What is a Bill of Materials?
A Bill of Materials (BOM) is a complete and accurate list of parts for each asset. Having correct BOM is a key element of the technical database. The list should include all parts that are likely to be used.
Why Are Bills of Materials Important?
With a reliable BOM, planners can focus on providing detailed instructions needed to perform efficient maintenance work. Even with an appreciation for the value, there are numerous roadblocks when undertaking an improvement project. However, BOMs can be systematically improved by following a 7-step process to achieve incredible results.
7 Steps to improve BOMs
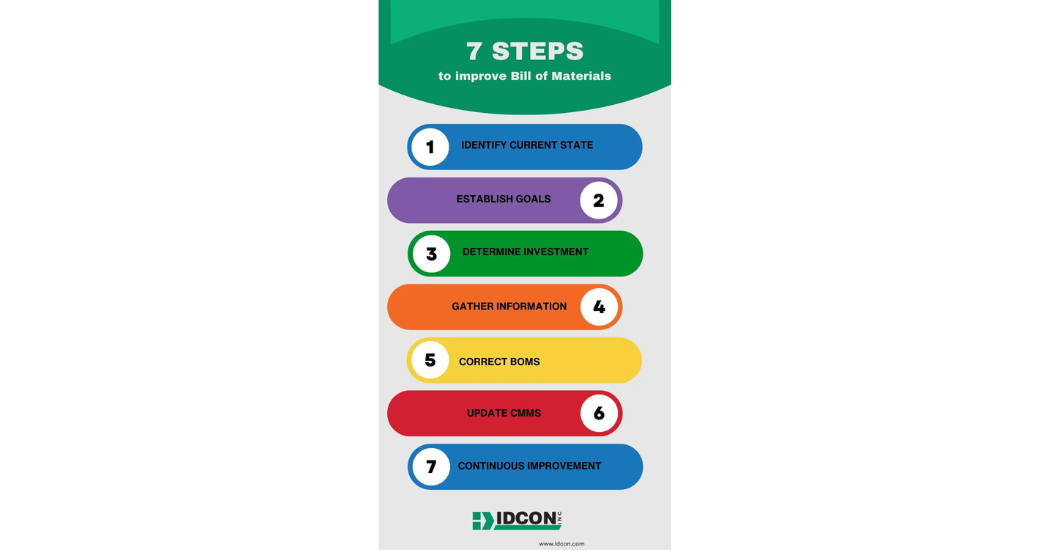
7 steps to improve BOM
Step 1: Identify the Current State
Begin with reviewing the hierarchy in your CMMS. Information you should review includes:
- Number of parts that are not currently linked to a BOM
- Number of equipment pieces that need a BOM
- Overall BOM accuracy and quality
We also need to interview key personnel and pull relevant data from the CMMS. We should review:
Consider Key Performance Indicators early in the process. Relate the current state of BOMs to useful KPIs that can be tracked throughout the project. Use KPIs that relate to stakeholder’s interests. Some examples include storeroom inventory reduction, decreased downtime or the amount of time freed up for mechanics.
- Time per week that mechanics typically spend planning their own jobs
- Time that planners spend per week tracking down or ordering parts
- Length of time outages are typically extended due to missing parts
- Cost of expediting parts over a typical month
Step 2: Establish Future Goals
These future goals can be based on benchmarking to best-in-class industry performers or other plants within the organization. Goals can also be based on targets set in conjunction with plant leadership. Link targets to larger organization goals. Take time to document a goal statement that is specific, measurable, achievable, relevant and time bound. The SMART goals will define and improve accountability of the project.
BOM Example
STEP 3: Determine Investment
Determine the level of effort required to reach goal. Build a workflow for the project. Identify the people and approximate time required to achieve each step. Look for ways to reduce hand-offs. Prioritize each goal based on the ultimate value, cost of the investment and time needed to reach the value.
The Return On Investment (ROI) can be calculated for each goal. Some organizations may require this be done for any project before resources can be used. Anyone can use this method to compare goals and help prioritize the next steps.
ROI % = (value-cost)/value x 100
When determining the investment be specific about the types and amount of information needed. Establish standards for data quality and define the taxonomy to be used. Spend time with the details of the CMMS. Identify the fields to be updated to meet the vision and achieve desired results.
BOM Workflow
To help reach the goals (see example above), a workflow will be developed showing the general steps.
If you have SAP. You need to determine the details needed and a standard developed for the project.
From the project workflow and understanding the details needed in the CMMS, a team of reliability engineers, production resources, mechanics and SAP experts will be needed for a full year to reach the stated goal.
STEP 4: Gather Information
Gather needed information to improve and build BOMs. This will include existing BOMs and current parts in the CMMS. Pull relevant data like “where used” reports. Note when parts were issued and to what equipment. Collect OEM and vendor manuals and relevant drawings. Save the collected information in a file structure that matches the equipment hierarchy.
STEP 5: Correct BOMs
Update and correct BOMs by checkBill of Materialsing parts lists against manuals and drawings. If possible, confirm parts listed in the BOMs have good issues against the equipment. Conduct field tours while the equipment is down and locked out. Make detailed measurements and pictures to aid in matching part descriptions against actual field information. Check the storeroom to verify OEMs and labels match part descriptions in the CMMS.
STEP 6: Update the CMMS
Transfer all updates to the CMMS. This may be done one-off as improvements are made or as part of bulk upload process at the end of the project.
Don’t underestimate the time and resources needed to update the CMMS. This may require a corporate team or specialized load sheets that will have to be developed and managed. Despite any challenges, don’t skip this step! BOM improvement projects that stop at a spreadsheet will fail to provide lasting value.
STEP 7: Continuous Improvement
Train end users on the new BOMs. Planners, supervisors, and buyers should be aware of updated BOMs and have confidence in the data. Ensure the equipment hierarchy and individual part details can be navigated. Include a step in MOC procedures to keep BOMs updated. Any changes made to field equipment must be reflected in the hierarchy and parts lists.
BOMs are an element of the technical database that support the overall work management process. No other element of the technical database adds as much value as BOMs. They enable planners to quickly order needed parts while primarily focusing on creating detailed instructions for the crews. This seven-step process can be used to improve BOMs at any plant, mill, or mine. Having accurate, accessible and applied BOMs is an investment in the future that lead to substantial returns for years to come.
Comments