During the preparation phase of any coating project, it is important to understand the strengths and weaknesses of the substrate.
In the case of industrial stainless steel, hardness and corrosion resistance are its strengths. However, this same hardness can be challenging for coating applicators to create a 3-5 mils rough angular surface profile, necessary for proper adhesion.
The Armstrong Fluid Technology team helped a customer with an ARC BX2 application that was delaminating from a stainless steel substrate. They were asked to figure out why this was occurring.
Proper Surface Preparation for Coatings
Typically sheet delamination can be attributed to surface contamination such as oils and greases. Another potential factor is insufficient surface profiling. Proper profiling “anchors” the product to the substrate as the liquid coating flows into the profile, locking in place when cured. It is critical, therefore, to select the media that will establish the ideal profile.
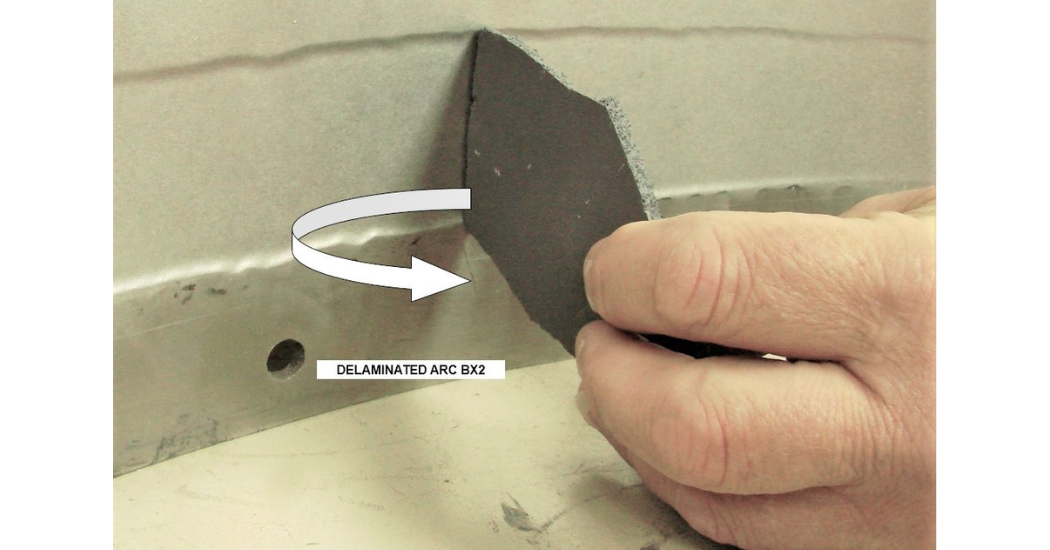
Proper surface preparation is vital to anchoring coating to a specific substrate.
To prove a point, we took some stainless steel and grit blasted it with three different medias using the same nozzle pressure. Two of these media were options specified for this application. The primary factors to consider in media selection are hardness and shape, as well as density. These factors define an abrasive’s ability to “cut” the anchor pattern during the grit blasting phase.
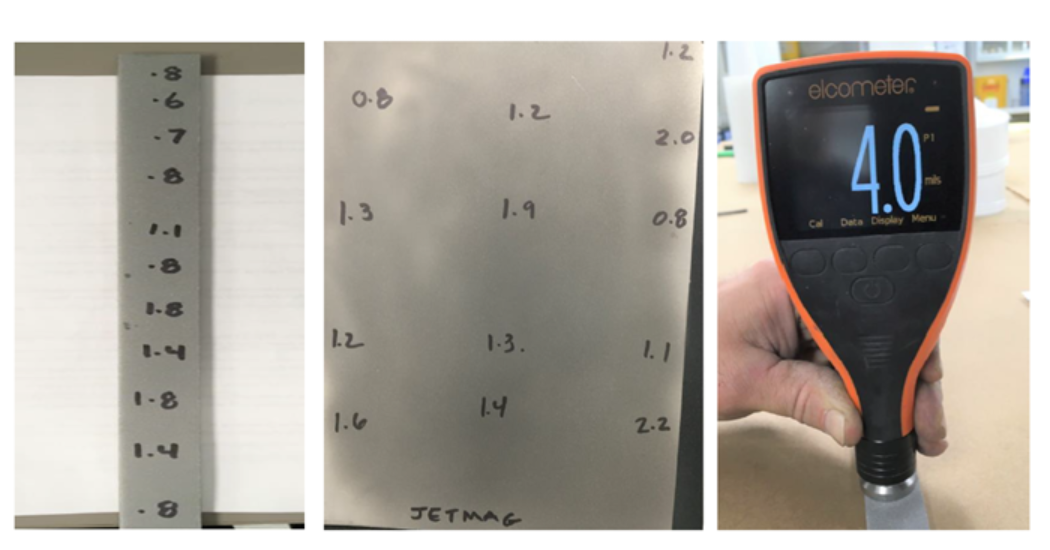
Blast profiles achieved:
Recycled Glass (left), Sintered Olivine (center), and Aluminum Oxide (right)
As seen above, recycled glass and sintered olivine (the two specified systems) are too soft to create the required 3-5 mils surface profile on stainless steel. The insufficient surface profile failed to create an “anchor” for the coating. This resulted in loss of adhesion and delamination.
To properly create the 3-5 mil profile on stainless steel, we recommend using Aluminum Oxide (24 grit) or Silicon Carbide (30 grit). Either of these grit media can create the appropriate surface profile range on stainless steels. They ensure proper adhesion of ARC coatings, while leaving the surface free of contaminants.
Do you have a question about a specific coatings application? Contact Ask the Expert service today.
About the Author: Steve Bowditch is the Global Market Development Manager for ARC Efficiency and Protective Coatings. He is a NACE Level III CIP Inspector and SSPC Corrosion Specialist with over 35 years’ experience in the areas of protective coatings development and applications. When he is not immersed in the exciting world of protective coatings, he is hopefully sailing on a Hinckley Bermuda 40’ somewhere near a tropical island chain.