Working with Large Hubs the Hard Way
As the world’s heavy industries strive towards larger and more powerful equipment, CouplingCorp is helping to make it easier to keep that machinery running using large clamp hubs. Historically, there have been several ways that hubs have been installed on large shafts (12 inches and above). These methods have advantages and disadvantages, but sometimes, the disadvantages become more significant as the shaft sizes increase. The Anderson Clamp Hub is specifically designed to help alleviate many disadvantages of these other methods.
Keyed Hubs With a Slip-Fit
This method is straightforward and relies entirely on the torque driven through the keyway. Installing and removing the hub require it to be held perfectly aligned with the shaft to avoid binding and galling. The more clearance between the hub and the shaft, the more the hub is free to wiggle on the shaft as loads change or misalignment occurs. Over time, this movement can cause fretting, galling, or stress risers on the hub shaft, hub, or keyway. Any of these conditions caused by movement can lead to premature (unexpected) failure, which would generally be catastrophic. This method would never be a good fit for higher performance or higher speed applications.
Hubs Using Heat to Provide an Interference Fit
An interference fit using heat is a typical installation on all performance levels. The hub is bored with a slight interference compared to the shaft size. Then, the hub is heated to create a very slight clearance for installation and quickly pushed onto the shaft. Hub removal requires it to be heated again in place and pulled off the shaft quickly. This system has several problems (check out this video to see some obvious ones!):
- Heating a large hub can be difficult and time-consuming, especially if you need specific induction heaters.
- When installing or removing, it is tough to know how well the hub has expanded, leading to hubs getting stuck halfway on or off, leading to using a hydraulic pusher or puller to finish the job. When this happens, there is an increased danger of damaging the shaft.
- It can be challenging to control the axial position when installing.
If the hub position is different than expected, or an adjustment is required for other reasons, it could be very challenging to heat the hub and move it a minimal amount. Lastly, depending on the application, hot work permits may be required before heating the hub. This process can be more time-consuming than the installation, depending on how the facility is set up (explosive gas nearby, valve locations, etc).
Hydraulic Expanding Hubs
These hubs rely on hydraulic pressure to increase bore clearance fairly quickly. Hydraulic hubs require porting through the shaft or the hub to route very high-pressure oil to the interface between the hub and shaft. In most cases, the shaft and hub must be tapered to allow for installation and removal. This means both the shaft surface and the hub bore have to be free from defects as well as very round. If they aren’t nearly perfect, there is a risk of oil leakage. This makes retrofitting (or even multiple uses) more risky because of the possibility of scratches or bores out of round.
Another typical problem associated with hydraulics is the need for the right equipment in working order. It is common for a hub removal to be delayed because the crew needs a hydraulic fitting to mate with that particular hub or shaft. The other potential problem is the safety aspect of high-pressure hydraulic fluid and having a large hub move very suddenly. In addition, the use of hydraulic oil on the shaft can require an additional waiting period to allow the oil to “weep” back out of the mating surfaces.
Make the Job Easier Using a Large Clamp Hubs
Recognizing the shortcomings of these existing methods, CouplingCorp is setting a new large clamp hub standard with the Anderson Clamp Hub. There are several reasons why this design makes installation and removal so much more efficient and safe.
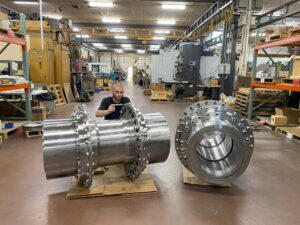
Large FLEXXOR coupling with Anderson Clamp Hubs
Clearance Fit
The Anderson Clamp Hub has a bore with a slight clearance fit over the shaft. So, one mechanic (with a crane) can slip the hub onto the shaft in seconds. The other benefit is that the hub can be positioned (and adjusted) to achieve the perfect distance between hub flanges to allow the flexible coupling to be in the correct axial (and angular if there is a timing component to the installation) position. Even though the hub starts with a clearance, it clamps concentrically onto the shaft to keep the hub on the centerline of the shaft.
Simple Tightening Process
Unlike the other methods, the Anderson Clamp Hubs only uses simple tools – usually a large socket with a breaker bar. There is no need for a flaming torch or a hydraulic pump. The process is simple and repetitive – tighten one load screw a small amount, move to the next, and keep going until the collar has moved the prescribed amount. One mechanic can do this, although having a second mechanic can make it physically easier. A hub is normally installed in less than 30 minutes, with very large versions (12-inch shaft and larger) taking 1 to 2 hours.
The Removal Process has a Backup Plan
With heated and hydraulic hubs, there is no plan B for relieving the interference to remove the hub. If the heating or hydraulic pressure doesn’t work, the only other plan is to destroy the hub by cutting it off or taking a considerable risk and using hydraulics to drag the hub off the shaft. In this case, there is a significant risk of damaging the shaft or the hub (or usually both). With the Anderson Clamp Hub, there is a built-in release mechanism if the hub doesn’t release when the loading screws are loosened. A set of holes through the flange allows a set of bolts to “pull” the collar back toward the flange and release the pressure between the hub and shaft. At that point, the hub can be pulled off with little to no damage to the hub or shaft.
Easy to Retrofit
The Anderson Clamp Hub doesn’t rely on a special feature on the shaft like keyways, hydraulic ports, or tapers. Therefore, it doesn’t matter what features the shaft has, the Clamp Hub is designed to fit. In addition, shafts that have damage (scrapes, flats, gouges, etc) can still work when clamped by the Clamp Hub.
For these reasons, the Anderson Clamp Hub is a superior option for large shafts. When analyzing the economics of the Anderson Clamp Hub, be sure to account for the reduction in manpower and man-hours needed to install and remove the hub. Also, take advantage of the avoidance of needing special (and potentially dangerous) equipment like high-pressure hydraulic pumps, flame throwers, and other heaters. The special features of the Anderson Clamp Hub can help eliminate the risk of lengthy outages caused by installation/removal problems or the case of damaging shafts enough to need repairs or replacement. Next time your large equipment needs a new hub, be sure to contact CouplingCorp to find out what an Anderson Clamp Hub would look like on your shaft.