Author John Dean
Ceramic materials are inorganic and non-metallic such as clay or kaolinite, and are generally in the form of oxides, nitrides and carbides. Silicon and tungsten can also be added to enhance hardness. While ceramics can handle very high temperatures in excess of 1,832 degrees F (1,000 degrees C), they are brittle and used selectively in many products. Machining ceramic materials is difficult, so ceramic components are generally formed or molded. The good electric properties of ceramics find wide use in the power generation / transmission industry, and are also popular in the consumer product markets. The greatest potential for ceramics is in the tile industry where more than 50% of the ceramic production is used. This is estimated to be a $270 billion market, and growing subsequent to high demand.
A Manufacturer Needed a Pump for Processing Ceramic Slurry
Manufacturing companies that specialize in ceramic products, production and disposal, use a variety of processes all of which require the transportation and storage of slurries. The crystalline microstructure of ceramic particles consists of sharp pointed edges which, combined with the high percentage of solids present in the slurries, can cause severe erosion and damage not only to rotating machinery like pumps, but also to piping systems and valves.
The ceramic industry recognizes the challenges and has tried several pump types. For example, all-metal pumps experience severe wear and erosion. The disadvantage of using air-operated diaphragm pumps results in severe damage, along with blockages and wear to the valves caused by the abrasive material. Maintenance costs are greater since pump components and the valves require frequent replacement.
A European customer, with a fireclear glazed tiles application which required processing a highly abrasive ceramic slurry, had also tried several types of pumps, but the results had been disappointing. Diaphragm pumps, in spite of expensive initial investment costs and high operating and maintenance costs, were failing in an unacceptably short time. NETZSCH became aware of the customer’s situation, and with their experience and expertise with difficult applications, offered a solution.
NETZSCH’s Rotary Lobe TORNADO® T2 Pump Offered a Solution
The NETZSCH team of engineers applied their experience with challenging pump applications and suggested the NETZSCH Rotary Lobe TORNADO® T2 pump. This uniquely designed pump has been successfully used in various abrasive slurry applications with excellent performance, excellent service life and has consistently satisfied customers.
After installing a TORNADO T2 Rotary Lobe Pump, the Operations Manager stated, “In terms of comparing the service life, the air-operated diaphragm pump barely lasted 2 to 3 months. On the other hand, the TORNADO® T2 pump is continuing to operate successfully for almost 2 years without requiring maintenance.” Various additional installations in this same ceramic company have also recorded operating times in excess of two years without requiring any maintenance.
The Operations Manager stated that, “One application with a high percentage of solids records very little wear on the lobes and is still operating at 110 gallons per minute (25 cubic meters per hour) at a differential pressure of 85 psi (5.8 bar). The speed is 262 rpm and a temperature of 86 degrees F (30 degrees C).”
As this ceramics customer saw positive results, they purchased additional lobe pumps for their facilities and to date employs a total of 9 TORNADO® T2 pumps operating in one location. The cost saving this customer achieved by switching to the TORNADO® T2 Rotary Lobe pumps for the entire installation has been approximately $1650 (€1500) in initial capital expenditure. The operation of the 9 pumps for variations ranging from 1 to 2 years has realized savings in maintenance, which includes parts and labor, for service totals of approximately $88,000 (€80,000).
A Pump that is Simple and Cost-Effective
The TORNADO® T2 is simple in design and easy to maintain. It provides a smooth continuous flow compared for example to a diaphragm pump that requires dampeners to minimize pulsation. At the same time it maintains lower power consumption and lower operating costs. These savings from a reduction in power usage are in addition to the above mentioned savings based on 8 hours of operation per day.
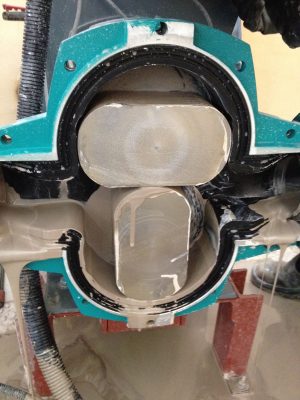
The NETZSCH TORNADO® T2 Rotary Lobe Pump demonstrates Full-Service-in-Place for simple and fast access without disconnecting piping.
As shown in the installation picture, it is a Full-Service-In-Place pump, and it does not require the disconnection of the piping or much space to disassemble. The synchronization of the lobes can be achieved by a simple tool that is an integral part of the pump.
The contra-rotation of the lobes within the pump chamber is a key factor in minimizing the wear as the flow characteristics prevent the particles in the slurry from lodging between the rotors.
The flow pattern from the suction to the discharge side does not permit excessive rubbing of the solids against the rubber liner further reducing wear and erosion. Traditional rotary lobe pumps generate excessive heat and cause greater wear from elastomer to elastomer contact.
The smooth curvature of the pump housing also helps significantly reduce the effect of particle impingement at higher linear velocities of the fluid resulting in minimal wear and tear to the elastomeric liner. An added advantage of the faster rotational speed and consequently the higher linear fluid velocity is that it prevents settling of the particles further reducing wear.
The TORNADO® T2 is highly engineered for tough applications, and with advanced materials, its modular design and longevity, low maintenance and low power consumption, it makes the total cost of ownership significantly cost effective compared to the available alternatives.
Tough applications such as pumping ceramics require tough solutions, and a tough yet cost effective pump. The NETZSCH Rotary Lobe TORNADO® T2 offers the best solution and benefits to the customer.