Concentrated solar power (CSP) stores the power of the sun in the form of heat to enable utility companies to produce carbon-free electricity. CSP plants can generate electricity 18 to 24 hours a day — and especially during the night, when solar panels do not work.
This form of energy storage provides a base load source for power that improves operational efficiency and reduces costs. CSP can also be used by industry as a heat source for manufacturing processes.
With temperatures reaching as high as 600°C (1,112°F), CSP plants need proven, specialized flow control equipment that can take the heat and keep on running. If your company can overcome the technical challenges of CSP, you’ll benefit by:
- Reducing carbon dioxide (CO2) emissions related to energy production
- Achieving objectives for the energy transition from fossil fuels to zero-carbon sources
Developing renewable energy sources like CSP lies at the very core of a superior energy transition strategy. That’s what Jeff Parish talked about at Destination Innovation, the virtual expo from Flowserve. The ultimate goal for utilizing this carbon-free method of energy storage is to provide the full range of temperatures required for industrial processes. Examples include cement and glass making, hydrogen (H2) production, seawater desalination and food processing.
Heating up industrial processes reliably
CSP efficiently and reliably stores heat as energy that can keep a plant running after sunset. That’s the key advantage of CSP compared to photovoltaic (PV) technology used in conventional solar energy plants.
Rapid advances in CSP design and temperature capacities are driving adoption:
- ~5,000 MW of operational commercial power generation is available worldwide
- ~4,300 MW of new capacity is planned in the next two to three years
Parabolic troughs are the most common CSP configuration. They focus sunlight onto pipes in which molten salts circulate. The salts absorb heat, which is transferred to a holding tank throughout the day. The heat is used to generate electricity immediately or at a later time. When CSP is applied directly to industrial processes, any residual or process waste heat also can be used to generate electricity for the facility or transmitted to a utility grid.
Power towers are the most common new CSP plant design. These towers can operate at higher temperatures and are more efficient than parabolic troughs. Nitrate salts are used in all CSP systems, but that will change. The demands for ever higher operating temperatures and improved efficiency require switching to chloride salts along with more robust flow control equipment construction. By doing so, CSP plants can withstand not only higher temperatures, but more corrosive conditions.
CSP System Performance: Read Flow Control in Solar Power Generation: Part 1 and Part 2
What’s next to support CSP adoption
The quest for greater efficiency and lower costs is pushing the limits of current solutions. The target goal for CSP is $0.05/kWh by 2030. But for that to happen, system reliability must be improved.
Among the challenges to be solved is how to improve resistance to corrosion and minimize leakage.
With nitrate salt CSP (Generation 2) units, operating temperatures of 580°C (1,076°F) can be reached. By utilizing chloride or fluoride salts in Generation 3 CSP units, operating temperatures of 750°C (1,382°F) or higher can be reached.
Fluoride salts are expensive. While less costly, chloride salts are more corrosive, i.e., they can damage valves and lead to both equipment failure and unplanned downtime. The use of chloride salts requires the development of new materials from which to construct the valves and pumps. What’s needed are advanced valve designs that incorporate high-strength nickel materials to better withstand the corrosive conditions.
On top of these hurdles are the existing issues that current nitrate-based CSP plants face, such as salt leaks through packing and gaskets, short maintenance windows, and recovering from salt freeze situations.
Withstanding thermal and dynamic sealing issues
To maximize your investment in CSP facilities, partner with specialists who offer a proven portfolio of molten salt valves and vertical turbine pumps. Flowserve is a leader in these applications. They design flow control equipment to operate for decades in the toughest environments with the highest levels of performance and reliability.
One example is the Valtek® Mark One™ globe valve from Flowserve, which is specified as a control valve as well as an isolation valve in CSP systems. Flowserve’s currently installed Generation 2 configuration includes bellows seals and pressurized metal O-rings for gasket seals. In combination with special load washer under-the-body bolting, these features compensate for thermal expansion issues, maintain dynamic sealing, and provide proven sealing capability to prevent leaks.
Careful thermal heating control and temperature monitoring help prevent the flexing of bellows in the presence of solid salt.
With the demand for higher Generation 3 operating temperatures using more corrosive chloride salts, new materials can be coupled with various design changes to meet the performance requirements.
Optimizing proven control valve design
Flowserve’s next-generation control valve technology incorporates high-strength nickel alloys and ceramics into the construction of valve components. They also have developed pressurized twin packing systems that resist oxidation, corrosion and salt packing. They quick-change packing canister makes packing easier to replace when maintenance is required.
The Valtek Mark One control valve for CSP applications now includes special seals that can handle thermal cycles without leaking. New multi-ply pressurized bellows construction technology lowers the pressure differential across the bellows walls, giving these types of seals longer life and greater resistance to corrosion and rupture.
Likewise, new methods of controlling system temperatures through a self-contained thermal management system (TMS) greatly enhance the ability to recover a CSP system from a salt freeze.
And Flowserve didn’t stop there. Flowserve is developing methods of isolating the corrosion zones away from critical valve components to extend their life. By combining these enhancements with our proven Generation 2 CSP technology and experience, a complete control valve system that addresses all the current pain points experienced by CSP plant operators can be accomplished.
Partner with molten salt process experts
Continued investments in CSP facilities by companies like yours will help drive further improvements in molten salt-based technologies. These include the introduction of other types of salts that more efficiently transfer and store heat or are used in petrochemical processes, and low-pressure, liquid salt-fueled Generation 4 reactor systems.
Bringing these to market must be done in ways that enable you to meet project timelines, achieve business objectives, and accomplish your energy transition goals. That requires a flow control equipment partner with global resources, deep engineering expertise to innovate materials, and design capabilities to withstand high temperatures and corrosive CSP environments.
It also requires a flow control partner with advanced testing capabilities. That’s the only way you should invest in new control valve designs. Working alongside such a partner enables you to be confident that your critical energy supply systems will indeed minimize leakage, enhance efficiency, and operate reliably to avoid unplanned downtime.
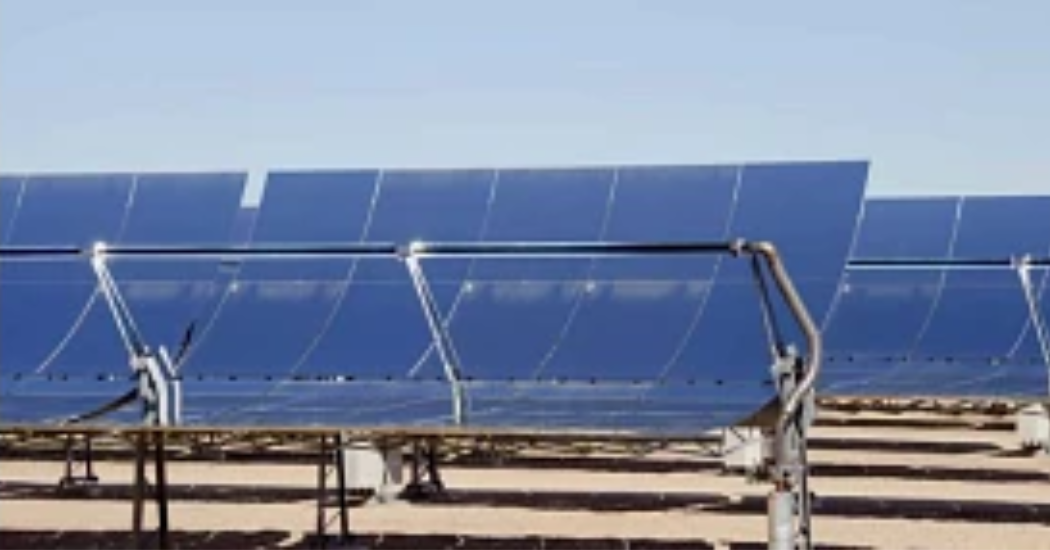
Concentrated Solar Power -Application Solution Guide
About the Author
Jeff Parish | Technology Development – Valve Applications Specialist
Jeff Parish is a valve application specialist and a member of a Flowserve team developing the next generation of valve technology focused on energy transition. He’s one of our experts in molten salt valve design, methane pyrolysis for H2 production, Generation 4 small modular reactor (SMR) and molten salt reactor (MSR) development, supercritical CO2 power cycles, and high-temperature molten salt carbon capture.