Author: Sven Olson, Sr Consultant, Leistritz Advanced Technologies Corp.
As complexity grows in processes and in transfer of fluids in pipelines and plants, screw pump technology has attracted increased interest from engineers and operators in the industry. The emphasis to increase energy efficiency while improving flexibility and driving down operating costs is leading the way. It is now the time to critically revisit conventional thinking about pump selection and take a fresh look at the evolution of screw pumps, how they could improve economics and safeguard the vitality of critical processes in plants and transfer systems.
Let’s discuss pump types with multiple screws, which are different from the often used single screw or progressive cavity pump. In principle, screw pumps are part of the positive displacement family, and as such, are designed to displace flow in direct proportion to the rotary speed of the pump.
The tight cavities formed when the profiles of the screws are meshing, transport fluids from suction to discharge, building up pressure enough to overcome the downstream system back pressure. The screws in the pump are the pumping elements where the driven screw or power rotor transfer the torque to one or several idler screws both mechanically and hydraulically. The smooth opening and closing pump cavities result in a pump flow with very limited pulsations and noise.
The pump screws or rotors are designed to eliminate any axial hydraulic thrust either by using balance pistons or having the screws in an opposed flow arrangement. Eliminating thrust bearings helps greatly to simplify the pump design and exclude potential wear areas. The multiple screw pump design is self-priming, can work with very low suction pressure, is also gas tolerant and able to handle free and entrained gases without loosing prime. Low internal fluid velocity and the gentle meshing of the rotors also contribute to very low shear rates, which is especially important for shear sensitive fluids or for different kinds of oil emulsions.
The operational flexibility of the multiple screw pump is also manifested by its ability to work over a very large viscosity range – from light hydrocarbons to residues and bitumen. The screws are normally case hardened for improved wear resistance, and customized coating are often used to protect the rotor bores, the rotor liner, or pump casing.
The Leistritz family of screw pumps with multiple rotors includes the following pump designs which are increasingly used not only in hydrocarbon related industries and applications, but also in chemical and petrochemical applications. Each series of pump has its specific set of operational advantages and possibilities. To find the right type of pump for an application is not only technically important for the process, but also a cost optimization opportunity.
This unique pump design relies on two screws, one drive and one idler screw, which are radially supported by large bushings lubricated by the pumped fluid. The bearing journals are also part of the axial thrust balance configuration where discharge pressure one side of the journal and suction pressure on the other side creates pressure balance and also provides the bearing journal with liquid for lubrication and cooling.
The torque transfer from one rotor to the other is by means of rolling (as opposed to sliding) contact over the screw profiles, which is important for good wear resistance. The rotors are at the
same time positioned without any radial support from the rotor bore, which also makes to pump very resistant to abrasive wear and suitable for fluids with low lubricity.
One and a single external bearing contribute to an extreme rugged design for service in a number of different applications with flow rates up to 1700 GPM and 250 PSI discharge pressure.
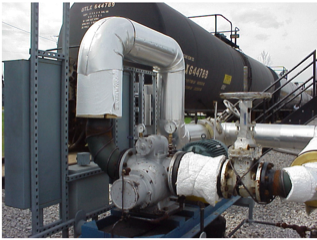
L2 Pump for rail car loading/unloading
Typical use of the L2 pump is with fluids like asphalt, bitumen, pitch and oily residues as well a variety of process fluids like MDA and MDI where the shaft seal is replaced by a seal-less mag drive. This series pumps can also be customized with a replaceable pumping cartridge and a fabricated casing to fit in a number of different process application where high temperature and very viscous fluids are handled. It is often a very good alternative to a timed twin screw pump where it’s simplicity and ruggedness by having no timing gears and with a single shaft seal which makes it easier to operate and maintain and with a lower installed cost.
The three-screw pump is used in number of different applications with fluids ranging from lube oil in lubrication systems to process fluids like pitch, asphalt and light end products such as condensate and VGO. The most common pump execution used in process applications has a pumping cartridge separate from the casing to allow for different installation options. This design uses one driven screw also called power rotor that is doing the major pump work and is surrounded by two idler rotors. They merely serve as rotating seals around the power rotor and are handling the radial forces supported by long journals formed by the rotor bores. As in the other screw pump designs the thrust load is hydraulically balanced without the use of thrust plates or bearings. The design also allows for higher speed, which results in very good volumetric efficiency also at higher pressure with low viscosity fluids. The L3 series flow rates are up to 1600 GPM with maximum discharge pressure of 2300 PSI.
The cartridges design is perfect for customized installations. In a useful application referred to as a “Re-Engineered Pump” the outer casing is designed so it matches the envelope of an older pump for a direct replacement without changing pipe connections or driver. By taking advantage of its flexibility an important process improvement can be done as shown below where the pump inlet is directly bolted to a suction box and the first section of the screws is open to act like an auger “pulling” the process fluid into the pump.
For light ends the three screw pump offers many advantages. Its compact design, compared to a horizontal ESP for the same differential pressure, makes it significantly smaller both dimensionally and lighter in installed weight. The internal hydraulic hydraulic thrust balancing eliminates the need for a thrust bearing arrangement and its lubrication system. In addition the pump is gas tolerant and can handle gas entrained liquids with out vapor locking or loosing prime. It operates outside any critical speed ranges and is not prone to surging or excessive pressure pulsations.
The unique five-rotor pump, Series L5, has emerged as a rugged and simple pump design for transfer products in tank terminals barges and ships. The pump design evolved as the market called for a simpler pump than the conventional timed twin-screw pump, eliminating the timing gears and keeping an often troublesome mechanical seal arrangement down to one single seal. The large pumping cavities formed by the meshing of five rotors results in superior suction lift capability also with viscous fluids. As a pure transfer pump the capacity combined with lower differential pressure was optimized still keeping the pump speed such so that standard synchronous motors without gearbox could be used. Flow rate range is from 500 to 5300 GPM with a maximum discharge pressure of 150 PSI.
The design has a lot of commonality with the L2 design including the same hydraulic thrust arrangement. The four idler rotors are surrounding the power rotor in a clover shape supported by journal bearings lubricated and cooled by the pumped fluid. The pump can be provided also as cartridge design and equipped with steam or hot oil heating jackets. An integrated relief valve can be included which saves on installation compared to a separate relief valve. The possible installation can be made vertically as deep well pump for barges and tankers equipped with a hollow shaft electric motor or with a right angle gear for diesel engine drive.
The most versatile of all types of screw pumps is the timed tworotor pump also referred to as the twin screw pump. Although some manufacturers offer pretty standardized twin-screw pumps, they are often customized for a particular fluid, installation and service. They are designed for larger flows than most other screw pumps and can develop high discharge pressure with anything from non-lubricating low viscosity fluids to high viscous heavy oils, bitumen and molasses. The L4 series flow rates covers up to 6500 GPM with pressure range up to 1500 PSI
As the screw profiles rotate without touching axially or radially the pump is totally independent on the lubricity of the pumped fluid. The clearances have the disadvantage at lower viscosity to increase the internal slip or leakage and thereby lowering the volumetric efficiency, however the opposite happens when the viscosity increases. The double suction flow neutralizes the axial hydraulic forces and the rotors can be positioned axially in simple angular ball bearings. The main hydraulic forces are radial and the bearings must be designed to handle high loads also when the physical space limits the selection of bearing and mechanical seal alternatives due to the short center distance between the rotors. To protect the timing gears and bearings from the process fluids single or double mechanical seals are used lubricated by either a simple oil bath or a circulating oil system. A particular application is as multiphase pumps being able to pump untreated crude oil with water and natural gas coming straight from an oil well without separation, which is becoming a growing market in onshore and offshore oilfields. To seal the screw profile and remove the heat of compression at higher gas fraction such twin-screw pump are equipped with liquid recirculation system
The twin-screw pump design is widely used in refineries, tank terminals and chemical plants. As the screws rotate without contact with each other or the surrounding liner the flexibility is almost endless when it comes to fluids it can handle. With variable speed control the pump can cover a wide flow range and keep flow and pressure constant also with low inlet pressure and entrained gas or vapor. Besides transfer and blending applications a very successful application in refineries is as Flare Knock Out Drum pump. In this case the pump speed controls the liquid level in the drum also with vapor carry under which would have vapor locked a conventional vertical can pump. The NPSH required of the twin-screw pump eliminate the sump or pit required by a centrifugal pump. The flow control is also an important aspect in pipeline installations where variations in supply and demand can be easily controlled by variation of pump speed. Pipelines designed for heavier crudes and diluted crudes are done favorable using twinscrew pumps with its ability to cover everything from light to the most viscous products. Also with light however waxy crudes the twin screw pump is helpful to start flowing a shut-in pipeline where wax precipitation is an issue.
The screw pump technology has taken big leaps forward in recent times and proven itself to be a good alternative to competing pump technologies used today in terminals, plants and refineries. With its different configurations as shown in this article there is almost always a screw pump alternative to be considered for a particular service. To optimize pump operability and at the same time minimize cost of ownership it is worthwhile for the system designer and facility operator to take a good hard look at today’s screw pump alternative.