What do Pump Pros Know and why do they know it? This series of articles highlight the brilliance of those who work with pumps. Read more Pump Pros Know.
Pump System Evaluation and Energy Costs
Understanding a pump system’s energy cost requires more than simply evaluating the pump, motor, and drive. Accurate calculations must consider the fluid properties, the system piping, additional end-use equipment, and the operating conditions required for the application. Fluid properties are significant because density and viscosity have a major effect on the pump’s energy consumption and the system’s piping friction losses. The diameter, length, and overall layout of the system can also affect energy consumption by adding additional head losses that the pump will have to overcome.
Fluid Properties
An essential characteristic required when evaluating a pump system is the fluid properties of the liquid being pumped. Whether pumping pure fresh water, water with additives or contaminants, or a completely different fluid, such as oil or other petroleum-based solution, physical properties of the fluid help determine the energy required to serve the application.
Important parameters to consider include:
- The specific type of fluid being pumped, whether it is water, a water-based solution, or other liquid.
- The temperature or temperature range of the fluid as it enters the pump and goes through the pumping system.
- The viscosity of the fluid, keeping in mind that viscosity may change as the fluid temperature increases or decreases. Rotodynamic pump performance is traditionally based on water as the pumping media and with all other factors being equal, pumping a fluid more viscous than water requires more power from the pump along with a reduction in head, flow rate, and efficiency.
- However, it’s important to note that positive displacement pump performance curves may be based on a fluid more viscous than water.
- The density of the fluid. Again, rotodynamic pump performance is based on pumping water. So, a fluid less dense than water—say, a light oil—will reduce the input power to the pump. Keep in mind though, that oil is generally less dense than water but has a higher viscosity. This is the reason why evaluating a pump system energy cost requires assessing more than just the pump, motor, and drive.
The Pumping System
A pumping system consists of straight pipe, elbows, fittings, valves, and other end use equipment for which a flow is required for a particular application. When a system is being designed, head loss calculations through all system components must be calculated. Limiting the resistance in flow throughout the system, either through increased pipe diameters or optimized system routing, can help reduce energy consumption and therefore lower energy cost.
Important factors to consider include:
- The length and diameter(s) of the system piping, plus the number of elbows, fittings, surface roughness, and additional end use equipment.
- The static lift (pressure head) the fluid will be pumped.
- The flowrate required for the application. In some cases, flow requirements vary according to operating conditions. In such cases, determining which energy efficient method for adjusting flowrate, such as throttling or a variable speed drive (or variable frequency drive), is most appropriate for the application needs to be addressed. Figures 1 and 2 show a comparison of two different methods of adjusting flow rate to meet a particular application’s operating conditions. For extreme changes in flow rate, there is a significant energy cost savings associated with variable speed pumping.
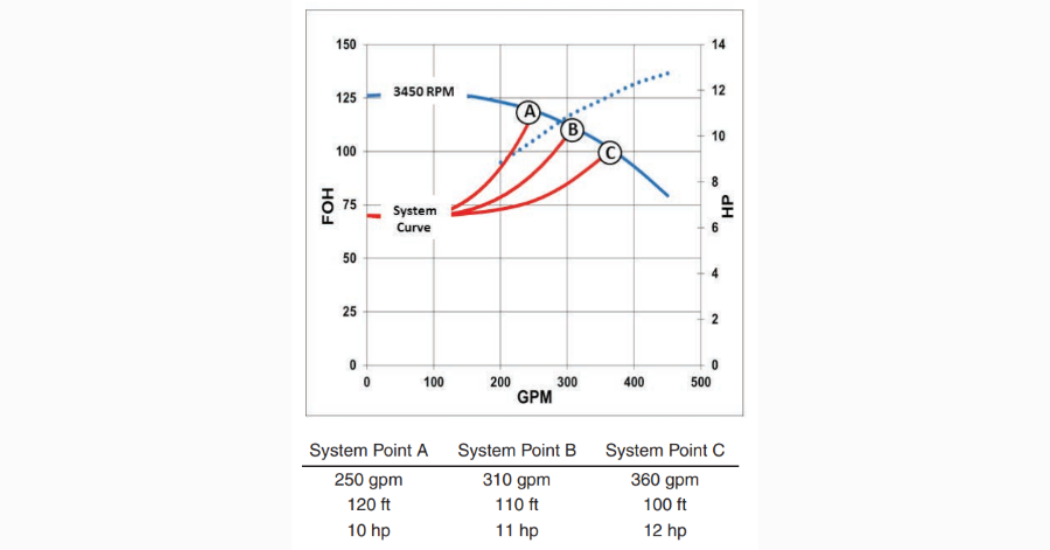
Figure 1: Power consumption by throttling. Image provided by the Hydraulic Institute (ANSI/HI 14.3 Rotodynamic Pumps for Design and Application)
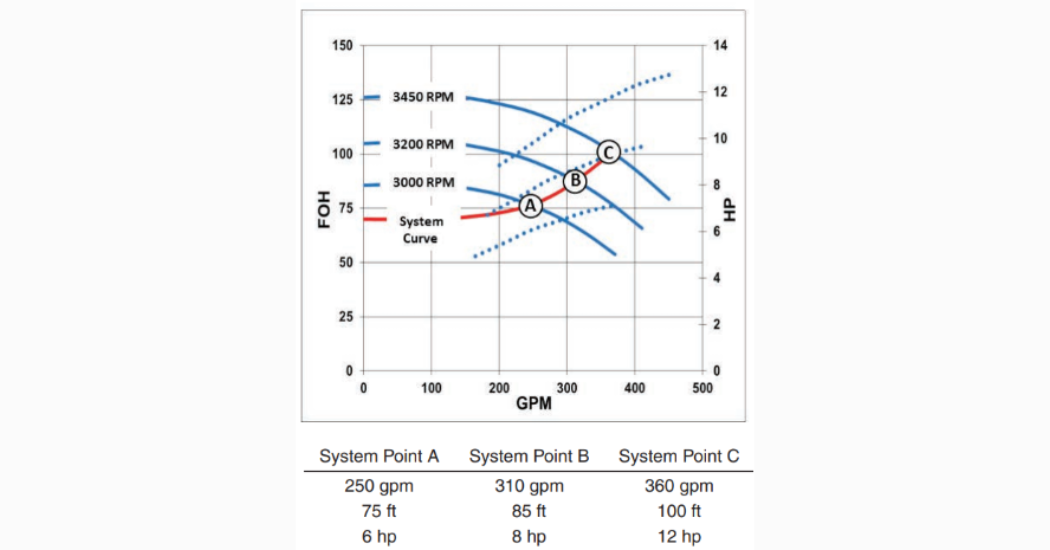
Figure 2: Power consumption using a variable speed (or frequency) drive. Image provided by the Hydraulic Institute (ANSI/HI 14.3 Rotodynamic Pumps for Design and Application)
The Pump, Motor, and Drive
Measuring energy consumption of a pumping unit (pump, motor, and drive) is achieved by installing an electric meter ahead of the main line that supplies electricity to the entire unit. The meter can measure the amount of power supplied to the motor or drive per unit of time, expressed in kilowatt hour (kWh).
This energy can be simplified to the consumed power over a period of time. For example, a pumping unit receiving 100 kW of power for one hour consumes 100 kWh of energy. The calculation becomes more complicated if the motor and drive operating the pump cycle on and off frequently.
For example, an application where the pump system provides cooling water to control process temperature may require the pump to cycle on and off several times per hour. If the pump mentioned above runs only 30 minutes total in an hour, you may be tempted to calculate its energy consumption at 50 kWh. This would be true only if the motor ran continuously for 30 minutes, then shut down for 30 minutes without a startup.
However, when a motor starts, an inrush current occurs that helps provide the starting torque required to bring the motor to full speed. Therefore, a motor that requires 50 kWh of power to drive the pump will momentarily require more at startup. In most cases, if a pump is scheduled to be cycled on and off several times an hour a soft start or VFD is used to reduce the inrush current by limiting the voltage supplied to the motor.
The use of a variable speed (or frequency) drive in an application that requires multiple operating conditions (for required rates of flow) can considerably lower the energy cost of the pumping system. However, if a variable speed (or frequency) drive is utilized in a constant speed application, the combined inefficiencies of the motor plus drive can cause you to be less efficient, compared to just a pump plus motor combination.
Pump Selection
Pumps are selected to meet system requirements, and their energy consumption depends on the system’s overall flow rate, pressure (head) and how often the pumps are operating. Selecting a pump based solely on maximum peak efficiency at the best efficiency point (BEP) can lead to a pump being under or oversized, or a type that is not applicable to the application.
Once all the variables of the pumping system have been accounted for, you can select a pump based on the flow rate and pressure (head) required for the application (the intersection of the pump curve and system curve, see Figure 3). Of course, pumps vary widely not only in size, but in the design and type. Some are made to accommodate solids, some handle chemical solutions that may be corrosive, caustic, toxic, or flammable. But for simplicity—and because they are the most common—the following discussion will focus on centrifugal pumps for water.
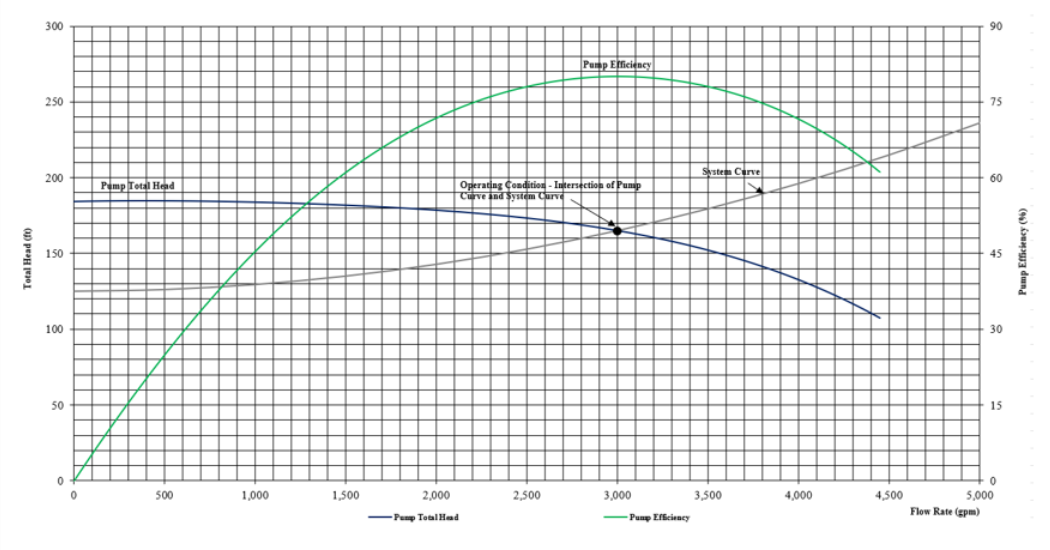
Figure 3: Simple system and pump performance curves.
Pump manufacturers’ technical datasheets contain performance curves that indicate the performance characteristics of the pump at a certain rotational speed. Adding to the complexity is that a given model of pump may use any of several different impeller geometries, and each impeller has its own performance curve based on its diameter, number of vanes and design.
Many pump manufacturers simplify this process by providing software that aids in selecting the size and design of pumps based on parameters provided by the user. Distributors and manufacturers representatives can also be helpful in selecting the pump best suited to a particular application.
From all this information, the energy costs associated with the entire system can be calculated by considering all the parameters of the duty cycle, piping network, fluid, pump, electric motor, and drive.