Veteran technicians place a hand on a pump and feel the vibration—recognizing even the slightest variation in performance and remaining in perfect sync with the health of the machinery. They listen to the rumbling and whirling sounds and instinctively know when something is not quite right. They are so in touch with how the equipment should feel, smell, and sound, they can pinpoint issues quickly and expertly. And they know how to fix them.
These “machine whisperers” roam factory floors using all of their senses to identify and diagnose equipment issues. After all, most of them have been keeping the machines healthy and running efficiently for decades.
Carolyn Lee’s grandfather was one of them—a machinist during WWII. In fact, manufacturing continued to be part of the family heritage. Her grandmother worked on a factory assembly line, and her father is a mechanical engineer in the manufacturing sector. Lee is the Executive Director of the Manufacturing Insitutute, the workforce and education arm of the National Association of Manufacturers (NAM).
“I grew up believing and knowing how important it is to make things here in the U.S.,” Lee said. “I can still hear my father saying that as I say it. At the NAM and the Institute we have the ability to keep manufacturing strong, and the key ingredient is the workforce.”
As the machine whisperers retire and take their tribal knowledge with them, American factories are implementing all kinds of smart technology that can hopefully do digitally what the veteran technicians have done instinctively for years. And while twenty-something graduates are hired fresh out of college and bring with them the ability to collect and analyze machine health data, there doesn’t seem to be a replacement for the seasoned operator and the depth of undocumented information he possesses.
The challenge of filling this huge gap between the new tech-savvy generation and the veteran machine whisperer has been troubling manufacturers for many years as the highly-skilled trade workers required for today’s advanced manufacturing workplace continue to be difficult to find. The skill shortages include all stages of manufacturing—from engineering to the trades.
“One of the biggest challenges and biggest drivers we have in the manufacturing sector is the retirement of the Greatest Generation,” Lee said. “Before Covid, someone in the United States retired every eight seconds. So when you look at a sector like manufacturing with an older average-age employee, the retirement is a huge transition we are battling. But the gap we have is also about growth.”
According to a study by Deloitte and The Manufacturing Institute, the manufacturing skills gap in the United States could result in 2.1 million unfilled jobs by 2030. The study’s dramatic findings come from online surveys of more than 800 U.S.-based manufacturing leaders, as well as interviews with executives across the industry and economic analyses. The lack of skilled labor was the industry’s major challenge even before the pandemic. According to the NAM quarterly outlook surveys—and this new study shows it’s still a major concern today.
The challenges have been compounded by the global pandemic with about 1.4 million U.S. manufacturing jobs lost in the early days of the Coronavirus outbreak. While the industry is beginning to recover the lost jobs, skilled workers remain highly sought after and elusive.
Manufacturers surveyed reported that finding the right talent is now 36% harder than it was in 2018, even though the unemployment rate has nearly doubled the supply of available workers. Executives reported they cannot even fill higher paying entry-level production positions, let alone find and retain skilled workers for specialized roles.
“The skills gap is more acute today as economic demand rebounds, digital transformation accelerates, and competition for talent heats up,” said David Beckoff, Vice President, Product Development & Insights, Manufacturers Alliance for Productivity and Innovation (MAPI). “Entry-level roles remain difficult to fill. Machinists, operators, technicians, and others who are in positions to drive efficiency and productivity gains from new technologies on the factory floor are in short supply. Other jobs that previously required limited training now increasingly require work with analytics and problem-solving.”
The skills gap threatens to slow the momentum in manufacturing output emerging from the pandemic and undercut competitiveness in the long term.
“I’ve heard concerns from Manufacturers Alliance members about a labor crisis in their businesses now, and we see it in economic indicators and reports,” Beckoff explained. “A widely quoted study this month estimates a 2.1 million employee shortfall due to the skills gap, resulting in a $1 trillion gap in productivity in the year 2030 alone – which highlights the magnitude of the challenge and opportunity.”
Perception is Truth
According to Lee, there are two key challenges in closing the manufacturing skills gap.
“The people who are available don’t have the skills that we need,” Lee explained. “But the key to overcoming the skills gap is the perception. People just don’t realize that these are jobs that they would want and jobs that they should seek out. From our own research, we know that the perception of manufacturing is not great. People think it’s important for the national economy and for the national defense and for the overall health of the country, but they don’t see it as a job for themselves or for their kids. We need to change minds and open minds to the opportunities.”
Automation has attracted some workers to manufacturing, but in contrast, technological innovations can scare away some potential skilled workers.
“There’s an interesting dichotomy,” Lee said. “It’s either humans standing on lines assembling things from the 1950s B-reel, or it’s all robots and no people. The reality is that it’s neither. There are parts of both. On the automation side, of course there are robots and industrial automation tools and technology, but every single person you talk to who works on a factory floor who sees automation loves it because it takes away the things that humans don’t like to do.”
Attracting workers to manufacturing has become more difficult due in part to perception.
“My grandfather and dad would say that in the past you would just hang a sign and people would come,” Lee explained. “But the economy has changed so much that people just don’t know that manufacturing is here. Our buildings are set way back from the road. The majority of manufacturers are small to medium sized. We have to tell our story in a different way than we did in the 50s through the 80s. We already know that people are two-thirds more likely to go into manufacturing if you already know someone in it. That’s because the awareness is there. We must make more people aware so that they are interested, and then they can get skilled.
“The great news is that we need people with high-technical aptitudes, but we also need human skills like communication, teamwork, punctuality, creativity, innovation, and problem solving. Of course, we need machinists and welders and CNC operators, but we also need people in design and engineering and supply chain and logistics. There is a place for everyone in manufacturing, but first they must know that we are here and that these are good paying jobs and jobs they should seek out.”
Fighting the Skills Gap with a Focus on Diversity, Equity and Inclusion
The challenges of the manufacturing skills gap is multi-layered.
“On one level, it’s a replacement problem,” Beckoff said. “As the workforce ages and retires, fewer workers are available and equipped to backfill them. At the same time, work itself is changing and requiring new skills to interact with advanced technologies, which means employers must invest in time-intensive and often ineffective reskilling efforts for employees or hire externally. Both factors reinforce the need to close the so-called perception gap (dirty, dangerous, repetitive tasks) about modern manufacturing to attract tech-savvy workers.”
It has not benefited manufacturers that four-year degrees have long been elevated over vocational education, limiting potential recruits with in-demand skills. The problem is further complicated by a lack of diversity, equity and inclusion (DEI) in the manufacturing sector. However, this is where some manufacturers see an opportunity.
The study found that DEI initiatives are influencing workforce trends and can help manufacturers fill these empty jobs. Manufacturers have more work to do to attract larger numbers of women and diverse workers to the industry, and MAPI is leading an industry-wide effort to close the opportunity gap.
“Given the foundational role the manufacturing sector plays in our nation’s economy, it is deeply concerning that at a time when jobs are in such high demand nationwide, the number of vacant entry-level manufacturing positions continues to grow,” said Paul Wellener, Deloitte vice chairman and U.S. industrial products and construction leader. “Attracting and retaining diverse talent presents both a challenge and solution to bridging the talent gap. To attract a new generation of workers, the industry should work together to change the perception of work in manufacturing and expand and diversify its talent pipeline.”
Manufacturers’ associations are working hard on DEI initiatives as a core solution to filling the gap.
“We have a math problem,” Lee said. “The overall population is changing dramatically. We have a huge gap in gender representation within the sector. Only 29% of manufacturing workers are female. If we are going to close the skills gap, we must be attracting the entire labor force. Making sure we are reaching out with a diverse perspective of manufacturing matters because the math won’t allow us to close the skills gap otherwise. It is as much a math problem as it is the right thing to do for our community.
Diverse opinions and representation can lead to success, according to Lee.
“We know that companies are becoming more diverse and more competitive, and we know that companies with diverse boards have proven to be more successful,” she said. “When you have diverse opinions and experiences you will have different ideas to help with problem solving and that’s a great thing. The business part is really about keeping your employees. There are small steps that are important and worthwhile that companies of all sizes can make to close the people gap we have in the sector.”
The momentum in many organizations behind diversity, equity, and inclusion cannot be understated in any holistic approach to the skills gap.
“Women and minority groups that have been underrepresented in STEM fields are among the most promising talent pools for retention, development, and hiring,” Beckoff said. “Advancing DEI in manufacturing will be critical to closing the skills gap.”
At the Manufacturers Alliance’s recent virtual seminar “Activate Change: Diversity in Manufacturing,” there was a continuous theme of how manufacturers are engaging and listening to their employees and committing to creating a culture of inclusion and continuous improvement. Manufacturers are hearing the strain and pressures of women and acting on their initiatives as partners with their employees.
Most manufacturing companies have taken roles that allow for greater flexibility to work remotely throughout this past year. Codifying and continuing these options could help companies retain and attract female talent.
“We need to close the racial inequities and the gaps that we have in our society because it is the right thing to do, but it is also the economic imperative for our sector,” Lee said. “We need more people—and the workforce of the future is going to look different than the workforce of today.”
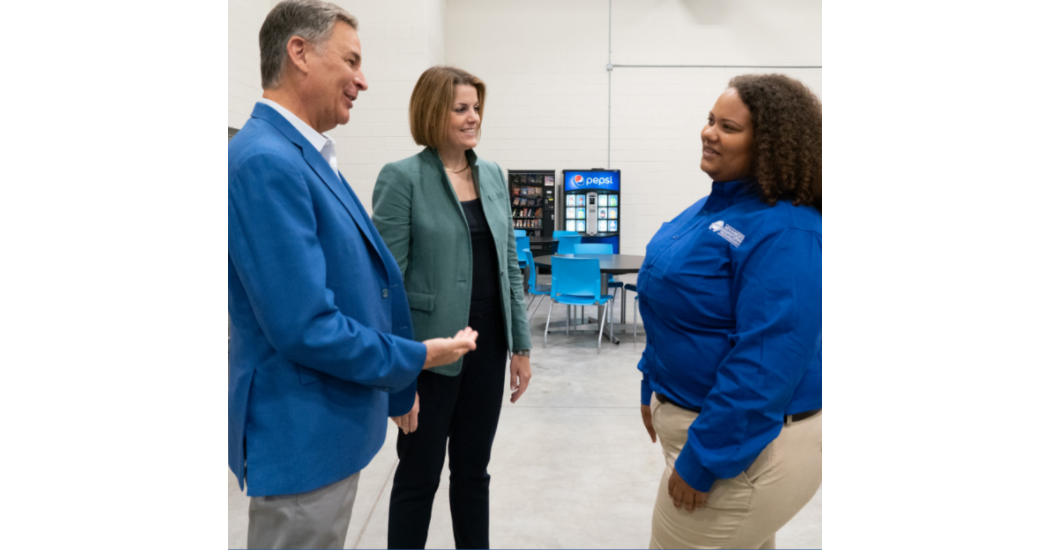
NAM President and CEO Jay Timmons with The Manufacturing Institute’s Executive Director at the FAME announcement in Huntsville, Ala.
More Initiatives to Help Close the Manufacturing Skills Gap
Addressing the issue is one thing, but creating action to solve it requires coordination, dedication, and creative ideas.
As The Manufacturing Institute, and their work with NAM, expand their efforts, they are working on initiatives like the Creators Wanted campaign and tour—designed to ensure that Americans of all backgrounds in all states can find a home in manufacturing and get equipped with the skills to seize the opportunities.
“Job openings in manufacturing reached an all-time high in March, according to the most recent Department of Labor data,” Beckoff explained. “For all the expectations for industrial automation, including artificial intelligence, a skilled workforce is, and will be, essential in advanced manufacturing—both for managing operations at a plant level and competing globally. Companies that develop and retain skilled talent will have the edge, as will communities that support this valuable workforce.”
Many manufacturing associations have initiatives to tackle the challenge.
“Manufacturers Alliance recently held a virtual event with industry leaders such as 3M, Hendrickson, Rockwell Automation, Stanley Black & Decker, and others to showcase practical solutions to solving the talent crisis,” Beckoff said. “Leaders are investing in partnerships for training, applying tools and technology, expanding the talent pool, and supporting continuous skills development. We also share these and other practical insights in our programming for members to help industry leaders adopt proven solutions.”
Partnering with Stand Together, and with a grant from the Charles Koch Institute, the Manufacturing Institute is enabling industry to grow the modern manufacturing workforce while closing the opportunity gap. Through roundtable discussions, webinars, C-suite leadership events, case studies and research, the Manufacturing Institute is helping manufacturers navigate second chance hiring and best practices.
One-in-three Americans currently possess a criminal record. Without second chance opportunities, many in this sizable talent pool are excluded from the workforce, needlessly leaving them on the sidelines as employers search for candidates who can fill skills gaps.
Meanwhile, the Federation for Advanced Manufacturing Education (FAME)—a premier advanced manufacturing workforce development and education program founded by Toyota in 2010—helps students become highly skilled, globally competitive, well-rounded and sought-after talent who can meet the unique needs and challenges of today’s modern manufacturing workforce. Every year, FAME graduates transition into well-paying, diverse career pathways in critical disciplines across the manufacturing industry and across the country.
Meanwhile, Manufacturing Day in its eighth year. Between 3,000 to 4,000 entities open their doors in October to let people see manufacturing first hand.
“There is no silver bullet,” Lee said. “There is no switch that can be thrown to instantly solve the challenge of closing the manufacturing skills gap. We need to work from multiple fronts from within the manufacturing sector, we need to raise awareness, and we need to start as early as the primary grades to educate students and peak their interest in some of these more technical jobs. We must do the work together as an industry to shore up the educational and awareness part, and we need to do a better job of reaching all populations to let them know we are here, and we need to talk about the opportunities. Its not just one job. In manufacturing you want retention, but we need to increase awareness that you can have multiple careers with one entity. This happens throughout manufacturing. We have CEOs who started on the plant floor and had multiple experiences within manufacturing.”
Is the Gap Closing?
While most manufacturers are aware of the problem and many programs are being implemented, it is difficult to tell if there is an end in sight.
“Given the labor shortage right now, it’s hard to say that a skills gap is closing,” Beckoff said. “The National Skills Coalition is one source tracking the deficit in skills in manufacturing. And with over 700,000 manufacturing jobs open, a record high, the scale and speed of change required demands action.”
The entire talent ecosystem—including the private sector, academia, government, and others – is critical to the progress in manufacturing, Beckoff said. “Partnerships for innovation can close the perception gap as well as narrow the skills gap with new training, credentialing, and experiential learning pathways beyond the traditional post-secondary degree. Technologies such as AV/AR and AI are enhancing reskilling opportunities on the plant floor.”
The digital skills gap is not limited to the entry-level work at the factory but extends to well-compensated and advanced positions, including engineering.
“A meaningful solution is not about optics and reframing the old modes of work, but shining a light on the technologies enabling exciting new work and well-compensated careers,” Beckoff said. “Desirable high-tech jobs are very compatible with factories today.”
Michelle Segrest is President of Navigate Content, Inc., a full-service content creation firm. She specializes in reporting about manufacturing and rotating equipment used in the industrial processing industries. She has published three books on Modern Manufacturing and hosts the podcast, “Factory of the Future.” Contact her at michelle@navigatecontent.com
Comments