hollow chambers — from which the press gets its name — that are surrounded by filter cloth. When the sludge is fed into the chambers using pressure, a “filter cake” forms inside the chambers and the filtrate flows through the filter cloths into drainage channels.
When all the chambers are completely filled, the sludge feed stops. The press is then opened and the solid filter cakes can be removed. After closing, the press is ready for a new pressing process.
To fill these presses, filter material and pressure is required. The pressure — usually between 8 and 15 bar (116 to 218 psig) at its peak — should be even in order not to destroy the sludge flocs during feeding. The flocs should also have enough free space in the feed area. In addition to the constantly increasing counter-pressure that occurs until the end of the pressing, a further constraint is the eventuality that an empty-running sludge tank can lead to dry running of the pump being used to generate pressure.
To build pressure, different systems of displacement pumps are frequently used, including piston diaphragm pumps, which are applied most frequently for large presses. In these large and costly units, one or two diaphragms are hydraulically actuated and feed the sludge into the press through a series of valves. These pumps require large overhead costs even for small plants, such as an air-pressure vessel to equalize the feed rate and a maximum pressure monitor or bypass. Eccentric screw pumps are also used, either as self-regulating pumps (with motors that are electronically controlled via a frequency converter) or as cyclical systems (where an air-pressure vessel is “charged” by the pump). This valve-free procedure is advantageous when processing large sludge quantities and when long fibers prevent the use of valves. However, there are operational constraints that need to be considered in small- and medium-sized plants due to their sensitivity to abrasion and dry running. The space required to use this system is also considerable.
The list of filter-press pumps also includes hose-diaphragm piston pumps, which function in a similar way to piston diaphragm pumps but with crimped hoses rather than diaphragms. Piston pumps typically generate strong pulsation and require constant lubrication. Both of these pumps are characterized by their simple electrical operation, with fairly high installation and maintenance costs.
By comparison, it is much easier to use an air-operated double-diaphragm (AODD) pump; they are resistant to dry running, virtually maintenance-free, self-priming, self-regulating and highly compact. Without the need of an operator or electronic system, the counter-pressure of the chamber filter press regulates the feed rate automatically. The feed rate decreases continuously as counter-pressure increases simultaneously to the degree of filling. This effect can be used to detect when the chamber filter press is full. When this point is reached, the pump virtually stops — zero feed rate — or only occasionally makes a delivery stroke. In addition, the use of compressed air as drive power to move the diaphragms results in a highly efficient, regular and gentle cyclic drive that allows the medium to be fed smoothly.
A standard AODD pump is typically limited to the pressure of the supplied air, which is often insufficient to fill the press. For this reason, it is often necessary to increase the pressure, for which there are three very different technical solutions:
- The first variant uses one of the diaphragms on a standard pump to generate additional pressure. The force of this diaphragm, which is surrounded only by air and compressed air, is transferred to the feed diaphragm via the internal diaphragm connection, enabling the feed diaphragm to work with double the pressure. This method is rarely used anymore, as it leads to high pulsation, low feed rates and high air requirements. It also commands high service costs as the diaphragm on the air side is very sensitive and breaks quickly.
- Another variant is to operate a standard pump with an air-pressure amplifier, which drives the pump with increased air pressure. This process is limited by the fact that a standard pump is used most of the time. Although these pumps are equipped with external reinforcements, from a technical perspective the standard pumps in question are designed and built for significantly lower pressures and as a result only have limited resistance to the increased strain. Additionally, the increased pressure resulting from these air-pressure amplifiers, or “boosters,” pulsates strongly, which can influence the flow of the product. Boosters also seem to reach their limits in maintaining pressure, i.e. during repressing. This is because the devices used are almost always too small. These devices yield the required end pressure, but may require a longer filling time.
- The third variant is a pump with internal pressure conversion. Fig. 2 below shows how this technical solution applies compressed air to a differential piston along with the diaphragms. The increased surface area — typically twice as large or more — causes the compressed air to generate a corresponding amount of increased force. This converted force acts on the feed diaphragms with increased (double) pressure. The entire construction is designed for the high strain caused by the maximum amount of pressure, as well as the strain caused by the typically abrasive sludge. For this reason, the pump housing is built from materials such as stainless steel or polyethylene (PE-UHMW). This tough material is a decisive factor in the durability of the pump (Fig 3 below).
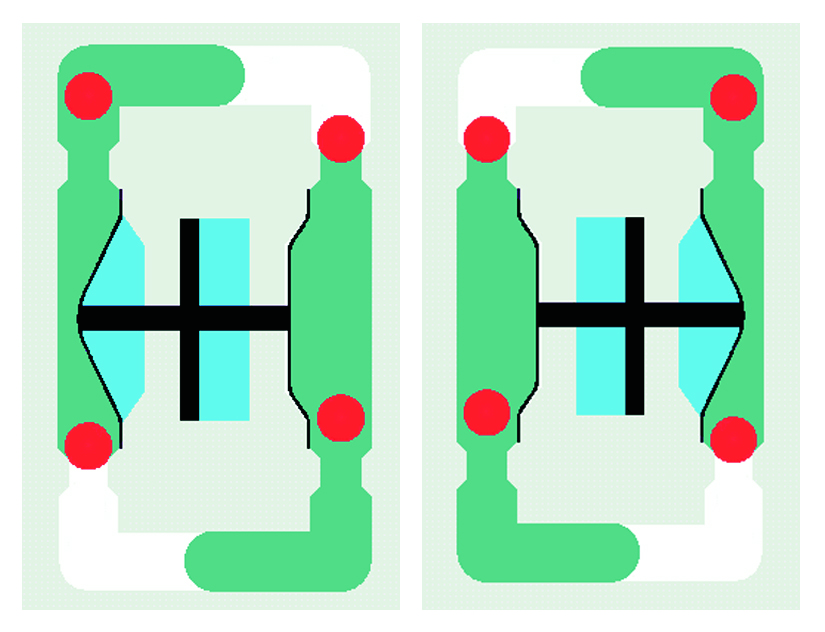
Figure 2. Functional principle of an air-operated double diaphragm pump with a feed pressure of 15 bar (Almatec AHD series).
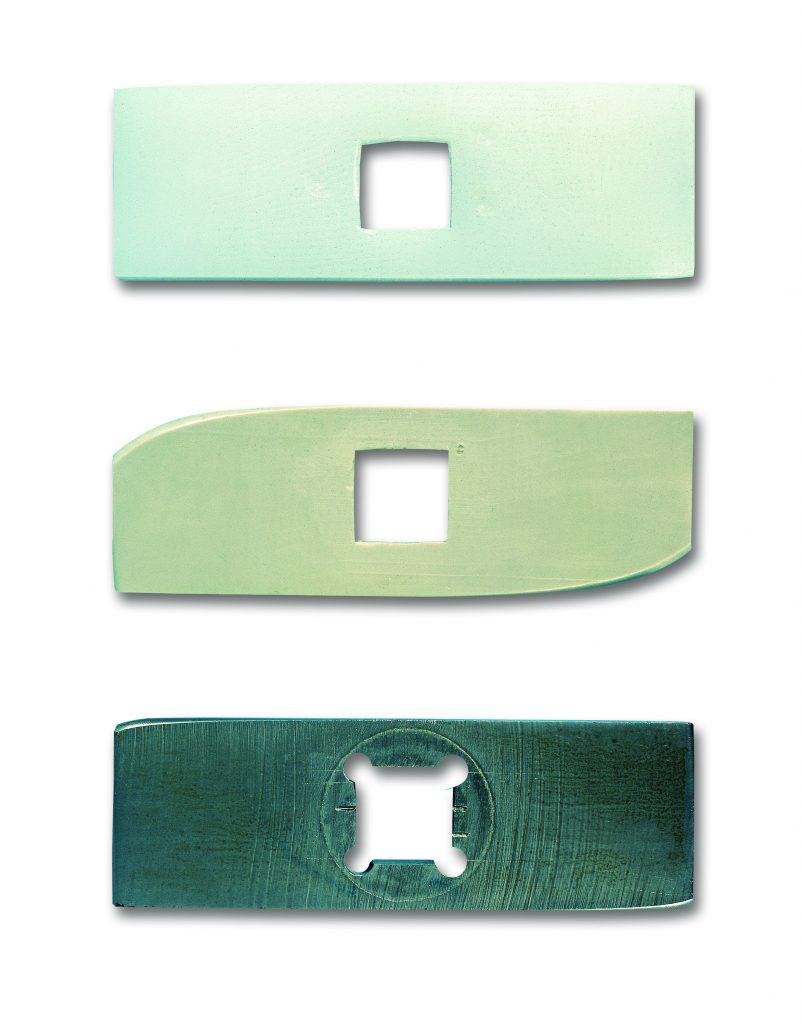
Fig. 3: Wear factors based on the sand-slurry process PE UHMW = 1 (top); PP = 7 (middle); steel = 1.6 (bottom)
Using compressed air to power a pump is very effective. The pump operates with minimal dead space, i.e. the space inside the pump that must be filled with air without contributing to the actual pumping process. As a result, the pump always has sufficient power reserves to handle large volumes of wastewater.
With the introduction of a new generation of high-pressure AODD pumps, there is now an additional variant that combines the highly robust housing of the pressure-converting pump with an air section where no conversion takes place (Fig. 4). This version is therefore suitable for all applications under heavy load conditions, ranging from low-feed pressures to high-pressure applications of up to 15 bar (218 psig). If the user operates a pump at such high air pressure — whether it is from an external booster or directly from the compressor — he or she can do so secure in the knowledge that the pump is structurally designed for such pressure ranges and does not need to be held together by external reinforcements.
These new pumps are equipped with specially developed heavy-duty diaphragms with an integrated metal core for long service life and the ability to handle heavy loads. The vulcanized core of the diaphragm supports extremely thick layers of elastomer. To transfer the suction forces, the core is also reinforced with a special textile that is barely flexible in any direction.
In addition, these pumps can be combined with the optional use of a sensor that responds to the movements of the diaphragm and allows the cycle to be easily monitored. Accordingly, the slow stroke frequency that accompanies a full press rarely triggers a signal. If a Programmable Logic Controller (PLC) is used to program a time window within which a stroke should take place, the operator will know that the chamber press is full when no PLC-generated signals occur during the time window.
The compressed air can be switched off and a signal can be set for the operator to empty the press. This method functions purely by physical means and is independent of sensitive pressure gauges and contaminating sensors in the wastewater current.
In conclusion, when selecting pumps for filter press operations, AODD pumps are the clear solution, incorporating a number of operational advantages. Conventional positive displacement pumps with electric drive and control elements do not have these properties that are specific to the design of AODD pumps, including dry-run capability, good controllability and a gasket-less mechanical design, to mention but a few.
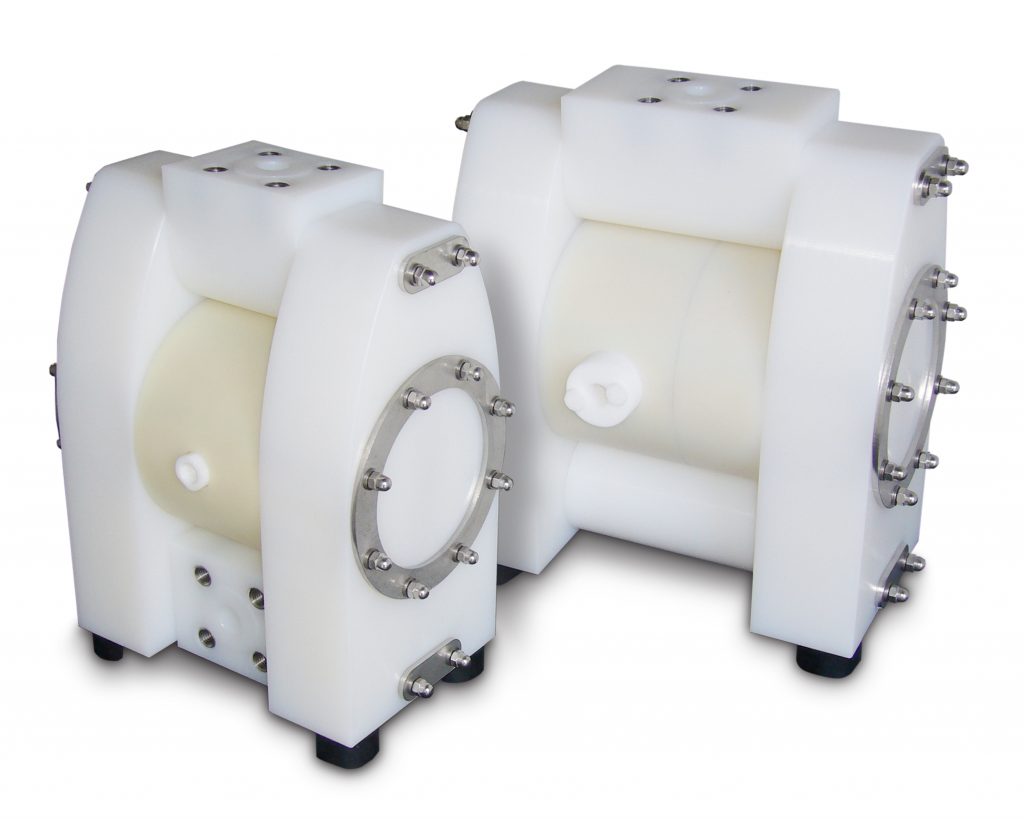
Fig. 4: Almatec® offers two models of high-pressure AODD pumps for use in chamber filter presses, the AHD Series with internal pressure conversion, and the AHS Series for use with an external booster.
About the Author:
Peter Schüten is a Product Manager for Almatec Maschinenbau GmbH, Kamp-Lintfort, Germany. He can be reached at Peter.Schueten@psgdover.com or +49 2842 961-0. Almatec® is one of the world’s leading manufacturers of air operated double-diaphragm (AODD) pumps, owns numerous patents and has one of the largest product ranges in the field of pneumatic diaphragm pumps. Almatec is part of PSG®, a Dover company. Headquartered in Oakbrook Terrace, IL, USA, PSG is comprised of several of the world’s leading pump brands, including Abaque®, Almatec®, Blackmer®, Ebsray®, Finder, Griswold™, EnviroGear®, Mouvex®, Neptune™, Quattroflow™, RedScrew™ and Wilden®. For more information on Almatec or PSG, please go to www.almatec.de or www.psgdover.com.
Comments