In this series of articles, IDCON delves into essential business processes crucial for enhancing overall plant reliability. Both this article and its predecessor concentrate on strategies for averting failures and prolonging equipment life. Subsequent issues will further explore topics including spare parts management, condition monitoring, planning, and scheduling, as well as root cause problem elimination.
If you ask any maintenance department how failures can best be prevented, the No. 1 answer is usually that the operations department needs to stop wrecking equipment. If you ask operations how reliability can be improved, the top answer is almost always for maintenance people to work instead of sitting idle.
It is known that maintenance people are idle because effective work processes such as planning, scheduling and spare parts management aren’t defined and/or well-instituted. But in this article, Torbjörn Idhammar discusses operating practices with regard to reliability.
Operating practices are a vital part of any preventive maintenance process. Good practices prevent failures. Poor practices encourage failures.
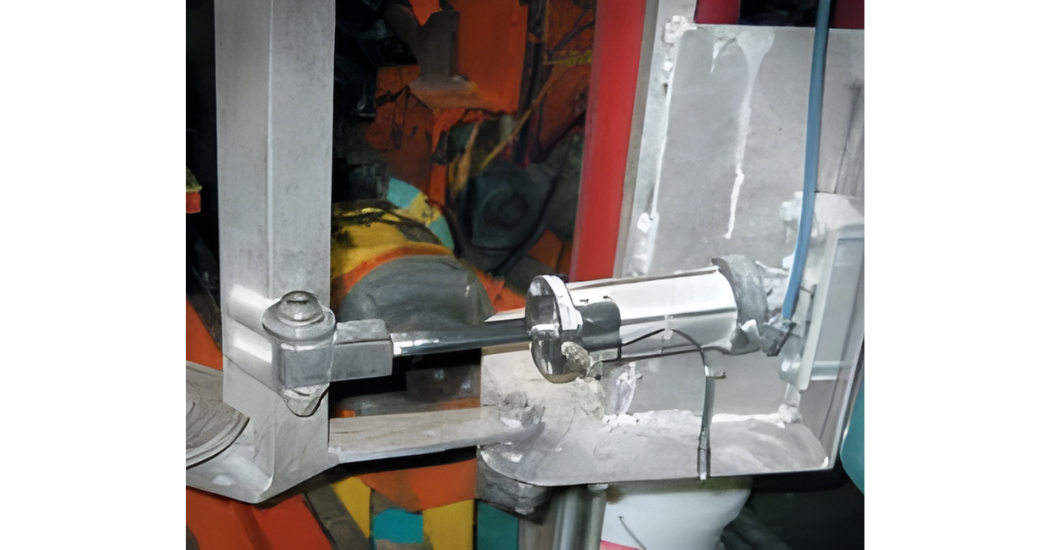
A plant worker changes the pressure setting on a cylinder.
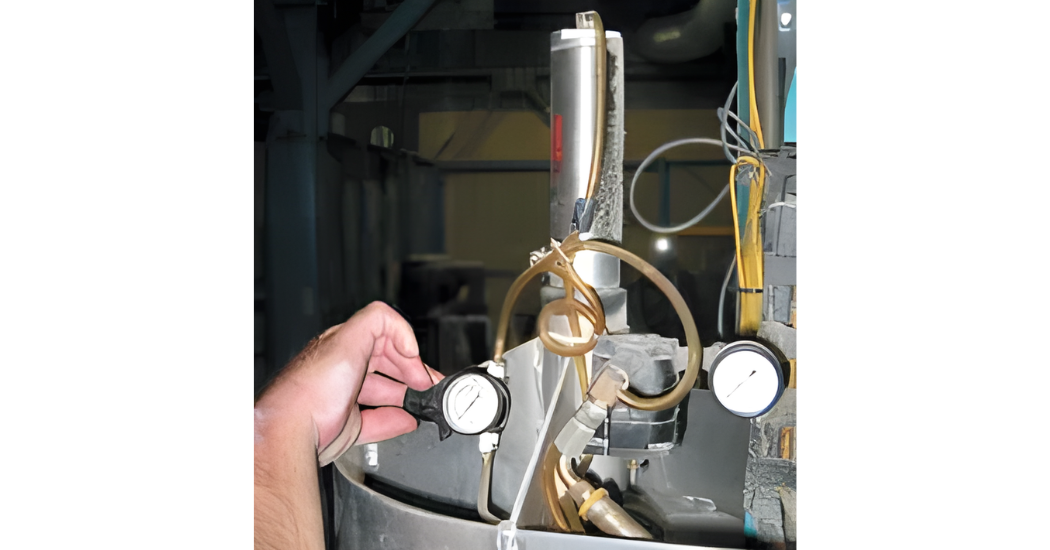
The cylinder dead-heads and shakes loose or gets damaged due to the wrong pressure setting.
Some good questions for the management team are: “Do we have well-documented and communicated expectations in our standard operating practices (SOPs)?” “Do the SOPs cover equipment reliability issues?” “Does maintenance provide adequate input into how equipment should be operated to avoid problems?” “Are operators trained in SOPs?” “Does operations management have the skills to understand reliability issues in an operating context?”
It’s common to see SOPs in plants, but do they include equipment reliability issues? A few examples follow.
Pneumatic cylinder: At one plant that I worked in, it was common to see operators increase the pressure setting on the pneumatic cylinder as much as 100 percent in order to get the equipment to run faster. When the cylinder exceeded twice its designed speed, it “dead-headed” and usually shook loose or bent the rod. As a result, maintenance changed the pressure setting during the area’s weekly PM. In talking to the operators, they can’t remember ever being told not to change the pressure setting. Air pressure settings weren’t part of the operator training. SOPs for the equipment didn’t exist.
Motor start-up: When you push the start button of an AC motor, the current surge through the motor is usually four to seven times the 100 percent load. If the start button is pushed several times in a short time interval, it’s common to damage or burn the motor windings. Do your operators know this fact and operate equipment accordingly?
Steam systems: An operating procedure as simple as opening a valve too fast can have devastating consequences for a piping system. The phenomenon is called water hammer. Here, steam enters a cold piping system and condenses into water. The water travels with great speed and causes damage to pipes and flanges as it travels through the system. Piping elbows are especially vulnerable. This is a common problem in many industries.
Open communication between operations, maintenance and engineering is needed during the design and selection phase of equipment. That communication must continue after installation.