Sheridan retrofits an existing control valve and enters the automated world of water efficiency.
Everywhere around us there are networks of water systems storing, controlling and moving water from one place to another. However, with every twist and turn of water through these distribution networks, the risk of water loss increases. Those losses accelerate with aging infrastructure, over pressurized systems and lack of maintenance.
For years, water management systems have exclusively used mechanical components. However, in recent years there has been a push to develop better methods for controlling water and having external interaction with the system. The focus of these solutions is aimed at reducing maintenance, saving water and reducing pipe breakage through remote control. By adding instrumentation and automation to existing systems, users can quite easily gain control over their entire system. Instrumentation, such as flow meters and pressure transmitters, give real time data of a system’s current working conditions. By adding automation tools such as control panels and SCADA integration, users can also manipulate and control the system. Here’s a simple example: To reduce pressures in a system during off peak hours, users can establish a sequence of control outcomes through SCADA to automatically throttle back the system. It’s a simple step that can produce major cost savings; by reducing pressure when demand is low, it can result in a significant decline in water loss – as well as less pressure stress on the system – which reduces pipe breakages and leaks.
The City of Sheridan, Wyoming wanted to add automation and instrumentation to bring part of their system online. This would allow for more control over their water system while implementing system redundancy. Their water system is fed from two water sources, which can be treated at two different water treatment plants and then distributed to the public. Different storage tanks are also utilized through the distribution system.
The City identified an opportunity to repurpose an existing pressure reducing valve so they could leverage gravity flow from an upstream treatment plant to fill a water storage tank. By reconfiguring the valve operation with instrumentation and automation (in combination with a realignment of buried valves in the yard), they could bring this otherwise hidden valve live into their system. The project would save them power as they would not need to use the booster station to fill the tank; however, it could remain as a redundancy when needed. Having two options to fill the tank means the city can use real time data to choose to run either option as best suited. The new automation will enable this to be done remotely from the control room at head office.
The existing Singer Model 106-PR was repurposed to a model 106-2SC-PCO. The current valve now has the capacity to interact and be controlled by a control panel via new valve mounted solenoids that replaced the hydraulic controlled mechanical pilots. An electronic valve position indicator and differential pressure transmitter were also added to the valve. To control the new reconfigured valve for both flow and level control, a Singer industrial control panel was added. The control panel uses the feedback from the valve position transmitter and differential pressure transmitter to calculate the current flow through the valve. The level sensor at the water tank measures the current water level and sends that feedback to the control panel. With all the instrumentation data feeding back to the MCP-TP, the control panel can now control the valve to ensure the user set level in the tank is always maintained.
To ensure over drafting of water from the upstream system is not an issue, the control panel also takes into account the flow rate and ensures it maintains the user-set flowrate while filling the tank. The user-set flow rate can be adjusted to ensure the tank is filling fast enough but not too fast to overdraft the system. The flow and level setpoints can be changed and manipulated at any time to optimize the operation of the system.
The user-set setpoints for tank level and flow rate is set locally at the MCP-TP control panel via a touch screen display, or via the SCADA control network. The control panel was integrated into the city’s existing network using Ethernet communication. This allows remote access to the site from the main control room to view/control the current flow, level, valve position, current alarms, control modes and gives easy access to set all the control setpoints. Essentially the integration gave the control room the same access as if they were standing right in front of the MCP-TP control panel pushing the touch screen buttons on the HMI.
Singer staff, along with Jacob McGough of Pipestone Equipment, finalized the commissioning of the project on site. This included full setup of all the instrumentation and testing of the control sequences of the MCP-TP panel and its control of the valve. The final steps were concluded when the system went live and the City of Sheridan operators could test all the SCADA controls and fully control the new system. Marcus Weaver the integrator and electrical technician said, “I was really happy with the support we got with field programming coordination and follow ups, it was above and beyond our expectations and solidified our confidence in the system.”
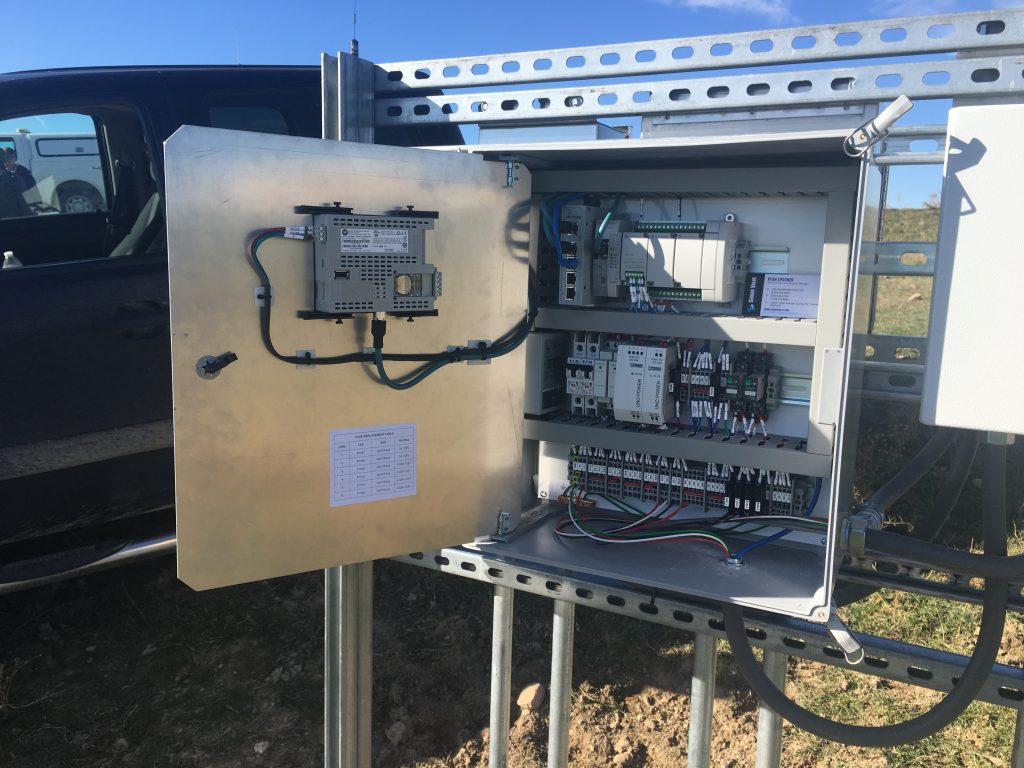
MCP-TP Field Wiring Connection & SCADA Ethernet Connection
For the people of Sheridan, this means they now have another layer of security and dependability on this part of their water supply system, while saving on pumping costs. For the operators of Sheridan’s water system, it means less time spent in the field monitoring and managing flow requirements. “This valve helps us operate, monitor and diagnose our water system remotely and in real time,” said Ken Hirschman, Sheridan’s Utility Maintenance Superintendent. “I am excited to see this technology expanded into our other existing infrastructure so that we can monitor how our pressure zones are operating remotely by using our existing SCADA system. These types of electronic operations and monitoring are all important steps in moving toward a smart and efficient utility”.
Jacob McGough, Application Engineering and Sales with Pipestone Equipment said, “Currently, 25% of our sales in the hydraulic control valve market is being offered with electronic capabilities. This percentage has been on the rise over the last couple of years as more people are introduced to the vast improvements of these types of solutions for mitigating non‐revenue water loss and resolving aging infrastructure problems.”
In today’s world, there is often a tendency to view things as disposable and simply replace the old with the new. This is not always necessary; sometimes a simple upgrade can bring on a whole new world of possibilities. This is the case for many water control systems, by adding instrumentation and automation you can often streamline operations and significantly reduce costs without the big expense of a complete replacement for the same functionality.
For more information visit www.singervalve.com