The benefits of using carbon graphite ball valve seats for severe service applications
Industrial ball valves are an essential component of fluid handling systems in a variety of industries, ranging from wastewater management to power generation. Their basic function is to regulate the flow of liquids or gases through a pipe by means of a rotatable ball with a flow path in the ball’s center. In many applications, this ball rotates against a Teflon valve seat or a metallic valve seat that is lubricated with ball valve grease. However, when ball valves are expected to perform reliably in harsh chemical environments or at high temperatures where grease lubrication is not feasible and engineered plastic materials like Teflon will deform, alternative materials must be used. Carbon graphite’s self-lubricating properties, chemical resistance and high-temperature capabilities make it the preferred material for ball valve seats in severe service applications. In addition to carbon graphite’s resilience in severe service, it is an impervious material, allowing ball valve manufacturers to ensure a leak-free design.
API 607 ball valves
Fire-safe ball valves are an excellent example of an application in which high temperature performance is essential. Fire suppression systems utilize a network of fire-safe valves to transfer and distribute water as necessary during a fire. These types of valves are prevalent in the petrochemical industry due to the combustible nature of oil and gas. Oil refineries, tankers and rigs are all outfitted with numerous fire-safe valves that undergo a strict qualification regimen. Each of these valves must perform to special standards set forth by the American Petroleum Institute (API), a trade organization representing over 650 corporations involved in the production, refinement and distribution of petroleum. API 607 is one of these standards – it outlines the fire safety testing that is required of soft-seated (i.e. non-metal) quarter-turn valves. This standard involves ensuring that these valves can handle a certain amount of pressure when the valve is heated to approximately 1,400-1,800°F, closely simulating fire conditions. Conditions
like these are what make the use of highly-engineered materials like carbon graphite necessary in fire-safe valves.
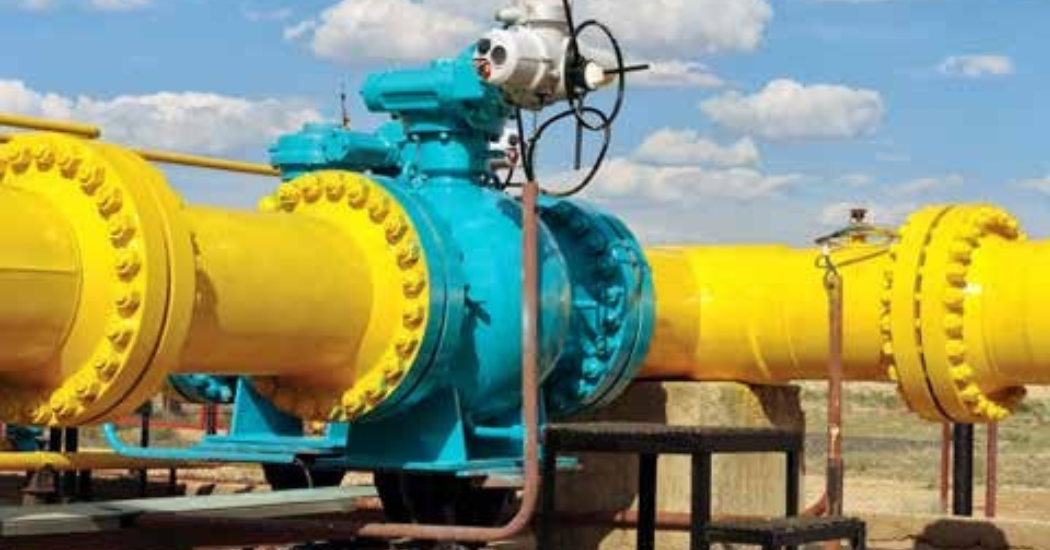
Industrial ball valves must be able to handle very large flow rates and pressures
Material property benefits of carbon graphite
Unlike plastic ball valve seats, which will soften at around 350°F, carbon graphite will not melt or deform at high temperatures. Graphite grades have been developed to withstand exposure to the extreme temperatures required of API 607, where nearly all other materials will fail. Even at these high temperatures, carbon graphite retains its self-lubricating ability and structural integrity.
It’s not just temperature resistance that makes carbon graphite such a versatile material. Carbon graphite is chemically inert, which allows it to operate in incredibly caustic conditions without chemical attack. As a result, carbon graphite ball valve seats are common in corrosive applications like chemical processing and distribution. Impervious carbon graphite grades have also been deemed GRAS-Generally Recognised as Safe – by the US Food and Drug Administration (FDA) for use in food processing applications, allowing carbon graphite ball valve seats to be used in food and beverage manufacturing. Carbon graphite also has excellent compressive strength. When held in compression in a metal retainer, carbon graphite ball valve seats can dependably withstand heavy loads without excessive wear. In other words, carbon graphite is an extreme material, designed for extreme conditions.
Manufacturing carbon graphite ball valve seats
Most carbon graphite valve seats must be shrink-fit into a metal retaining ring and held in compression in order to function properly in application. The interference between the carbon graphite and the metal housing and the resulting compressional forces allow the spherical sealing face to better retain its shape during operation and withstand a much greater radial load. This interference also ensures that the carbon graphite is retained within the metal housing when the housing experiences thermal growth at high temperatures. Since the retaining ring and the ball are often made of the same material, the seat and the ball will also grow and shrink at the same rate as temperature changes, allowing the ball and the seat to maintain a consistent sealing surface without leakage at high temperatures. Final machining must be done during assembly to ensure that the spherical sealing face meshes perfectly with the ball and a leak-tight fit is maintained between the seat and the retaining ring. The end result is a pressure tight ball valve that can perform in environments where other ball valve seats fail.
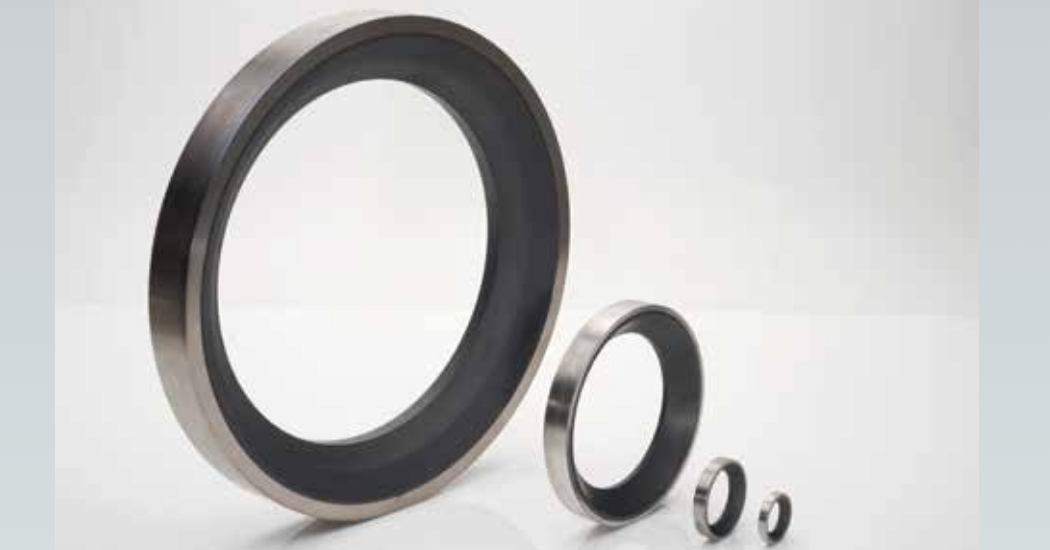
Steel-encased carbon graphite ball valve seats are an industry-standard in many severe service applications
The future of carbon graphite ball valve seats
Carbon graphite manufacturers are always striving to improve their materials to allow valve designers to design for even more extreme conditions. Through the use of advanced processing techniques, we are developing materials that can operate at higher temperatures, have better dry running capabilities, and a longer wear life. Contacting a carbon graphite manufacturer directly is the best way to stay abreast of these developments.
This article was written by Keith Hoge, product manager at Metallized Carbon Corporation. Visit: www.metcar.com
Originally published in Fluid Handling International.