Complexities in wastewater are growing. Municipal wastewater contains elements such as organic matter, oils and greases, fibers, polymers and other substances that present us continuously with new challenges. Moreover, extreme weather conditions increase the variation of drought, rainfall and the risk of flooding, while there is a tendency to consolidate wastewater handling and centralize it in big wastewater treatment plants. Grundfos addresses these challenges with new wastewater hydraulics and material variants offering increased reliability and durability of the pumping solution, while reducing cost of operation and maintenance.
Purpose
This whitepaper provides recommendations for selecting the optimal material variant for different wastewater applications, including the new material variant in white iron execution and its properties, and discusses in detail the concepts of wear, abrasion and hardness. Performance including clogging behavior will also be discussed.
In addition, this whitepaper shows how wear and clogging are related, how they are tested in the Grundfos Water Utility Laboratory and results are presented, comparing different impeller materials available in the market.
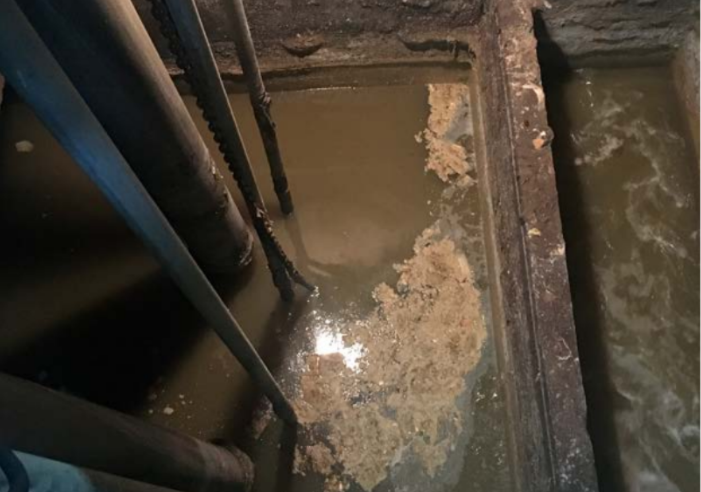
An example of a wastewater installation where pumps are submerged and installed on auto-couplings.
Executive Summary
Wear is the damaging, gradual removal or deformation of material at a solid surface. In wastewater applications, it is mainly the combination of abrasive particles, fibers and grease that cause wear. In this whitepaper, we focus on comparing the wear-resistant properties of hardened cast iron, stainless steel, and white iron materials for our new Open S-tube® hydraulics, using accelerated sand wear tests.
This whitepaper documents that hydraulic components in white iron are 2 times more wear resistant than hardened cast iron components after an accelerated wear test; equivalent to approximately 5 years of continuous operation. Moreover, our white iron material variant proves itself more wear resistant than one of our competitor’s white iron alloys in the market. Grundfos shows that with a wide offering of hydraulics and materials, we can provide you with the most optimized solution to handle wastewater; no matter how challenging the environment and reduce your operating costs with improved wear resistance and pump reliability.
Wear and Abrasion
Wear is the damaging, gradual removal or deformation of material at solid surfaces. The terms abrasion and wear are frequently used interchangeably; however, there is a difference. Abrasion is the action causing wear, the process of wearing down the material. Wear is an unwanted effect of exposure to normal use.
There are many types of wear, but for wastewater pumps, we are mostly interested in examining erosive and abrasive wear. The latter is the progressive loss of a metal surface material from the cutting or abrading action of solids or hard particles, carried in suspension in the pumped liquid, that are forced against and move along a solid surface with the flow. Erosive wear is caused by the impact of liquid or solid particles against the surfaces. ( To find out more about definitions of erosive and abrasive wear, go to www.sciencedirect.com/topics/engineering/erosive-wear)
In pumps, wear affects impellers, suction covers, volutes and other wetted parts in contact with the liquid. With higher velocity (relative velocity between solids and metal surface) inside the pump volute, water erosion is accelerated. Other factors impacting the rate of wear are size, shape, hardness, angle of impact of the particles and solids concentration and mass. Wear rate generally increases with increasing particle size, angularity, hardness and impact velocity.
For wastewater, it is mainly the combination of abrasive particles, fibers and grease that cause wear. The sand content found in wastewater may increase as a result of less water infiltration in urban areas, and it can be worsened by combined sewage pipes. Some of these combined sewer system installations are oversized and, although the sand concentration in wastewater is relatively low, the low flow velocities build sand deposits inside the pipes.
Market trends are towards utilising longer retention times (up to 24 hours), and to transport wastewater over longer physical distances to capture economies of scale, when treating wastewater in increasingly larger wastewater treatment plants. Even in rainy periods, the sand consistently enters into the sewer system, but the collector itself is not flushed. However, when heavy rainfall occurs, all the sand is carried away inside the system. Since the systems collect not only wastewater – the sewer system is used for all sorts of wastewater types such as drainage water, effluent and sewage – they present an ever-growing range of operational problems.
If we consider just 0.5% of sand content (by weight) in the wastewater and a pump that is pumping 350 m3/h (9,250 US gpm) for eight hours a day 365 days per year, then the pump is pumping a total volume of 5,110 tons of sand per year – this corresponds to approximately 255 truckloads of sand every year!
To compare the wear or abrasion-resistant properties of the different materials and structures, several test methods can be used, including an accelerated sand wear test. There are many factors that influence abrasion resistance, and this depends on the type of wear, but wear tests carried out with a disk rotating in a sand-water mixture have given an essentially linear relation between wear and hardness, albeit with a large scatter inherent to the testing techniques employed. (Source: www.springer.com/gp/book/9783662518281)
Hardness
Hardness is the resistance of the material to deformation, and it is tested with a mechanical indentation or abrasion which measures the surface resistance*. The most common hardness tests are defined by the shape or type of indent, the size, and the amount of load applied. Normally for metallic materials, the industry uses an indentation hardness test. This uses a specifically dimensioned constant compression load with a sharp object that causes an indentation, which is then measured. Typical hardness scales based on indentation are Rockwell, Vickers and Brinell, and it is possible to convert from one scale to another.
HB or HBW Brinell:
Proposed in 1900, it was the first widely used and standardized hardness test in engineering and metallurgy. According to the standards the Brinell method should be used for cast components, which are rough. The typical test uses a 10 mm (0.39 in) diameter steel ball as an indenter with a 29.42 kN (6,614 lbf) force. The large size of indentation and possible damage to the test piece limits its usefulness. For harder materials, a tungsten carbide ball is substituted for a steel ball.
Source: en.wikipedia.org/wiki/Brinell_scale
HR(C) Rockwell:
The Rockwell test uses the depth of penetration of an indenter under a large load (major load) compared to the penetration made by a preload (minor load). There are different Rockwell scales (A, B, C…) that use different loads or indenters. Rockwell C scale (abbreviated HRC) uses a cone-shaped, diamond-tipped indenter with a 150 kg (331 lbs) load. The higher the number, the harder the material. The Rockwell test is quicker than the Brinell and can be used on fully hardened steel.
Although metal hardness is not the sole criterion of resistance to abrasive wear as mentioned earlier, it does provide a convenient index in selecting ductile materials usually available for centrifugal pumps.
To find out more about definitions of hardness, go to www.sciencedirect.com/topics/engineering/hardness or en.wikipedia.org/wiki/Hardness
Hardening Of Different Impeller Materials
Hardening is a metallurgical metalworking process used to increase the hardness of a metal. The hardness of a metal is directly proportional to the uniaxial yield stress at the location of the imposed tension. A harder metal will have a higher resistance to plastic deformation than a less hard metal. To find out more about definitions of hardness, go to en.wikipedia.org/wiki/Hardening_(metallurgy)
Erosion and abrasion occur primarily in areas with high velocity and turbulent flow and is typically seen on impellers and volutes. The impeller is the most exposed part to abrasion and erosion – especially the impeller vanes – and that is why Grundfos has decided to harden them.
Grey cast iron:
Grey cast iron, named after the grey colour (due to the presence of graphite) is the most widely used cast material in water and wastewater pumping applications. It is used for housings where the stiffness is more important than its resistance to impact or shock. It is a relatively low-cost material with good machinability. It has a fair level of wear resistance but needs surface protection to withstand the special requirements for abrasive content, cavitation and corrosion resistance. Its hardness is around 180-230 HBW.
The guide vanes of Open S-tube® impellers from Grundfos are heat treated to increase the hardness (by forming cementite, which is a very hard compound) of the top of the blades by induction hardening. The hardening depth is more than 2 mm (1/16 inches) and the resulting hardness around 500 HBW (50± 3 HRC).
Stainless steel:
Stainless steel is a group of iron-based alloys that contain a minimum of approximately 11% chromium content, a composition that prevents the iron from rusting and also provides heat-resistant properties.
Stainless steels have a long history of application in contact with water due to their excellent corrosion resistance. Nevertheless, they are not recommended for use in an abrasive environment, and they are out of scope when talking about hardening. The hardness value is around 130-200 HBW (10-20 HRC).
White iron:
High chromium white cast iron (from the white cementite surfaces) is a ferrous alloy typically containing 11-30% chromium and 1.8-3.6% carbon, and with variable amounts of molybdenum. During the solidification process, the chromium and carbon transform into hard carbides and this combination results in a very good wear resistance when compared to other metallic materials. White iron is too brittle for use in many structural components, but with good properties for using it in typical wastewater applications. White iron has better corrosion resistance than cast iron but not as good as stainless steel.
Open S-tube® impellers in white iron execution offered by Grundfos are in accordance with GJN-HB555_XCR18 (with a minimum chromium content of 21%). The hardness of this selected alloy is 550 HBW (55 HRC).
Grundfos Test Laboratories
Grundfos Global Laboratories is a certified and accredited group of laboratories applying world-class knowledge and expertise for testing and developing wastewater pumps. Tests include performance testing, reliability testing, clogging testing, durability testing, sound and vibration testing, long-term tests, and a wide range of other tests.
These test facilities are independent of our factory testing. There, we validate our new designs and verify that our products not only fulfil our customers’ requirements, but also endure extreme conditions. In addition to complying with the most important international standards and norms, we have also developed our own testing standards and methods to reach the highest quality level in test performance and handling, making sure that the results are repeatable, tangible and reliable in any sequence or form.
The Grundfos Water Utility Laboratory in Hungary is a top modern test facility that to a very large extent is unmatched in the market. It is equipped with all necessary, and some unique, state-of-the-art test facilities to simulate the conditions that our solutions face in wastewater transport applications.
The evolution and diversity of the wastewater composition requires an innovative approach to ensure the constant improvement of our products, so that they can handle all kinds of wastewater reliably; without clogging and jamming, and with the minimum wear and tear.
Wear Resistance Testing
As stated previously, an accelerated sand wear test is used to compare the wear resistance of the different materials, which are used for components in direct contact with the pumped liquid. In Grundfos test facilities, we use the entire pump for the testing, in dry installed conditions, instead of only recreating the real field conditions inside the pump volute.
The test lasts 72 hours and the pumps run at their Best Efficiency duty Point (BEP).
For Grundfos SE/SL pumps fitted with Open S-tube® impellers, the material variants offered are hardened cast iron, stainless steel and white iron. The hardened cast iron and stainless steel versions come without a guide vane in the suction cone.
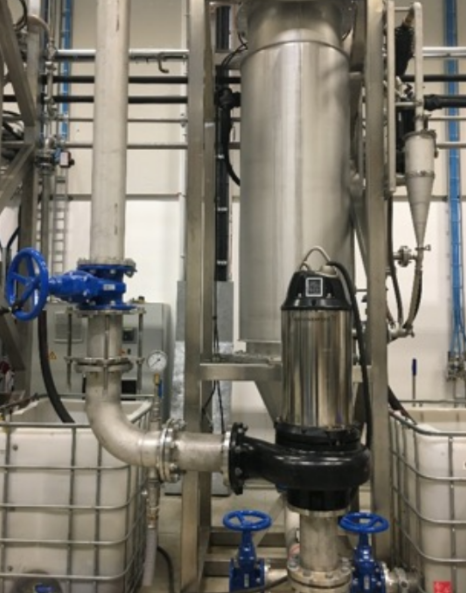
Grundfos SE pump subjected to a wear-out test.
The white iron includes a guide vane because it is meant to be used in applications with an unusually high or extreme content of long fibers and abrasive solids.
The wear affects more in areas of high velocities, specifically increasing the impeller gap clearance between the impeller and the suction cone. Increased gaps and geometry changes lead to reduced head, due to the bigger leakage flow between the high and the low-pressure side of the pump. With this kind of hydraulic solution, we set the clearance gap between the impeller and the suction cover at 0.5 mm (0.02 inches) before the first test, and then we monitor how it evolves every 24 hours.
To evaluate the extent of the wear and where is it happening, we 3D scan the wetted parts before and after the full test. Moreover, to assess the impact of the wear in the pump performance, we carry out a hydraulic performance and clogging test after every 24 hours in the test cycle.
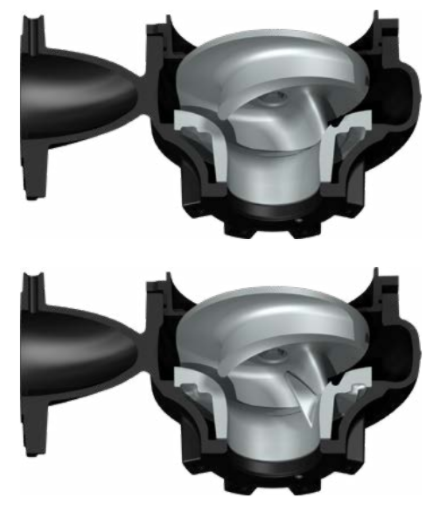
Open S-tube® hydraulics for SE/SL pumps, without and with guide vanes.
Clogging Testing
The consequences of clogging and jamming in wastewater pumps always result in an increase in total operating costs, therefore these phenomena must be avoided as much as possible.
There is no international standard way for assessing the performance of a wastewater pump against clogging, nor for providing a reliable performance comparison in a repeatable environment. In recent decades, technical universities and wastewater professionals have tried to work out a standard to define the composition of traditional wastewater. The aim has been to use such a definition to be able to test, replicate tests and to compare performance and clogging capabilities of wastewater pumps of different brands and types. However, as the composition of wastewater fluctuates and is different around the world, this has proven not to be possible.
Consequently, several technical universities have identified challenging objects and the volume of these to categorize different contamination classes or levels. It is the work done by these technical universities that Grundfos has used as a strong source of inspiration when doing internal performance and clogging tests.
The Technical University of Berlin has defined a liquid that when pumped, will have the same behaviour and effect to the pump as when wastewater with a certain content of fibers is pumped. This liquid consists of water with extra sturdy wet wipes that have a net of reinforcement plastic or nylon material.
During the test, flow, head and power consumption parameters are monitored. A video recording of the inlet helps assess the clogging evolution during the test. At the end, the pump is disassembled, and pictures of the fiber accumulation are taken to document the clogging.
Clogging tests after each wear test loop of 24 hours give us information of the change in pump behavior with increased gap and worn edges. The tests were performed with 3 levels of contamination – low, medium and high
– except for the white iron material variant, which endured a doubled high contaminated liquid plus towels. The pumps were running at the Best Efficiency duty Point (BEP).
Comparison Tests Results
Impeller gap clearance:
The first parameter to be discussed is the suction gap evolution. In the chart, you can see how after 72 hours the smallest clearance gap increase is for our white iron material, followed by a similar alloy present in the market. From this, we can conclude that our white iron material components have a very high wear resistance and are two times more wear resistant than hardened cast iron components after only 72 hours of testing. In this case, the behavior of the stainless steel can be explained by the hardness, depending on the chrome content of the steel used and other factors, such as the type of wear induced.
Performance and clogging:
Hydraulic performance measurements after each 24-hour test cycle show how the wear of the impeller blade affects the pump behavior at Best Efficiency duty Point (BEP).
As expected due to the higher wear, after 72 hours of wear test the stainless steel has the highest performance drop, reaching up to a 14.63% in head loss and a 4.78% increase in power consumption. However, Grundfos white iron has only a 3.63% loss of head and a 0.72% drop in power consumption. As it can be seen in the 3D scan illustration, the wear is barely noticeable. Our white iron competitor alloy has almost the same head loss but a 1% increase in power consumption and a 3.2% drop in efficiency.
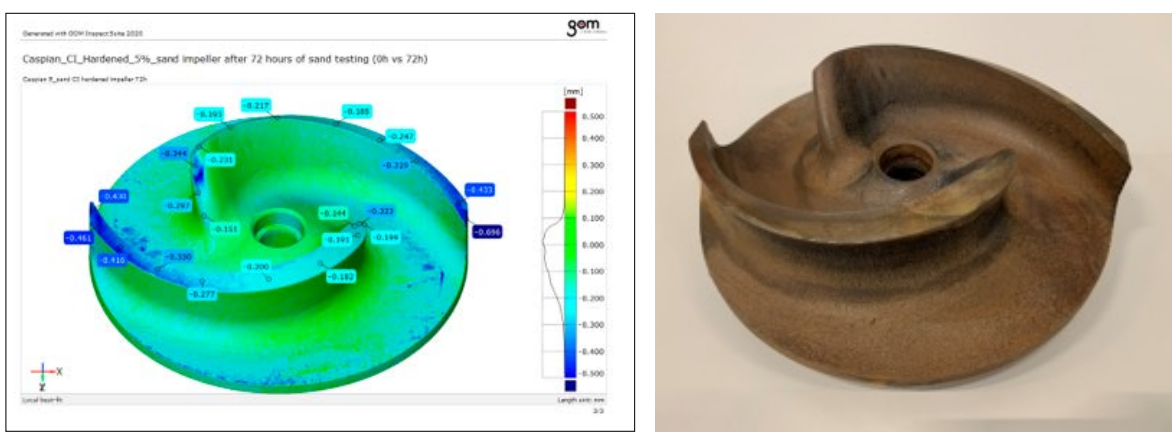
3D scan results after the full wear test with the hardened cast iron impeller.
The blue color shows where the deepest wear is. Next to it, a picture of the impeller after the tests.
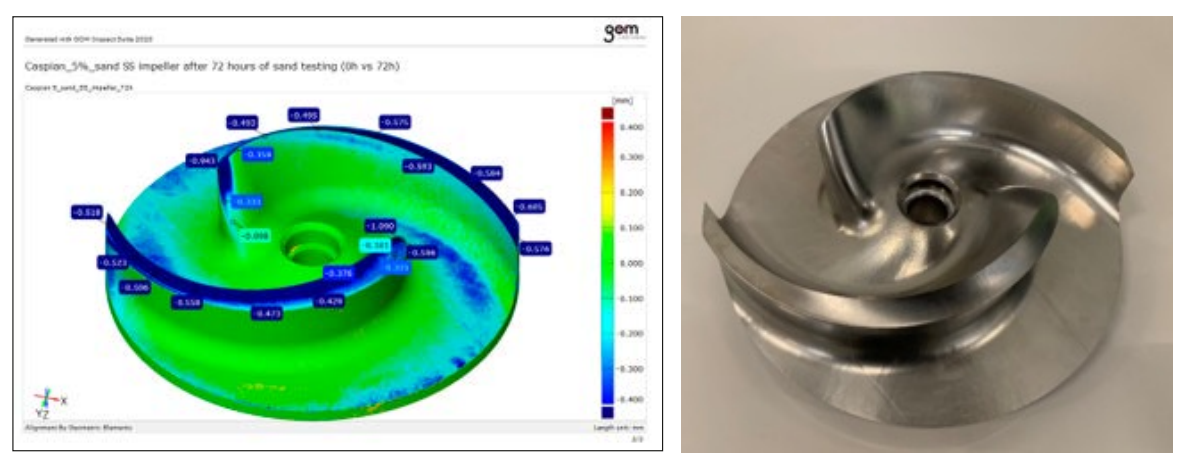
3D scan results after the full wear test with the stainless steel impeller. The deeper the blue colour the more wear there is. Next to it, a picture of the shiny impeller after the tests.
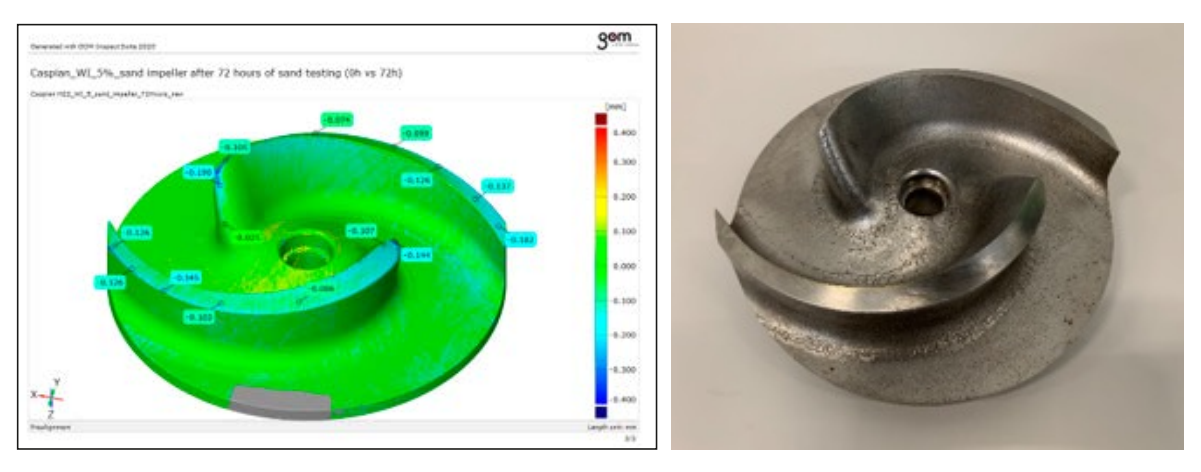
We can see in the 3D scan results after the full wear test that the Grundfos white iron impeller has barely been affected (there are only hints of light blue color showing a minimal wear on top of the blades). Next to it, the corresponding impeller picture after the test.
In the table ‘Weight loss of impellers’, the different impeller weight losses for each material can be seen. Grundfos white iron has the lowest material loss, followed by one of the white iron alloys present in the market.
Regarding clogging, all the materials passed the clogging testing after the wear tests, according to our acceptance criteria. In this whitepaper we will comment only the Grundfos white iron behavior, since it endured a doubled high
contaminated liquid with extra towels, which is a level that would be very difficult to find in real life.
For better comparison and assessment, we use a normalized head, which means we measure the head of the pump before we start the test– with clean water – and after adding the contamination, we divide by the new value, to see if we have any degradation of the head. It gives more information than the real head value.
The pump works seamlessly in high contamination. When we add the doubled high contamination and the towels, the flow of the pump drops to a 92% on average and the head to a 78% of its original value. The Open S-tube® impeller self-cleans, which means that when the dusters or wipes accumulate on the tongue of the volute, they clean themselves when they reach a certain amount. This happens with a frequency that increases with the number of dusters. This phenomenon results in a temporary increase in power consumption, which is normally what the customer sees, but then it goes back to the original level. The same behavior goes for the current consumption.
Conclusion: Material Selection For Pump Hydraulics
When selecting a pump, the first things to do are select and size the right pump type for the application. When selecting the material for the hydraulics, factors such as wear resistance, corrosion resistance, intermittent or continuous duty, expected pump life and cost must be taken into consideration. The actual operational cost is the one that should be taken into account. Cast irons are typically the least expensive and most available for replacement, nevertheless they can become expensive if they fail prematurely and need to be replaced often. They have a fair level of wear resistance
but need coating (which Grundfos offers) to withstand the special requirements for abrasive content, cavitation and corrosion resistance. Stainless steel, on the other hand, is very good in corrosive environments; however, as we have seen, wear resistance is quite low.
Finally, one can choose white iron, which is obviously the most expensive material, but with excellent properties for using it in typical wastewater applications, such as a fair corrosion resistance and outstanding wear resistance. Since we add the guide vane to our white iron Open S-tube® hydraulics, we can also target the highest fiber content applications.
With the new Open S-tube® impeller and the availability of the white iron material variant, Grundfos addresses the growing challenges of complex urban wastewater. Greater durability in the pump hydraulics help increase operational reliability in the wastewater network.