Contributor: EagleBurgmann
Latex is a dispersion of tiny polymer particles in water. The milky fluid contains about 50% water by weight. The diameter of the latex particles is close to ten-thousandths of a millimeter. The polymer core is surrounded by a polar shell that interacts with water, stabilizing the dispersion. Synthetic polymer dispersions are produced by polymerization of monomers in an aqueous solution in a reactor.
Mechanical seals are required on the latex manufacturer’s pumps at all stages of the dispersion production process including raw material in-feed, polymerization, dispersion processing and finished product tank storage. The pumps run continuously or discontinuously at different stages in the process.
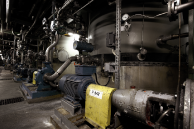
A typical tank storage area with transfer pumps
The engineering challenge is to design seals for the pumps that are used to handle dispersions (latex). The problems are particularly acute in process steps where the dispersion contains latex laden with residual monomers; for example, during dispersion processing. All of the process stages in the latex production process run at low temperature and pressure.
One major reason why more extreme production conditions are avoided is the fact that polymer dispersions are not thermodynamically stable and tend to coagulate, making the medium difficult to pump. Adhesiveness, which is desirable in the finished product, can cause leakage or total failure of the seals. Latex adheres to the warmest surface (the seal faces) and diffuses after only a few hours in between the sliding faces. The seals then open against the force of the buffer pressure. Ensuring that the shaft seals do not leak is particularly important in this difficult process step.
Causes of Seal Failure in Latex Pumping Applications
Double mechanical seals are pressurized with buffer fluid. The buffer pressure, acting in the direction of the product side (latex), decreases in the seal gap. As a result, latex and the buffer medium intermix on the product side. Friction heat in the seal gap causes agglomeration of the polymer particles. When this happens, the seal gap opens and the seal may be destroyed. The buffer fluid can then leak out, or latex can penetrate into the buffer chamber, causing the seal to fail.
To avoid this scenario, the EagleBurgmann engineering team had to develop a seal design that prevents contact between the seal and the product. Because the pumps run continuously or discontinuously depending on the process stage, a different sealing solution was needed for both operating modes.
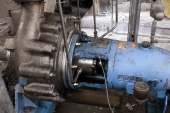
This type of pump with a special
EagleBurgmann cartridge
seal is used at various stages
in the process
Customized Sealing Solution
For pumps that handle latex that contains monomers, EagleBurgmann engineers developed an enhanced version of a seal which complies with clean air regulations (TA-Luft): a double Cartex cartridge seal with throttle for controlled flushing in the direction of the impeller. For an added margin of safety, a knife-edge is placed on the product-side seal face, ensuring that the mechanical seal does not fail due to insufficient flushing. No shutdown seal is needed because the pump runs continuously.
Development and optimization for this project included the rubber bellows single seal and the double cartridge seal with flush throttle ring on the product side and a knife-edge face. These Cartex dual-action mechanical seals also created an opportunity to optimize the pumps and significantly increase their service life. Due to shear forces, lumps can form behind the impeller, blocking the impeller and causing the motor to shut down as a result of overload. In addition, the back vanes on the impellers were removed, reducing shear forces and preventing agglomeration. These modifications along with other improvements, which in turn extend the total service life of the pumps, were only possible in conjunction with the modified seal system.
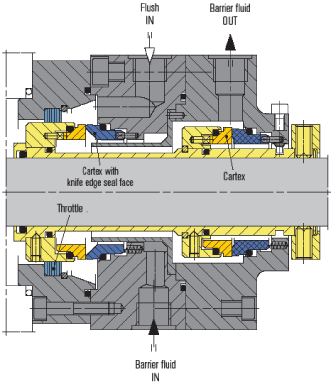
Cartex cartridge seal with throttle and knife-edge face
The operating mode of the Cartex seal is also unusual, as there is no pressurized buffer system. An external water supply is used simultaneously for the buffer and flush system.
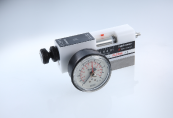
FLC flow controller
The central water supply ensures high availability. An EagleBurgmann FLC flow controller ensures a constant, defined flush flow that is not dependent on pressure.
Efficiency and Productivity Gains
The level of collaboration between the latex manufacturer and the EagleBurgmann Service Center has been excellent. Through a very constructive and professional joint effort, EagleBurgmann quickly developed initial prototypes that provided a solution to what appeared to be an intractable problem. Subsequent development work has been equally satisfactory. Service life in the most problematic process stage has been increased dramatically from just a few hours of operation to as much as three years.
Based on the positive results so far, the customer has deployed modified Cartex seals in approximately 30 or more pumps at the plant, with additional seals being planned. In most cases, even when the pumps are removed and cleaned, the seals are reinstalled without repair.
For more information on this application, contact us at info.us@eagleburgmann.com.
Interested in Same-Day Shipping for Your Mechanical Seals?
Complete the form below to get more information about EagleBurgmann’s program to get qualifying mechanical seals into end users’ hands faster and at a better total cost of ownership!