Meet our Industry Person of the Week – Brandon Schaner, Director of Reliability Services at SRT Corporation!
Q. How did you get started working in the Industry?
Brandon: My father owned an industrial motor repair facility in the Pittsburgh, PA area. From a young age, I was in the shop, and had been introduced to many aspects of corrective services – such as balancing of rotors and mechanical repair. In my teenage years, I began to operate vibration analysis equipment, performed field balancing, and initially learned to perform shaft alignment with dial indicators (obviously pre-laser alignment days!). I assisted in field rebuilds and overhauls for clients. From that point, and over the next 20+ years, I began to expand into providing reliability-based services for large scale clients, both domestically and abroad.
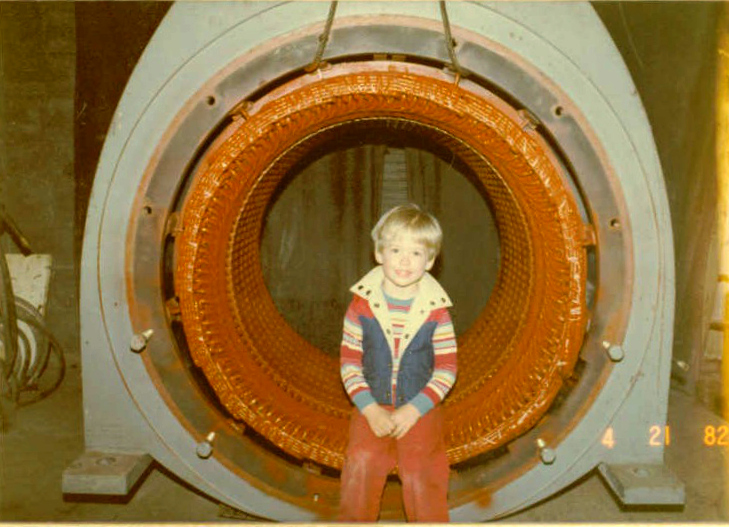
Brandon at 4 years old, sitting inside a 3000 HP motor frame at his father’s shop.
Q. What is your favorite part of your job? What are you most proud of?
Brandon: My favorite part of my job is that it isn’t a job. It is my passion! I’m satisfied by solving client problems and helping them improve their facility’s reliability. My goal is always to take a client from a place of frustration (in cases of ongoing failures and/or forced downtime) to a position of proactive, planned maintenance and uptime. I provide the absolute best in customer service along the way. I make my client’s problems my problems, and I won’t quit until I’ve solved those problems. I am most proud when I receive an email or phone call from a client simply saying “Thanks”. Maybe it sounds simplistic, but today when a client takes time to make that brief personal connection because you’ve been able to help them, it means a lot.
Q. What advice would you give to someone new to the industry?
Brandon: Put your time in! Get in front of experts. Ask for mentorship. Get into the field and see first-hand what is happening inside a machine. Twenty years ago, there was already concern about the future problem of having less qualified maintenance personnel available to help maintain a facility’s uptime. As that has become even more of a reality today, the problem is now being compounded by the fact that the trained Reliability Professionals who can provide earlier warning of equipment faults and failures are also shrinking in numbers. Maybe I sound ‘old-school’, but the answers are not going to magically appear on a computer screen at the push of a button – quality analysis means getting into the data and finding the answers! The next generation that are interested in getting into the Reliability Services industry need to learn the true ‘nuts and bolts’ of providing real analysis to gain an understanding of what is actually taking place in the mechanical systems that the analysis is being performed on. There are many people with many years of experience who would love to mentor and share knowledge with the next generation – take full advantage of it!
Q. Can you tell us about a cool project you worked on?
Brandon: I have had the privilege to provide services to so many interesting process facilities, both at home and around the world, so it is really hard to pinpoint any particular facility or project. However, I recently completed an installation and implementation of our wireless online monitoring system for a client with a large number of cooling towers in a refining facility. Forced-air cooling tower cells traditionally rely on hard-wired accelerometers, associated wiring and hardware for reliability monitoring, and ultimately the operating environment is not friendly toward the wiring, landing boxes and sensors themselves, leading to higher maintenance of those systems. In this case, it was great to deliver a next generation, high quality and lower-priced system that eliminates all of the labor intensive installation and shortcomings of a traditional wired system – it’s great to see clients embracing newer technologies!
I was excited to perform this install for this particular client, because it was a departure from the “we’ve always done it this way” mentality a lot of industrial facilities have, and it’s refreshing to move into an entirely new (and better) way of doing things. Off the record, I have performed projects in some really amazing places, but since this is an open publication, if I get too specific, it can cause me more problems than it’s worth!
Thank you, Brandon, for being our Industry Person of the Week and for your work in the Maintenance & Reliability field. We look forward to keeping up with you through the #PumpTalk Community!