When pumps run dry, it can lead to failures and unwanted expenses due to downtime.
When a pump does not have enough fluid present dry running can occur. In submersible pumps, the fluid acts as a coolant to dissipate heat generated by the pump through the media and lubricant. However, there can be catastrophic failures within the pump when no fluid is present.
When using metal components, the heat generated while running dry can result in parts damaging and ultimately, the pump seizing. As the impeller of the pump spins, heat is being generated and heating the other components of the pump (bearings, seals, and shaft). This results in increased wear of the pump components and ultimately, failure of the pump. In addition, the excess heat generated can cause these metal components to weld together.
Causes Of Dry Running
Dry running can be the result of cavitation, where excess vapor formation results in a dry running atmosphere within the pump, or more commonly, the result of human error. It is normally recommended that submersible pumps not run dry for longer than one minute; this includes both when adding and removing the fluid in the pump. When in use, the operator of the pump is responsible for ensuring that the pump is shut off in time to prevent the pump from encountering a dry running environment.
Why Use Carbon/Graphite?
Because there is no fool proof method to correcting human error, another option is to look at the pump design. Carbon/graphite and graphite mechanical components – seals and bearings – are able to be used in dry and wet applications without the risk of parts seizing or galling when running dry.
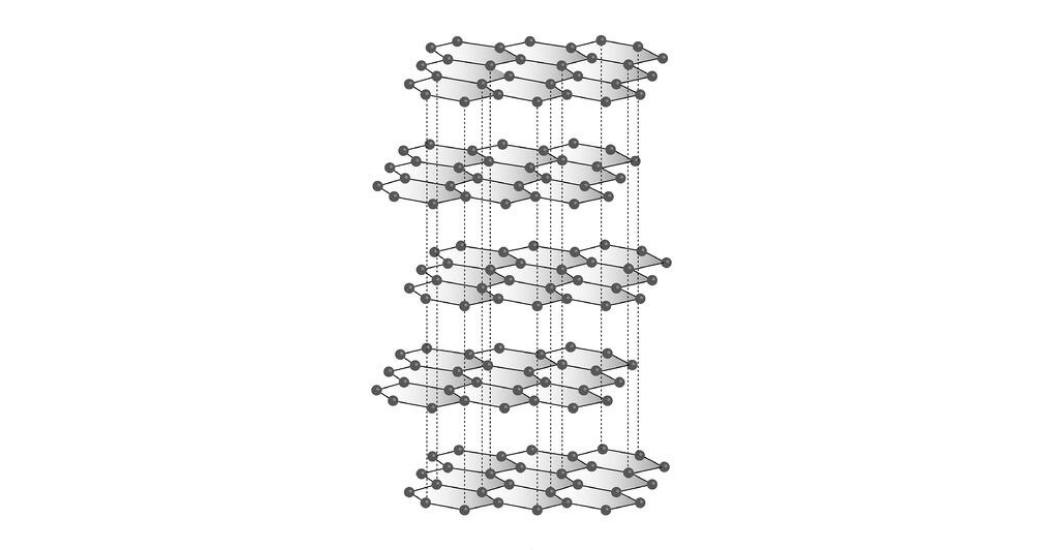
Figure 1: Graphite atomic structure showing layers of graphene connected by weak Van der Waals forces
Carbon/graphite is self-lubricating and does not require any additional lubrication to run successfully in dry applications; this is due to its chemical structure. While running, layers of graphene are deposited onto the countersurface. This deposited film acts as the lubrication needed to have the part run successfully in dry applications.
Both carbon/graphite and graphite material grades exhibit self-lubricating properties. Graphite serves as the main component for providing lubrication for these mechanical parts while the amorphous carbon provides strength.
Graphite’s chemical structure is aligned into graphene layers (Figure 1) that aid in the film depositing process during use. Each graphene layer is held together by weak Van der Waals forces that are easily broken as the part runs against a countersurface.
The graphene layers that are deposited fills the surface roughness on the counter surface to allow the carbon/graphite component to run against the graphite film instead of the countersurface itself. Hence, providing self-lubrication. This is critical in dry running conditions where there is no fluid lubrication present to mitigate the harmful effects of friction.
In addition, because graphite’s chemical structure is well aligned, it exhibits better thermal properties to disperse heat away from the contact point and reduce heat buildup.
By using carbon/graphite mechanical components in a pump that may run dry, there is no need to install protection or control devices to account for human error and prevent the pump from running dry by shutting it off.
Consider using carbon/graphite in your next pump application and contact an engineer at Metcar for assistance today.