The Challenge: High-performance pumps and valves for critical services onboard the world’s largest FPSOs.
The Solution: Custom-engineered pump systems and versatile valve/positioner packages suited for severe service applications.
Global capabilities for a global project
When planning began for ExxonMobil’s Kizomba A and B floating platforms, a critical component for meeting project timelines was the installation of special-service, high-performance pumps and valves immediately following keel-laying in Korea, where construction took place.
To meet the challenge of building the world’s largest FPSOs, with the capacity to produce 500,000 barrels of oil per day, ExxonMobil chose Flowserve Corp. to complete special orders for multiple offshore production pump and valve control systems.
“ExxonMobil is an innovative and pioneering company, and the Kizomba project proves the extent of their vision,” says James Quain, Flowserve vice president and executive sponsor for the Kizomba project. “Flowserve is pleased to have been chosen to provide critical service elements for these massive FPSOs.”
A proven ExxonMobil supplier and single-source provider of fluid motion and control products and services, Flowserve used its global reach to execute the project. With on-the-ground support in Korea, Angola and the United States—including worldwide manufacturing facilities, engineering and design, project management, service operations and technical support—Flowserve built the Kizomba A and B pump and valve systems, then unitized and tested the packages for shipment to Korea and installation on the FPSOs.
Flowserve provides wide-ranging pump systems
Flowserve manufactured 74 pump systems for the Kizomba FPSOs and TLPs in various sizes and capacities for such critical services as water injection, bullheading, sulfate removal, crude transfer, crude offloading, and fire water service. Flowserve also supplied pump systems for seawater lift and process cooling.
All of the Flowserve pumps are API 610-compliant and are designed to meet ExxonMobil’s varied and detailed specifications. Many were built from special alloys and steels. Most were custom-engineered and manufactured, designed to be modular and to accommodate the weight and space parameters of the FPSOs and TLPs.
“Flowserve’s experience in the offshore market allowed us to supply ExxonMobil with the wide range of pump systems it needed at Kizomba,” says George Lekas, Flowserve Pumps ExxonMobil global account manager. “Our global manufacturing, technical capability and ability to provide local support to ExxonMobil allowed us to coordinate manufacturing, service and technical support for the U.S., Europe, Asia and West Africa.”
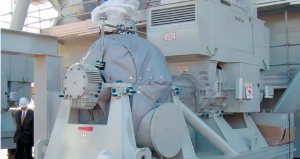
A model 12LPN29
single-stage process
cooling pump with a 1000 hp motor; six in total are installed on Kizomba A and B.
Flowserve supplies vertical pumps for seawater lift and rig ballast water services; process pumps to move and handle oil, gas and water; high-pressure pumps for seawater injection; high-capacity high-pressure pumps for crude oil transportation; and pumps for utilities and fire protection.
Flowserve took advantage of its integrated project management and global manufacturing, packaging and testing capabilities to deliver the Kizomba pump systems. While some Flowserve facilities manufactured the pumps, others unitized and tested the packages—a process that requires a high level of coordination and teamwork. A global project manager served as a single point of
contact for ExxonMobil and coordinated the efforts of the project managers during execution, from quotation to installation and startup.
“Flowserve is the largest supplier of pumps to the oil and gas industry, and has always been a leader in pump technology,” adds Lekas. “We are a global supplier of pump systems with the ability to serve new geographies and markets, and are always interested in developing new technologies.”
Flowserve valves tackle severe service
Drawing on 25 years of experience in the offshore oil and gas industry, Flowserve provided 360 control valves for the Kizomba project. The valves were primarily variations of its Mark I globe valve, with severe service trims designed to reduce noise, cavitation and vibration. With sizes from 1 inch to 30 inches and ANSI pressure classes from 150 to 2500, the Mark I valves meet the wide range of high-pressure and severe service parameters. For the FPSOs, Flowserve provided sixteen 20- to 30-inch valves. Alloys required included Monel, Duplex stainless steel, carbon
steel and stainless steel.
A key feature of the solution offered by the Mark I valve is the high degree of interchangeability afforded by the use of one valve type in several disparate applications around the ship. This minimized the number and type of spare parts required a significant cost and weight benefit in the tight confines of the ships.
Flowserve was also able to outfit the entire project with just five sizes of its standard doubleacting piston actuator, further increasing part interchangeability and decreasing the need for
spare parts.
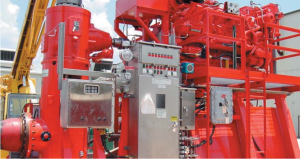
One of eight 28EKM dieselpowered, three-stage, vertical turbine pump packages in use on the Kizomba FPSO
vessels.
“These products are designed for high performance and long service lives,” says Wayne Buhler, Flowserve Flow Control oil and gas marketing director. “Statistically, we would expect a very high mean time between failures and a very long mean time to repair these control valve and actuator packages.”
Another important feature was the use of the Flowserve Logix™ 1200 digital positioner to control all of the modulating control valves. The Logix 1200 uses the HART communications protocol to communicate with a facility’s DCS (distributed control system) and enables a 30-inch valve to maintain a precise position within
thousandths of an inch.
“These positioners perform self-diagnostics and have a health indicator light that lets the operators know whether the positioner is functioning at peak ability or if there are problems,” notes Buhler. “They are ‘smart’ positioners with user-configurable alarms and the ability to provide remote valve diagnostics, including valve signatures and alarms.”
Another key reason ExxonMobil selected Flowserve for the Kizomba project was the compactness of its valve design. “Space is very important with a facility like Kizomba because you only have the deck of the ship to work on,” says Buhler. “Flowserve valves saved a lot of onboard space and weight, which enables the FPSOs to hold more oil.”
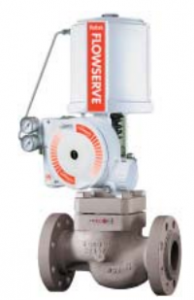
Mark I valves with specialized trim packages are used in varied severe service
applications throughout the Kizomba FPSO vessels.
He adds, “We have years and years of expertise doing FPSOs. We cut our teeth in the North Sea, considered by many to be the most difficult offshore environment. We’re great at special valve and pump design, engineering, manufacturing and service for the offshore oil business.”
A global leader in fluid motion and control
Flowserve offers a complete line of performance proven pumps, valves and seals for offshore oil and gas services. A global supplier operating in 56 countries with 24/7 capabilities, Flowserve delivers innovative product and service solutions and lean, high-quality manufacturing, making it a one-stop shop for all types of fluid motion and flow control applications.
For more information regarding Flowserve pumps, contact George Lekas, glekas@flowserve.comand for Flowserve valves, contact Wayne Buhler, wbuhler@flowserve.com. Or visit www.flowserve.com for complete details on Flowserve fluid motion and flow control solutions.
©2004 Flowserve Corp