Learn how to choose long-lasting wear rings to help increase pump efficiency and reduce metal-to-metal contact.
Both case wear rings and impeller are commonly found in centrifugal pumps. These pumps transfer energy by centrifugal force and are used in many applications. The centrifugal pump’s impeller rotates, pushing the fluid outward along the circumference and directs the flow towards the pump outlet as depicted in Figure 1.
Because centrifugal pumps are required to move liquids by adding kinetic energy to the fluid, the impeller operates at high speeds. Unfortunately, these high speeds can result in excessive wear of the impeller and casing due to shaft deflection.
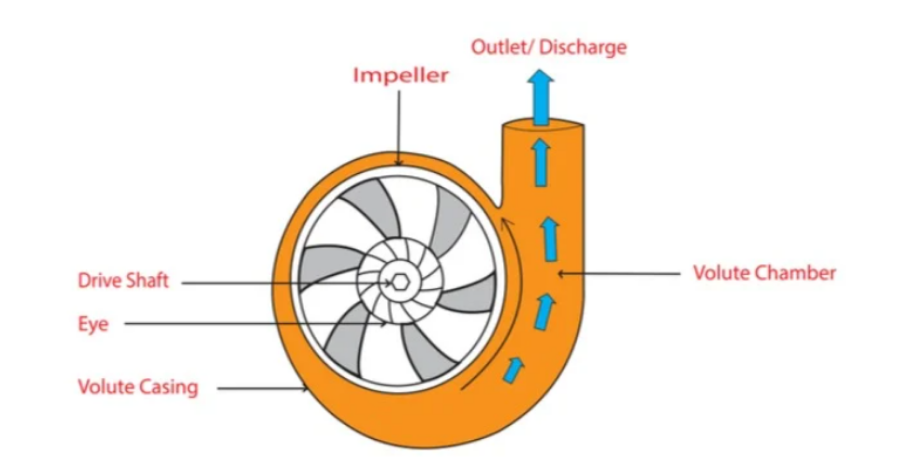
Figure 1. Centrifugal pump diagram showing flow direction out of the discharge, high pressure side.
How Wear Rings Increase Pump Efficiency
Shaft deflection and the resulting wear that is experienced by the pump parts can be reduced by using wear rings. Wear rings help reduce the running clearance between the impeller and the casing which help increase shaft stiffness and minimize vibration within the system.
Reducing running clearance results in increased efficiency of the pump. Per the Lomakin Effect, the use of wear rings to maintain a small running clearance helps stabilize the system.
A stabilized system is less likely to be affected by shaft deflections which can negatively affect running clearance. For instance, shaft deflection can result in a varying running clearance around the shaft which consequently lets more media leak from the high-pressure discharge side of the pump to the low-pressure suction side.
The Benefits Of Non-Metallic Wear Rings
Non-metallic wear rings, such as carbon/graphite, are a great replacement for metallic wear rings. Carbon/graphite wear rings eliminate the possibility of metal-to-metal contact during shaft deflections that can result in seizing or galling and offers a self-lubricating non-metallic surface for the impeller to run against if a failure occurs.
Carbon/graphite deposits a film of graphite onto the counter surface it is running against to essentially run against itself and protect the metal parts of the pump.
In addition, carbon graphite parts have a low coefficient of friction, 0.10 – 0.25 for dry running applications and less for submerged applications, that results in less heat being generated when running against the counter surface.
Custom Wear Ring Grades
While carbon/graphite is a beneficial fail-safe, it is also beneficial when the pump is operating successfully. Carbon/graphite can be impregnated with various metals, resins, or oxidation inhibitors to withstand many application environments. Metcar produces carbon graphite with impregnations that results in parts being able to withstand extreme temperatures (>1000 ⁰F), pressures, and chemicals.
Changing to carbon/graphite wear rings has numerous process and system benefits as mentioned above. It is also a great preventive action to help avoid wear on other pump components which are much more expensive to replace.
Consider changing your wear rings to carbon/graphite during your next routine maintenance.