Leistritz Advanced Technologies recently held a thread whirling and peeling lunch and learn event at AmTTech’s Dallas, TX, metroplex location. The event featured a seminar reviewing helical profiling processes and their advantages by Attila B. Catto, President-Machine Tools, Leistritz Advanced Technologies Corp. and a demonstration on the Leistritz LWN 90.
“The purpose of the event is to bring whirling technology to customers,” said Catto. “Whirling is a technology that many people have heard of but do not know or understand how it works and how it can help improve their manufacturing process.”
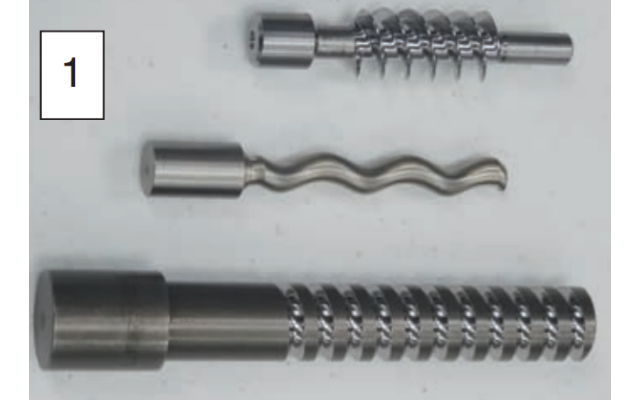
Whirling is a specialized manufacturing operation in which a geometrically oriented cut removes chips (1) Threaded workpieces on top and bottom machined using whirling process and elliptical workpiece in center machined using peeling;
Whirling is a specialized manufacturing operation in which a geometrically oriented cut removes chips. When cutting external threads, the cutters face inwards instead of outwards. Applications include screws for extruders, spindles for screw pumps, eccentric screws for use in the oil and gas industry, ball screws for automation tasks and linear drives and EPS-screws for high quality steering systems.
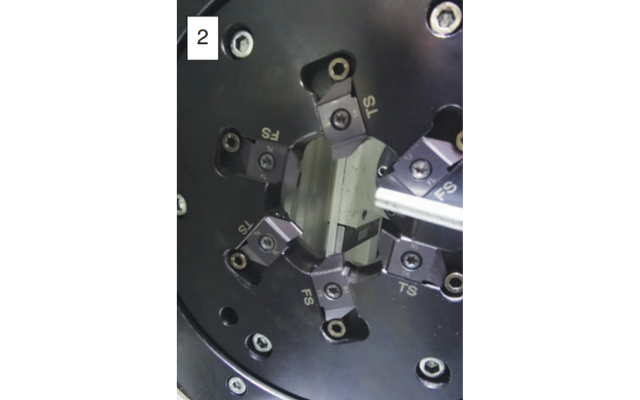
(2) Cutting is the result of the whirling ring rotating eccentrically at high speed while the workpiece
“Whirling can be applied to any part or component that has a helical profile to it. The benefits of whirling or peeling over conventional manufacturing is a 50% reduction in cycle time. In many cases there is a reduction in environmental costs compared to conventional manufacturing. The process of grinding can be eliminated or greatly minimized,” said Catto. “With whirling, there are no finishing operations needed since the parts are machine to print tolerances and finishes.”