Solids content of sludge cake in sewage sludge handling operations is a persistent problem. High-solids sludge leads to bridging, which in turn can lead to significant process downtime and pump maintenance demands. Traditional bridge-breaking technology fails to adequately address bridging in the resulting difficult-to-convey sludge applications. More recently, improved technology, such as NETZSCH Pumps & Systems’ aBP-Module®, has proven to be highly effective in ensuring effective bridge prevention, leading to continuous plant uptime and minimal pump system repairs.
Bridging causes downtime, harms equipment in sludge handling
Bridging, a stubborn issue in sewage sludge handling applications, occurs when thick and dry dewatered sludge cakes together. Once the sludge sticks together, bridges between the side walls form as sludge falls into the hopper of a pump and starts to stick to the side walls above the pump auger. These bridges can prevent additional sludge from falling into the pump by blocking off the opening, thereby ceasing pump operation. As the sludge piles up on top of the bridge, it backs up the process until eventually it overflows out of the hopper or triggers an alarm, at which point the portion of the plant in question must shut down until the maintenance crew can break down the bridge over the pump auger, clean up any overflowed sludge, reset alarms, and pump the overflow sludge manually until the sludge feed is back within normal operating parameters. Depending on the plant setup and failure modes, the above delay to plant operation can last anywhere between an hour and a whole day.
An even more troubling issue caused by sludge bridging occurs if the pump continues to run without any sludge feeding into it. If the pump runs dry in this manner, the stator will heat up and, if the pump is not switched off in time, can be destroyed. Stator damage causes the entire pump to fail, requiring repairs and extensive plant downtime. Typically, plants have safeguards in place in order to avoid dry running and the resultant pump damage, although occasionally these safeguards are not suffient and damage occurs anyway. Even when dry running is prevented, bridging problems likely impact plant schedule and require reassignment of staff and equipment, delivery/pick adjustments, or adjustments to other portions of the plant process.
Traditional bridge-breaking technology
With the growing need to remove more water from sludge cake within the field of sludge handling, the percentage of solids in sludge cake is increasingly high. The higher percentage of solids, however, causes the sludge to be stickier and harder to convey, and therefore exacerbates bridging.
As a result of the serious issues caused by sludge bridging and the increase in bridging frequency and severity, a number of pump companies incorporate bridge-breaking technology into their pump systems designed for sludge handling. The traditional type of bridge-breaking technology is a single or dual paddle wheels resting above the auger of the pump. While somewhat effective in reducing bridging, this technology has two areas where bridging can still form: above the paddles and between the paddles and the auger. In addition, given that the paddles are in the direct flow path of the sludge, they can collect a buildup of hair, rags, or other materials that can get wrapped around the shafts.
Another common anti-bridging technology present in pump systems is vibrators. These devices vibrate the walls and the sludge media in order to prevent sludge buildup. However, vibrators decrease in efficacy as solids percentage and sludge stickiness increases. With highly sticky sludge, pump systems require improved sludge handling equipment in order to prevent bridging, and specialized cake pumps in order to properly and efficiently handle thicker sludges.
Benefits of improved anti-bridging technology
One such example of improved bridge-breaking and prevention equipment is the aBP-Module®, created by NETZSCH Pumps & Systems for sludge handling. The aBP-Module® works by creating the effect of a moving wall with the use of spoked wheels. By having the wheels rotate into the auger feed zone, bridges do not have enough time to form, or, if they do form, they are carried along to the auger by the wheels, thus breaking the bridge as it engages the auger. The spoked wheels continually change the wall dynamics and keep it free from bridgingMoreover, the wheels are very close to the sides so as not to interfere with the sludge flow into the pump. The aBP-Module® is typically used for sludges with solids content ranging from roughly 25 – 40%.
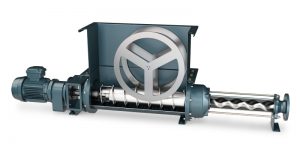
The aBP-Module®’s spoked wheels prevent sludge buildup while conveying any bridges that form directly to the suger to be broken up.
The patented aBP-Module® bridge prevention and breaking technology is superior to traditional methods for multiple reasons. Given that the wheels are to the sides and not in the product flow path, there is no buildup of sludge, hair, rags, or other materials. The paddle wheels of the traditional technology require 4x more power to operate per paddle than the aBP-Module®. Finally, the aBP-Module® requires zero maintenance due to buildup or bridging, with the resulting lesser chance of the pump running dry during a blockage than traditionally-designed systems. The aBP-Module®, therefore, does not lead to process downtime due to either pump shutdowns or maintenance
The aBP-Module® technology is compatible with all of NETZSCH’s open hopper pump models and can be adapted to hoppers of all sizes. For very large hoppers, the wheels can be doubled or tripled as needed.
Conclusion
Given the rise in solids content of sludge cake in sewage sludge handling operations, and the failure of traditional bridge-breaking technology to adequately address bridging in difficult-to-convey sludge applications, improved bridge-breaking technology is necessary to ensure continuous plant uptime and minimal pump system repairs. With the aBP-Module®, pump systems require considerably less maintenance, and exhibit higher productivity and less power consumption.
Comments