Contributor: Applied Flow Technology
Rupesh Soni, a Senior Process Engineer for Stone Oil & Gas, was asked to design and size a new booster pump station on a plant site to increase peak pumping capacity from a Tailings Management Facility (TMF) from 4,650 m3/h (20,500 gpm) to a target 6,000 m3/h (26,400 gpm).
TMF ponds are a critical point of containment in mining operations, and as such it is imperative to regulate its liquid level during cyclones and rainy seasons to avoid environmental contamination. To manage the overall water level at this facility, excess process water (such as tailings run‐off or rainwater) is pumped via a 14.6 km (9.1 mi) pipeline from the TMF to an ocean outfall diffuser.
The existing system consisted of a floating pump barge located in the TMF South Basin which had three (3) barge pumps connected in parallel. The original design was rated for 4,000 m3/hr (17,600 gpm) through the pipeline, which culminates in a 100-diffuser port marine outfall which drains the excess water.
As a precautionary measure to meet flow demand, the pipeline tied into six (6) diesel pumps located 2000 m (1.2 mi) downstream of the barge pumps and 500 m (0.3 mi) upstream of the system’s valve station. The valve station is the highest point in the system, raising potential Hydraulic Gradeline (HGL) concerns that flow may not continue downstream as intended. HGL analysis was essential for all considered pumping setups to ensure a sufficient gradient for flow over the high point. While changes in pump set-up increased the flowrate to 4,650 m3/h (20,500 gpm), the overall flow remained below the target 6,000 m3/h (26,400 gpm) peak flowrate for rapid draining.
To accommodate future operation needs, it was determined that a new booster pump station needed to be installed in the middle of the pipeline. The new booster pumps would be installed alongside the existing overland pipeline, downstream of the valve station,
consisting of two (2) 50% pumps operating in parallel. The booster pumps would not be required for continuous operation, instead only being run when additional flow was required to manage the TMF level. In most cases, the booster station would be bypassed by the pipeline.
One consequence of the increased flowrate is increasing the fluid velocity above the maximum allowable velocity, reaching 3.3 m/s (11 ft/s) compared to the allowed 2.4 m/s (7.9 ft/s). This necessitated steady-state and transient hydraulic analysis using AFT Impulse to ensure adequacy of design and piping supports (Figure 1).
A steady-state simulation model incorporating the supplementary diesel pumps was benchmarked against reported client plant data. An additional K Factor loss was specified to match the AFT Impulse model to plant data, accounting for pressure losses in the system without modeling large numbers of elbows or similar fittings. The marine outfall diffuser was modeled as a general flow component, fitting a single resistance curve to account for losses through all the individual ports.
Stone Oil & Gas engineering expertise allows them to provide a full range of domestic and international multi-discipline engineering, procurement, and project management services. With offices located in Toronto, Canada and Abu Dhabi, UAE, Stone Oil & Gas, a division of Norda Stelo, brings North American engineering execution and international presence to global markets.
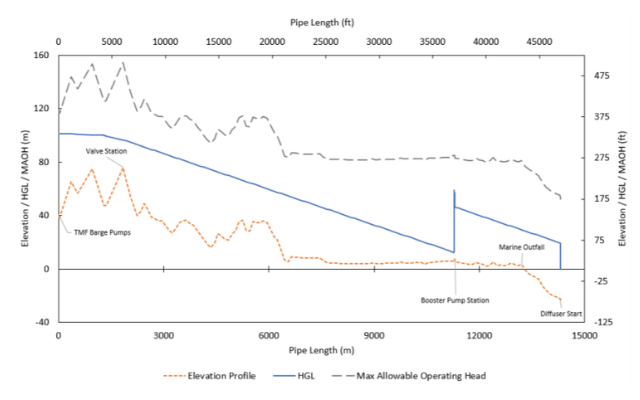
Figure 2: Steady-State HGL for pipeline, with 3 Barge Pumps + 2 Booster Pumps. This analysis indicated sufficient gradient to ensure flow without exceeding allowable operating head of pipes.
The common discharge pressure at the temporary pumps in the model was 645 kPag (93.5 psig) compared to the 650 kPag (94 psig) reported by the client. The modeled pipeline flowrate was 4,660 m3/hr (20,520 gpm) compared to the reported 4,650 m3/h (20,470 gpm). These differences were negligible and indicated positive agreement between the simulation model and the existing return water pipeline system.
Using the calibrated model, Soni could then size the booster pumps with no fouling in the pipeline. He then tested these sized pumps with fouled pipeline conditions to ensure HGL gradients were sufficient for flow and the Maximum Allowable Operating Head of the pipes was not exceeded. He also experimented with other pump combinations to find the maximum possible flowrate, unfortunately below the desired design flowrate due to pipeline fouling. Cleaning the pipe would easily improve the peak flowrate.
AFT Impulse helped Soni finalize a booster pump datasheet, allowed him to analyze the pipeline for Maximum Allowable Operating Head (MAOH), and ensure there was sufficient HGL. He said the man-hours spent on finalizing the booster pump datasheet, related instrumentation, and creating steady-state & transient models for various scenarios was significantly reduced by using AFT Impulse. Ultimately, his analysis resulted in reduced costs and a shortened schedule for the lumpsum project.